Finishing for effect: labels and packaging
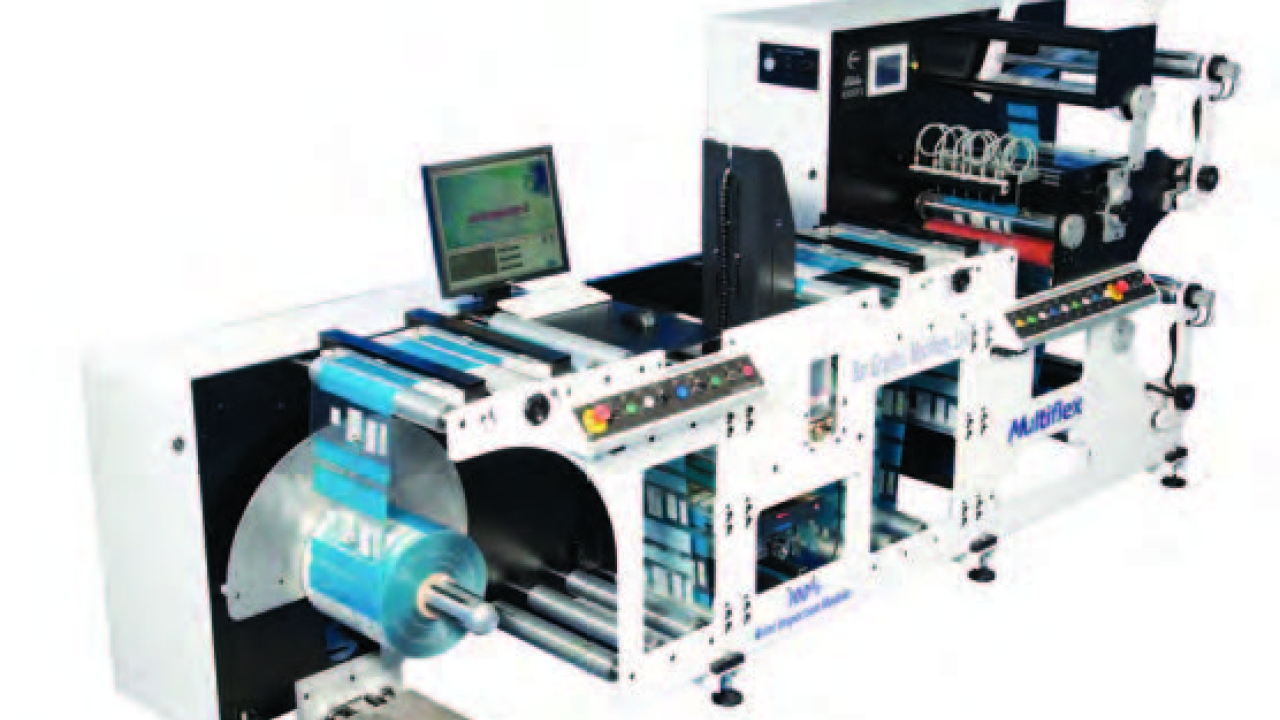
The role of post-press finishing and converting has improved greatly in recent years, thanks largely to automated technology. It has brought new approaches to reducing set-up times, minimizing waste, and increasing throughput without sacrificing quality. Changing market demands have encouraged a move towards integrated systems that are flexible enough to handle high volumes of short-run jobs, as characterized by the growth of digital printing.
Consequently, post-press finishing is no longer a means to an end. Rather, it is increasingly seen as a source of new business opportunities. Typifying this view is Raymon Lee, managing director of Brotech, a Chinese manufacturer of finishing systems. At last year’s Labelexpo South China conference he said: ‘Label converters should see post-press equipment as an opportunity to transform themselves into packaging solutions providers. This might include adding RFID, QR code, or booklet-label functionality. And we are now moving into packaging solutions – tubes and flexible packaging as well as integrating labels with printed electronics. This is where label printers can make a big difference and differentiate themselves.’
The technical back-up comes from electronically-based systems, which accurately control the positional movement of unwinds and rewinds at faster speeds, while servo-assisted nip rollers pull the web smoothly through the machine under controlled tension. This is especially important in preventing web wander when running thin-gauge filmics and unsupported films. As on roll-fed presses, synchronized control also speeds-up changeovers between substrates and aids smooth acceleration and deceleration of webs.
By replacing traditional pneumatic clutches and mechanical brakes on slitter rewinders, operators no longer need to calculate the changing weight, mass and diameters of the unwind and rewind rolls to maintain correct tensions. This is now done automatically in real-time over both short and long web paths. Touch-screens assist faster set-ups and fault identification, while accessing electronic counting sensors, job data recording devices and on-line diagnostics.
Servo drives also affect the design of equipment. Rotoflex’s redesigned DSI die-cutting slitter rewinder has a smaller footprint because its new servo technology requires smaller power cabinets compared with the former AC vector motors. Independent servo drives manage the unwind, die-cutter, matrix and rewinds, all controlled by Rotoflex’s URC 2.0 system. In addition to higher quality slitting and die-cutting, there is a 30 percent increase in output speeds of up to 300m/min, compared with existing DSI models.
Greater versatility is another benefit. ‘The updated design accommodates a variety of inspection systems, and the die-cutting unit can be disengaged for specific jobs, meaning it can be run as a slitter rewinder or as a die-cutter, accommodating more applications and job types. This means production managers can manage the job mix and optimize workflows,’ says Kevin Gourlay.
Stay up to date
Subscribe to the free Label News newsletter and receive the latest content every week. We'll never share your email address.