UV flexo for food packaging
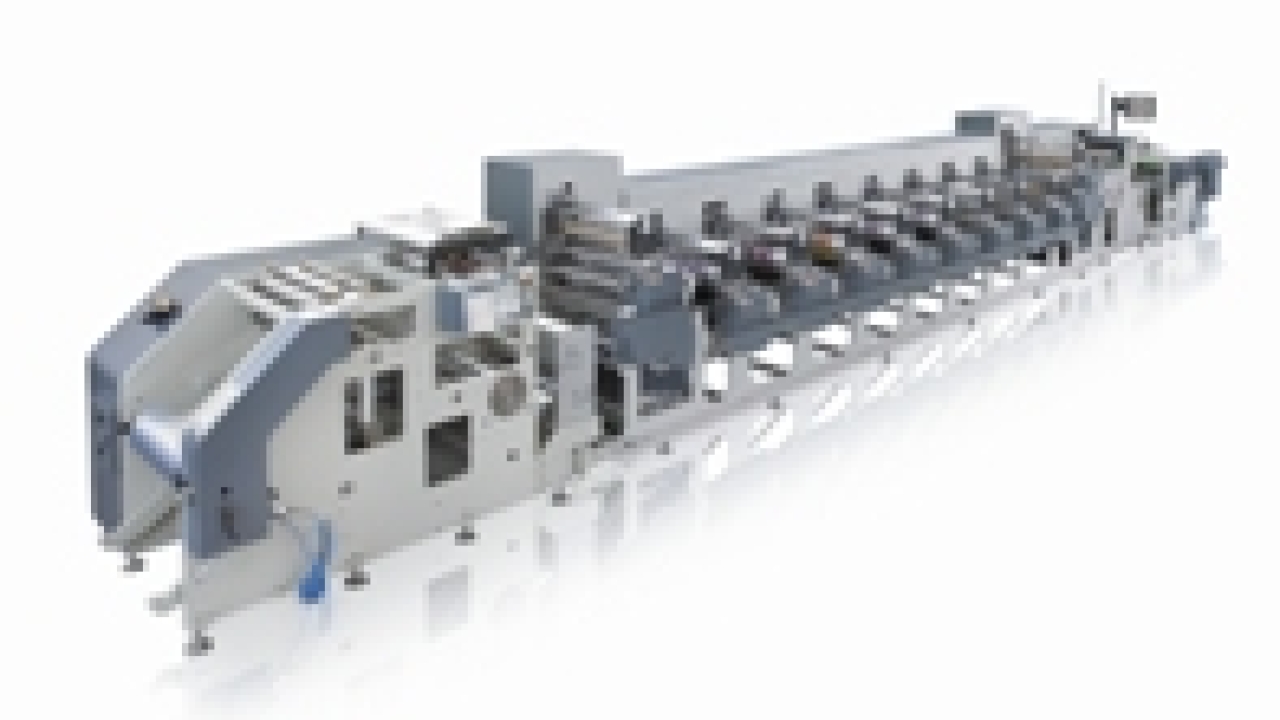
Federico d’Annunzio, managing director of Nuova Gidue Srl, assesses issues of UV flexo inks and in-line UV flexo presses, and looks at a solution for food packaging using solventless lamination in-line
Interaction between the packaging and label industry is becoming common, and it is supported by major industry suppliers (ink, substrates and printing machines) that are often serving both industries. The use of UV curable inks has been a widely adopted practice in the narrow web label industry for more than a decade. The first truly successful industry applications, however, started in the packaging industry (alufoil for pharma blisters, yoghurt caps, tooth paste tubes) in the early 1990s.
Advantages of UV flexo inks
UV flexo inks have changed rheology and formulations to provide full safety to consumers, enhance production speeds and consume less curing energy, in cooperation with UV lamp suppliers.
In terms of energy sustainability, UV curable photoinitiators and UV lamp efficiency have greatly advanced in the past few years, becoming faster in curing with the lowest level of energy consumption. The new generation of UV curing lamps is reducing energy consumption by 40-50 percent without reducing the press speed. For example, a 630mm-wide, eight-color UV flexo press, running at a speed of 200m/min, uses a total of 80KW/h for UV curing, meaning UV is the most eco-friendly ink process in term of energy consumption.
Environmentally, UV curable inks are odorless, solventless, do not generate VOCs and do not need solvent recovery or explosion-proof presses, storage areas and manufacturing practices. A UV flexo printing environment is clean and operator friendly. And new low-migration inks guarantee limited risks for the health of the consumer, as heavyweight, long chain polymers are unlikely to migrate and selected non-toxic ingredients are chosen.
Waste is reduced as UV inks do not dry on the plate. Long runs, starts and stops create substrate waste but UV ink is instantly ready for printing. UV inks are 100 percent solid, ink properties are not affected by evaporation and a shelf life of six months for mixed inks is common, meaning waste from stored inks is greatly reduced compared to solvent or water-based inks.
With the new UV inks come enhanced ink transfer properties as well as faster reactivity to UV curing, meaning speeds over 200m/ min are achievable. Plus: new HD and flat top dot technologies in flexo plates greatly enhance UV flexo characteristics, reduced dot gain (comparable to offset), deep image contrast (comparable to gravure), 80 lines/cm screens (comparable to gravure), consistent print quality during the run (and during the year), independent from temperature conditions and operator skills (unique to UV flexo) and a predictable standardized print result in repeat jobs independent from the operator (unique to UV flexo).
A new generation of presses has been launched in 2010-2011 by several in-line narrow and mid web press manufacturers. The higher cost of UV inks is compensated by deep digital automation and efficient part handling to produce high-quality short and medium run packaging, with the lowest running costs in the market. Traditional packaging converters are still not fully familiar with the efficiency and sustainability of in-line UV flexo presses. Educational articles and technical information are a recommended instrument to grow the overall awareness of UV flexo possibilities for the packaging converting industry.
The new generation of in-line UV flexo presses is taking advantage of the limited number of variables of the UV flexo process, such as no ink evaporation, which allows for digital flexo servo automated adjustments. Repeatable, predictable and digital set-up waste of less than 20m are becoming the norm among several in-line UV flexo press manufacturers.
New servo technologies for short web paths on over-dimensioned chilled drums (less than 10m web path for an eight- color press) allow for accurate registration on any web printable substrate, including LDPE and the most difficult applications. Register performance and press flexibility are comparable to CI flexo presses while keeping the advantages and accessibility of in-line presses.
Digital flexo fully automated adjustments, convenient handling of parts (lightweight, easy to remove and install) and the equal height of printing units drastically reduces set-up times. A realistic overall set-up time of 10 minutes (and 20m of real substrate waste) per packaging job (including 1-2 spot colors ink change) has no equal comparison with other press configurations in the packaging industry, such as CI flexo, in-line gravure and offset.
Digital automated set-up and production adjustments, in combination with the inherent stability of UV inks, require fewer skilled and less expensive operators in the printing process, meaning the operating cost of the new generation of presses is reduced. In addition, print quality can be reproduced digitally with limited dependency on operators’ skills. Highly predictable waste levels, set-up and production times, repeatable standardized digital productivity and quality are possible.
Obstacles to UV flexo in food packaging
As UV flexo inks have a high potential for technical development many formulations are new, and require safety regulation authorities to undertake stringent procedures and undertake expensive testing to reassure the consumer’s health. On the other hand, established solvent and water-based ink formulations are less often under such scrutiny due to a slower drive to innovate, at the same time reducing overall ink costs against UV inks.
Safety regulation uncertainty also prevails. EU regulation 1935/2004/EC, Swiss Ordinance and upcoming German Ordinance, EFSA procedures, GMP EU Procedures, FDA authority and additional safety tests requested by major brand owners are some of the compliances requested for food packaging. As an independent and globally recognized authority for food safety in packaging is not yet available, a relatively young industry product such as UV ink is confronted with the obstacle of unclear guidelines and authorities.
The high cost of research and development of food packaging compliant inks is another obstacle. The UV flexo ink industry is highly dynamic and constantly looking for new solutions for higher curing speeds and lower ink migration, to eliminate toxic components and reduce energy consumption, provide better adhesion and shrinkage properties, better ink transfer for high print quality results and reduced costs.
Ink ingredients are constantly changing, following research and development innovation. High toxicological testing costs and long bureaucratic times of legal approval for each ink component reduce the speed of innovation, which is potentially higher than in the solvent and water-based inks industry.
Some inherent risks of UV technology also exist. The most commonly used free-radical UV inks do not cure 100 percent under UV exposure. A minimal fragment percentage of non-cured
UV ink is trapped within a network of long chain polymers created by the UV polymerization. If Good Manufacturing Practices are not followed properly, as UV curing is not controlled, the risk of mass product recalls are possible due to UV ink migration to the food.
Solutions for safe use of UV flexo inks
The UV flexo industry has developed new technologies to serve the food packaging industry by reducing the quantity of photoinitiator in the ink and by increasing its ability to eliminate risks of migration of non-cured free-radicals.
Several private brand safety tests have been claimed successful by major suppliers of low-migration UV flexo inks.
However, uncertainty and unsafe market perception remains among the majority of brand owners and traditional packaging converters. The set-off of ink inside the printed reel migrating to the back of the reel (in contact with food) is seen as a major obstacle for 100 percent adoption of UV flexo inks for food packaging applications.
Cationic UV inks are opposite to free-radical inks as the polymerization process is 100 percent complete once started. Delays of 24 hours or more until full polymerization are possible, making the safety to set-off ink migration questionable, as ink can even migrate during its post-curing time inside the reel. Curing speeds are not as fast as free-radical inks, ink costs are higher and the process efficiency is related to the working environment (humidity in the air can reduce curing performances). A number of packaging converters have, however, had success adopting cationic UV inks in niche short-run food packaging markets, with the benefit of excellent adhesion, high print quality and reduced waste.
A major obstacle to full polymerization is oxygen. UV radiation in the lamp head breaks the oxygen molecule (air in the lamp house) in two parts which combines with the monomers and photoinitiators in the ink. This undesired effect interrupts the chain of polymerization inside the ink and leaves some light molecules free to migrate. Inerted UV dryers substitute ambient air in the lamp housing with an inert gas (usually nitrogen), greatly reducing the effect of oxygen to inhibit polymerization. Full polymerization, less quantities of photoinitiator, higher curing speeds and very limited ink migration have been experimented.
Practical obstacles, such as the need for a nitrogen reservoir, feeders and pipes inside the production environment, and high capital investment costs, have limited adoption of this technology in some UV offset applications for food packaging.
Low-migration free-radical UV inks seem to be the preferred technical choice of the major UV ink suppliers.
New ink formulations allow for heavyweight, long chain polymers to be formed with extremely reduced ink migration. Results well under the 10 ppb migration levels (which comply with most of the international safety legislations on food packaging) have been reported under intense industrial use. Provided that Good Manufacturing Practices for UV curing are followed, few major brand owners are accepting, in limited food packaging markets, the use of new generation low-migration UV inks with skepticism and uncertainty on set-off ink migration still preventing wide adoption of the process.
UV flexo printing and solventless lamination in-line
By joining together the quality and efficiency of UV flexo technology with well established solventless lamination, which has been used for many years in flexible packaging production, it is possible to overcome most of the obstacles related to the use of UV flexo inks in the food packaging industry.
By installing a solventless laminator in-line with a UV flexo printing press, the ink is effectively protected by a transparent film layer, which in most cases would be laminated off-line. Ink is trapped between two layers and simply cannot make contact with or migrate to any surface. This solution collects the advantages of both processes, such as reduced wastes, high printing and functional quality, for the production of high-gloss and high-quality short and medium runs of food packaging.
A majority of food packaging applications are printed on CI flexo or gravure printing machines, where the reel of packaging is printed and then taken to an off-line solventless laminating machine. The solventless laminator applies to the surface of the printed substrate (or vice-versa) a second layer of an alternative substrate to add high-gloss, scuff-tear resistance, protection from ink contamination, plus other mechanical and functional properties to the final packaging. Solventless lamination is the predominant packaging laminating technology due its good bonding properties, no VOCs, reduced set-up waste, reduced capital investment cost, single operator operation, low energy consumption and flexibility to laminate most of the available packaging substrates.
For in-line solventless laminating with a UV flexo printing press, a solventless laminator is added at the end of the press. The packaging web is printed, then a transparent film layer is laminated on top of the printed surface before rewinding the reel. The additional film layer acts as a protection layer, trapping the ink inside two layers: the printed web and the laminated web. The ink does not come into contact with the inside of the web while rewinding so no set-off ink migration is possible, and the ink cannot later come in contact with any food as it is trapped in the sandwich of the two layers. Provided that low-migration UV flexo inks are used, in order to avoid ink migration through the substrates, as well as Good Manufacturing Practices, solventless lamination in-line with a UV flexo printing press virtually eliminates the risks of UV flexo ink migration and provides a definitive solution for the use of UV flexo technology in the food packaging industry.
To keep the converting process profitable, the press manufacturer should provide highly automated digital operations both on the printing and laminating processes to allow for reduced waste, quicker set-up times and the use of less skilled operators. At the moment, only one press manufacturer, Nuova Gidue, has ‘invented’ and is offering a fully integrated UV flexo/ solventless laminator solution, although similar projects are under development by other press manufacturers.
UV-Flexo is a dynamic and innovation-oriented industry. The efficiency and environmental sustainability of the UV flexo process is well proven in the narrow and mid web labels and packaging industry. Along with alternative new ink solutions, in-line solventless lamination on a UV flexo printing press provides a universal safety compliant solution for food packaging.
Innovative food packaging converters can take advantage of the new digital flexo technologies developed by press manufacturers in combination with the inherent limited waste and high printing quality of UV flexo process.
Profitable production of high-quality fragmented, short and medium runs of food packaging is possible. Safety risks for consumers are virtually eliminated; the entry level costs and times for food packaging converting and selling are reduced with fewer laboratory tests needed as ink is not in direct contact with any surface.
Stay up to date
Subscribe to the free Label News newsletter and receive the latest content every week. We'll never share your email address.