The evolution of Hapa
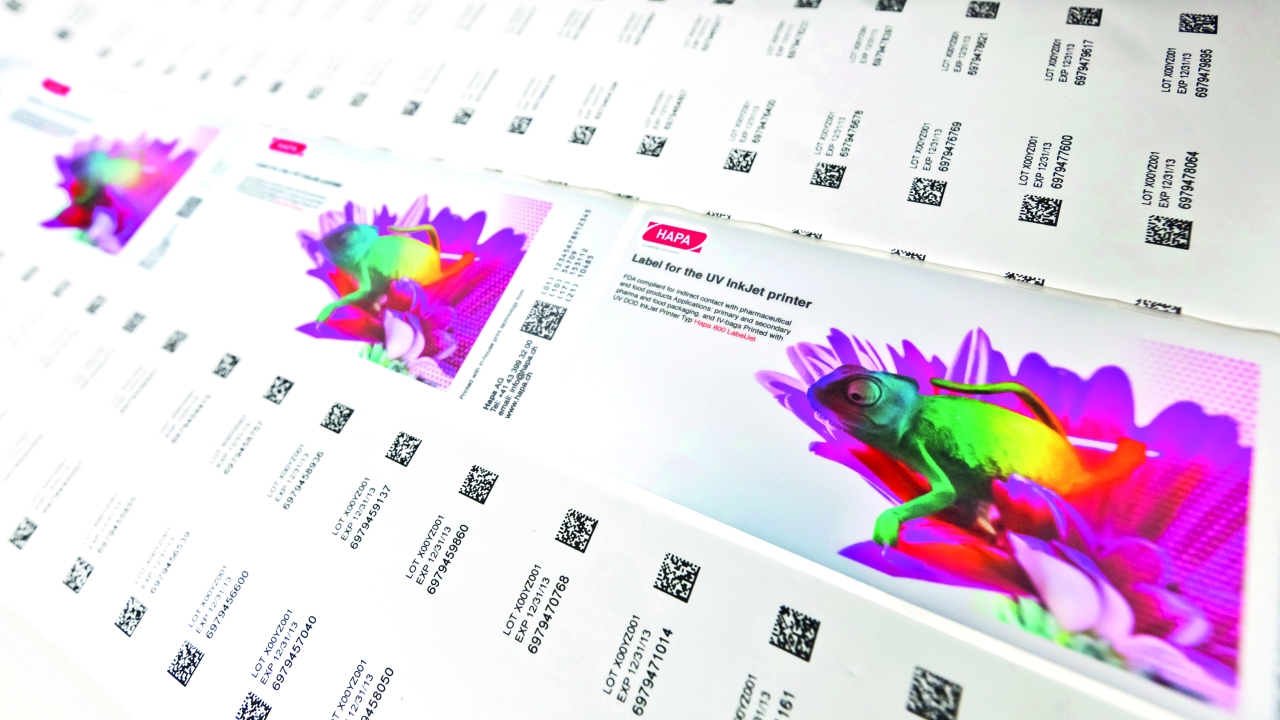
Swiss manufacturer Hapa specializes in late-stage customization and on-demand printing equipment for the pharmaceutical packaging industry, with a strategic aim to grow in the cosmetics, food and medical industries.
Today, the company has more than 2,000 machines working at 1,100 customers in 75 countries, but its roots go back to the 1930s as a company buying and selling patents. Since then, it has witnessed a number of technological developments: in the 1950s, it took one of these patents and built a mechanical machine for stamping simple alphanumeric data onto a carton or label. The 1970s saw the creation of the world’s first pharmaceutical in-line foil printing system. During the 1990s, UV flexo emerged, removing the need for solvents and providing a cleaner process, a faster drying time and a better print quality with repeatability.
In the early 21st century, Hapa was involved in a development project with a major pharmaceutical company for a digital printing machine for cartons. Although the project never came to fruition, Hapa was able to take the technology and lessons learned and, in 2007, launch systems for digital printing blisters, foils and labels.
More recent developments include the format-free redcube printing module, a compact, single-color UV drop-on-demand (DoD) piezo inkjet unit capable of printing on labels, aluminum foil, paper-backed foil, paper, glass, PVC, Tyvek, polypropylene, polycarbonate, ABS, PET and LDPE/HDPE. Applications include blisters, folded and glued cartons, erected cartons, pouches, bottles and ampoules. redcube plus is a scalable version that prints up to seven spot colors or CMYK plus three spot colors, format-free. It prints widths up to 144mm, at speeds up to 60m/ min with a print resolution up to 720 DPI. Pinning stations for white or color-on-color printing are available. ‘At the top end, we can print white then CMYK and put a lacquer over it at 60m/min,’ comments James MacKenzie, Hapa commercial director.
Understanding ink behavior is central to delivering such performance, with Hapa acquiring a DoD ink manufacturer to form its own in-house laboratory and production facility. ‘Ink behavior takes on much more importance with digital printing,’ notes MacKenzie. ‘Understanding the chemistry between the ink, material surface and substrate tension gives us an advantage to match the requirements of the application and deliver good contrast, flow, adhesion and print result.’
Also integral is material handling and control of the substrate, another core competence of Hapa, alongside UV flexo and UV DoD inkjet. Further, data processing and digital workflow integration are emerging as important aspects of project delivery. Digitalization and the use of digital technologies to change a business model and provide new revenue and value-producing opportunities, is another area where Hapa is investing.
Growth in labels
Foil printing is the main area of business for the company today, although installations for label and carton printing exist. The Hapa 800 LabelJet is a fully-digital piezo inkjet system that prints pre-cut, self-adhesive labels. The roll-to-roll system can serve several labeling lines, while an in-line LabelJet is available, which can be integrated with a conventional labeling machine. ‘We are working to move more into labels, which is part of our strategic plan to maintain a focus on blisters, expand our presence in labels and medical, and enter into the FMCG market. New technology is allowing us to expand into new areas, and opening up new opportunities.’ Examples include printing on tube laminates and bottle closures, in full color at 1,500 pieces per minute.
This is being driven, in part, by the growth in personalization, which is being seen more and more in the FMCG and pharmaceutical industries. ‘Batch sizes are getting smaller, and we’re going to see more heavily customized packaging, with variations increasing the complexity.’ Hapa’s technology suits the trend towards late-stage customization, with blisters pre-produced then printed using its BlisterJet CMYK machine just before entering the market, with text and graphics printed in CMYK.
‘Why do that?’ adds MacKenzie. ‘In the pharmaceutical industry, many blister packing lines have a low OEE. Batch sizes are so small, that they run for up to an hour, then need to be changed over for a new product. What Hapa technology allows is blister lines to be run for days or weeks, produce a whole quarter’s worth of product, then at the last minute, when the order is received, take the finished blister, put them into our machine, customize them, put them in a carton and send them straight to market.
‘The market is talking about late-stage customization and we’re seeing big brand owners using digital printing to achieve this. Our technology lends itself to that.’
Stay up to date
Subscribe to the free Label News newsletter and receive the latest content every week. We'll never share your email address.