Aquaflex in-line flexo press features CI benefits
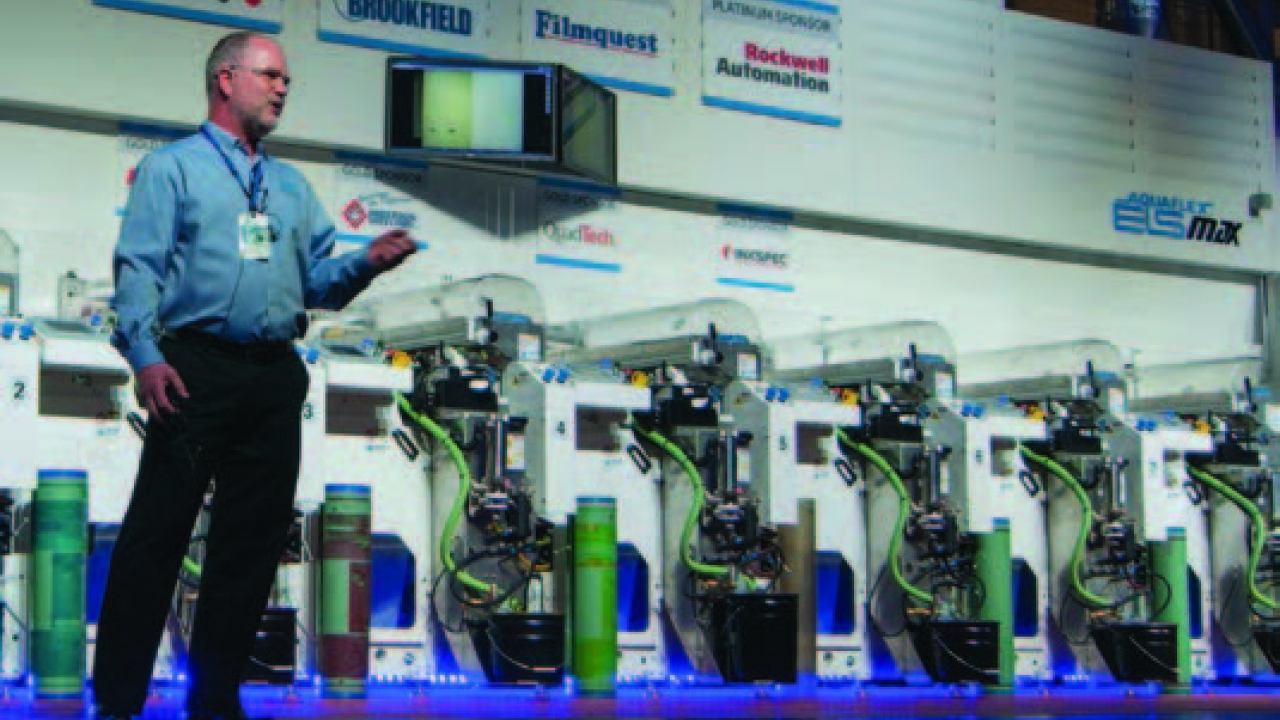
Paper Converting Machinery Corporation (PCMC), a global supplier to the tissue converting, packaging, flexographic printing and non-wovens industries, recently demonstrated the benefits of the Aquaflex ELS-Max in-line flexographic printing press at Impact 2015, an event held at its global headquarters in Green Bay, Wisconsin. The Aquaflex ELS-Max has been integrated with traditional design aspects used in CI printing press configurations into an in-line production format to service the growing need of ‘small’ volume orders of labels, pouches and cartons. The press is available in 24, 28 and 32-inch web widths; it can hit speeds up to 1,000ft/min (305m/min) and print on half-mil films and carton stock up to 14pts.
Tim Fox, Aquaflex sales manager, says: ‘Our goal was to put together a feature set on the ELS-Max that could fulfill the many requests of packaging converters in the market. There is no other CI or in-line printing press with this kind of feature set. The ELS sets up as quickly as a CI, produces with similar waste numbers to that of a CI, and has all of the automation in impression setting, plate pressure and the anilox.’
ELS-Max features include force loaded ink chambers with viscosity control that offer quick set-up and automatic wash up without tools. Operators need only to adjust two screws.
The ink decks slide out automatically, making it easy to remove and replace anilox sleeves. A system for automatic monitoring of doctor blade wear supports quality control. The press can be equipped to use solvent, UV and water-based inks. The press will include a VOC capture system for solvent requirements.
There is a nip roll on each station at the impression cylinder to maintain web control on thinner substrates at higher speeds. There is an option to have heated or chilled nip rolls for dedicated substrate and adhesive requirements. It also includes mark to pulse registration and a job store feature to recall an infinite number of order recipes.
PCMC has installed more than eight ELS-Max presses into the US market, including one at a large packaging company to produce shrink sleeve labels and another at a Wisconsin-based label business focused on offset printing and film labels.
Stay up to date
Subscribe to the free Label News newsletter and receive the latest content every week. We'll never share your email address.