Pacificolor upgrades to Miraclon’s Shine LED Lamp Kits
Beta testing site enjoys productivity and sustainability gains.
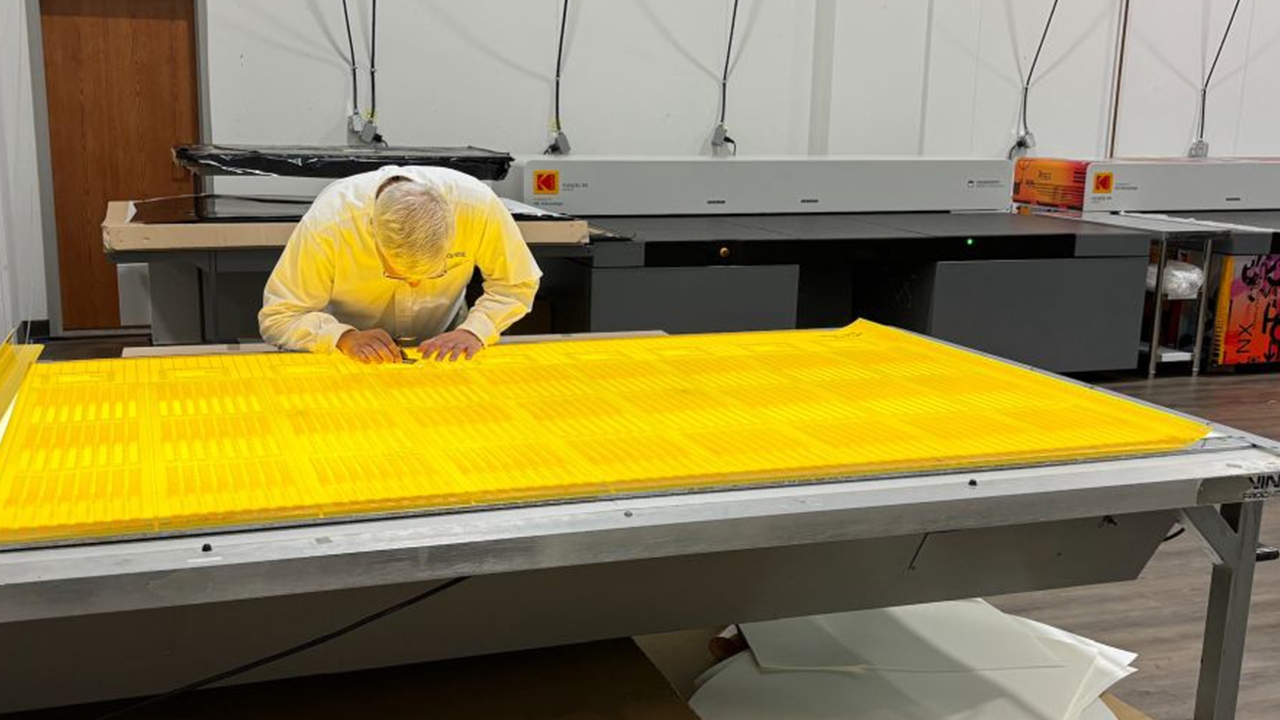
US-based flexo packaging trade shop Pacificolor has invested noting significant production and sustainability gains after upgrading from fluorescent exposure to LED technology with a Shine LED Lamp Kit, innovated by Miraclon.
The Shine LED Lamp Kit is known as a simple, low-cost route to the multiple benefits of LED exposure, necessitating just a straightforward retrofit upgrade to existing fluorescent exposure frames.
‘We’re experiencing faster, more consistent plate exposure times and reduced maintenance. These add up to greatly enhanced productivity in the plate room across the group for a fraction of the cost of alternative routes into LED. In addition, and important from the sustainability perspective, it’s all achieved by ‘upcycling’ our existing equipment,’ said Nick Brunk, Pacificolor’s chief revenue officer.
According to Miraclon, LED lamps offer significant advantages over fluorescent tubes. They last longer — 5,000 compared to 800 hours — with intensity remaining consistent over time.
LED technology also increases productivity as exposures are not only consistent, but up to 20 percent faster, because the lamps warm up and cool down instantly.
Sustainability is enhanced due to reduced waste, lower power consumption and lower disposal costs.
Approached by Miraclon to evaluate the Shine LED Lamp Kit, Pacificolor did not hesitate to act as a beta site.
‘Fluorescent exposure technology is on the way out, and the tide has turned in favor of LED,’ added Brunk. ‘Beta testing gave us the opportunity to confirm our instincts and prove the benefits of LED. Routine measurement of UV output showed no fluctuation in the power the LEDs were putting out.’
Tim Hirsch, owner and CEO of Pacificolor, commented: ‘The installation of Shine LED has proven to be exceptionally straightforward, seamlessly integrating into our production processes. It has emerged as our preferred exposure solution, primarily due to the notable enhancements it has brought to plate uniformity and efficiency.
‘By adopting Shine LED, we've successfully eliminated the variables associated with fluorescent UV tubes, resulting in consistency across every plate. Our operators have expressed their satisfaction with this change, as they no longer have to wait for lamps to warm up, and the change in exposure times, leading to an overall improvement in productivity within our plate room.’
The company was an early adopter of Flexcel NX technology from Miraclon, and has successively upgraded imaging formats from narrow- to mid- and now wide-web.
Pacificolor has also quickly leveraged the latest imaging technologies, including PureFlexo printing, the most advanced iteration of advanced plate surface patterning technology from Miraclon, and screening technologies ProjectBlue and Vortex, developed by our Reproflex3.
‘Switching to LED exposure is in line with our technology due diligence,’ said Brunk. ‘This confirmed the shortcomings of fluorescent tube exposure technology, principally the consequences of tubes degrading over time, and at different rates. The resulting risk of inconsistent exposure means we spend a lot of time on process control and maintenance to avoid poorly exposed plates and remakes.
‘Between flexible packaging and corrugated, we’re exposing a variety of different reliefs, some deeper than others. Getting consistent fluorescent exposures means following a stringent process to make sure you’re getting the power from the bulbs that you need. This can mean significant downtime.’
Stay up to date
Subscribe to the free Label News newsletter and receive the latest content every week. We'll never share your email address.