Sheet-fed automation pushes IML and wet glue forward
Sheet-fed technology for the production of wet glue and in-mold labels has moved forward in leaps and bounds in terms of automation, efficiency and the ability to add value during in-line production.

Rapida 106 X in a typical configuration for label production - seven printing units, RS 106 X reel-to-sheet feeder, cold foil module, in-line coater with AniloxLoader and extended delivery
The great bulk of in-mold (IML) and wet glue labels are printed on sheet-fed offset presses. For some high-volume markets such as metallized beer labels, gravure is the preferred choice, and there is some in-line flexo production of IML. Still, generally, sheet-fed offset is dominant for both wet glue and in-mold labeling formats.
Wet glue labels are experiencing strong growth in industrialized markets. Consultancy Research and Markets estimates the paper glue-applied labels segment will reach a value of USD 19.7 billion by 2030, with a CAGR of 4.5 percent year over year from 2013.
Finat’s quarterly Radar survey of trends in the European market showed wet glue labels surged by 14.6 percent year over year in Q3 2024, though this was still slightly behind Q3 2022 levels. This represents lingering economic uncertainties and cautious consumer spending, which are impacting the broader package printing sector. The beer segment in Europe is the biggest driver of wet-glue growth, bolstered by continued demand for premium and non-alcoholic beer categories.
IML continues to be a strong niche market. It’s share of the global labels market has hovered unchanged at around 2 percent for many years, with the European IML market estimated to total around 24,000 tons per year. Finat’s Q3 Radar report shows IML recording a modest year-on-year growth of 0.5 percent.
In Europe, food remains the largest end-use segment for IML, largely due to its extensive application in products such as margarines, yellow fats, ice creams, yogurts and salads, where the IML format dominates. A slowdown in the food segment primarily impacted year-on-year growth in Europe. At the same time, industrial chemicals, the second-largest application for IML, experienced a slight upturn in demand driven by the ongoing post-pandemic recovery in this sector.
Sustainability is expected to drive the growth of IML in Europe as brands look for mono-material packaging. Sustainability concerns could also boost wet glue label growth.
Technology landscape
The sheet-fed offset technology landscape
has undergone an enormous change since L&L looked at the technology in depth a decade ago. Press speeds have almost doubled, up to 22,000 sheets/hour (s/h), yielding a printed area equivalent to 2.4 soccer pitches every hour. Automation has moved to a whole new level, and what used to be separate off-line processing steps have moved in-line.
Sheet-fed offset presses dedicated to label printing might typically consist of more than seven print units, a flexo coater or double coater, an extended delivery and optionally an in-line cold foil unit.
Seven print units allow label converters to move from a CMYK+spot color workflow to an extended color gamut (ECG) workflow, where Pantone colors are simulated from CMYK+OGV and controlled by an in-line spectrophotometer during the print run.
This allows multiple SKUs with any number of Pantone colors to be ganged across the same sheet, allowing efficient handling of shorter runs.
Print units do not have to be washed up between jobs, dramatically cutting changeover times.
CIP4-driven ink key automation and pre-set computer-controlled dampening curves have further reduced make-ready times and waste.
"Press speeds have almost doubled, automation has moved to a whole new level and what used to be separate off-line processing steps have moved in-line"
The technical requirements for in-mold labels and wet glue cut and stack are very different from a printing point of view. Label papers, supplied either in sheets or from the reel, are generally between 70 and 90 g/sqm, coated and uncoated, while in-mold films are supplied as a reel stock with a thickness of 50-90 microns in white or transparent variants.
Modern sheet-fed presses can rapidly switch from sheet feeding to reel-based production and back again with minimal manual intervention.
In-mold label films require specially configured sheet handling and drying packages to protect the film, eliminate static build-up, and prevent heat damage during drying.
Post printing, press manufacturers like Heidelberg and KBA have also developed off-line rotary die-cutting and automated blanking technologies.
Rotary cutting delivers major productivity gains compared to flatbed, while automated blanking removes the manual stripping element from the sheet processing workflow.
Heidelberg and KBA are two of the leading players in the 3B format sheet-fed offset wet glue/IML sector, and looking at their print and processing technology in more detail helps illustrate the broader points outlined above.
Koenig & Bauer
Koenig & Bauer’s commitment to the labels sector is demonstrated by a specially configured Rapida 106 X at its Radebeul Customer Experience Centre. Printing at 22,000 s/h, the press is configured with an RS 106 X reel-to-sheet feeder, seven printing units, an in-line coater, extended delivery and a cold foil module.

In-line flexo coaters are now standard equipment on offset presses specified for labels. These flexo units have reached a high level of automation to match the rest of the modern offset press system.
On the Rapida 106 X, all functions of the CPC+ fully automatic coating plate changer can be controlled from the press console. There is essentially no longer a difference between printing and coating plate changing: all manual intervention is eliminated, no tools are required, and changing times are identical.
The AniloxLoader, meanwhile, allows three different anilox rollers to be stored in the magazine on the coater and selected at the press of a button. The anilox rollers in the magazine can be swapped at any time to provide a high level of flexibility for different coating applications.
In-line cold foiling is another increasingly common addition to labels-specific sheet-fed offset presses. Koenig & Bauer has developed the FoilTronic cold foil module for this purpose, further extending finishing options to include 3D effects, anti-counterfeiting features and other special effects used on both labels and folding cartons. Process automation features include automatic threading of the foil web.
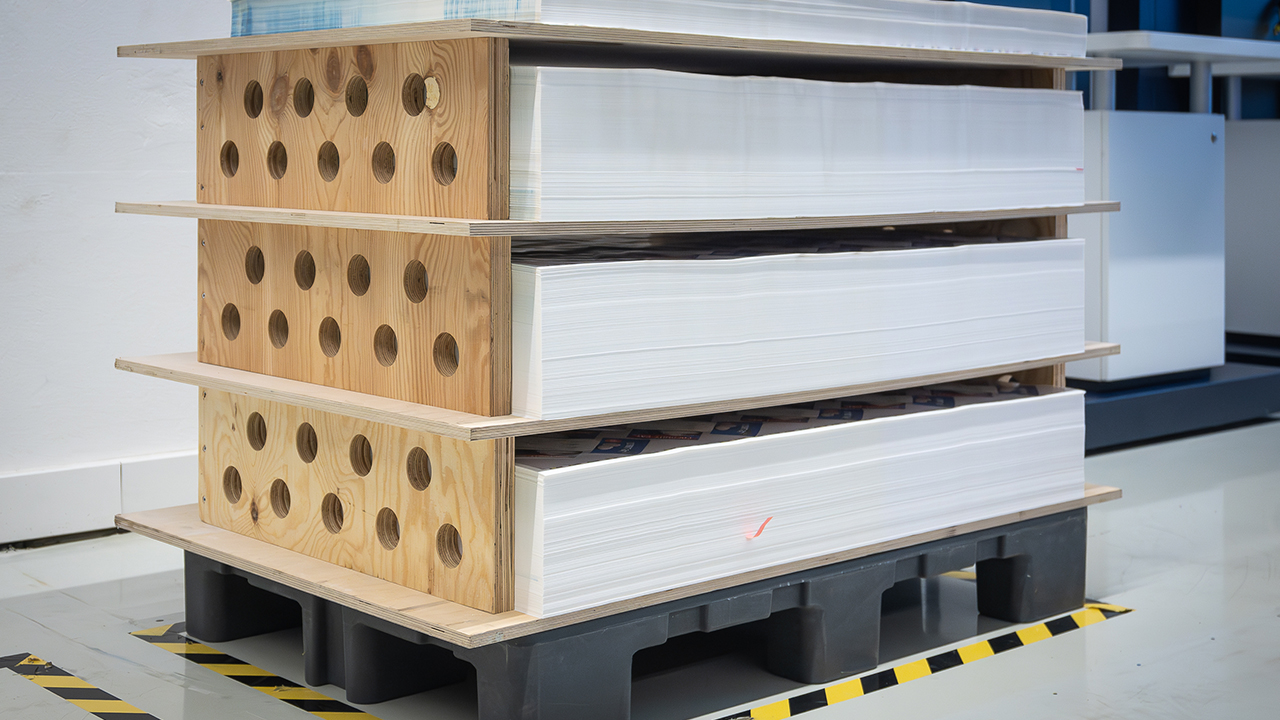
For IML production Koenig & Bauer has developed an automated hurdle delivery, which provides for smear-free non-stop production, with small batches of printed IML labels gathered into separate piles. The individual hurdles are created automatically by the Rapida, leaving the operator to insert the supports and board. The unblocked pile can then be passed on for further processing.
Rotary die-cutting
Off-line rotary die-cutting of label sheets is handled by the CutPRO X 106, running at speeds of up to 16,000 s/h. It handles both ultra-thin in-mold films and label papers of all kinds.
An anti-static film-handling package is optional. The ‘Click & Cut’ register pin system positions the process forms on the cylinder without additional manual intervention, reducing make-ready times to less than fi ve minutes. The pile of die-cut sheets is immediately available for further processing.
"Rotary cutting delivers major productivity gains compared to flatbed, while automated blanking removed the manual stripping element from the sheet processing workflow"
On both in-mold and paper labels, it is often the case that small pieces of waste must be removed from within the blanks. To cater to this, Koenig & Bauer has developed a hole punching and extraction tool for the CutPRO X 106. In a separate die-cutting unit, waste elements ranging from 5 mm diameter can be cut out within or between the blanks and removed immediately, all in an in-line process.
The company’s Master Blanker system then separates blanks from the remaining waste using programmable pins or a blanking tool.
The rotary die-cutter and blanker combination can handle the same throughput as several flat-bed die-cutters. The system delivers blank stacks for further processing or shipment to the customer.
Heidelberger Druckmaschinen [Heidelberg]
Heidelberg has dedicated solutions for the printing and conversion both of wet glue and in-mold labels on its Speedmaster XL 106. The new Peak Performance Generation of the press presented at drupa last year prints at up to 21,000 s/h and is as an additional option supplied with the CutStar reel sheeter.
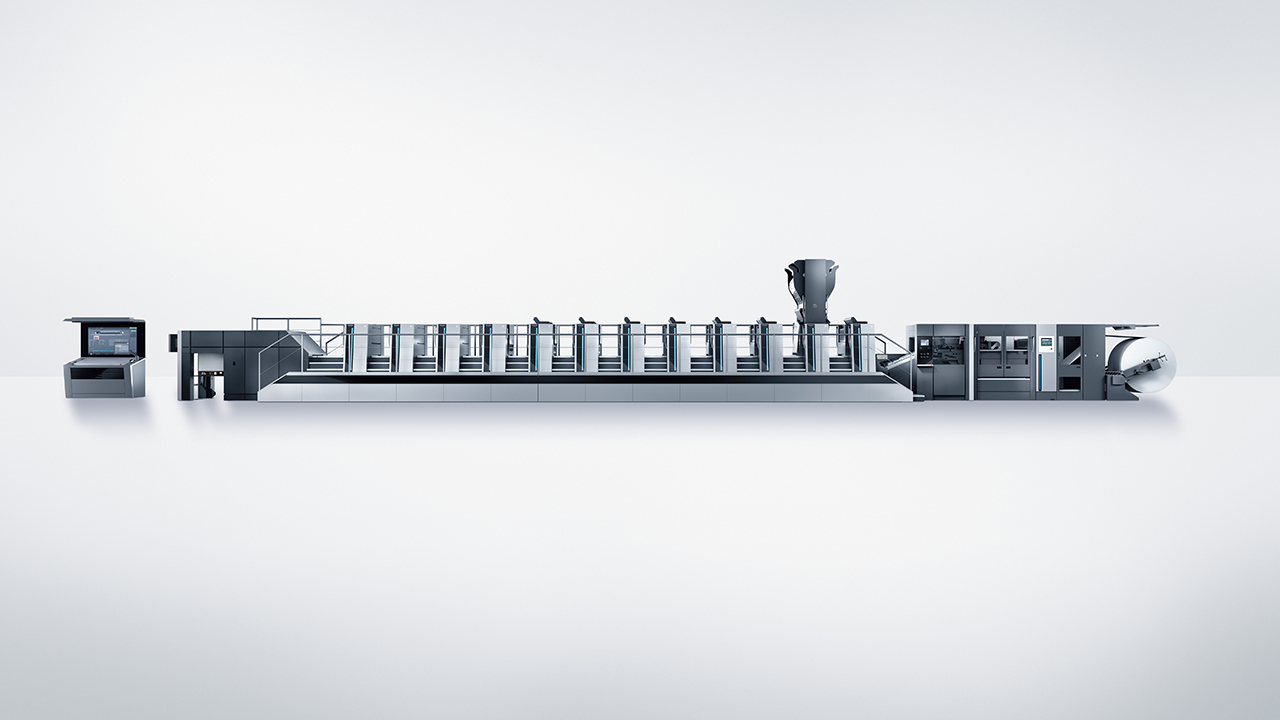

The IML Performance Equipment 4.0 package allows the press to handle the thin, lightweight materials found in IML applications. It includes special handling components on the feeder and delivery and optimized sheet travel to prevent creasing and stretching of substrates across the entire machine length.
This allows films from a thickness of 40 microns and grammages from 30 g/sqm to be processed at speeds up to 14,000 s/h.
"The technical requirements of in-mold labels and wet glue cut and stack from a printing point of view are very different"
The DryStar Advanced dryers have ten drying zones to ensure optimum drying of IML labels. Hot air and infrared settings are adjustable in 1 percent increments to enable gentle processing of delicate materials and maintain register with thin plastic fi lms. Alternatively, the drying section can be accommodated in an extended delivery, which is four times as long and equipped with the DryStar Combination ECO, which can reduce energy consumption by up to 40,000kWh a year.
On the press coating section, anilox roller and coating plate changes can be performed with various levels of automation, including semi- and fully-automatic coating plate changes using the AutoPlate Coating/Pro system. Fully automatic anilox roller changes are carried out using Heidelberg’s Autoloader technology. The coating is changed from matte to gloss or vice versa fully automatically from the Coating Center located behind the press.
This is all a part of Heidelberg’s Push to Stop automation mode on the coating unit, enabling parallel changeovers without manual intervention at the same time as other set-up processes and automatic cleaning functions are taking place.
For In-line foiling Heidelberg has developed the FoilStar cold transfer module.
The modified FoilStar Cure makes it possible to produce metallic effects with cold transfer on in-mold label material using LED-UV. The web guidance system is modified with a long wrap angle on the impression cylinder, allowing the transferred metallic pigment and UV adhesive to be bonded to the substrate by means of an LED UV interdeck dryer. This produces better adhesion of the metallic pigments along with high process stability and a higher metallic gloss. Up to six foil ribbons can be used with the entry level module, allowing for waste-saving production with or without indexing.
The Push to Stop concept also applies to the delivery, where an automated hurdle mode allows efficient small pile production. A movable belt table system allows reliable pile separation and precise placement of the auxiliary pile.
We noted earlier that some label converters are shifting their focus to extended color gamut (ECG) printing to eliminate the need for washing up multiple spot colors between jobs. Heidelberg has developed the Prinect Multicolor Toolset to display different spot colors on one sheet as part of its automated color management workflow.
Label finishing
Heidelberg has also developed dedicated downstream label processing equipment.
The Speedmaster XL 106-D rotary die-cutter has been adapted for in-mold labels with improved anti-static equipment on the feeder, cylinder and delivery and stiffer die-cutting cylinders, allowing for production speeds up to 10,000 s/h.

The Speedmaster 106-DD twin-unit die-cutter adds another important IML production step.
The first unit places an injection hole using a die on a magnetic cylinder down to 5 mm diameter, with waste removed by an additional extraction system.
The Speedmaster XL 106-D can optionally be connected to the CutStar reel sheeter, allowing registered die-cutting of preprinted rolls.
Waste stripping can be handled automatically by the Kawahara TXS-1100 blanking machine, now available through Heidelberg. The Kawahara TXS-1100 is a powerful off-line machine which addresses both in-mold label and folding carton post-press applications. It has a blanking cycle of 30 seconds for a pile of die-cut sheets up to 80 mm high.
The TXS-1100 operates using a system of upper and lower pin beds to match the required label shape, configured using templates. It is optionally configurable with a direct pallet infeed and a conveyor for removing the die-cut blank pile.
Stay up to date
Subscribe to the free Label News newsletter and receive the latest content every week. We'll never share your email address.