The low migration story
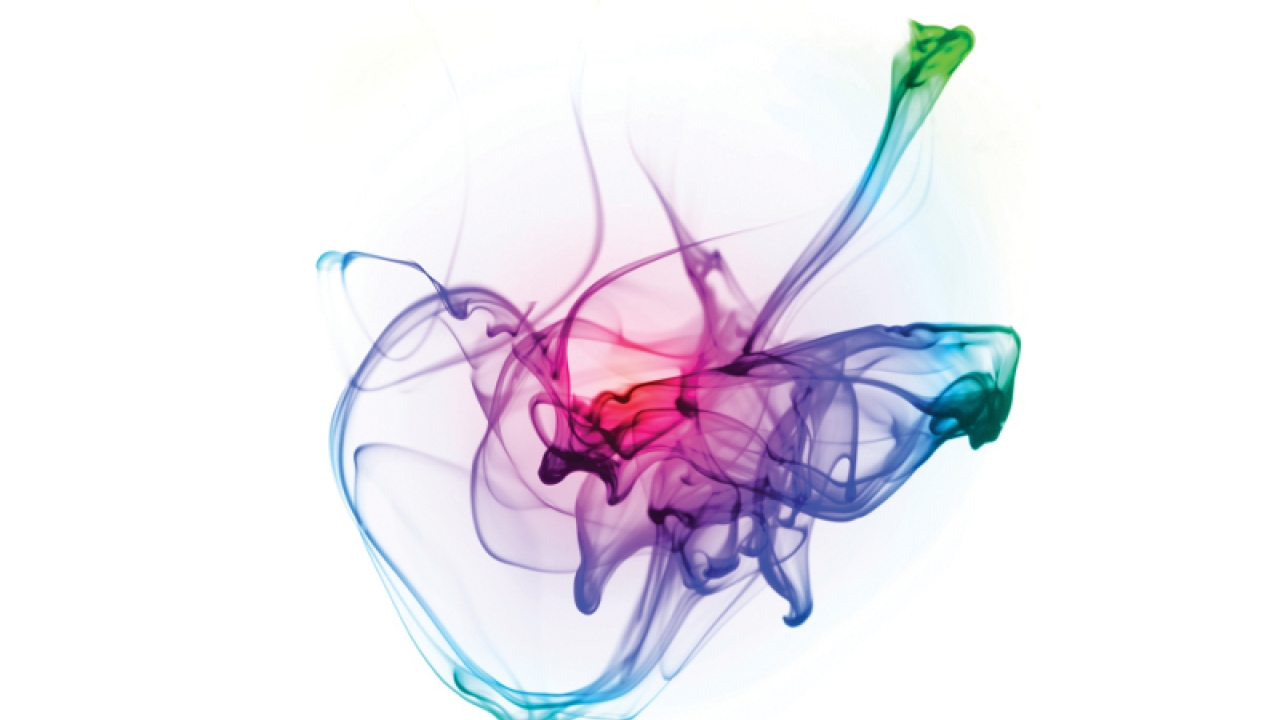
Low migration inks have become a focus for intense discussions, but does the industry understand the consequences? Eva Freudenthaler, VP marketing and technology, within the packaging and narrow web division of Flint Group, explains the issues
In the past packaging products were classified as being primary or secondary packaging. Most food packaging fell into the secondary packaging area. In this case the printed material was not considered to come into contact with the food stuff, which was generally packaged in another material. Although some printers may have been aware that ink components from printed items could migrate or transfer from the back side of the printed article, the legislation which applied was unclear.
But in 2005 the first big food packaging ‘scare’ took place, when ITX, a commonly used photoinitiator at the time, was found in a packaged milk substitute. Due to a lack of information and readily available toxicological data, ITX was subsequently ‘banned’. The migration of this substance from the packaging material into the packed foodstuff was alarming, particularly as there was no information at the time whether the migrating substance might affect the odor or taste properties of the food stuff or even be harmful.
One result of this scare was that many brand owners started to seriously look into their responsibility according to the Framework Regulation (EC) No 1935/2004 regulating materials and articles intended to come into contact with food. The outcome of this was that some brand owners put their own guidelines regarding migration and formulation practices into place. Shortly after this scare, more legislation was introduced in Europe including the so called 'Good Manufacturing Practices' directive, (GMP; EC/2023/2006), to support the Framework Regulation.
Independently of European regulations, the Swiss government decided to introduce the Swiss Ordinance on materials and articles (SR 817.023.21; 2010) which for the first time included provisions that apply to packaging inks as specific constituent elements of materials and articles.
These two pieces of legislation together started to clarify the previous gray areas. The GMP directive defines the rules for good manufacturing practices for groups of materials and articles intended to come into contact with food, whilst the Swiss Ordinance – only applying to the Swiss market – details a positive list with substances which are allowed to be used in the production of printing inks in combination with clear regulation about accepted migration limits. Although there is still no European legislation regarding the use of printing inks for food packaging per se, these pieces of legislation gave a clearer picture to both brand owners and the packaging supply chain about their obligations.
Both pieces of legislation support brand owners with proving compliance with the framework directive (EC/1935/2004), which states that materials and articles, whether printed or unprinted, must be manufactured under GMP, so that under normal or foreseeable conditions of use, they do not transfer their constituents to food in quantities which could endanger human health, bring about an unacceptable change in the composition of the food, or bring about a deterioration in the organoleptic characteristics thereof. The legislation is very clear in that it applies to all types of packaging, regardless of the technology used, and also clearly state that the responsibility for the compliance of the food package is the responsibility of the entire packaging chain. No one link in this chain can assume overall responsibility or take over the responsibility of another member of the packaging chain, should something go wrong.
Why does everyone focus on UV?
In reality everything in any ink or coating with a molecular weight under 1000 Daltons can potentially migrate. Whilst materials with a molecular weight above 1000 Daltons can still migrate, they pose no risk to human health, as they pass directly through the body.
When considering potential migrants, a number of different types of raw materials need to be considered. Generally speaking they are additives, which are added to the printing ink formulations. These include flow additives, flexibilisers, surface treatments on pigments, dispersing agents and photoinitiators amongst others.
The migration limits which are applied are always the same regardless of ink or varnish technology type;
- 60 ppm global migration for substances without migration limit
- Specific Migration Limits (SML) for evaluated substances
- 50 ppb for not evaluated substances with three negative mutagenic tests
- 10 ppb for unevaluated substances
Although the Swiss Ordinance is the only legislation regulating these migration limits, the European Printing ink association, EuPIA, published in 2010 a document advising the suitability of photoinitiators for low migration UV based printing inks and varnishes, and also recommend these limits to their members.
Many of the readily available photoinitiators did not have published toxicological data available, and as such were ‘unknown entities’ with respect to migration.
But a scare in the market place is not often based on facts. As recently as 2010, there was a scare with the photoinitiator benzophenone. This photoinitiator has known Specific Migration Limits as well as FDA approval and is used as a flavor enhancer. But the reality is that this photoinitiator has a high volatility and so is not preferred, and even banned by packaging manufacturer groups, due to its negative affects on the organoleptic (taste) properties of the packaged article.
Photoinitiator development has progressed a lot during the last few years, and most development work has been focused on increasing the molecular weight of the materials without reducing the efficiency. The European printing ink organization, EuPIA quotes the European UV ink and varnish market to be around 23,000 tonnes, and considering that there are approximately 10 percent photoinitiators in an UV printing ink formulation, which can be split between three to five materials, then individual photoinitiator market sizes are relatively small.
UV curing is a process where free radicals become excited under UV lamps and then initiate the cure process. Traditionally low molecular weight photoinitiators are extremely efficient, and thus the first generation of low migration UV inks typically had much slower cure response, when compared to these traditional products. The traditional photoinitiators can also generate bi-products which have an undesirable impact on taint and/or odor properties of the packaged product, so ink and coatings formulators are forced to combine these larger molecules in a way so that cure response is not impacted.
This is particularly tough in darker colors, where the pigments absorb a large portion of the UV energy available to initiate the curing process. However photoinitiators are not the only source of migrants in an UV printing ink or coating. The monomers, which are the ‘solvents’ of these systems, differ from normal solvents as they are reactive and combine with the oligomers to form a film on curing. Many of the monomers which are effective in reducing the viscosity and controlling the rheological properties of a printing ink also have a low molecular weight themselves, or contain portions of low molecular weight materials, and can also contain other additives and stabilizers, which can potentially migrate.
Another migration concern, although not restricted to UV inks alone, is the use of unsuitable pigments. A good example is ‘so called’ fanal pigments, which are often preferred by end users for their clarity, depth and cleanliness of color. These can easily set-off on the backside of a print, or can bleed into foodstuffs and therefore also pose a potential risk.
Today however, low migration UV inks and varnishes are developed so that when correctly applied and cured, onto the correct choice of packaging substrates, the legal migration limits can be met. Nevertheless no ink or varnish supplier can guarantee that the formulated migration levels will always be achieved in practice, as so many practical factors have an impact. The printing ink or varnish manufacturer actually has only an obligation to formulate an ink which, when applied and cured under the correct conditions, should enable the end user to be in compliance with the framework regulation. All ink manufacturers which are members of the EuPIA have also committed to produce these inks according to GMP guidelines and to provide a statement of composition for each ink.
Ink manufacturers try to balance the lowest migration raw materials with functional materials to reduce the risk of contamination from accidental misuse of any press side additives. Inks therefore are developed to have the correct rheology profile, cure response, scratch and adhesion resistance, as well as being commercially viable.
This is again another tough challenge, particularly maintaining a commercially viable product, as not only are raw material costs higher, but there are additional processing stages as for all food packaging intended materials, along the packaging chain (eg GMP compliance) to be taken into account, so that the finished, packed article can be considered to be compliant. Although printing ink and varnish costs are estimated to be only three percent of the overall packaging article cost, these extra stages will eventually push up the prices to the end consumer.
Many ink manufacturers have therefore adopted an approach of having dedicated production facilities for low migration products, as this reduces the risk of contaminants from human error and also from common working areas, assuming that any potential volatile migrants are also removed from the facility. After production ink manufacturers that are members of EuPIA, have committed to provide data to the packaging supply chain, in the form of a statement of composition which supports the brand owners in showing compliance with the framework directive. Many ink manufacturers choose to test only one of the stimulants specified as a worse case study, but the stimulant choice will ultimately be governed by the packaging type and foodstuff to be packed. Some ink manufacturers also provide ‘in-house’ testing facilities, but the end user is still responsible to supply a conforming package into the market place.
Basically the only way to be sure that you have stopped migration is to use a functional barrier. Today this is defined as a barrier consisting of one or more layers of any type of material which ensures that the final material or article complies with article three of the Framework regulation and with the provisions of this regulation, but in reality the only materials which practically conform with this are aluminium foil (if not too thin), glass or metal. No other materials offer true barrier properties.
The conclusion and consequences?
The implementation of the Swiss Ordinance in April 2010 meant that all ink products used or printed articles imported in Switzerland needed to be formulated using the materials listed on the Annex one and six of the Ordinance 817.023.21. This will no doubt make its way into national legislation of other European member states or even legislation at an European level.
It is however important for the complete packaging chain to understand their impact and responsibilities when producing food packaging articles, and that they fully understand the complex nature of manufacturing these types of products. It is essential that all members of the packaging supply chain co-operate with each other, and work together with knowledgeable ink manufacturers, and industry associations (eg EuPIA). Many other printers and brand owners could definitely benefit and challenge market share if they were to adopt a proactive approach to food packaging safety, before legislation takes shape, in the form of making risk assessments already at the design stage, to determine what requirements there are for printing inks and varnishes.
This article was published in L&L issue 3, 2011
Stay up to date
Subscribe to the free Label News newsletter and receive the latest content every week. We'll never share your email address.