Telrol sets the pace
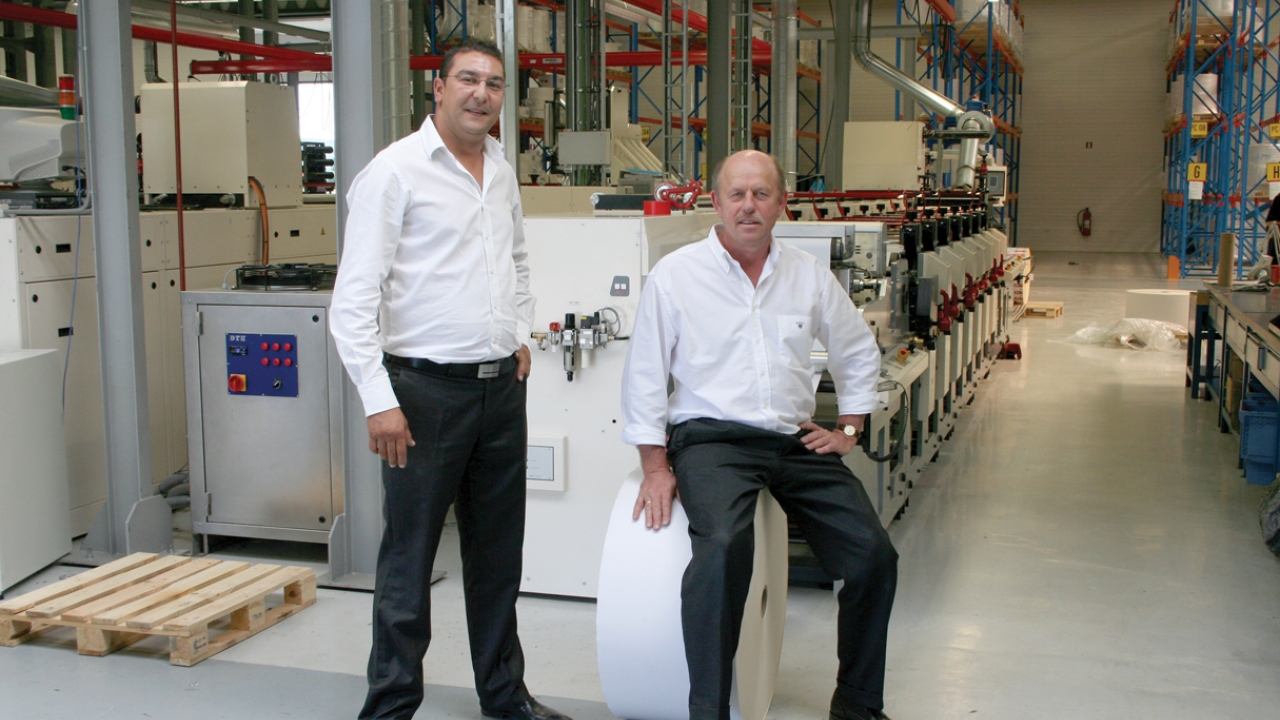
One of Europe’s biggest and most efficient label converters is looking to make its mark on the world stage. Andy Thomas reports
Dutch-based labels powerhouse Telrol works for some of the biggest names in global retailing but has kept a relatively low public profile. According to joint owners, Ton Jacobs and Hoessein Hadaoui, this is set to change. The company is moving to position itself as a major global player in market sectors, from fresh foods to pharmaceuticals and cosmetics.
With an approximate turnover of 30m euros and projected sales growth of 40 percent in 2011, Telrol claims to be the biggest label converter by volume in Holland and the Benelux. In June 2009, the company acquired Peha Labels from CCL – next door to its Almere plant. Telrol undertook a 10m euro capital spending program - completely refurbishing the building in just three months and investing heavily in MPS press technology. MD of the former CCL, Peter Maaskant remains with the company.
Telrol’s label converting operations are organized in the Labelmakers Group and members act as a center of excellence for different market sectors.
Telrol itself specializes in food, fresh produce and retail, recently achieving BRC/IOP food hygiene certification. The Peha operation focuses on pharma and cosmetics labels, including a secure working area which doubles as a security labels operation. Labelpoint supplies retail labeling systems including thermal transfer printers and consumables, barcoding systems and enterprise software, and the Biolabel division supplies (PLA) biodegradable labels which conform to the EU’s EN13432 composting standard.
The Labelmakers Group, including two logistics plants, employs 170 people and runs 43 machines across a total floor area of 26,500 sq m. Telrol has its own tool making plant capable of manufacturing high spec cylinders and gears.
The expertize of its customer service representatives sets Telrol apart from many of its competitors. ‘We do not employ sales people, we employ consultants who are experts in their field. Our sales are what comes in through the door,’ says Hadaoui. ‘If they deal with fruit, for example, they will know where strawberries come from, where and how they are grown and how they are stored and distributed. It is the same if you deal with poultry, fish or any other fresh product.’
Global reach
Market trends in the fresh food and retail sectors are pushing Telrol to extend further into Europe and Africa, where the company is now looking for partners. ‘The world is definitely getting smaller and we need to be present in countries like Spain, Italy, France, Egypt, Kenya and Morocco,’ says Hadaoui.
‘The major retailers are looking to get fresh produce into their stores faster and more cheaply. Instead of us providing labels to contract packing houses, they want us to help the farmers pack their own produce.’
When L&L visited Telrol, Hadaoui had just returned from Egypt on a project to advise a farmers’ co-operative on automating their packaging operation. ‘There were 500 people doing the packaging by hand. They needed an automated label applicator and a new range of labels suitable for automated application,’ says Hadaoui.
‘If they want to supply the big supermarkets in Europe, they just have to invest in new software and labeling systems which pack the right product for the right location. We are now sending millions of direct thermal or thermal transfer labels a year to this one site.’
In an important new trend, retail groups are looking to eliminate labels on fresh food products with a known weight. ‘They want to wrap fresh produce and print the weight on the film rather than adding price-weigh labels,’ explains Hadaoui. ‘This is already being done by some major UK retailers – for example flow packs of tomatoes at Asda, where all the nutritional and weight information is printed on the film.’
Some of Telrol’s biggest customers have promised to support the converter in making this transition over the next two years. The company is considering adding a web offset capability to handle films as well as carton sleeves.
‘Our label business will always exist, but in the future we want to supply our customers with the whole package, whatever the format or print process required,’ says Jacobs.
‘We will have a lot to learn about printing on materials like gas barrier films, including issues of ink migration and how these films stretch on the press. But with our customers’ support we see great opportunities in these areas.’
Telrol’s MPS UV flexo presses have been specified with chill rolls and heat management packages. ‘We already use the MPS presses for film, and the quality is fantastic, for example when you are reverse printing,’ says Jacobs.
Print technology
Telrol is MPS' biggest Dutch customer, with eight Effective Flexo (EF) presses in both 330mm and 410mm web widths and in configurations between 5- and 9-colors. On the 8- and 9-color machines, Telrol’s expert operators can make ready on the non-printing stations while the rest of the press is running. Unlike line shaft machines, servo control allows print units to be started up and shut down independently of the press line.
The presses are organized with three operators for each pair of machines, with one operator moving to whichever press is making ready.
Telrol largely uses Gallus presses, including three EM280s, four EM410s and one 8-color EM510 with turret rewinder. When the Peha plant was acquired, Telrol inherited four older letterpress machines, which were soon joined by four fully loaded MPS EF 410 presses when the plant was refurbished. The company still uses its R200 letterpress machines – 9-colors plus three screen units and hot foil – for complex cosmetics labels.
Matrix waste is taken away by a factory-wide suction system supplied by Matho, it links each press to ducts which transport the waste to a skip outside the building.
In January 2010 Telrol moved into digital printing for the first time, with a Xeikon 3300 featuring an off-line Digicon finishing unit. After Labelexpo Americas, Telrol took delivery of an EFI Jetrion 4830 inkjet press.
Off-line finishing systems include five Grafotronic rewinders fitted with inspection cameras, as well as FIT blank label converting systems. The cameras take their ‘master image’ from the approved PDF file via the CERM MIS. A ‘roll report’ is sent to the rewinder after the defective images have been verified and the rewinder stops automatically at each defective label.
Super-Lean
Telrol’s highly complex production operation is controlled by an extremely advanced implementation of a management information system (MIS) from CERM. Telrol employs three staff full time to control process management issues - including real-time planning and machine monitoring.
‘We invested a lot of time building a model of what we want to achieve and making sure people have the tools to use it. This is important – you must take your people with you,’ stresses Hadaoui.
The planning system deals with 1,000 orders a week, with work normally planned 2-3 days in advance.
The company uses a ‘train network’ analogy to describe the workflow. Jobs – ‘trains’ – run either on the fast or slow track depending on the priority assigned to them. Each job is scheduled to stop at a number of stations – pre-press, plate making, ink mixing, plate mounting, printing and finishing. At each station the CERM MIS advises operators on what jobs are coming down the track, their priority and what operations need to be carried out.
Machine monitoring is a recent implementation. ‘We can see in real time which machines are running, how fast they are running and the costs of each machine,’ enthuses Jacobs. ‘This works together with the roll materials tracking module which gives every roll a unique code which stays with it from goods-in through the plant. The system ‘knows’ how many meters are on the roll and counts down from when the press starts running. If the press stops before the end of the roll, the system notes how much material is left, and prints out a label with the new length.’
The CERM MIS has also reached out to Telrol’s customers, who can log in securely and see the production and stock status of their labels along with a full technical specification. The CERM system even connects to Telrol’s GPS-enabled transport fleet. Click on a truck on screen and you can see what time it is due to arrive – ‘some customers want to know whether their labels will arrive at 9am or 11am,’ says Hadaoui.
The next major investment will be a fully automated materials handling warehouse, which will pick and transport rolls of material to the production floor, move finished rolls back into storage or dispatch them.
Telrol has grown rapidly over the last few years, making them one to watch on both the European and wider world stage.
Pictured: Hoessein Hadaoui and Ton Jacobs
This article was published in L&L issue 6, 2010
Stay up to date
Subscribe to the free Label News newsletter and receive the latest content every week. We'll never share your email address.