Uflex manufactures glitter printing rotogravure cylinder
Uflex is the first Indian company to manufacture a glitter printing rotogravure cylinder on its direct laser engraving line.
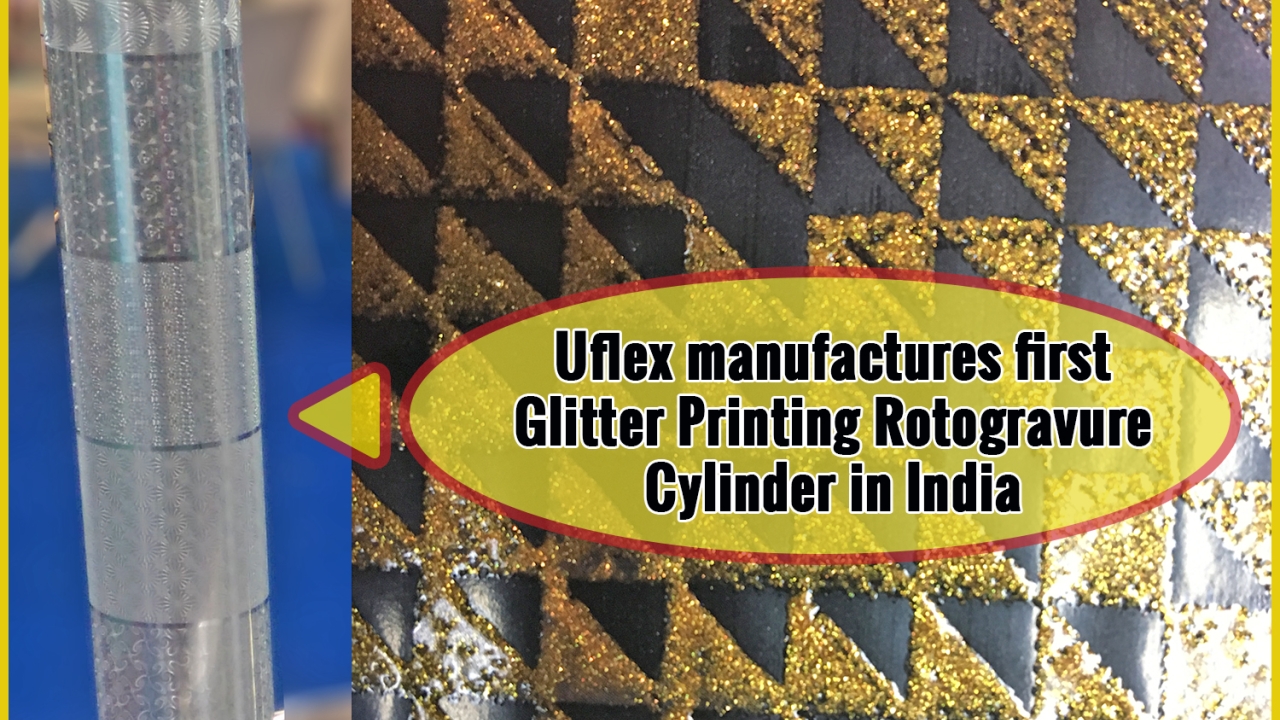
‘It is extremely difficult for a cylinder with electro-mechanically engraved conventional gravure cells to pick up pigments of glitter ink and transfer them on to the substrate because pigments of glitter inks are substantially bigger in size as compared to conventional gravure inks,’ explained P K Agarwal, joint president of the cylinders business at Uflex. ‘Therefore, we developed bigger sized customized pits or cells that trap a high solid content of glitter ink for this specialized cylinder.
‘The cell geometry of the rotogravure cylinder has been customized on our direct laser engraving line. When the printing surface is sandwiched between the impression roller and the gravure cylinder, high solid contents of the glitter ink are transferred from recessed cells to the substrate with the help of capillary action and the tangential force of the roller.’
The specialty glitter ink has been manufactured for flexible substrates like paper and heat sensitive films and can be cured using LED lamps applied in-line with the gravure printing process using solvent or water-based ink systems. Uflex manufactures different variants such as metallic glitter and polymeric glitter inks, among others. Conventional metallic shades are available only in gold, silver and copper, whereas polymeric glitter inks are available in several colors.
Agarwal added: ‘Glitter inks, unlike other conventional gravure inks, do not possess self-curing properties. Therefore, to enable quick and effective curing of glitter ink, we developed a LED curing system and installed it on printing machines at Uflex. Solid content of glitter ink on the printing surface imparts a superior tactile effect along with the shimmer, thereby enhancing the shelf impact of the pack. It took us about a month to develop the glitter printing rotogravure cylinder. Our chemicals business simultaneously developed the glitter ink.’
Rajesh Bhasin, joint president of the chemicals business at Uflex, said: ‘This was one of the toughest challenges posed to us by our client, wherein we were asked to develop glitter ink for a variety of flexible substrates including heat sensitive films. This ink was required to perform at high speeds and cure quickly on a gravure press.’
Agarwal concluded: ‘We see great demand for this type of printing from convertors of flexible packaging for high impulse buying consumer goods, particularly in the food and confectionery segment, for which we are fully braced.’
Ashok Chaturvedi, Uflex chairman and managing director, added: ‘Addressing a need gap congruently is the real contribution that the manufacturing industry can ever deliver. Our cylinders and chemicals businesses demonstrated perfect synergy and engineered the most contemporary and innovative glitter printing cylinder and inks in record time delighting our clients.’
Stay up to date
Subscribe to the free Label News newsletter and receive the latest content every week. We'll never share your email address.