The history of anilox volume measurement
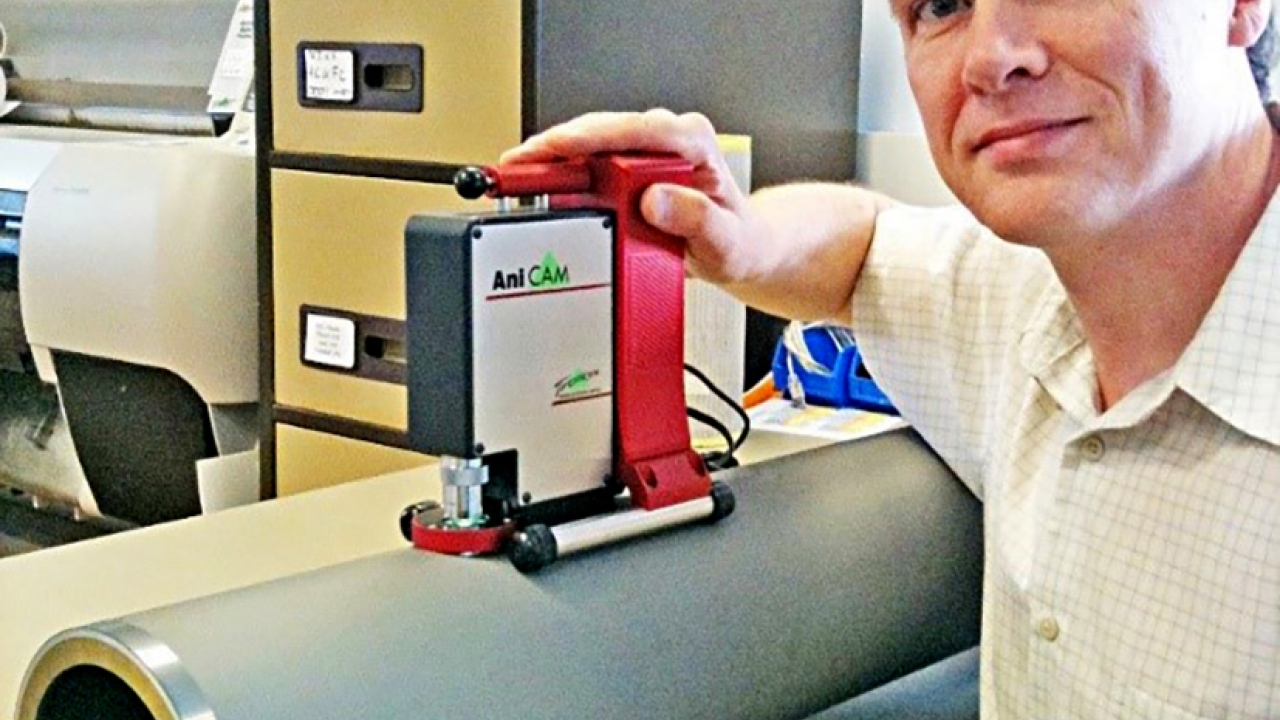
It appears to be standard procedure to blame first the ink or what the ink technicians have done, then the doctor blade set-up, the substrate and the plates; finally, when all else fails, to consider the aniloxes.
The condition and actual volume of the anilox needs to be known to minimize press set-up time and cost. Accurate anilox volume measurement is a recent part of the evolution of flexographic printing, which in reality was never possible historically.
This article does not discuss the measurement of screen count (LPI or LPCM) or the screen angles or cell shapes, which can be hexagonal, elongated hex or an open cell structures (ie tri-helical or Apex GTT) – all of which are easily measured with the AniCAM and Anilox QC software, and should be checked when receiving new aniloxes from the manufacturers for possible errors in manufacturing which will cause many hours of frustration and lost production time and waste if not found before running on press.
History of volume measurement methods
The methods of volumetric measurement on laser ablated ceramic rolls, as with any science, has progressively developed and evolved into something that can now be described as accurate.
Originally the measurement method was, quite naturally, copied from the mechanically engraved charts where the screen count and the opening of the cell was easily established. Knowing the angles of the engraving tool, the volume was calculated using trigonometric formulae.
In the early days of anilox measurement most anilox engravers used a chart to give an indication of the cell volume. However, there can be a large difference in volumes due to the shape of the cells.
In the example pictured, if the sharp pyramid were accurately measured at 3 volume, the flattened straight cut cell would have a volume of over 8 volume, the middle flattened-pyramid, which is comparable to the early ceramic engraved cells, would have a volume (if measured accurately) of approximately 6 volume. Measurements with a large variation in readings were good enough at that time, simply because flexo was still in its evolutionary stages and certainly nowhere near the quality we have today.
As time progressed, laser ablating of longer lasting ceramic aniloxes was a real step forward in anilox manufacturing. This allowed the evolution of higher screen counts and hexagonal cell structures (30 and 60 degree) also over time the evolution of complex open cell structures, all of which have really advanced the quality of flexo printing.
With laser engraving all anilox manufacturers had to evolve their measurement system from the simple chart method of volume measurement to a more sophisticated method. This was the Liquid Volume - Ink drawdown method.
Many manufacturers developed their own method of liquid volume checking, however they needed a reference point from which to use when stating the volume of the aniloxes. If they had done their calculations on the sharp cell above, that volume would be very different to those that made their reference from the normal cell, and certainly very different from the U-Shape straight cut, wide bottom cell example. This explains why there can be a very real difference in the ink carrying capacity of aniloxes from different manufacturers, despite the aniloxes document stating they are of the same volume.
This difference was proven in research carried out by Troika Systems in 2007, when a banded roll with 12 engravings from 100-1200 LPI was taken to 15 different anilox manufacturers, in Europe and North America, to be measured by them using the measurement method they were using at that time.
The results shown on the chart demonstrate the maximum and minimum volumes stated by the manufacturers. With these significant variations on each band it is no wonder converters have such elongated press set-up times and so much waste. Nor is it a surprise that coating companies waste so much solution when they have so little idea of what the actual solution carrying capacity is on their rollers.
As higher anilox screens and new elongated cells and open cell structures evolved, the need for volume measurement could not be done by conventional methods and measurement systems had to evolve. This variation between what should have been comparable aniloxes has been very costly to all flexo printers from the smallest of narrow web to the huge corrugated sites. It was time to help them save costs and time.
Liquid Volume - Ink drawdown method
While the Liquid Volume test was the first positive step towards attempting to improve volumetric measurement and was adapted by many anilox manufacturers as described above it certainly could not claim to be an accurate or consistent method of volumetric measurement.
It attempted to follow a similar process to the press by dispensing a known amount of ink which was spread by a doctor blade onto the anilox. The area the ink spread over was measured in square millimeters, and using the formulae of ink volume/square area (cm3/ m2 or BCM/inch2) a volume was calculated. Whilst this method was a positive step forward over the original mechanical method of volumetric calculation, it is prone to many opportunities for errors as follows:
• If the ink density is not absolutely constant variations in measurement will occur. Therefore, if there is a density difference between the pots of ink, or the ink in the pots evaporate at all during use, a very real variation in measurements is seen.
• Studies have shown very significant variations between operators. In October 2010, at Clemson University in North Carolina, the American FTA carried out a gauge repeatability and reliability (R&R) study on the variety of rolls measured which had different circumferences and different screen counts. The study, done under controlled conditions, showed average variations of in excess of ±10 percent using the Liquid Volume method of measurement. Which meant that a 5 volume anilox was measured at anything between 4.5 to 5.5 volume; far beyond the requirements printers need to manage their aniloxes for optimal productivity and minimizing set-up waste. It is interesting to note that at subsequent tests at one global anilox manufacturer, eight of their competent and experienced Liquid Volume users were only able to achieve a minimum 16 percent variations in their measurements on a 5-banded master roll, and when similar tests were carried out at another international anilox manufacturer using six experienced operators on a banded roll, the best results still showed a variation of 14 percent. These variations are beyond what is acceptable as measurement variations today.
• If the anilox has been through a cleaning bath it needs to cool down to room temperature before measurements can be taken, if it is warm the ink used for the measurements evaporates and gives very inaccurate readings.
• This method is not suitable to measure open cell structures such as tri-helical or other complex open cell structures because it simply flows out of the open cell structures and does not fill the cells as needed for this kind of measurement.
Therefore, it is not surprising that when anilox manufacturers were taking their measurements using Liquid Volume test method (nicknamed ‘Squirt and Scrape’ method by some users) printers found they would get different densities from anilox which were stated to be of the same volume. Fortunately very few anilox manufacturers use this method today.
Digital methods of anilox cell volumetric measurement
Fortunately, towards the end of the 1990s electronic systems of volumetric measurement started to evolve. These used interferometric measurements and gave good reliable readings but are very vibration sensitive, expensive and would not survive long in the print shop environment, so were impractical for converters.
From 2005 the Troika AniCAM with the Anilox QC made its first appearance and over the years evolved to meet the demands of the large print groups who recognized what the cost benefits to them would be if they could know what the condition and volumes of their anilox inventory.
The demands of the label groups (Coveris, CCL etc), wide web groups (Bemis, Amcor etc) and corrugated groups (DS Smith, Mondi etc) can best be summarized by the requirements of a world leading carton print group, which are: • Accuracy: of ±0.1 cm³/m² for process aniloxes
• Repeatable measurements of ±0.1 cm³/ m² when measured on the same place
• Inter-operability: the ability for different operators to get the same readings
• Ease of use with data archiving for anilox inventory management
• No time, or minimal time, lost in production due to measurement times
All of these objectives were achieved using the AniCAM with Anilox QC with inventory management (Anilox Management System), however ‘accuracy’ of measurement was the biggest obstacle – simply because it had never been proven. This gave all anilox manufacturers the ability to argue that their own measurements were correct on historical grounds, and the other anilox manufacturers were wrong – not a very satisfactory situation for the industry.
With the significant differences in measurement standards used by all the anilox manufacturers in the 2007 research, who was right – if any?
Accurate anilox volume measurement
The accurate measurement of cells was proven in 2007 by Dr Davide Deganello (pictured) at Swansea University, Welsh Centre for Printing and Coating (WCPC), under the leadership of Professor Tim Claypole, one of the leading print universities in Europe. Dr Deganello’s thesis and equipment proved with the use of high-end digital analysis using laboratory interferometers the volume of cells.
In comparative tests between the high-end interferometer at WCPC at Swansea University and the AniCAM, it was found the measurements on all 12 bands were very comparable, and Dr Deganello stated that the measurements were certainly well within the requirements needed in our industry.
Calibration for accurate measurements:
Most important for accurate volumetric measurement is calibration: this is required in all three axis. X & Y axis are relatively simple using an optical graticule, which is small glass surfaces with a grid etched onto them at 100 μ spacing allowing for very accurate calibration in the X & Y directions. Depth measurement needs to be particularly accurate to give the exact depth, and with the X & Y data the depth is used to calibrate the units to give the exact volume of the cells.
Calibration for depth is achieved by scanning a very small sphere (ball bearing) of a known size, which logically is the same dimension in all three axis. Spheres have been used as a method of calibration by some interferometer manufacturers since 1998 and is known to be mathematically accurate. With this system of measurement and calibration, the industry had at long last a mathematically proven, accurate measurement standard to work from.
Consequently, in 2013, Troika Systems developed a method of using a sphere of a known size as a valid reference standard for dimensional and volumetric measurement and hence the AniCAM Calibration Program (ACP) was developed so users could calibrate their AniCAM, usually annually, or as frequently or infrequently as desired.
Anilox measurements value conflicts
Clearly there is a conflict between the accurate, mathematically proven measurement system used by many hundreds of printers globally, and the historic values used by the 38 plus anilox manufacturers around the world. It would be very difficult for the anilox manufacturers to change their historic measurement values, so a solution needed to be implemented.
The solution was to export from the Anilox QC both values of measurement (this is done in the anilox manufacturers special version of the Anilox QC application), so if an anilox manufacturers original measurements are different to the accurate readings they can export both the accurate value and their individual standard values to the anilox roll information sheet.
So, if the manufacturer’s value was 10 percent higher than accurate, a 10.1 volume roll, measured with a historic measurement method, would show as 9.3 using the accurate measurements.
Provided the anilox manufacturers have the correct version of Anilox QC application, they have the ability to export both values.
Conclusion
The evolution of anilox manufacturing has bought many advantages to all users: they are now produced to a high standard of consistency and repeatability which was not possible even a decade ago. With the evolution of the anilox there was a need for accurate and reliable measurement, giving flexo printers the ability to manage their anilox inventory to a point where press set-up time is optimized and make-ready waste is reduced to a more practical minimum.
This is not the end of the story. There are some interesting developments on the horizon with different materials being used in the production of aniloxes. Also, now volumetric measurements can be accurately measured, we can progress to analyzing and optimizing ink release characteristics with different cell structures optimized for the individual print or coating processes. It’s still a very exciting time in flexo.
Stay up to date
Subscribe to the free Label News newsletter and receive the latest content every week. We'll never share your email address.