Omet sharpens flex pack focus with X7 demo
Omet’s XFlex X7 mid-web press was demonstrated at a flexible packaging-focused open house that also included a visit to film converter ACM
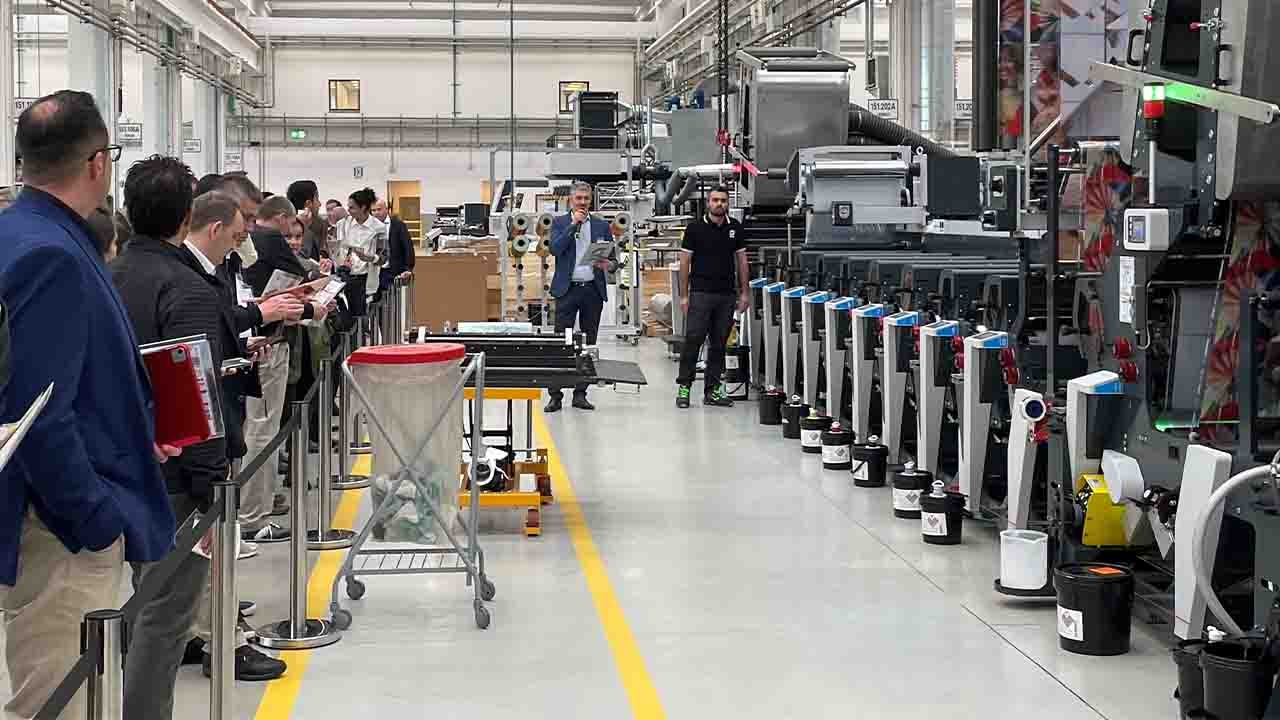
In May Omet hosted an open house dedicated to flexible
package converting at the company’s Innovation Park, its new permanent showroom and demo center in Molteno, Italy.
Over 60 visitors attended the event that featured live
demonstrations of flexo printing of shrink sleeve labels on a
mid-web Omet XFlex X7.
This was followed by a visit to flexible packaging specialist ACM Spa in Cremosano, who were printing shrink sleeve labels and flexible packaging on an XFlex X7 and Varyflex presses.
The press was shown printing a high-quality shrink sleeve label, 8 colors UV flexo plus cold foil application, with two extended dryers for soft touch matte varnish application and an embossed varnish
Marco Calcagni, Omet sales and marketing director, opened the event with a speech that emphasized the increasing customization of the presses manufactured by Omet today, with tailor-made configurations making use of Omet’s R&D expertise.
Focus on sustainability
The open house hosted a presentation by Fabrizio Radice of Corapack, who focused on new compostable and biodegradable flexible packaging materials. The application was for dry pasta containing anti-fog additives.
The packaging utilizes Planet Ethic’s PLA film. ‘This has
characteristics similar to polyethylene and polypropylene,’
says Radice. ‘It is transparent and with excellent resistant
characteristics. It can be printed with OK Compost certified inks in four colors with excellent results not inferior to the printing of oil-derived film.’
Radice says the film degrades in about 70 days in an industrial composting center, where it is transformed into fertilizer. ‘Waste quickly becomes a useful and natural resource. Furthermore, PLA is produced with natural and renewable raw materials and not from petroleum.’
Radice stressed the difference between biodegradable and
compostable film. Biodegradable films are degraded by biological agents and break down into simple substances – water, methane and carbon dioxide – and there is no clear guideline for how long this process will take.
‘The composting process uses aerobic biodegradation,’ he says. ‘A mature compost looks like loam and contains the nutrients useful for agriculture.’
Tony Parsons of Nazdar brought delegates’ attention to UV-LED inks for packaging, with some guidance on the use of inks for food-contact packaging.
Daniel Yjord of Flexowash spoke about the importance of
automated plate and anilox cleaning with a live demonstration of the Flexowash machines installed at the Innovation Park.
Yjord stresses that thorough cleaning of anilox rolls, particularly on high count jobs, is key to print quality and color consistency.
‘Our customers have seen this leads to a decrease in setup time and a reduction in print stops, as well as the elimination of cleaning solvents, and means operators can focus on running the press,’ he says.
Experience in the field showed that improperly cleaned anilox and plates led to over three hours of press stoppage time a week, culminating in costs to the business of almost 30k Euro. ‘This means the payback for an automated cleaning system is between six months and two years,’ Yjord says.
Silvano Tamai presented Tesa’s technology for mounting plates, focusing on the Twinlock compressible self-adhesive sleeve onto which flexo plates can be directly mounted. ‘This allows converters to eliminate the use of double-sided tape, which leads to a reduction in waste and transport emissions, improving your overall carbon footprint,’ says Tamai.
X7 demo
At Omet’s headquarters, guests saw a printing demo on the XFlex X7, optimized for flexible packaging and shrink sleeve labels. The XFlex X7 combines the best features of both the XFlex X6.0 and Varyflex V2. It is a 670mm (26in)-wide mid-web press designed for printing unsupported film down to 9 microns.
The XFlex X7 incorporates motorized printing pressure
adjustment on anilox and impression cylinders, Multivision cameras for automated register control on each printing unit with on-the-fly pre-register. The press was shown printing a high-quality shrink sleeve label, 8 colors UV flexo plus cold foil application, with two extended dryers for soft touch matte varnish application and an embossed varnish. The press can also be configured with a 670mm-wide rotary screen unit and high-value rotogravure unit, which is capable of both surface and reverse printing and equipped
with an integrated chill drum.
This demonstration job required holding stable print register at high speeds, demonstrating the effectiveness of Omet’s Zero Gears system, which combines direct drive with anti-bounce technology.
Stay up to date
Subscribe to the free Label News newsletter and receive the latest content every week. We'll never share your email address.