Bobst opens Italian labels and flexpack center
The new Competence Center showcases Bobst narrow and mid-web portfolio across labels and flexible packaging.
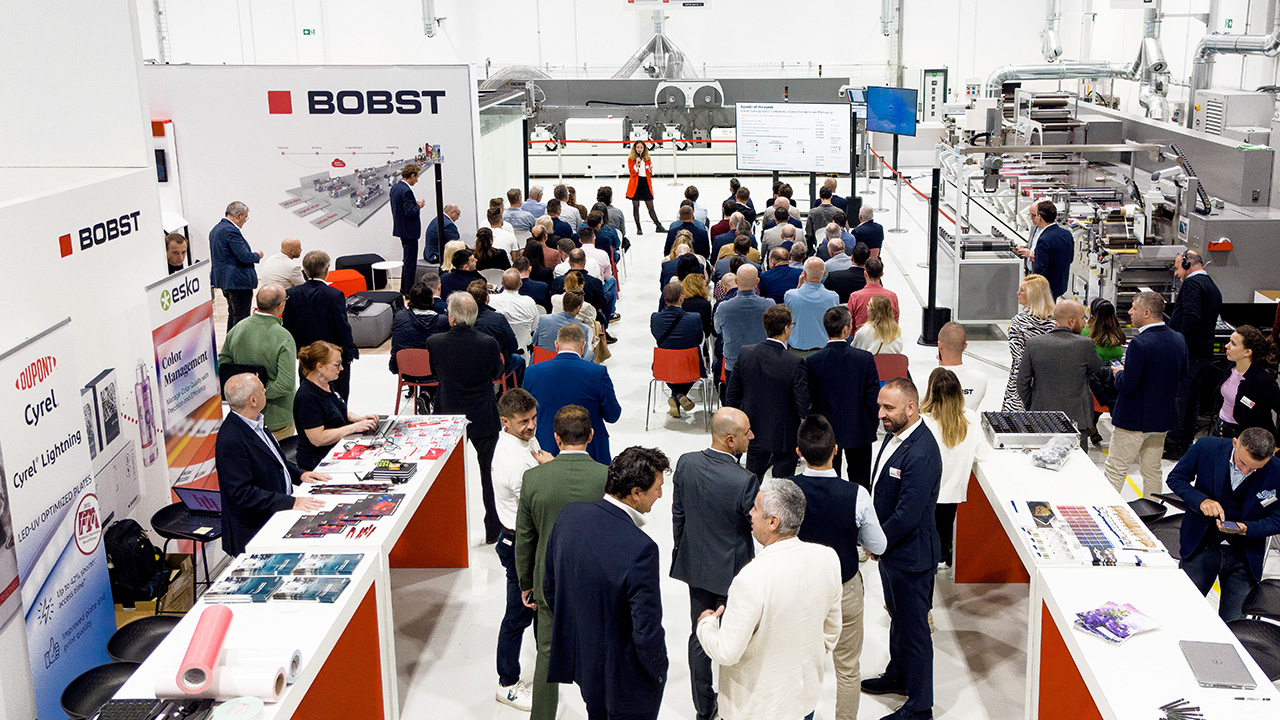
Bobst labels and flexible packaging Competence Center in Firenze
Following the successful establishment of the Atlanta Competence Center in the US, Bobst has opened a new 1,200sqm Competence Center in Florence, Italy, dedicated to labels and flexible packaging. Providing access to the company’s full range of narrow and mid-web printing technologies with six complete production lines — including inline flexo, digital and All-in-One technologies — the new Italian facility is designed as a hub for collaboration and innovation.
‘The major investment in the narrow-mid web printing and converting product line demonstrates Bobst Group’s strong commitment to this segment,’ states Matteo Cardinotti, head of Bobst’s narrow mid-web printing and converting product line.
‘Bobst has experienced exceptional growth in labels in recent years and we are supporting that development by opening more local Competence Centers and hiring more staff worldwide. In Italy specifically, we have also expanded our production facilities and reinforced our service organization to match the needs of our European customers.’ Bobst employs a total of 350 employees dedicated to the narrow and mid-web inline segment.
Cardinotti said drupa and Labelexpo Americas 2024 demonstrated how the industry is ‘moving beyond innovation in hardware and software in isolation towards full integration of processes. In this respect, Bobst is leading the way with its portfolio of complete workflows designed for the future of packaging production.’
Six production lines
The production lines on show represent all Bobst’s technologies dedicated labels and short-to medium-run flexible packaging.
A Bobst Master M6 flexo press is integrated with a near-line Novolam MV mid-web laminator. This setup, in combination with oneECG printing and DigiFlexo technology, allow production of short- to medium run flexible packaging and shrink sleeves.
Bobst’s ‘All-in-One’ platform with inkjet and flexo technology inline, was represented by the Digital Master 340 press running pressure-sensitive labels for the beauty segment. For inline flexo, Bobst demonstrated its Master M5 with single-pass production of multi-layer labels, also featuring oneECG (extended color gamut) technology and DigiFlexo automation.
All presses demonstrated live were operating with direct integration to the Bobst Connect digital platform.
Acting as a central data hub, Bobst Connect integrates every aspect of the workflow, from job management and pre-press setup to printing, converting and quality control, based on collection of real-time production data.
‘The ability to capture these valuable insights allows converters to enhance their business planning and optimize the entire production process,’ says Cardinotti.
The platform is continually evolving, and Bobst recently added a new certified substrate library, job quality reports, and ‘Job and Recipe Management’, which streamlines machine integration and enables faster setup.
‘Bobst has brought into reality the idea of the closed-loop workflow, what we call “PDF to twin-PDF” concept, addressing the main industry trends with easy-to-use machines, all orchestrated by Bobst Connect,’ says Cardinotti. ‘Our main focus is to provide customers with complete workflows that help them overcome a multitude of market challenges, allowing them to deliver consistent and high-quality results much quicker and with low waste, without having to rely on highly skilled operators.’
Implementing ECG
Another issue addressed at the event was how to maintain color consistency across different types of technologies, applications and over time. This is an issue as converters move beyond labels, leveraging inline flexo technology to produce a range of short-run flexible packaging applications. With such a highly complex market, it is a great challenge for converters to maintain the consistency of brand colors from job to job.
During the event, Bobst, together with its network of partners, demonstrated how oneECG works by standardizing the colors on press and automating the color matching process, moving it from the pressroom into pre-press.
This ‘digitalizing’ of color management means operator skills will have less impact on the print outcome.
The benefits of oneECG printing on inline flexo presses also include savings on ink and plate costs, substrate waste reduction, faster setup, and a reduction in cleaning time and related consumables.
The event reinforced Bobst’s industry partnerships with the presence of Esko, Kurz, Avery Dennison, Sun Chemical, Kongsberg PCS, DuPont and Lohmann.
Stay up to date
Subscribe to the free Label News newsletter and receive the latest content every week. We'll never share your email address.