Offset pioneer
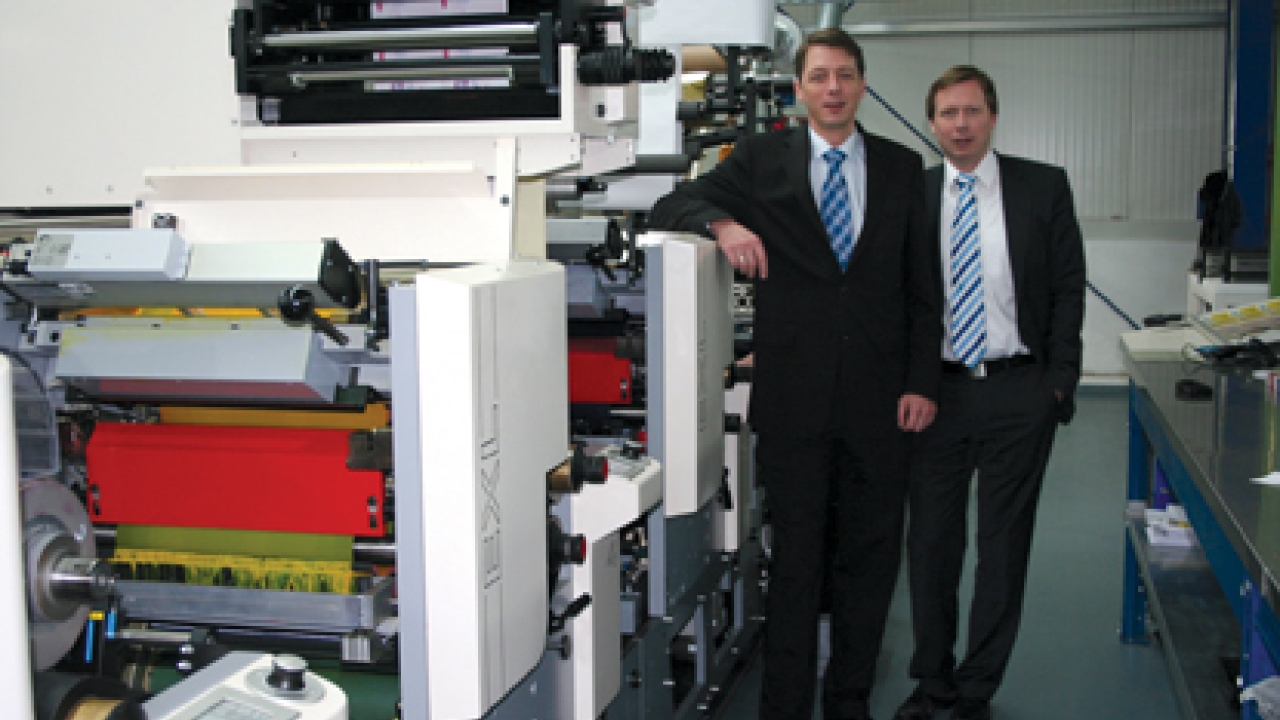
Optikett was among the first converters to install the new MPS EXL UV web offset press. Andy Thomas reports on the company’s early experiences with this innovative machine
It takes a company with a pioneering spirit to become an early adopter of radical new technology. Optikett is just such a converter, and recently became only the second European company to install the MPS EXL, a variable sleeve web offset press which introduces some novel concepts in print unit design.
The Ostendorf group of companies was founded in 1968 in Vechta, Germany, as a sheet offset company. In the mid-1980s Ostendorf expanded into business forms, setting up the Optiform division. In 1989 the company’s biggest customer moved from sheetfed to self-adhesive labels, and to keep the business, a new roll labels division was established with Arsoma flexo presses and a Rotoflex rewinder. There remains today a small amount of sheetfed labels business – mainly for honey and jam labels – but overwhelmingly the labels business has moved to pressure-sensitive rolls.
In 1994 Optikett consolidated its operations onto one site and sold the Optiform division as the business forms market slumped. In the same year the company constructed its own UV offset machine based on a Rotatek RK100, because at that time a UV offset machine for labels was not commercially available.
‘My father came from an offset background and was looking for that quality in the roll-fed press,’ says Daniel Ostendorf, who along with brothers Mathias and Frank runs the Optikett business. ‘We were the first company in Germany to print labels and foils in UV offset, and in the beginning it was not an easy thing to do, because of the lack of the right inks.’
As the quality of UV flexo improved, Optikett bought its first MPS press, an EP410, in 1999/2000 in combination with a laser engraving system for flexo plates. A key factor was the ability to print high quality flexo and screen in the same station.
‘And we switched many costumers from the offset quality to this new flexo quality,’ says Daniel Ostendorf.
‘But the demand for best printed labels was still rising, so Optikett decided in 2006 to get a new offset machine with sleeve technology,’ continues Daniel. ‘The machines in the market didn’t satisfy Optikett, so we started in 2006 a new machine technology with Rotatek. This ended in 2008 with the new Rotatek 520 Universal, specifying variable sleeves for the machine rather than fixed cylinder inserts.’
By the end of 2011 Optikett employed 75 people, working two shifts on the sheetfed side and two to three shifts on the labels side.
Back to the future
With UV flexo proving such a high quality print process, why did Optikett choose another UV offset press? ‘Over the last year the market has started to change,’ says Daniel Ostendorf. ‘More customers wanted UV offset. Lidl in particular now requires UV offset, and Aldi will probably go the same way.’
A key requirement for the new offset press was variable sleeves to cope with the wide range of label repeat sizes required by the company’s food industry customers. After extensive trials, Optikett opted for the new MPS EXL offset press, which was installed in October 2011 shortly after its launch at Labelexpo Europe. This is now the fourth MPS Press at Optikett.
‘We decided for this machine concept, because the change over time is quicker compared to the Rotatek and the printing quality is on the same level,’ says Daniel. ‘We wanted to have a machine for the middle run length jobs. Our Indigo is for the short run, and the Rotatek for the big jobs.’
The 7-color 410mm (16in) MPS EXL press measures 12 meters, compared to the 25 meters for the 9-color Rotatek. The EXL press prints at speeds up to 200 m/min and repeat size is infinitely variable between 18-25 inches. ‘The machine is in register and color within 250 meters,’ says Daniel Ostendorf. ‘Another advantage of the machine is the ease of use, so we brought one of our flexo press operators with no previous offset experience to work on the MPS EXL press and he was able to set up and run the press within a few weeks. We are also very satisfied with the service from MPS. If you have got a machine problem, it is mostly solved by MPS in one day.’
Variable sleeve
While MPS’ first offset press was a traditional fixed cylinder machine with inserts, the EXL is built from the ground up as a sleeve-based, variable repeat press using MPS patented technology.
Most importantly, the EXL press does not require bearers to ‘lock together’ the plate, blanket and impression cylinders to give the press stability. Instead, the plate cylinder is locked into the inking train – with inking roller contact controlled by pressure sensing technology – and the blanket sleeve is moved automatically into contact with the plate. Changes to blanket position can be made on the fly without stopping the press.
The free running steel impression cylinder moves independently to adjust for changes in substrate thickness. ‘This is the same technology used in MPS UV flexo presses, a free running impression cylinder to create a frictionless print momentum and removing a potential source of gear marking or baring,’ says MPS joint managing director Eric Hoendervangers.
This design concept, with automated print pressure setting, allows the printer to make use of ‘normal’ sleeve technology without the need for special support bearer rings or any other form of mechanical support. Optikett, for example, is using the latest ‘off the shelf’ lightweight aluminum sleeves from Spilker, which are mounted off-line on a Sleeve Service Station, which MPS developed together with AVFlexologic.
This cylinder arrangement also eliminates the differential build-up of heat between bearer and sleeve, which can affect the stability of the print unit and requires constant correction by the press operator.
Automation
The EXL is highly automated, and inherits from the MPS UV flexo press line both APC (automatic print control) and iControl. MPS recommends that users undertake calibration of the different substrates the press will run. This variable affects a range of parameters including ink key setting, impression cylinder setting, ink/water balance curves, and the frequency and dwell time of the ductor roller, automated per material and job. All pressure, ink, and water balance settings are servo driven and can be uploaded from the job memory.
The EXL is a combination press, and like the other machines in the MPS press series, uses a rail system to change the position of any print process unit. Optikett’s EXL press is configured with five offset color units, one fixed flexo unit and rail-mounted flexo and cold foil units with a turnbar. Rail mountable screen and hot foil units are also available, along with a fixed gravure station.
Digital options
Complementing Optikett’s conventional label presses is an extensive digital offering for both labels and commercial print. This includes wide format inkjet printers, a sheetfed HP Indigo 3050 and an HP Indigo WS6000, which replaced a WS4050, with finishing handled on a GM unit.
‘The cut-off against flexo for the HP Indigo WS6000 is somewhere around 2,000 meters in 7-colors,’ says Daniel Ostendorf. ‘Although it does depends on format and the amount of different designs.’
Optikett is also equipped with a complete pre-press facility, starting from design to digital plate production for flexo, offset and screen printing.
Pictured: Matthias and Daniel Ostendorf with the MPS EXL offset press
This article was published in L&L issue 1, 2012
Stay up to date
Subscribe to the free Label News newsletter and receive the latest content every week. We'll never share your email address.