Print on the cutting edge
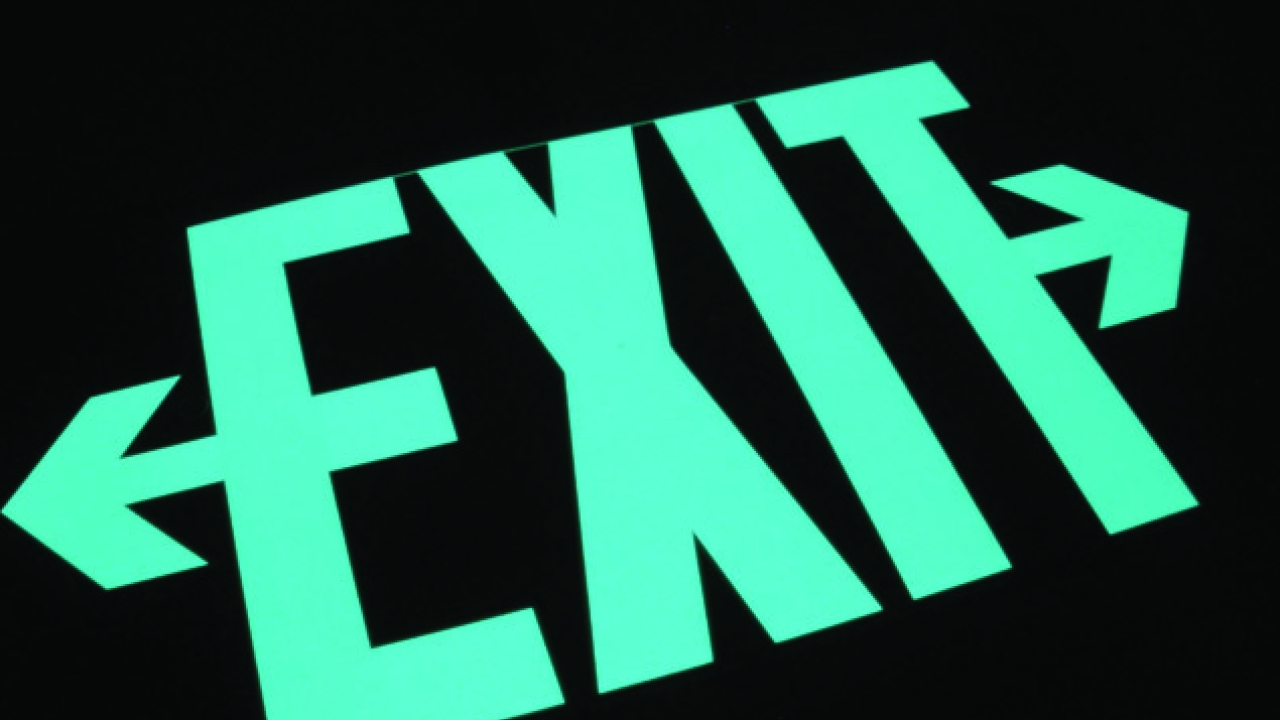
GSI Technologies has leveraged cutting-edge engineering techniques to develop a range of unique functional and electronic print solutions, writes Danielle Jerschefske
Functional printing and printed electronics are creating a buzz in the print community as challenges are overcome and new levels of quality and process control reached. GSI Technologies (GSI), located in Burr Ridge, Illinois, has blazed the trail for others to follow.
Brother and sister co-founders Bob and Suzanne Zaccone launched the operation in 1985 to produce prime and anti-counterfeit labels and polycarbonate overlays. The pair guided the business to profitable growth while maintaining a strong involvement in TLMI, having both served on its board. Among key personal qualities have been a willingness to put family before business, and the audacity to take risks to drive innovation.
Today, industrial graphics and prime label production represents only 15 percent of GSI’s business. The balance is a vast range of advanced functional printing products including strips to measure glucose for diabetics, electroluminescent lamps, smart card displays, sensors and automotive circuits.
Printed electronics is set to be a multi-billion dollar business. According to Frost and Sullivan’s World Printed Electronics Report, the market is projected to grow from $910 million in 2011 to $5.04 billion by 2016. The same research firm named GSI Technologies a ‘prominent participant in the medical sensors market’ last year.
Method to madness
To make the transition to a functional printing specialist, GSI needed to take on a different mindset. In the early years GSI had seven sales people and no engineers on staff; now the business has one salesperson, two business managers and employs a staff of engineers with expertise in materials, electronics, process and quality control, and different product-specific areas.
Printed electronics is not primarily about reducing cost, explains Suzanne Zaccone: ‘What we develop at GSI is not considered disruptive, because it is typically not replacing something that is currently in the market with something that is cheaper. Our work is far more encompassing. We’re adding value and finding success by enabling a product to be produced that could not have been done any other way.’
GSI must be able to help overcome a problem in order for its solutions to be viable. For example, printed batteries are often touted as a more environmentally friendly alternative to coin cell batteries. But it is difficult and far too costly to attempt breaking into a market with affordable infrastructure and solutions already in place.
GSI is looking for something unique, like a requirement for a printed battery of a specified thickness. Ideally the design is nearly complete with a few hurdles to overcome in either form or function. GSI business managers are technically minded, allowing them to communicate directly with their engineering peers to filter through the business concept and help in the final design and development.
To drive such innovation, GSI has made major investments in equipment, engineering capital and quality systems, all dedicated to scaling up promising ideas to commercial reality.
Says Jack Kraemer, president of GSI Technologies, ‘our investments have brought more science and less art to the processes involved. You must be able to follow the rules for science to work correctly. Our objective is to have predictive production for whatever we’re manufacturing.’
Engineering handles the layout of the complex multi-layer constructions of high-cost consumables that can cost as much as $30 per ounce. The risk is high, which is why the converter works on the value proposition right from the get-go.
Four manually fed screen presses are used to create prototypes and low volume orders as projects are massaged into viable, marketable business solutions. Cylinder screen presses then lay down one layer on each pass to create the final product. Roll to roll production is utilized for high volume applications where customers wish to perform downstream operations in roll form. All lines are equipped with camera systems to monitor layer-to-layer registration to ensure each piece has dimensional consistency.
The dimensions of each deposited layer are critical in determining functionality. With the inherent qualities of some of the advanced coatings used, such as PEDOT:PSS [Poly(3,4-ethylenedioxythiophene) poly(styrenesulfonate)], thickness can directly impact electrical properties as well as characteristics such as light transmission.
Silver is used as the conductor of choice in printed electronic devices as it has the lowest electrical resistance, and therefore the highest conductivity.
Copper is a close second to silver in the low resistivity category, but is easily oxidized, limiting its usefulness. Any exposed copper surfaces, such as the surfaces of particles in inks, will oxidize, readily forming a highly resistive (low conductivity) copper oxide. The conductivity of printed inks containing copper oxide-coated copper particles is essentially zero. Still, new products have been introduced with pre-oxidized copper particles that convert to copper when printed. These systems show great promise for lower cost production in the future.
The GSI operations team uses a range of analytical tools including real-time SPC (Statistical Process Control) software, which works with the in-line inspection equipment. Team leaders located anywhere in the plant can access this frequently updated data for continuous improvement purposes.
After each functional layer is printed, an engineer reviews the designs and through a microscope compares the design to the print. Most recently GSI installed a 100 percent in-line verification system for testing electrical resistance and conductivity.
‘With in-line and end-of-line testing tied to real time feedback, we have the ability to run the production lines at targeted precise functional attributes,’ says Gordon Smith, CTO.
There is no tweaking allowed on-press. Each and every product going through the machine is manufactured with methodical accuracy. Operators are disciplined, given the data and tools needed to set the press to lay down the precise amount of material, which has already been tested and formulated to work reliably. While there is little turnover of associates within the company, less experienced and newer shop floor workers follow a lead and are paired with experienced engineers and line staff.
The converter has taken screen making in-house so it can control quality and provide quick turnarounds, allowing engineers to rapidly adjust the dimensions and thickness of each printed layer.
GSI moved into electroluminescent lamp (EL) manufacturing in 2003 with the acquisition of the assets of BKL Electroluminescent, moving the capital equipment to the plant in Illinois. The business manager, application engineer and the CAD leader have remained on-staff and continue to support the expansion of the business.
The converter produces commercial EL exit signs and night lights that light up when an electric current runs through the material. CTO Smith explains that EL is a cool light source emitting little heat. Combined with the high flexibility of EL lamps, the technology has an edge over popular LED technology in some applications. It takes about eight to ten layers in order to produce a functioning EL exit sign.
Business Development
Business development and project adoption is handled carefully. The converter isn’t always certain where new business will come from. For example, printed automotive circuits had not been on the strategic plan, but have proved a great fit for both client and GSI.
‘There are so many different applications that are being constantly evaluated,’ explains Bob Zaccone. ‘To some extent, how the business evolves, and where it develops, is due to a project first offering a market advantage and second fitting with GSI’s production capabilities.
Bob continues to say as he smiles knowingly at Suzanne, and she grins back, ‘You can lower the risk by keeping the right amount of balls in the air. It can be a scary and subjective process with a lot of technicality involved, which is why we take the time for proper engineering and accurate prototyping beforehand.’
‘Our goal is the same as our clients - to bring a unique product to market,’ Smith chimes in. ‘We desire to find projects which require significant uptime on press. The longer the process runs, the better we’re able to track the parameters. We filter through each business concept as it comes to ensure that the capabilities we offer will give a technical advantage to the product’s development.’
Screen Star
Screen printing is currently the best process for producing functional materials. Smith says, ‘screen printing has the widest printing window out of all the print technologies. Dry film thicknesses from a micron to several microns have successfully been produced on commercial products. Multi-layer stack structures are quite common.’ He explains that there are simply not enough specialist consumables available for other printing processes.
The integration of digital printing into the printed electronics sector is not yet a reality, but is a focus area for development. Explains Smith, ‘Digital printing offers the ability to deposit small amounts of inks and to change designs in real time. The disadvantage of digital printing is the very thin layer structures which result. Thin layer deposits directly lead to more resistive structures which can create design barriers in end applications. The next commercialization breakthroughs will likely be with flexography as new ink systems are beginning to enable functional products.’
Where next?
When Jack Kraemer became president of GSI five years ago, he brought in-depth experience of developing medical and surgical products for the healthcare industry. As the population ages, the company is looking to bring new diagnostic innovations to the doctor-patient relationship, allowing patients to be monitored remotely.
In fact, much of the development of GSI’s quality systems can be attributed to its participation in the healthcare market, where guaranteed performance and measurability are key requirements.
The Zaccones were eager to develop their traditional converting business into an operation that could produce unique and special printing that cannot be commoditized. They have achieved this with GSI. Armed with a team of esteemed experts, GSI will continue to position itself for and capture the opportunities that functional printing holds.
Milestones
2006 - Zaccones won prestigious TLMI Converter of the Year award
2010 – Suzanne Zaccone published A Random Interruption: Surviving Breast Cancer with Laughter, Vodka, Smoothies and an Attitude
Global dimension
The US market is not the only place functional printing is driving forward. There is significant government funding in the EU and particularly solid support from German universities, as well as a new project based in the UK you can read about in this edition of L&L. Korea too dedicates significant budget for printed electronics R&D. GSI was an early member of the Organic and Printed Electronics Association (OE-A), which groups domestic and international businesses under the German Engineering Federation (VDMA). The association hosts regular tradeshows and networking events to stimulate collaboration between all elements of the supply chain.
Pictured: Electroluminescent exit sign
This article was published in L&L issue 4, 2012
Stay up to date
Subscribe to the free Label News newsletter and receive the latest content every week. We'll never share your email address.