Labelexpo Americas 2024: Dies and tooling
Dies and tooling suppliers are increasingly adopting automation to shorten setup times, reduce human error and improve waste management, streamlining production processes for label converters.
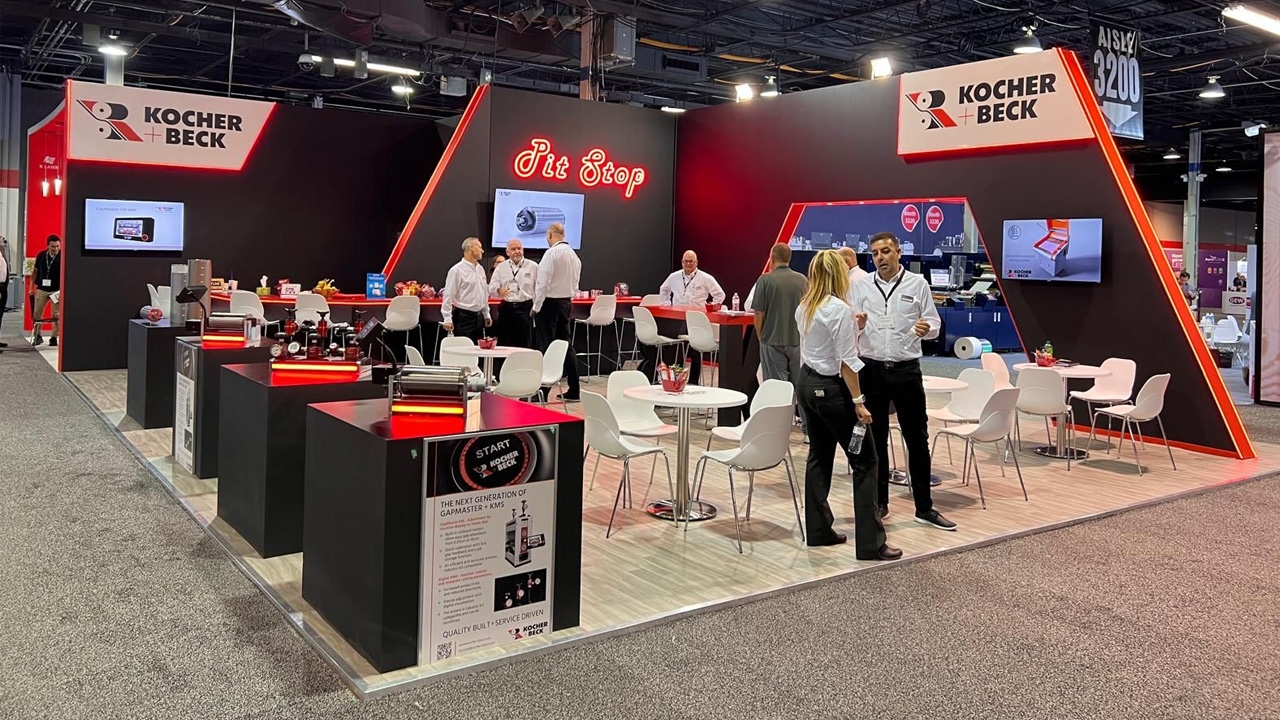
In recent years, the printing industry has seen a growing emphasis on automation, efficiency and waste reduction. After reaching record flexo and digital printing speeds, the focus has shifted to dies and tooling manufacturers, who are responding with improvements in setup time, ease of use and faster cleaning to contribute to overall productivity gains.
Apex International showcased the GTT 2.0 anilox technology. This product, developed over nearly 10 years, is specifically engineered to mitigate liquid turbulence, resulting in a calm liquid surface that increases quality and performance at high press speeds. According to Apex, it reduces ink spitting, mottling, pinholing, plugging and dot gain. The company states that the GTT 2.0’s improved engraving ensures up to a 50 percent reduction in cell wall surface area across the anilox while also decreasing the required channel depth by an average of 25 percent. Additionally, the company introduced ultra-shallow Apex UltraCell engravings designed for greater ink release and easy cleaning.
CTS Industries promoted the pro-lite HD laser-engraved ceramic anilox roller, developed for ease of care and cleaning. Dubbed an ‘operator-friendly anilox,’ this product is up to 76 percent lighter than conventional bases, resulting in lower shipping costs, easier lifting, and less susceptibility to damage. The company also showcased its EZ View Pro engraving specs, which help operators easily view details such as LPI, BCM, and serial ID to better identify and protect anilox inventory.
Dies and tooling manufacturers introduce improvements in setup time, ease of use and faster cleaning to contribute to overall productivity gains.
One of the highlights of the Kocher + Beck stand was the Gapmaster EM (Electronic Move), a servo-driven adjustable anvil system that allows users to adjust increments as small as 0.25 microns using a rotary dial and digital input with haptic feedback for the operator. The Gapmaster em also features user-friendly calibration, a home/start function, job history storage, and limits on adjustments if needed. The EM retrofit, with the same capabilities, can be retrofitted to all existing Kocher + Beck gapmaster units on-site by replacing the mechanical handle with an electrical drive unit.
Kocher + Beck also showcased its latest innovations in die-cutting, including the new industry 4.0-ready digital KMS Pressure Gauge System, which is equipped with various sensors and offers greater stability under load changes.
Maxcess introduced rotometrics’ new flexible die portfolio, re-engineered with automated manufacturing processes for enhanced precision and reliability. Additionally, chrome coating processes double the lifespan and durability of the dies. Maxcess promoted its award-winning rotorepel anti-adhesive performance coating, which provides comprehensive adhesive control benefits and improves overall die and press performance by reducing adhesive buildup and minimizing die wear and damage.
Rotometrics’ intelligent adjustable anvils offer the reliability of AccuAdjust, which can be upgraded with RotoAdjust for additional features such as job recall and operator interface. The company also showcased RotoScan, an intelligent die station providing fully automated anvil adjustments to cut perfect labels while delivering industry 4.0 analytics for smarter operations. RotoScan will be available commercially in 2025.
Maxcess also introduced the Fife guiding systems, featuring the new Fife SmartDrive Actuator and GuideLine Digital Sensor for maintaining precise web alignment. Webex tension control products, with advanced Magpowr technology, allow press operators to monitor and control web tension, ensuring consistent material handling and waste reduction. Additionally, Maxcess launched Tidland SmartSlit, an automated slitting system designed to minimize manual adjustments.
Rotometal showcased its Alulite Magnetic Cylinders, manufactured from aerospace-grade aluminum, offering up to a 50 percent weight reduction. This translates to time savings and improved ergonomics. The company also promoted its Antifriction Print Cylinders, which undergo a unique surface treatment that allows tape to be peeled off in one piece. This treatment simplifies preparation and changeovers, enables quicker tape changes, and enhances durability, adhesion, and scratch resistance.
Rotometal also introduced ultra-lightweight rotosleeves made from composite materials or aluminum.
Wilson Manufacturing highlighted its expanded line of accessories, including the Cylinder Inspection Tool, which accurately measures the undercut in magnetic cylinders and assesses cylinder surfaces for wear and irregularities. The company also presented newly designed magnetic-base bearer wipers.
Wink unveiled its latest developments in SuperCut flexible dies, including advanced coatings and optimized cutting angles designed for various label applications. The company also demonstrated its SmartGap system, featuring the newly developed SmartGap advance. All SmartGap versions utilize extra-wide bearing rings to support the anvil cylinder body. While the Advance version is controlled mechanically using adjustment knobs, the touch digital version is managed through a control unit and display that provides several powerful functions.
Stay up to date
Subscribe to the free Label News newsletter and receive the latest content every week. We'll never share your email address.