Marzek Etiketten + Packaging grows business across Europe
Marzek Etiketten + Packaging is unique as a family-owned business for producing labels, flexibles and cartons with high levels of creativity and a strong sustainability focus.
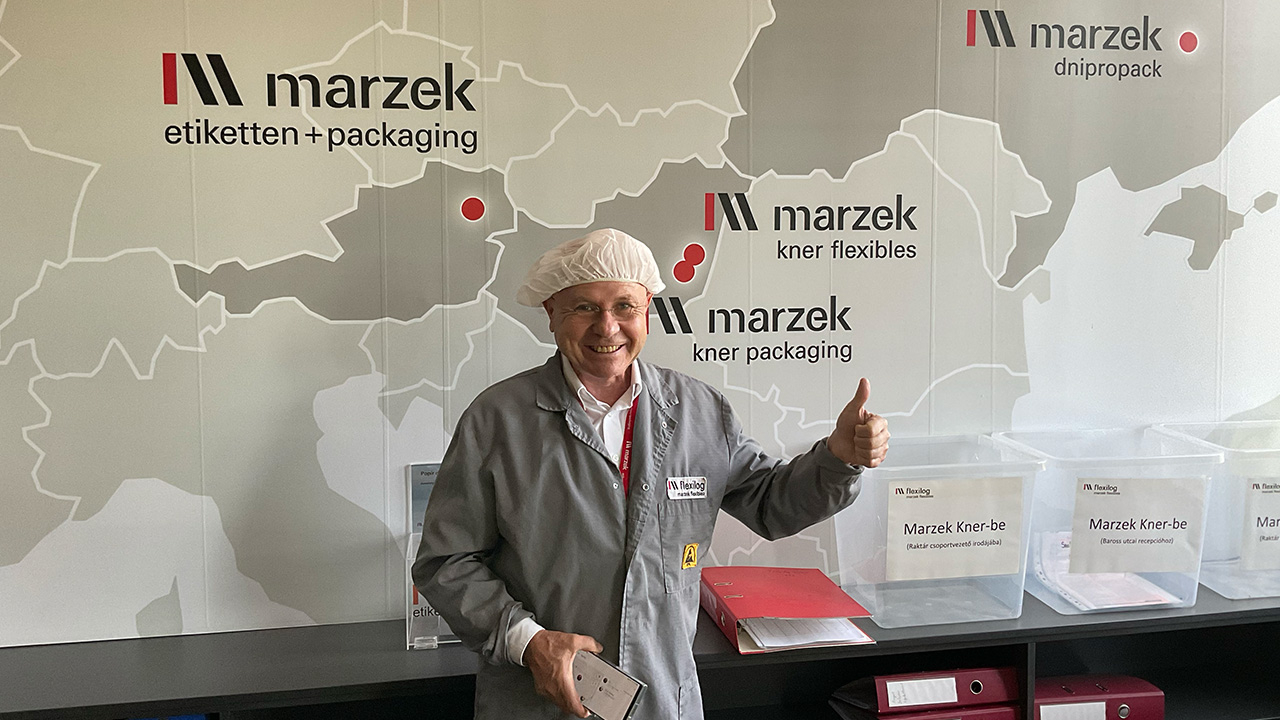
Marzek Etiketten + Packaging remains unique in the European labels market. Not only is the company still fully family-owned – by the fourth and fifth generations of three families – but it covers the full range of package printing applications, from roll and sheetfed labels to flexible packaging and folding cartons, in plants spanning Austria, Hungary and Ukraine. The company has over 700 employees and a turnover of 87M USD (80M EUR).
CEO Dr Johannes Michael Wareka says the Marzek Group is big enough to benefit from cooperation between multiple production sites and international sourcing while at the same time being more agile than bigger, PE-owned labels and packaging groups.
The success of the company can be measured not only in its employee numbers and turnover but also in the multiple Finat and World Label awards it has won for superbly creative label and packaging designs. All these award-winning designs originated from the company’s own in-house creative department.
“In the future, it will be the people who prepare the data who are responsible for quality control, not the machine operator. This is a change in the mindset”
Going forward, Marzek Group is committed to a major ongoing investment program, with a current commitment to invest 17.5M USD (16M EUR) across the group in 2024/2025.
Greenfield flexibles
When L&L last visited Marzek, the company had purchased the flexible packaging operations of Mondi group in Kner, Hungary, and was planning to develop a new greenfield site. That has now been realized.
The flexibles plant operates under the name of M-Flexilog Kft, located in Békéscsaba, close to the existing Marzek Kner Packaging Kft factory. The 25,000sqm site includes 8,500sqm of factory space dedicated to the manufacturing of flexible packaging, pouches, sleeves and wraparound labels. Overall, the value of the four-year investment project exceeded 12.9M USD (11M EUR).
Financing of the M-Flexilog Kft plant was strongly supported by the Hungarian government, which saw it as a major strategic investment for the country. The government not only supported Marzek financially but also sent high-ranking representatives to the inauguration ceremony from the Hungarian Ministry of Foreign Affairs and Trade, as well as the Minister of State for Economic Diplomacy. High-ranking Austrian diplomats, including the Austrian commercial deputy attaché, also attended.
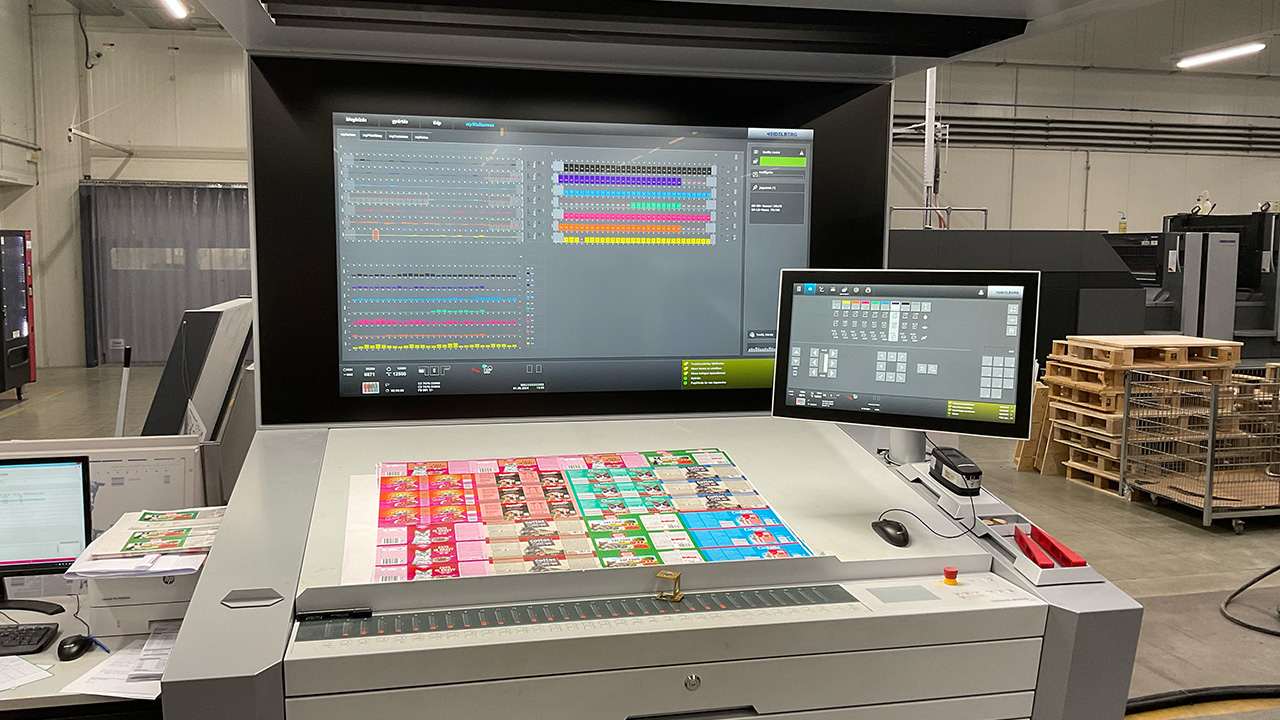
The centerpiece of the M-Flexilog Kft plant is an 8-color solvent-based Windmoeller & Hoeslscher (W+H) Miraflex CI flexo press, installed in 2017. The press runs at speeds up to 400m/min.
The W+H press is complimented by a Nordmecanica Combi 4000 solvent laminator and Soma Venus III slitter-rewinder and a fully automated color mixing system.
The workflow includes an automated 14m-high rack warehouse with induction loops for over 8,000 pallet spaces.
Construction of the M-Flexilog Kft plant was designed to meet high environmental protection standards with state-of-the-art energy recovery systems. The operation complies with BRC/IOP hygiene standards essential for servicing the food and pharmaceutical packaging industries.
“Labels and packaging are all about communicating the product to the consumer. Packaging is a piece of communication”
A short drive across town is Marzek’s folding carton plant, Kner Packaging, housed in a communist-era multi-story building with floor upon floor of state-of-the-art carton printing and converting equipment.
The plant houses nine offset presses, both Heidelberg and KBA, including a short-inking Anilcolor press for shorter runs. Printed sheets go to a fleet of Bobst cut-crease machines and a Gietz 740 foiling machine.
Sheetfed labels
A sheetfed wet glue label plant also operates from the Kner Packaging site.
The plant houses six Heidelberg and two KBA printing machines, each 6-color plus coater, one of which prints with an extended color gamut (ECG) ink set. This means that over 95 percent of Pantone colors can be simulated using the same seven inks (CMYK+OGV), so there is no wash-up of spot color units between jobs.
This brings offset color management into line with digital, where brand owners have shown themselves prepared to accept a 7-color simulation of brand colors. It also means multiple jobs with different Pantones can be ganged across the same sheet, greatly improving efficiency on shorter-run, multi-SKU work.
Running ECG does require that everything about the workflow is standardized, including fingerprinting the press with each different substrate.
Printed sheets are sent to a Polar finishing line, where they are either square cut or die punched and bundled.
Marzek’s wet glue model is to produce at maximum efficiency and allow brand owners to call off stock when required. The company has built its own management information system (MIS) to allow this to happen.
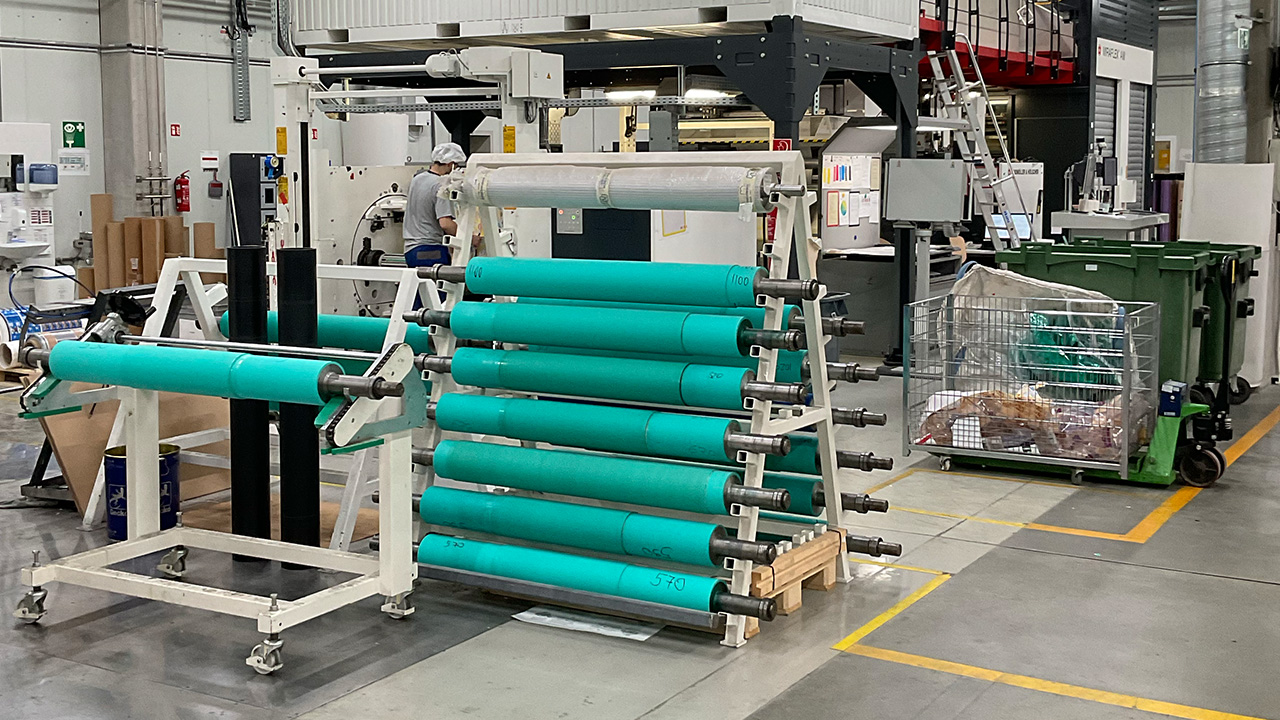
The humidity-controlled warehouse stores some 1,500 SKUs. As soon as an SKU reaches a set minimum quantity, the MIS automatically re-orders a new production run.
‘This means we are free to schedule printing and finishing for maximum efficiency, and our customers are assured of consistent levels of stock at a price set once annually,’ says Wareka. ‘Customers anywhere in Europe can call off their order on Friday, and the next Thursday, they have everything they need. This is our key advantage.’
The sheetfed division processes around 20,000 tons of label materials a year, of which 15 percent is filmic material.
Pressure-sensitive labels
Marzek’s pressure-sensitive label converting operation is based in Traiskirchen, Austria, a short drive from Vienna airport.
The plant runs a mixture of printing processes, mainly offset but also flexo and digital.
For short-run and customized work, Marzek has installed two HP Indigo 6K presses. In fact, the company has been a digital pioneer, installing the first HP Indigo 6000 press in Europe in 2009 and the first 6K press in Austria.
Marzek’s internal label design team has used that experience to push the boundaries of digital print.
An example of this is the ‘Flying Bird’ project, which uses HP’s Mosaic software to generate an animated flying sequence when labels are viewed side by side.
Further creative possibilities are added by the SEI Laser Label Master laser die-cutter.
“PPWR is coming, and it will be relevant to everything we do. Packaging will finally be required to become more sustainable”
The laser die-cutter has been faster than we expected,’ says Wareka. ‘It is also very versatile. It not only eliminates the need to change tooling, but it allows for a vast range of possibilities like security marking, micro-perforation and creating unique and variable label designs, which would be impossible with standard die-cutting techniques. We can score through an ink onto a metallic substrate to create fine embellishments or cut out complex shapes. This in itself is a security feature as it makes the label harder to copy.’
Applying the laser to hot foil creates hologram-like effects that cannot be replicated with a photocopier.
‘The counterfeiter would actually need the same equipment,’ says Wareka, ‘Digital can do so much more than just copying conventional printing. Each collection of labels can be different, and not just the design but the shape. There are endless possibilities. And digital today matches offset quality.’
The multiple ABG Digicon finishing machines add further possibilities for creative design.
The latest Digicon 3 includes two Big Foot hot foil/embossing stations and flatbed silk screen. Marzek has perfected micro-embossing that gives an additional layer of security protection.
Add to this the ability to create a huge range of metallic shades with digital overprinting, and Marzek has a formidable resource for brands looking for truly innovative and secure packaging systems.
Marzek’s offset press fleet consists of three Rotatek Brava presses, which can be switched between semi-rotary and full rotary operation. Additional modules installed since L&L’s last visit include a Pantec Rhino embossing unit, Kocher+Beck automated unwind and ABG turret.
In addition, a 11-color + varnish Omet Varyflex V2 offset press with extended hot air dryer on the varnish station has been transferred from the Kner Packaging site in Hungary.
Marzek Vienna also runs an MPS EFA 530 flexo press equipped with K+B non-stop unwind.
In-line booklet and multi-layer label production is a specialty on these machines.
Offset plates are made in-house with a Kodak CTP system, along with flatbed and rotary silk screen production. Flexo plates are produced on an Esko CDI XPS Crystal 4835.
Automation will be a key component in Marzek’s investment plans. ‘In the future, it will be the people who prepare the data who are responsible for quality control, not the machine operator,’ notes Wareka. ‘This is a change in the mindset.’
Servicing brands
The Traiskirchen operation specializes in designing and printing wine labels, which can be produced either in self-adhesive or sheetfed offset formats. The company currently has over 3,000 different wine label projects open.
The Traiskirchen facility hosts an in-house creative design agency and artwork department that uses Esko WebCenter software to proof 3D virtual prototypes to customers. ‘We have a big emphasis on storytelling when we work with brands across all food and drink sectors,’ says Wareka. ‘Labels and packaging are all about communicating the product to the consumer. Packaging is a piece of communication.’
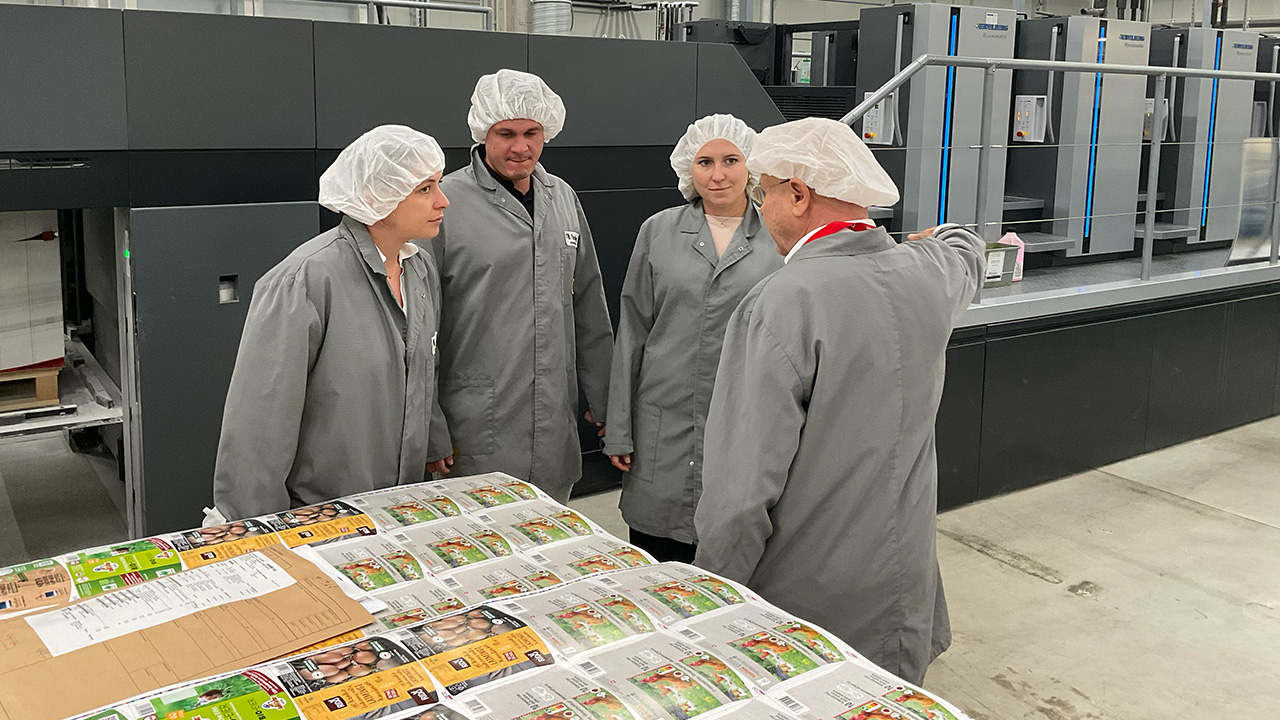
Marzek can leverage its multi-format capabilities to provide brands with coordinated sets of packaging – for example, premium decorated cartons and labels for promotional wine, spirits and beer brands.
The company has made a heavy investment in e-labels, which means linking a QR code or RFID on the bottle label to extensive online information about the product. Marzek provides this as an end-to-end service to brands, including online database management.
As part of its wider service offering, Marzek supplies dispensing systems and thermal transfer printers for point-of-sale and logistics/warehouse labeling.
Sustainable business
Sustainability has become a central topic when discussing new projects with brand customers. This is a core value for Wareka personally, and it has deep roots. ‘I define sustainability as: You should leave for the next generation a better company than you found it. This is the only way to be sustainable, and family-owned companies have always done this effectively.’
Wareka sees the EU Packaging Directive (PPWR), with its three-pronged approach to Reduce, Reuse and Recycle, as the ‘big topic’ in Europe. ‘It is coming, and it will be relevant to everything we do. Packaging will finally be required to become more sustainable.’
The company is developing a range of more sustainable packaging products, including alternatives to non-recyclable multi-layer flexible packaging.
Marzek reports on a wide range of sustainability metrics.
‘We subscribe to SBTI – Science-based target initiatives - which is a reporting system currently very few companies follow,’ says Wareka.
SBTI targets show businesses how much and how quickly they need to reduce their greenhouse gas (GHG) emissions to prevent the worst effects of climate change. The Marzek Group has a wide range of sustainability certifications, including ISO 14001 and FSC.
Marzek also subscribes to the CSRD (Corporate Sustainability Reporting Directive) and the GRI (Global Reporting Initiative), which involve standardized reporting on a wide range of diversity, equality and social responsibility metrics.
The big brands and retail chains are doing this themselves and they are looking for suppliers who also do this reporting, even smaller ones,’ says Wareka. ‘It is an administrative burden for small companies when you add it to ISO and BRC and so on, so this is an advantage for larger companies which have more resources to meet the criteria.’
Sustainability also means reducing inefficiency and waste in the production process.
In conclusion, Marzek is, in many ways, a remarkable company. It has managed to grow into a multi-plant, multi-national scale business while retaining the core values and characteristics of a family-run business, with the next generation fully engaged in the process.
Marzek history
The Marzek company was established by Dr Johannes Michael Wareka’s grandfather in 1879, making Michael the fourth-generation CEO. His three children are now fully involved in the business: Oliver in customer relations, Marie in accounts, and Stefanie in marketing. On a day-to-day basis, the Marzek Group is run by a board, and a new COO has just been appointed, taking up position in January. Michael Wareka will remain as CEO centrally involved in Marzek’s future strategy.
Center of the storm
During the eastward expansion from its base in Vienna, Marzek has found itself at the center of historic European events.
The Hungarian packaging operation was originally a communist-era state-controlled business with 1,500 employees. After the collapse of the Soviet Union, the operation was privatized and broken up. When Marzek acquired the business in 2005, there had been literally no investment since the early 1990s and only 120 employees remained.
Today, there are 500 employees in Marzek’s Hungarian business; there has been a major investment in modern equipment. Production volume has expanded by more than six times.
Then there is Ukraine.
Marzek started manufacturing in Ukraine in 2009. The Marzek Dnipropack plant is situated in the east of the country, worryingly close to the front line of the conflict with Russia.
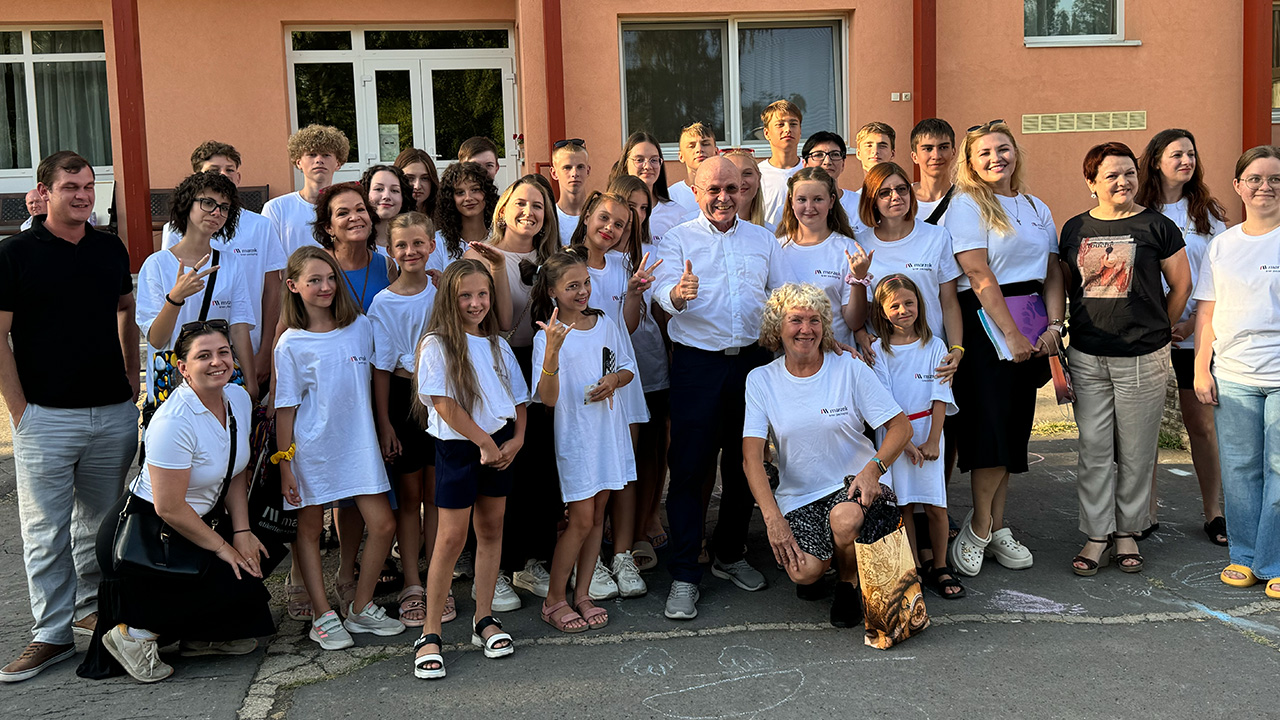
‘In Ukraine, we are still producing, even under very challenging circumstances,’ says Michael Wareka. ‘If there was stability there, the growth rate would be in double figures.’
To help provide some relief, Marzek arranges for groups of its employees’ children to be brought across the Hungarian border to spend two weeks resting and recuperating in Békéscsaba, close to where Marzek’s packaging plants are located.
Marzek’s employees, led by Wareka and his family, arrange parties and excursions and the children all stay together in a hostel donated by local people.
‘It is challenging making all the arrangements to bring the children over the border. The Hungarian government can be hostile towards Ukraine, but the people of Hungary are amazing and welcome the children with open arms to their country,’ says Wareka.
Stay up to date
Subscribe to the free Label News newsletter and receive the latest content every week. We'll never share your email address.