Grafotronic’s ambitious plans
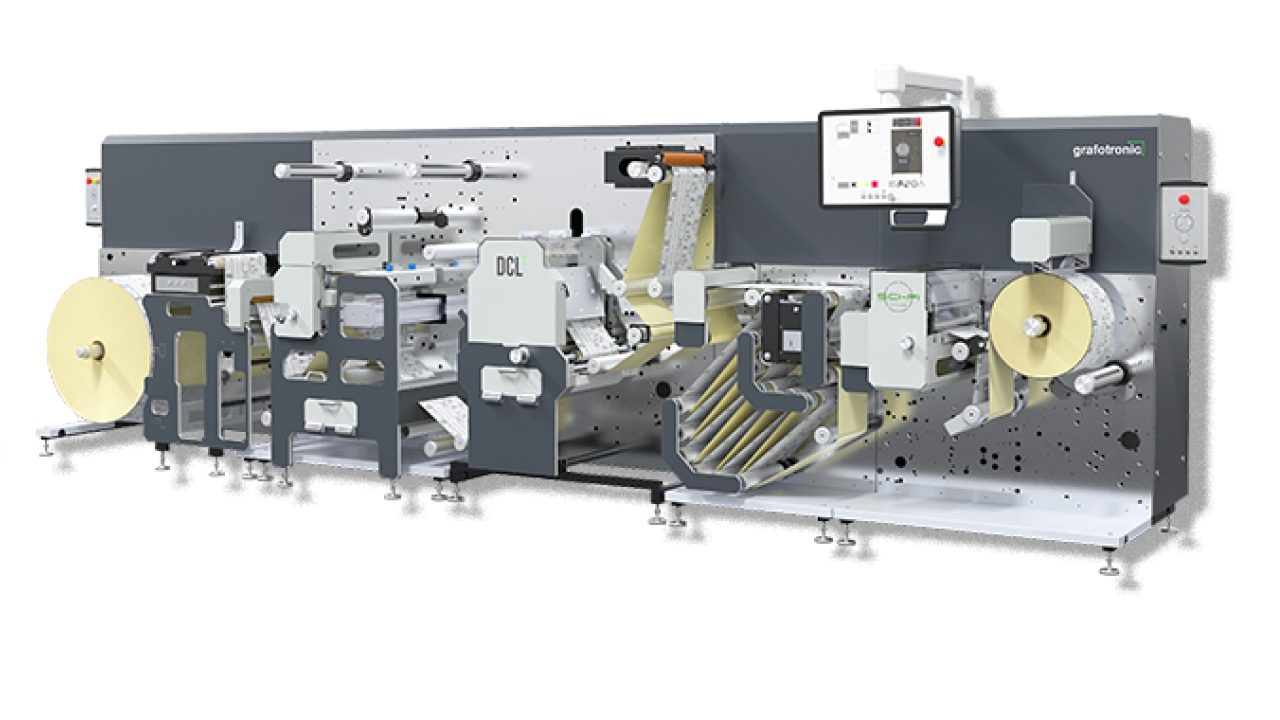
‘At Grafotronic, we strongly believe in and invest in innovation, and that’s reflected in everything we do: from our unique modular and future-proof concept to our new features and market-leading connected services,’ said Morten Toksværd, Grafotronic’s new business development director, opening its recent virtual event.
Toksværd might be new at Grafotronic, but he is well known in the industry. He joined in January from GM, where he was responsible for global sales and marketing. He has over 20 years of experience working in manufacturing and graphics, including stints at Konica Minolta and Canon. At Grafotronic he’s responsible for the global expansion of the company’s connected digital finishing technology.
When Toksværd joined the company, Mattias Malmqvist, vice president of Grafotronic, didn’t hide his excitement: ‘To drive the market development of Grafotronic, we needed someone with a proven track record of success in professional equipment and services around digital label production technologies. We’re excited to have Morten on board, and I’m sure that he’ll be a great asset to both new and existing customers.’
Grafotronic is a Swedish/Polish company founded in 2004, with sales and service centers in Chicago, Illinois, for the North and South American markets, Brescia, Italy and Bangkok, Thailand, for the Southeast Asian markets.
Opened in 2015, the company’s 2,600 sqm factory in Warsaw houses some 110 employees. Grafotronic has supplied more than 900 machines to companies in more than 60 countries around the world. Last year alone around 100 machines left the factory floor, and the company is hinting at further extension of its Polish facility to double the size of production and R&D space. This will be the third expansion in five years.
Such growth is indicative of the path Grafotronic now finds itself on, having decided in 2015 to redesign its machinery and processes to become a lean and efficient supplier of finishing equipment largely for the digital printing market. Its machines are now fully modular and automated, with short set-up times and high productivity at their core.
‘Redesigning the platform in 2015 gave us the perfect opportunity to create the most versatile and future-proof platform in the industry,’ remarks Toksværd. ‘So that’s exactly what we did. Grafotronic’s portfolio is now a unique offering of three different concepts: compact SCF, semi-compact CF2 and fully modular flagship concept DCL2.’
Innovator
According to Toksværd, the company believes that being connected is the future, and it insists on being an innovator. ‘For Grafotronic, being innovative is in our company DNA. It’s our approach in all we do and how we evaluate ourselves, our products and our services,’ adds Toksværd. ‘We already have a modern company culture, the foundation of it all. The best examples of how we change the world of digital finishing are our groundbreaking innovations. Our semi-rotary die unit is the heart of our machines, and we are very proud of our unique designs. Grafotronic has the fastest system in the world, named Gigafast, where we can go up to 200m/min, which is an extreme speed and an incredible advantage for longer jobs. Gigafast is a genuine showcase, demonstrating the heavy duty and solid design of the Grafotronic machines.’
For converters who don’t need Gigafast’s speeds, Grafotronic is working on a new system that can match the faster inkjet presses but still features short set-up times and low waste.
‘As we speak, we’re finishing our 120m/min die-cutting system, which will be a game changer,’ notes Toksværd. ‘The system has some important features beside the speed, of course, such as unique design for an almost no-waste set up, where a trained operator can set up with 30cm waste. With Grafotronic’s Compensation System, a converter will be able to use the existing flexible dies and still reach speeds of over 100m/min.’
Another example of Grafotronic’s innovative approach is the flexible die loading system with no need for a camera. A magnetic cylinder is set into position and when the new die is loaded it finds its place automatically. When the job is finished the flexible die simply slides out.
‘Slitting is also a very important part of the production process and one of the most time consuming during the job change. For some years now, there have been several automatic systems available on the market, but all have limitations. We decided to improve upon them. One of our latest innovations, Sci-Fi Knives, is the fastest automatic knife positioning system in the world. The knives require only 1.5 seconds each to fix into position and can slit labels up to 15mm wide. This is the only system on the market offering this combination. The system can even be operated with a sensor that automatically reads the gaps and then sets the knives,’ says Toksværd.
Modular and connected
In 2015, Grafotronic redesigned all its machines and developed a 100 percent modular concept. Each module is completely independent of the others. A new module can be installed in an existing machine, onsite, in less than eight hours, giving converters freedom to combine new modules and change or add new functions at any time.
‘It’s the only 100 percent future-proof machine on the market,’ says Toksværd. ‘It’s fully modular, which means each module has its own tension control and is therefore 100 percent independent. The standard configuration can include large unwind, flower style flexo printing, lamination, semi-rotary die-cut, full contact matrix removal, on-stop buffer, Sci-Fi knives and semi-automatic turret. The DCL can be standalone, as part of a hybrid set up or in-line with any other digital presses available on the market today. The versatility of this machine is second to none. The most advanced machine we have built so far consisted of 11 different modules.’
The company offers an extensive portfolio of modules covering different end-user sectors such as food, pharma and cosmetics; different labeling formats such as multilayer and booklet labels; as well as turrets, lasers and numerous automation modules. In the future, all these modules, including hot-foil, embossing and screen printing will be added onsite in one working day.
‘Modular has been a mantra in this industry for a long time. But when we say modular, we mean modular for the customer. And not only when owning the machine, but onsite in the future and that’s what we call future-safe,’ adds Toksværd.
In November 2020, Grafotronic released a new system to increase productivity and efficiency for its customers. With Grafotronic Connected, the company’s headquarters in Warsaw can monitor all its customers’ machines in real-time.
‘We can detect any abnormality in machine functions and can act long before something happens,’ says Hubert Stasiński, head of service at Grafotronic. ‘Our service team can take immediate action and guarantee efficient production for our customers. The main idea is that our customers should be in safe hands. We take care of the machine, and they can focus on their business which is label printing.’
Another new feature is the Connected+ application, taking data management to another level. Production managers can find bottlenecks that decrease output from the machines. The application collects data from all Grafotronic machines in the plant, measuring waste, uptime, daily production, overall equipment efficiency and other job statistics.
‘With the Grafotronic Connected service we keep track of all our customers in a cloud-based MIS system with a logbook of all machines,’ adds Toksværd. ‘This allows us to support our customers with various online services. The Connected+ app collects an extensive amount of production data. Supplying this data to our customers means that they’re in full control of their performance and can fine tune their workflow. They have all the information they need to excel in their production and boost productivity.’
The company is planning to focus strongly on its embellishment products. ‘We have hired Luca Goldoni [formerly of Cartes] to drive our wine and cosmetics embellishment technologies. Right after the summer holidays, we are launching a new platform with a series of new screen and hot foil modules,’ says Toksværd. ‘We have invested significant R&D resources in developing the software driving the Lasx module, which is fully integrated with our Sci-Fi Laser series. This provides our customers with seamless workflow integration, highly automated production hand in hand with market-leading production speeds. Together with the coming patented Edgeless technology, Grafotronic is taking the laser die-cutting driver seat.’
Thanks to its Connected services, Grafotronic can currently solve 19 out of 20 service cases online. To take the technology even further, the company will use it to maximize customers' productivity and uptime, with online preventive services combined with data-driven capacity analysis.
‘We strongly believe that being connected – that’s both people and machines – is the future. We insist on being the innovators of this industry and being on the forefront with cutting-edge technology,’ concludes Toksværd.
For more information, go to www.grafotronic.se
Stay up to date
Subscribe to the free Label News newsletter and receive the latest content every week. We'll never share your email address.