Sustainability trends boost wet glue label appeal
Glue-applied labels remain the dominant form of prime product labeling, providing key volume, sustainability and print quality benefits for end users
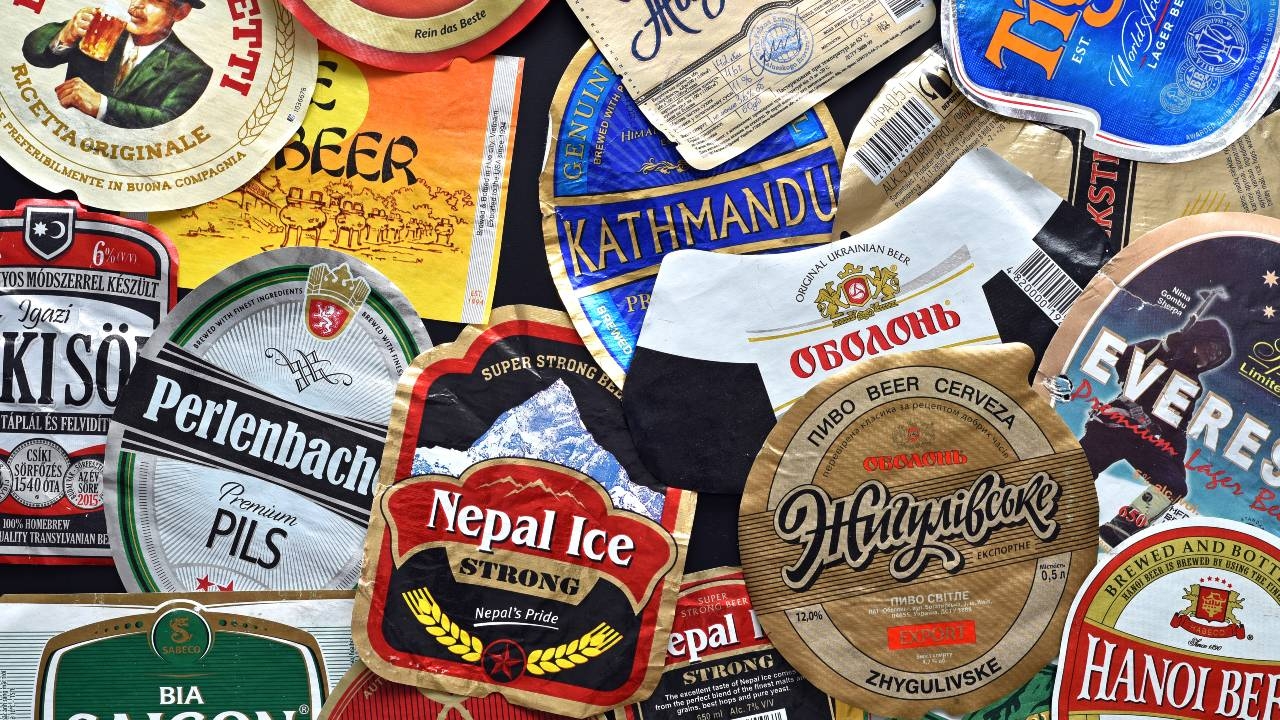
Despite the consistently higher growth rates of pressure-sensitive and shrink sleeve labels, glue-applied labels remain, by far, the dominant method for prime product labeling.
How do we define a glue-applied label?
Wet glue labels are printed in sheets – or on rolls that are sheeted – then cut or die punched into single labels and stacked into a magazine, which is inserted into the label applicator. Glue is then applied to the reverse side of the label, either to the whole label or to the leading and trailing edges, and the label is applied to the container.
A second type of glue-applied label is the roll-fed wraparound label. These are delivered to the label applicator on a roll, then cut on the machine into single labels and adhesive (usually hot melt) is applied to the leading and trailing edges.
According to figures compiled by the AWA consultancy, glue-applied labels account for just one-third of the 71 billion sqm of labels consumed annually, against 41 percent for pressure-sensitive labels. But when we consider only the primary (prime) label market, glue-applied represents 44 percent of total label volume compared to only 23 percent for pressure-sensitive. The remaining PS volume goes to industrial and VIP labeling.
The market share of glue-applied labels is markedly different in different regions of the globe, reflecting different levels of development. Generally, the more developed economic regions show a higher percentage of PS and shrink sleeve compared to glue-applied.
Thus, according to AWA’s figures, glue-applied has the highest market share in Asia, representing 46 percent of all label consumption. In the Americas, glue-applied represents just 14 percent of the market and in Europe 20 percent. The figures for Europe hide important regional differences however: the consumption of glue-applied labels is higher in eastern and southern Europe compared to the north and west, where pressure-sensitive and shrink sleeve labels have made a bigger dent in glue-applied volumes.
The key end-use markets for glue-applied labels are in the labeling of drinks bottles and canned human and pet foods. Of the 25 billion sqm of glue-applied labels consumed annually, 70 percent goes to the beverage market and 23 percent to the food market. The remaining 7 percent is mainly used in the household chemicals and automotive segments. In Europe, beverage applications account for 84 percent of wet glue volume, with food representing 12 percent.
Glue-applied labels have applications across a wide range of container types including cans, jars, bottles, composite tubes and boxes. As well as appearing as body and neck labels, glue-applied labels are also used as top straps over the closure as a tamper-evident or security feature.
The key glue-applied end-user markets are characterized by high volume, low margin and highly industrialized production systems. Label converters in this sector are highly automated and consolidated operations compared to the self-adhesive label converting sector.
Converting Process
Glue-applied labels are supplied by the converter in either traditional cut & stack wrapped bundles or on a reel. Cut & stack labels are either cut to shape or ram-punched into specific profile shapes compatible with the container profile. These are also referred to as patch labels. Cut labels are rectangular or square in shape, and this profile is suitable for 360-degree wrap-around decoration or patch labels.
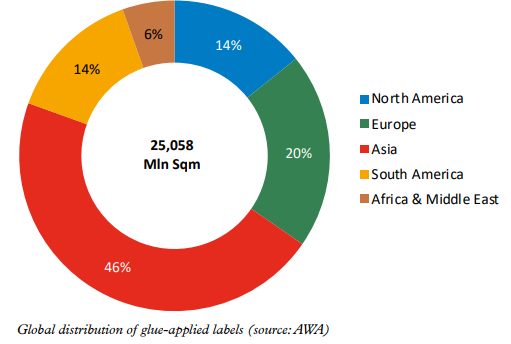
Glue-applied labels can also be supplied in reels for 360-degree wraparound decoration. These are not pre-cut to shape but cut singly from a reel at the point of application.
Cut & stack labels are manufactured in a multi-stage operation starting with the printing of label sheets on an offset-litho press. If subsequent processing is required – for example over-varnishing, foil blocking, embossing or bronzing – the printed sheets are moved to different workstations on the production floor.
The finished sheets of labels are then guillotined and square cut or profile punched, batched, packaged and palletized. Manufacturing using this multi-pass process can have a production cycle of several days, or in some instances several weeks dependent on the quantities required, with perhaps 10 people involved as sheets pass through the printing, embellishing and converting processes.
High-volume wet-glue labels can also be printed on a web-fed gravure press. The printed reels are transferred onto a sheeting unit which can be an in-line or off-line for further processing. The production of roll-fed wraparound labels is a simpler process involving high-speed printing on CI flexo, gravure, or mid-web inline presses, with or without lamination. The rolls are slit to width and delivered to the packer.
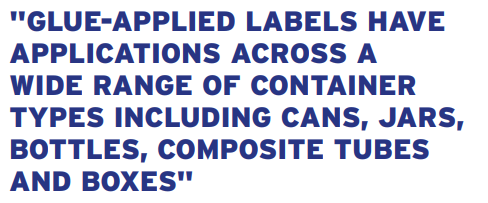
Materials
A wide range of both paper and filmic label materials are available for glue-applied label applications.
Wet glue label papers are available in a range of formats: standard, wet strength, humidity and alkali resistant, embossed, cast coated/high gloss and metalized, covering all the technical and marketing requirements of the end-user market. They are also suited to a wide variety of other applications such as box covering, lamination, food wrapping and interleaving.
Wet glue papers are available in either coated or uncoated grades. Uncoated paper has a low gloss level, greater absorbency and is less suitable for quality image reproduction. Coated papers, available in matte coat, semi-gloss, gloss and cast-coated grades, have a coated gloss/reflective surface, lower absorbency and are more suitable for quality image reproduction.
A range of specialist craft/antique papers are available specifically for wine labels and craft beverages.
When selecting papers for use in wet glue label applications, a range of performance factors must be considered: direction of the grain and the resulting effect on label curl in uncontrolled humidity; substrate moisture content during storage and transportation; humidity levels in the printing environment; and humidity levels in the filling and label application areas.
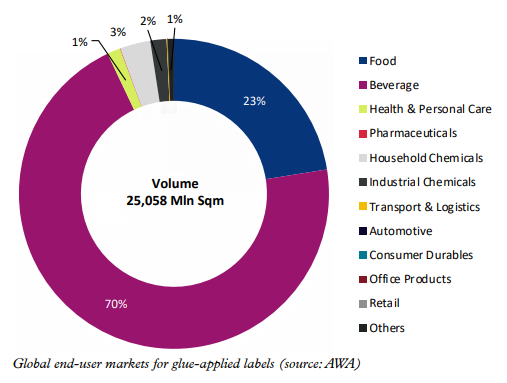
Films are available for both cut & stack and roll-fed wraparound applications. Films are usually selected for performance reasons, typically for applications requiring durable moisture resistance, chemical resistance, wet strength and burst resistance on large PET bottles.
These films are available in transparent, opaque (white) and metallic grades and are supplied both for surface printing and for lamination.
To run smoothly and efficiently on the applicator line, reel-fed wraparound films need to combine controlled stiffness with anti-static properties, web flatness and strong ink and adhesive compatibility. A key trend is to downgauge the filmic material to get closer to the economics of paper labels.
Examples of the new generation of filmic wraparound labels include Innovia’s RayoWrap ETF transparent label film, targeted at no-label-look monoweb applications without requiring lamination, while the company’s RayoWrap LRH is a high-yield, white label film. Jindal’s Label-Lyte OPP film is targeted at beverage applications using reel-fed, wraparound glue-applied labels, and is available in clear, white and metalized grades for both lamination and surface print applications.
Jindal also provides films for wet glue cut & stack magazine-fed labeling. These films are coated on both sides to provide litho printability and compatibility with a broad range of wet glue and hot melt adhesives on the reverse side.
Decorative Effects
Although cut & stack labels are targeted at low-cost, high-volume applications, there is a wide range of decoration options available to add value to each product category.
Gloss lacquers, for example, are used on the face of glue-applied labels both for scuff resistance and increased shelf impact. For lithographic printing, the norm is UV lacquers, while photogravure printed labels use a range of solvent and water-based lacquers.
Embossing is used where a specific part of the design needs to be raised to enhance the label’s appearance. With gravure printing, in-line all-over or partial embossing is possible, producing a tactile feel to the label – particularly effective when used on metalized paper labels.
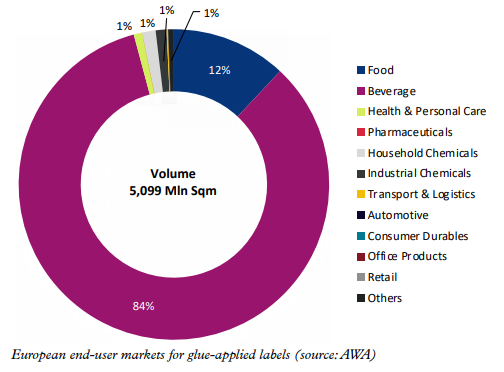
For metallic effects, foil-blocking is available as a separate process step on wet glue labels in a wide range of colors. Foil laminate and metalized papers are also available, offering a reflective metallic finish that can be over-printed. The superior transparency of offset inks allows high brilliance levels to be achieved in these applications. Holographic effect wet-glue label papers are also available.
Wet glue labels can be die punched in complex shapes, which, combined with embossing or other textural elements, delivers an effective promotional tool for high-end premium products.

Label Applicators
Cut & stack labeling machines operate by applying glue to the back of each label before applying it to the container. There are two main types of adhesive used. ‘Wet’ glue is water-soluble and liquid at room temperature and is the most common type of cut & stack adhesive. The second adhesive type is hot melt, a solid glue that is heated to become a liquid.
The adhesive can be applied to either the full area of the reverse side of the label or by gluing the trailing and leading edges. The type of adhesive application can be selected from options such as skip, pattern or stripe, depending on adhesion, application speed or drying speed required.
When labeling cans, the adhesive is first applied as a stripe to the container and a second stripe of adhesive is applied to the trailing edge of the label as it rotates over the label magazine.
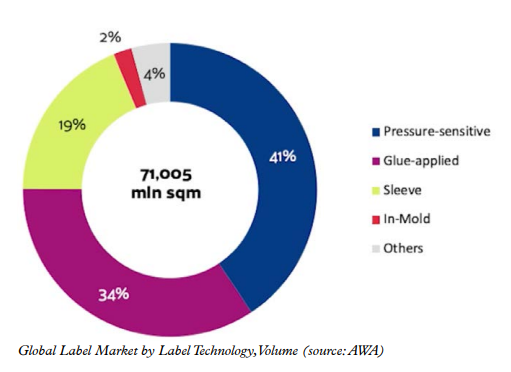
Wraparound roll-fed glue-applied labels typically use hot melt technology. Several kinds of hot melt adhesives are available to suit different purposes, such as particular packaging materials or the conditions within the factory environment.
A wraparound hot melt labeling system consists of two gluing units. The first applies a vertical strip of glue which adheres the label to the container, while a second unit applies glue to the trailing label edge as the label is wrapped around the container.
It should also be noted that there is a third type of wet glue labeling machine using pre-gummed labels. In the pre-gummed system, labels are pre-coated with glue, then water is applied either through dipping or spraying to activate the adhesive properties of the glue. As techniques and materials have developed, however, the pre-gummed labeling method has waned in popularity in favor of wet glue and hot melt systems.
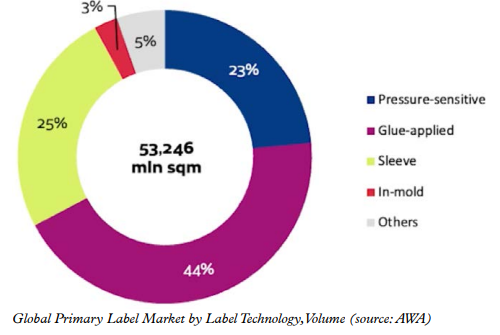
Wet Glue vs Self-Adhesive
The choice between wet glue, glue-applied roll-fed wraparound and self-adhesive can be a complex one when the Total Cost of Ownership (TCO) is considered. TCO includes a wide range of factors including material costs, printing and conversion costs, manufacturing window/lead time, application equipment investment, operational cost of application lines, application flexibility, application speed, application downtime, and logistics.
Wet glue labeling offers the lowest per-label cost of all methods of label decoration. This starts with the offset-litho provides itself, which provides excellent reproduction of photographic designs, tone-work and metallic colors with relatively low plate costs.
Another press technology factor moving the TCO dial in favor of wet glue labels is the increasing use of in-line technologies on sheetfed offset presses, which can dramatically shorten lead times. Offset-litho presses for wet glue labels are already equipped, pretty much as standard, with single or dual UV coaters or extended delivery hot air dryers for water-based coatings. And more processes are going in line.
Germany-based Cito group, for example, has been adding in-line capabilities to offset presses for scoring, cutting and perforating. UK-based wet glue specialist Gavin-Watson says it can now save several hours in the production of orders using the Cito equipment.
‘This technology has become the standard which is now completely indispensable. From a bespoke shaped perforation to a scored, perforated and part forme cut project.’
Offset litho technology also benefits from higher levels of industrialization and automation than a typical PS label converting operation, along with a fully standardized color management process from design and proofing to print. Heidelberg’s Prinect Image Control, for example, controls every stage of the workflow from prepress to press using a single measuring system.
Some converters have their own in-house offset color management systems – Inland Printing is a good example with its InColor technology, which ensures color standards are met before live production takes place.
Automation has also been happening on the cut & stack finishing line, both for square cut and die punched labels. The ability of sheetfed offset presses to gang multiple jobs up on the same sheet, added to automated finishing, has allowed the economic production of shorter runs and smaller batches, as well as reduced cycle times.
Polar, for example, demonstrated at Labelexpo Europe 2019 an automated finishing system for small to medium-sized runs of both square-cut and die-cut labels. The LabelSystem SC-25 allows two strips of square-cut labels to be processed simultaneously to produce up to 1,560 bundles an hour. The LabelSystem DC-11plus was demonstrated carrying out automated in-line production of die-cut labels. A counter pressure system allows the processing of non-paper materials such as compressible plastics or metalized foil.
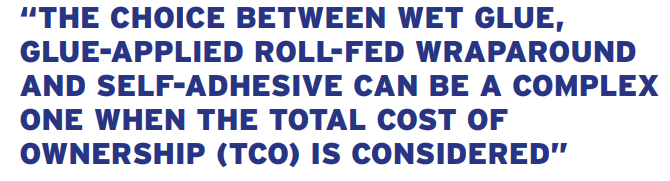
Sustainable Solution
From a sustainability viewpoint, glue-applied labels have several key advantages. Most obviously there is no waste matrix or liner to dispose of. Wet glue labels applied with water-based adhesives can be easily removed from returnable bottles in a caustic wash bath, while a new generation of alkali-based washable hot-melt adhesives now allows these labels to be washed off cleanly as well. Modern conventional offset inks are non-bleeding, avoiding contamination of the alkaline water wash.
Generally, UV offset inks are specified for one-way (non-returnable) containers. In addition, companies like Inland Packaging are now offering soy-based offset inks as a more eco-friendly option, as well as water-based gravure.
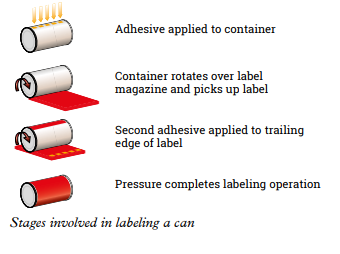
Downsides of wet glue labels include the multi-stage sheetfed manufacturing process. Lead time becomes more of a factor when the specification requires multiple embellishment processes such as hot foil-stamping, embossing and lamination, all of which require separate steps in a sheet-fed workflow.
The ability of inline self-adhesive converting equipment to print and embellish in one pass considerably reduces the manufacturing time frame. In addition, wet glue labels cannot be applied to highly shaped areas of containers, and paper labels have limited moisture resistance compared to plastic labels unless specially developed for ice bucket resistance.
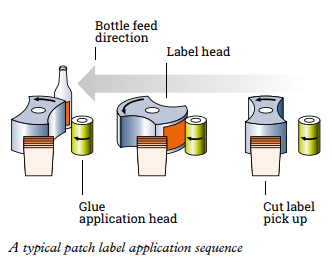
Wet glue applicators tend to require higher investment, including change parts and adhesive, while self-adhesive label application equipment requires fewer resources to set up and does not require labels to be stacked in a magazine before application.
Against that, as we have noted, self-adhesive labels are more expensive, as they include the cost of the liner and the ready-applied adhesive.
Label applicator speeds are not as wide apart as they once were, so this is not usually a factor differentiating wet glue from self-adhesive. Wet glue labelers typically operate at speeds around 600 units per minute, against around 500 per minute for PS applicators.
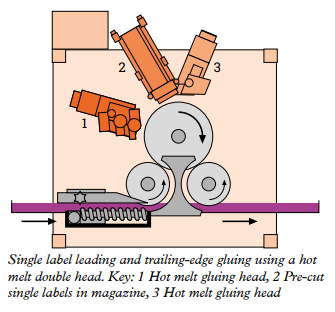
Paper Investment
Paper manufacturers are gearing up for increased production of added-value wet glue papers as the industry recovers from the intense paper shortages caused by a combination of forestry strikes and supply chain disruption.
Sappi, for example, is investing heavily in wet glue label production at its Gratkorn mill in Austria. The double-digit million-euro project includes a new embossing calendar, enabling the paper mill to produce high-quality wet-strength wet-glue label papers from Q4 this year.

Robert Gabriel-Jürgens, head of label paper sales at Sappi Europe, explains: ‘Extensive technical innovations in the paper machine’s water and material cycles are planned, as well as investment in the new embossing calendar. This is key to producing the kind of wet-strength, wet-glue label paper used in the beverage industry, for instance on returnable beer bottles, and to enabling the production of exceptional, high-quality labels.’
Gabriel-Jürgens says Sappi is seeing increased demand for wet glue label papers. ‘Paper-based products give sustainability benefits, including the use of water-soluble adhesives. We also see a (wider) trend towards fiber-based products, with paper of growing interest to brand owners.’
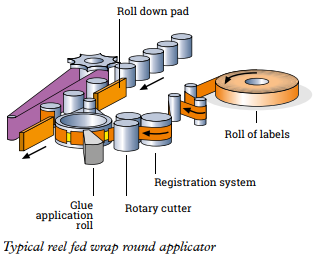
Sappi has also been developing a new range of non-wet-strength, wet-glue label papers. The Parade Label Pro is designed for applications including standard labels for bottles, tins and jars, as well as wrappers. So, despite the continued inroads made by self-adhesive and shrink sleeve labels, particularly in the more developed markets, the usage of glue-applied labels continues to grow at a healthy rate.
Driven by moves towards sustainability and continued automation, Consultancy Research and Markets forecasts the glue-applied label market to grow by 5.94 billion sqm between 2022 and 2027, accelerating at a CAGR of 4.99 percent.
For more information on glue-applied labels, visit www.label-academy.com
Stay up to date
Subscribe to the free Label News newsletter and receive the latest content every week. We'll never share your email address.