ISO comes to in-line color
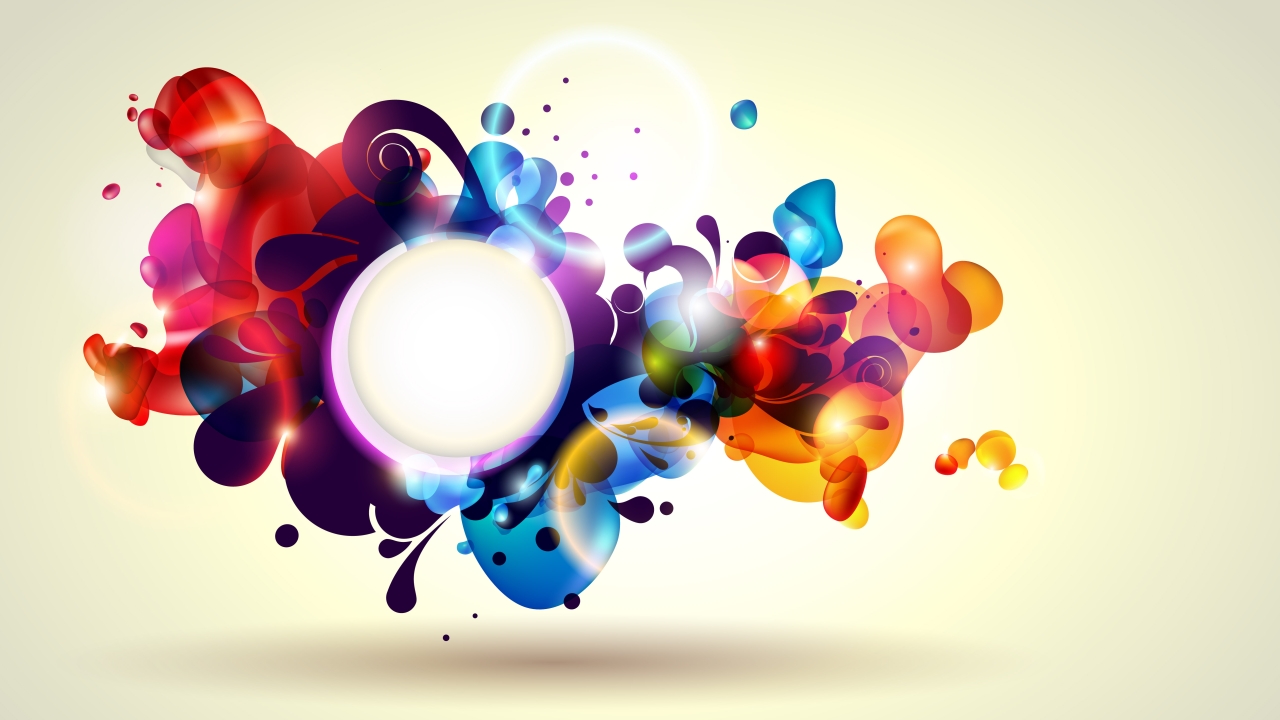
Achieving ISO compliance with an in-line spectrophotometer is a more difficult project than first appears. John Seymour, color expert at QuadTech, lays out the issues.
Conformity to global standards is the basis for ensuring the products and services we use are safe, reliable, and of good quality. The organization responsible for ‘benchmark’ global standards is the Geneva-based International Organization for Standardisation (ISO), which since 1947 has published over 19,000 voluntary standards concerning technology
and business.
In label and packaging printing, there is a need for globally recognized, objective color standards. Global brand owners expect the same color, from one print run to the next, wherever it may be produced. If we are to achieve predictable results in the most efficient way, irrespective of printing equipment or location, it follows that we need common standards to describe how we measure color.
Accurate color measurement is achieved with a spectrophotometer, which measures the light reflected from a sample in (typically) something like 30 slices from the rainbow. In-line spectrophotometers are proving to be reliable solutions for measuring light on web-fed packaging print. Using high powered software, they can take readings continuously throughout the production run, from a large number of image targets, with minimal human input and without stopping the web, at high speed.
These are rather complicated instruments which are defined by a number of standards – standards which are, even today, still evolving. Spectrophotometers which comply with the most recent of these standards have the best shot at agreeing with one another.
But do in-line spectrophotometers comply with the ISO standards for the graphic arts?
The relevant standards
One standard is the mother of all the standards for 'proper' printing in the graphic arts world: ISO 12647. This standard defines how printing should be done. There are several parts to this standard that refer to different types of printing. There are parts of the standard that pertain to web offset (part two), newspaper (part three), publication gravure (part four), screen printing (part five), flexo printing (part six), and digital proofing devices (part seven). There is not yet a corresponding standard for gravure packaging, or for packaging in general, but work is underway.
In terms of color measurement, there are two key specifications in this standard. First, there are target values for the color of the paper, the solids (C, M, Y, and K), and for the overprints, all measured as CIELAB values with tolerances given in terms of delta E. The second color-related specification is for tone value increase. Again there is a target value and a tolerance.
This standard, as is common with ISO protocol, is built on a number of other standards. The plumbing diagram shows the standards most relevant to color in graphic arts. To be compliant to ISO 12647, all of the other pieces must be adhered to. ISO 12647 references other standards that cover ink manufacture, viewing booths, and color measurement.
In order to comply with 12647 printing, you must use inks that comply with the ink standard, ISO 2846. This standard describes the target colors (CIELAB values) for each of the process inks, as well as a host of other properties. Like 12647, the ink standard has multiple parts for different types of printing. [The 2004 version of 12647 suggests but does not require that the inks comply with ISO 2846, but the most recent draft of the revised version does require this.]
The color you see when you look at a print depends on the light that is shining on the print. A proof and a press sheet may match outdoors under sunlight, for example, but not in your living room under incandescent lamps. So, in order to assess whether there is a match, you must standardize on the illumination in the viewing booth. ISO 3664 defines this.
Color measurement (CIELAB) is defined in the CIE 15 standard, and specifics of the measurement for graphic arts are laid out in ISO 13655.
Color measurement standards
There are two key standards that cover color measurement, one of which is more or less irrelevant. The earliest of these color standards is ISO 5. (Note the low number!) This defines how a densitometer measures ink on paper. Years ago, when the color of print was specified in terms of density, ISO 5 was a critical standard.
Density is simple and easy to understand. Unfortunately, a density value does not uniquely define a color, so it is somewhat lacking when it comes to specification of color. Because of this, the mother of the print standards, ISO 12647, defines the color of patches in terms of CIELAB values instead of density. That is to say, compliance to ISO 12647 does not require a spectrophotometer to comply with ISO 5.
This does not mean that density is unimportant. In fact, ISO 12647 recommends (but does not mandate) that the printer establishes a target density value for every combination of printing ink and substrate, preferably at the start of the print run. With that target, density can then be used for process control. Density may not be used to demonstrate compliance.
The other key standard for measuring color is ISO 13655, which defines how a color (CIELAB) measurement device works, and how to compute CIELAB values. I will explain this a bit further, but first, there is a bit of a history lesson.
Measuring density
The 'old' version of ISO 5-3 (from 1995) specified that a densitometer must use an incandescent bulb as its light source. This is the light source used in almost all handheld densitometers because it is inexpensive, relatively stable, and well-understood.
One of the problems with this standard is that, while the light source was defined, the spectral power distribution (the relative amount of light hitting the sample at each wavelength) was not. This was not an oversight by the standards committees, but rather an intentional compromise to accommodate the variety in existing spectrophotometers.
Two spectrophotometers that use incandescent bulbs may use different filters between the light and the sample. Incandescent bulbs irradiate a lot of heat and damage a sample, so one company may decide to filter this out. Incandescent bulbs put out considerably more light at the red end of the spectrum than at the blue end, so another company may decide to balance this out by using some sort of bluish filter to knock down the red. Still another company might decide to add a filter to eliminate UV light in order to eliminate the effect of fluorescence.
Another problem with this standard is that an incandescent light source is completely impractical for an inline device. If a handheld densitometer required a tenth of a second to make a measurement, there would be no complaints. But for an inline system on a web moving at 3,000 feet per minute, five feet of web would get blurred past the detector in that time period. Just like a camera taking pictures of quickly moving objects, an inline measurement device needs to have a strobe light to freeze the motion of the web. The length of a strobe pulse should be in the order of microseconds to measure a small color patch.
Thus, there are no inline spectrophotometers that comply with the 1995 version of ISO 5-3. This is not a compliance issue, since the newer revision (ISO 5-3:2009) does not require an incandescent bulb, but the basic problem remains that the light hitting the web for an inline measurement will be different from the light hitting that same sample when measured off-line.
New lighting conditions
ISO Technical Committee 130 (the committee that writes the standards for printing) has recently been wrestling with the print assessment issues revolving around the use of optical brightener agents (OBAs). OBAs are one cost-effective way to make a paper brighter by boosting the light at the blue end of the spectrum. An OBA will absorb UV light (which we can’t see) and re-emit that light at the blue end of the spectrum.
The use of OBAs to make paper white has increased steadily to the point where, today, it is difficult to find paper without OBAs. This is a good thing in that a brilliant white paper can be manufactured cheaply, but not so good in that it causes problems with the visual and measured assessment of color. These assessments depend on the amount of OBAs in the stock, and the amount of UV in the light source. Both of these vary.
It is important to note that non-paper substrates do not generally contain OBAs, but this may change!
ISO TC 130 has addressed this issue by changing all the related standards: the densitometry standard (ISO 5-3), the viewing booth standard (ISO 3664), the spectrophotometer standard (ISO 13655), and the printing standard (ISO 12647). These changes have more precisely defined the UV content of standard illumination so that all viewing booths and spectrophotometers will have the same degree of fluorescent enhancement.
For a spectrophotometer, revising the standards is a bit more complicated. It was recognized by the committee that there are a large number of spectrophotometers in use today, so an abrupt change to the standards would be met with resistance.
The updated version of ISO 13655 and ISO 5-3 define four so-called 'measurements conditions', called ‘M0’, ‘M1’, ‘M2’ and ‘M3’. Of these, M0 and M1 are relevant for package printing.
The M0 condition is the 'loophole' that allows basically all existing spectrophotometers to– in legal parlance – ‘grandfather in’, or comply to a differing agreement from that which is already in place. It specifies that an M0 light source be what is called 'Illuminant A', which resembles an incandescent light bulb. This may at first seem to preclude the strobe lights that are used by inline spectrophotometers, but there is one tiny little word that opens this up. The standard says that the relative spectral distribution should conform to illuminant A. That word, should, is an important word in a standard. It is a 'reserved word' that is used to clearly delineate a recommendation that is not mandatory. By virtue of this one little word, any light source may be used in a spectrophotometer, so long as the spectrophotometer is identified as M0.
Compliance with the M0 lighting in ISO 13655 does not ensure that one instrument will agree with other M0 instruments when the substrate has optical brighteners. Compliance to M1 ensures agreement with other M1 instruments.
The M1 condition is met when the illumination of the spectro provides the amount of UV light which is defined as 'D50' illumination. This is one of several standard illuminants that resemble various 'shades' of hypothetical sunlight.
Finally, the mother print standard (the ISO 12647 series) has not yet been updated since the changes to the other standards, so it is a bit difficult to say what will constitute a 'valid spectrophotometer measurement' if one is required to be compliant with the print standard. Many parts of 12647 are currently under revision, and the most recent include the provision that M1 be the preferred condition, and that M0 is also allowed.
Where are we now?
When printing on substrates without OBAs, the changes to ISO 3664 and ISO 13655 have little effect. But, when OBAs are involved there are numerous issues caused by the transition.
People who buy paper will continue to be impressed with the price and brilliance of paper with OBAs, as well they should be. Manufacturers of proofing paper will continue to be confused by the conflicting messages of 'don’t use OBAs', and 'use the same amount of OBA as whatever paper I decide to put on press'.
Owners of viewing booths have been (or will be) transitioned automatically. In most cases, when the bulbs are routinely replaced in a viewing booth, the resulting viewing booth will comply with the new standard. This may be a surprise, since viewing booths will generally have more UV content as a result of the new standard. This will, of course, accentuate any existing differences in OBAs between proofing stock and press sheets.
For owners of spectrophotometers, the transition is not as automatic. Clearly, an M0 spectrophotometer that has not been sent back to the factory will remain an M0 instrument. If this instrument is sent back to the factory for repair or for periodic calibration, it may or may not be upgraded to M1. Please check with your spectrophotometer manufacturer. If you buy a new spectrophotometer, it may be M0, M1, or it may have an option for either.
Since M1 instruments are rather scarce right now, it is likely that in any print shop today the UV portion of the illumination in the viewing booth will not match that of the spectrophotometer. During this transition period, this will be a potential problem.
Another, less obvious transition is the transitioning of data. Any standardized target CIELAB values for process colors and spot colors may need updating. This includes ICC (International Color Consortium) profiles.
The printers who buy the in-line systems (and the brand owners that drive the purchase) quite naturally want the system to agree with whatever offline spectrophotometer has already been decided upon. This may, of course, be an M0 instrument or an M1.
Manufacturers of in-line spectrophotometers have a bit of a conundrum. Since the standards no longer explicitly require an incandescent bulb, it is now possible to build an in-line device that can be considered M1 compliant. More importantly, with the proper amount of UV, it will agree with an M1 spectrophotometer.
But on the other hand, the reference offline spectrophotometer might be an M0 instrument. In this case, complying with the rather loose specification for the UV component will not insure agreement with other M0 instruments. Unfortunately, each M0 instrument will require its own special adjustment of UV content.
Ultimately moving to the new standards will reduce the general problem caused by OBAs, but the transition may not always be smooth. Transitioning only a few of the pieces may make color matching temporarily worse. All of the updated pieces must be put in place for the entire workflow to provide the most accurate color possible.
Some definitions
CIELAB values are a standardized way for measuring color which is based on human perception. The value of a color is uniquely identified by three numbers:
L* - which represents the brightness of an object.
a* - which represents the extent to which the object is viewed as reddish (positive a*), greenish (negative a*), or neither reddish or greenish (a* of zero).
b* - which represents the extent to which the object is yellowish (positive b*), bluish (negative b*), or neither yellowish or bluish (b* of zero).
A s E (pronounced “delta E”) is a measure of how far apart two colors are.
Tone value increase or TVI has historically been called “dot gain”. It is computed as the difference, in percentage points, between the intended dot and the apparent dot, based on the reflectance. If a 50 percent tone value in the file comes out looking like a 65 percent tone value, then we say the TVI is 15 percent.
About the author
John Seymour is an applied mathematician and color scientist. He works in the role of principal research engineer for QuadTech, where he has been doing advanced product development for 20 years. He holds 17 patents and has written over 20 technical papers. He has served on the US printing standards committee (CGATS), and the international printing standards committee (ISO TC 130) for over 10 years.
This article was published in Labels & Labeling issue 6, 2012
Stay up to date
Subscribe to the free Label News newsletter and receive the latest content every week. We'll never share your email address.