Changing the face of flexo
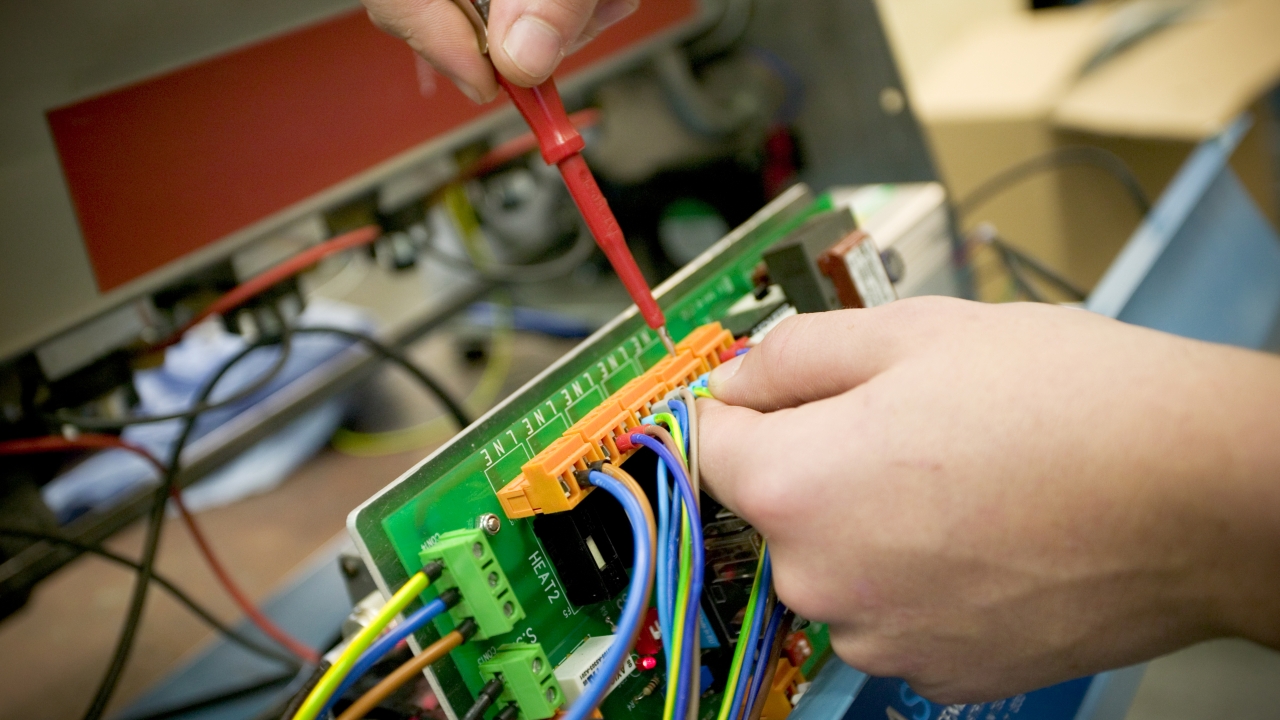
As someone who travels the globe, listening, witnessing and trying to get a general feel for what is happening across the whole of flexo, I am sensing more and more the sheer frustration felt by print managers as they try to somehow produce a print job of an acceptable standard while using anilox rolls that they simply cannot get clean, or clean enough using their existing system.
I have also reached the conclusion that many print managers and even business owners, have lost focus on what the ‘process of flexo’ actually is, while still believing that it’s all about printing, which is not the case. As print managers are usually ex-printers, they often tend to gravitate to the print end of the operation, which is understandable. However, standing back and looking at their whole process, jobs could be made so much easier. However I understand that it is not always their fault as they are often under pressure and can only work with what equipment they have.
In my opinion, print is simply the output from the process and nothing more. An output of some sort will always be achieved no matter what press, ink, paper, substrate or anilox condition. However, a consistently good, high quality output is only achieved if the pre-press, where the true process of flexo can be found, is controlled. We all know the term ‘garbage in equals garbage out’. Within the pre-press arena, the most vital element that will affect the output more than anything else is the condition of the anilox roll.
It is clear to me therefore that if the anilox can be controlled, up to 80 percent of the output problems will be eliminated. So the following statements hold true: ‘Control the anilox, you go a long way to controlling the process. Control the process, you go a long way to controlling the output. Control the output, you go a long way to controlling the profit.’
It’s a very short, very simplistic line, but very fundamental nonetheless.
Anilox control – the new paradigm
As flexo moves forward in the 21st Century, it is becoming increasingly clear that the anilox should not just be kept ‘clean’ but it should be controlled. We are seeing several of the larger groups looking very closely at this and adopting the concept wholeheartedly. This is achieved by using a cleaning system that has the ability to safely render the roll 100 percent clean every time, to deliver a consistent base line from which to work and there are five tangible benefits that can be delivered by ‘anilox control’. These are:
- Non-requirement for over pigmentation of inks
- Quicker and more consistent make ready times, leading to...
- Greatly reduced waste
- Higher and more consistent print quality
- Easier anilox inventory management (through the regular use of a quality control system such as Troika’s AniCam range)
All of these benefits lead to considerable cost savings, progression for the industry and a very short ROI on the equipment, thus impacting the press ROI. More to the point, it is not difficult.
Suitability and ‘Project Fear’
Looking across the market at alternative technologies of various forms, it’s also very clear to me that in view of the above, their suitability for the task at hand is severely lacking as our industry moves ahead of what they can deliver. This statement is not emotive, but based on fact and data, on experience, and through witnessing the real struggles faced every day through the use of technologies that simply do not ‘cut the mustard’. These technologies leave the print manager to firefight the consequences and the business owner to count the cost.
Quite often I am dismayed to find out that the business owner had overruled the print manager and bought an alternative piece of equipment based on price instead of technology. Another reason, which is equally alarming, is because their head has been turned through fear provoking falsehoods regarding Alphasonics’ technology and or misleading statements regarding a competitor’s equipment. How such undoubtedly intelligent people can be persuaded so easily down a different path is difficult to comprehend. This is especially troubling as it boils down to being scared or misled into buying something that will not do the job that their print manager and indeed their company so desperately need.
However, that fact that certain competition’s only sales tool is to instil fear into the customer regarding our technology, tells us that we have the immediate advantage. Over the years we’ve affectionately termed scaremongering of this nature ‘Project Fear’ and I sense that the people in flexo are starting to become aware of the fragility of the arguments.
However, an alarming and frightening aspect is that Project Fear has taken hold and become deep rooted in the US, more prominently than elsewhere in the world. I believe that individual companies and the industry in general are actually being held back in terms of consistently achievable print quality through the widespread use of very poor and ineffective cleaning systems.
The truth of the matter
In 2016 Alphasonics was approached by a well-known, globally operating flexible packaging group to discuss anilox cleaning. This group has several different cleaning systems and methods across many sites and although it realized that there was a problem, before a change could be made from the current approved suppliers, proof was required in the form of hard and fast data. We were asked to provide demonstration systems so that the company could carry out completely independent, extended trials against a number of different systems. As a result of the trials and the data gleaned from them, Alphasonics was appointed worldwide approved supplier with immediate effect.
The graph below shows results achieved during head-to-head trials against a well-known jet wash cleaning system. It should also be noted that these results were achieved with only 20 percent of the chemistry and in a third of the time of the jet wash.
The graph below shows results obtained during head-to-head trials against a well-known bead blasting system.
We are currently awaiting the head-to-head trial results against laser cleaning, but fully expect that our technology will again come out on top based on reports from several users across the industry, across various geographies. The direct comments have implied that Alphasonics equipment is far more versatile, faster, reliable, effective, less expensive and indeed safer than this technology.
It is clear that the methods examined compared to Alphasonics must now be questioned in terms of suitability for the task at hand. The question now lies in whether these technologies are actually fit for purpose. The data points to the conclusion that they are not.
Measuring ground-breaking technology
The technology employed by Alphasonics has been developed in house over the past 24 years. Step by step, bit by bit and over this time, we have been very mindful of screen count development and the need to keep pace with it. This constant development over such a time span has placed the company is a unique position, as we now have technology that is so far advanced we have been able to look at other sectors. Namely healthcare, where our equipment is cleaning surgical instruments to a never-seen-before level, which I’m sure many will agree is good news all round.
Within the development of the healthcare device, we also had to develop a validation system that accurately shows exactly what is going on within the tank fluid on a weekly basis. This was a critical requirement insisted upon by decontamination scientists. The resulting device is called a CVD (cavitation validation device) and its use actually showed results that even surprised Alphasonics engineers, with our technical manager commenting that, ‘we knew our kit was good, but now we can prove it conclusively’.
Ultrasonics, when applied into fluid, is very patchy with areas of high activity as well as areas of low or even no activity, and it is this disparity that has the potential to damage an anilox roll. This produces the dreaded hot and cold spots found in early ultrasonic equipment and alarmingly, in some examples found in the field today.
However, there are ways of greatly reducing this spread to a point where it is incredibly small. The one thing that our healthcare project showed us is that the hot and cold spots can never be completely eradicated, but can be rendered so tiny that they cease to be an issue, thus making the system completely safe for hourly, daily or weekly cleaning of even the highest screen counts because of the supremely even distribution of the sound.
The CVD expresses ultrasonic activity in millivolts (mV) and, as the graph above shows, the main band of activity has a spread of only 1mV (1/1000th of a volt) which is incredibly small. The spikes and drops witnessed either side of the main band show an overall spread of 4mV. From the readings on the left hand column, two of the three readings show a spread of only 3mV and the final reading shows a spread of 4mV. The mean reading is 20.4mV and the average spike 22.3mV, making the spike only 1.9mV. The spikes and drops shown are only 1/10th of a second in duration, meaning that they can essentially be ignored. The average rounded up spread reading is 4mV. The figure of 7mV shown across the bottom is the total spread after nine readings. This device takes 1,800 random readings within a three minute validation, meaning very accurate and very revealing results.
In the graph below, the hot and cold spots can be clearly seen and it is noted that there is no main band of activity. The spread is very erratic and this type of activity is indicative of a system with the potential to damage a roll. While the spread in this graph is only 11mV, it is three times wider and the spikes are of a longer duration than the Alphasonics system. The mean reading is 12mV and average hot spot reading is 18, making the size of the spike 6mV, more than three times the Alphasonics unit, with much more regularity and of longer duration. The spread across all nine readings was 17mV being 2.5 times higher than the Alphasonics system.
What can’t speak can’t lie. Alphasonics cannot be compared to other ultrasonic systems on the market. Using a scientific approach, distinctions are clear between a typical ultrasonic anilox cleaner and the super-sweeping Alphasound technology, central to Alphasonics’ systems.
From the past…going forward
Over our time in the industry, we estimate that our equipment has cleaned in excess of seven million anilox rolls. Over this period we have never, not even once, had a complaint for anilox roll damage. So, despite Project Fear, we are on very firm ground.
Since the year 2000 when we introduced our Alphasound technology, customers have won in excess of 120 print awards, in several cases actually ‘sweeping the board’ of awards on offer. This is not co-incidence, but further evidence of the effectiveness of this unique technology.
So confident are we as to the performance and safety of this equipment that we will be offering a written guarantee that will be given to any prospective customer at Labelexpo Americas 2016, which will also be included within the manual of any system we sell. The thought process is to ensure our customers can feel confident in our equipment, in our technology, and most importantly our honesty and sincerity.
As a further reminder of the safety credential of Alphasonics, a unique trial was carried out in which six rolls were cleaned continuously for five days and nights, equivalent to 1,300 cleaning cycles or five years’ worth of cleaning. Watch the video of the Safe with Sound live anilox cleaning trial here.
It is hoped that the undisputable data shown in this article will finally kill off Project Fear by empowering the decision makers within the sector with the facts. More to the point, it shows what is achievable through anilox control and the benefit therein for flexo as a process.
This article is written for those who are genuinely looking to move forward in terms of achievable and sustainable high print quality for the good of our industry. A goal that we at Alphasonics are fully and unreservedly committed to.
Alphasonics has been shortlisted in the 'Award for Innovation (for companies with less than 300 employees)' category at the 2016 Label Industry Global Awards, which will be presented during Labelexpo Americas 2016. Read the full shortlist here.
Stay up to date
Subscribe to the free Label News newsletter and receive the latest content every week. We'll never share your email address.