100% track and trace EPC solution for pharmaceutical industry
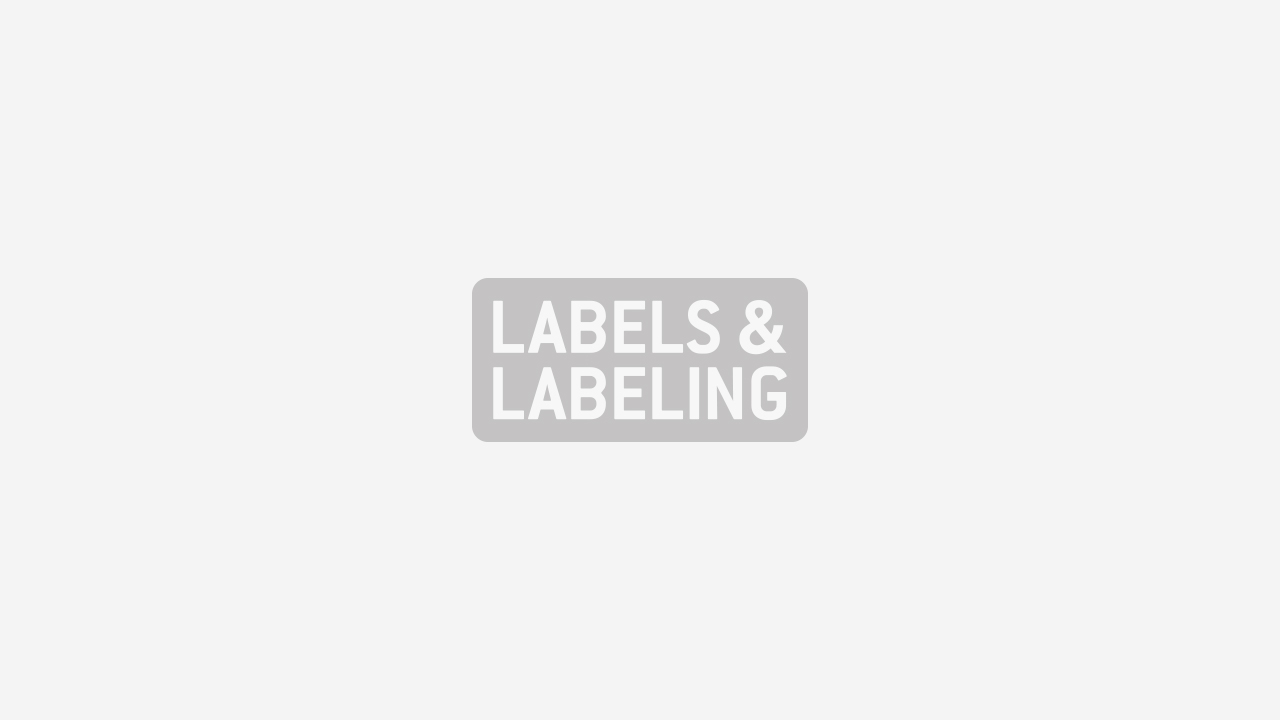
Domino Integrated Solutions Group, the National Centre for Hereditary Coagulation Disorders in Ireland (NCHCD) and global supply chain standards organization, GS1, have announced the successful implementation of the a fully integrated EPC solution for the pharmaceutical industry, involving 100 per cent track and trace of drugs administered to Haemophilia patients of St James’s Hospital in Dublin.
Project-managed by Domino and GS1 Ireland, the pilot concentrates on end to end traceability of Haemophilia products in Ireland, allowing secure deliveries and stock optimization in full respect of cool chain logistics and patient safety.
The drug track and trace system uses GS1’s latest electronic bar coding technology to trace expensive and time-sensitive Clotting Factor Concentrates (CFCs), the product used to treat haemophiliacs. The integrated EPC technology (electronic product code) assigns a unique number to every single item that rolls off a manufacturing line, allowing every company in the supply chain to track products at the individual item of use level. Following a two year trial period, the solution has been successfully implemented and is ready to be rolled out nationally.
The use of unique serial numbering and bar coding on each vial box to enable automatic electronic data collection and processing will result in safer patient treatment and 100 per cent traceability and accountability of every drug and patient involved in this critical treatment process.
The trial was the brainchild of Dr Barry White, director of the NCHCD, whose vision was to establish a comprehensive and fully traceable drug administration programmed, from manufacturer through to patient. His concerns were in respond to the publication of the Lindsay Report in 2002, which reported the infection of hundreds of haemophiliacs with HIV and Hepatitis C as a result of receiving contaminated blood products.
Dr Barry White commented: ‘The contamination of blood products was one of the most catastrophic medical complications of the last century and some of the infections were due to defects in the supply chain. There were considerable difficulties in identifying who had received the infected CFCs and in recalling all the contaminated products.’
Jim Bracken, chief executive at GS1 Ireland, explained: ‘The NCHCD project is being studied by an expert group, which includes the EU Commission, the FDA, the World Federation of Haemophilia and other stakeholders. Working with such a high-profile consultative group means they can validate the solution during the implementation and specify the needs for a system that can be adopted globally and extended to other patient groups and vaccines. Additionally, the solution has been validated to Good Automated Manufacturing Practice.’
The key objectives of the programmed were to implement real time identification of CFCs to ensure immediate product recall, optimize stock management and save on wastage. The unique coding allocated to each drug product, and the additional data captured during the supply process will automatically validate each step of the cold chain storage and delivery process, ensuring that the correct drug is prescribed to the right patient as well as automatically update patient history and assist in ongoing diagnosis and future treatment.
Tony Walsh, European business development manager at the Integrated Solutions Group of Domino Printing Sciences Plc, commented: ‘This 100 per cent item-level track and trace solution is a tremendous breakthrough and heralds a new area for patient safety. Tracing blood products accurately throughout the supply chain is absolutely vital to ensure the safer administration of Haemophilia drugs. This solution will guarantee that the right patient receives the right dosage of the right blood product, at the right temperature and at the right time - every time.’
Domino co-ordinated the individual expertise and responsibilities of all the organizations involved in the programmed, and integrated each part of the supply chain to deliver a seamless solution. These suppliers included Baxter BioScience, the CFC manufacturers based in Belgium; EPC network provider VeriSign; software company Melior Solutions; and specialist cold chain logistics suppliers Temperature Controlled Pharmaceuticals Ltd (TCP) who in turn worked with Advent Software as a local solution provider.
It was possible for the first time to embed EPC technology within a Data Matrix code, and present a fully workable end to end trial from original manufacture of the blood product, through to delivery to the individual patients at their homes in Ireland. Domino, Melior Solutions and VeriSign developed an automated solution for the creation of the EPC numbers on the Data Matrix Code which can be linked to the EPCglobal Network. In addition to a serialized number, the Data Matrix code also includes a Global Trade Item Number (GTIN) as well as a lot number and expiry date.
Tony Walsh explained that the achievement of EPC generation and networked connectivity means that no matter where the product is within the supply chain, once can trace when it was made, who handled it and whether it is authentic.
Having proved that full traceability is now a reality, with data being captured at each product movement within the supply chain, the next step will be to introduce a handheld web-based device such as a mobile phone, which can be used by the individual patient to scan the bar code on the drug when self administrating the product. This will automatically update the patient’s records at the hospital and prevent any manual errors in recording data.
Dr White added: ‘As a product moves through the supply chain, manufacturers, trading partners and regulators all have access to key data which becomes invaluable when addressing issues such as product recalls, product authentication or defective ingredients, which, in the case of haemophiliacs, can mean life or death.’
Tony Walsh at Domino concluded: ‘This really is one of the most exciting and challenging trials that has successfully demonstrated track and trace capabilities, with huge scope for taking this one step further by introducing RFID into the process. Once this RFID technology is ready for widespread deployment, I am confident that in the next few years, we will be looking at the next “Holy Grail” in terms of logistical development and traceability for a wide variety of applications.’
Stay up to date
Subscribe to the free Label News newsletter and receive the latest content every week. We'll never share your email address.