From color pains to performance gains
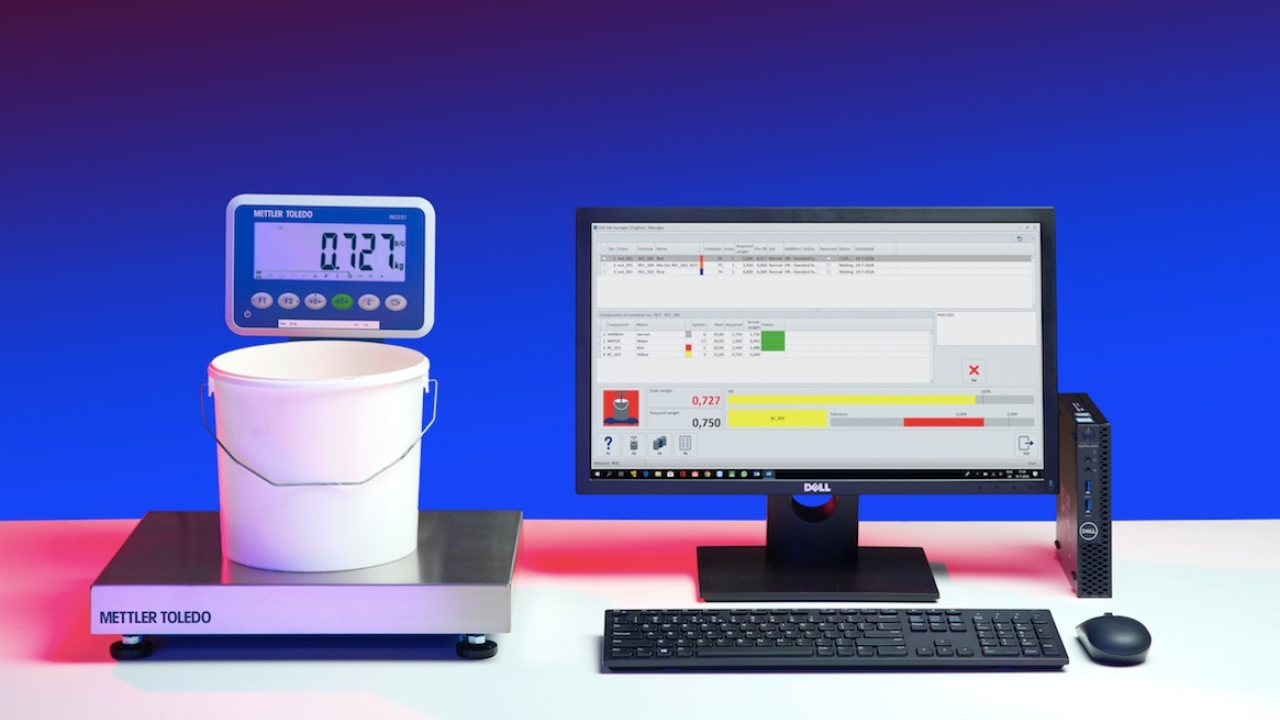
In conventional process printing for labels and packaging, spot-color printers must control ink-related processes with care to deliver quality, limit costs and maintain uptime. Mixing the right shade requires extreme accuracy. Without computerized equipment, the color making process is unreliable, causing delay and heavy substrate waste. Other spot-color challenges include managing inventories, reusing press-return inks and economical procurement. Appreciating ink’s total ownership cost is therefore critical.
The goal of ink management is getting consistent, repeatable quality, while limiting expenditure of ink-related resources to create customer value. Ink dispensing systems, for creating spot colors accurately and fast, are crucial for achieving this. They are available for flexo, gravure, offset and letterpress processes, and all label and packaging applications.
Automatic ink dispensing systems dose exact shades and volumes by calculating and mixing the recipe from connected barrels of base colors. The operator enters the target color and volume requirements into the interface; a computer calculates dosage volumes and activates the blending. These are suited for flexo, gravure and screen processes.
‘Manual’ dispensers feature precision scales plus computer, keyboard and interface. The computer calculates the recipe as above, but the operator adds and mixes the ingredients. Easy to self-assemble, these require lower capital investment and are suited for all conventional process inks. An example is GSE’s new Colorsat Formula Checkweigh System. Generally, if yearly UV ink consumption is over 3T, automatic systems are best. The figure is higher for water-based inks, which are cheaper.
The following checklist of benefits and costs can help you determine the most suitable dispensing system for your printing needs.
Benefits
Lower ink prices: purchasing basic inks in bulk instead of ordering ready-mixed inks means better prices. Mixing your own colors eliminates import duties and taxes on ready-mixed inks.
Lower transport costs: transport of base colors from your supplier is cheaper than transporting small batches of ready-mixed colors.
Lower ink consumption: dispense the right quantity on-demand, instead of ordering excess amounts of ready-mixed inks ‘just in case’. ‘Press-return’ inks remaining after the job can go into new recipes. Ink consumption levels can be cut by up to 30 percent.
Less ink and substrate waste at job change: the ink dispenser’s precision means colors are first-time-right, reducing substrate and ink waste due to ‘trial-and-error’. Mixing is faster, enabling swift job setups and more uptime – especially with repeat jobs that can be easily recalled from a dispenser’s recipe database.
Lower ink stocks: inventory is simpler because all shades are mixed from a limited number of base colors, with no ready-mixed inks, while ‘press-return’ inks are swiftly reused. Managing fresh and return-ink stocks is optimized with ink management software.
Reduced ink containers and discharging costs: inks for a dispenser come in larger containers instead of buckets, reducing container costs and the costs of discharging polluted packaging.
Fewer indirect tasks: reduce the shipment, handling and carrying of inks by installing the dispenser near the printing press. There are also fewer purchase orders and administrative tasks.
Importantly, consider also the added value of the dispenser’s ink management software. For instance, GSE Ink manager (GIm) has optional reporting, scheduling and machine connectivity modules, including real-time costings and stock reports, ink batch traceability, and the possibility to integrate with ink formulation and management information software. GIm comes with all GSE ink dispensers, and can be retained when upgrading to a higher-volume dispenser. Its connectivity makes a manual dispenser capable of integrating peripheral operations – like a legacy letterpress press or a complementary folding carton division – within the corporate MIS.
Costs
Consider both capital and operating costs in your calculations. Capital costs comprise the dispensing system, transport, system installation, training, plus costs of preparing the ink room, i.e. infrastructure, electricity and air supply.
Operating costs, associated with operating, cleaning and maintaining the system, include dispensing speed and desired accuracy; user-friendliness and functionality of the ink management software; ease of exchanging base inks (e.g. with drum modules); dripless valve design, valve cleaning system and a stainless steel dispensing area; modular system design, easy accessibility to key technical components and (remote) help from the equipment supplier.
Calculating the return of investment depends on your typical business situation, print operation, substrate and applied ink technology. Managing ink and mixing color was once a hindrance to quality and profitability. Not now: the right dispensing system can give many years of happy returns in a service-driven, fast-moving, quality-conscious supply chain.
Stay up to date
Subscribe to the free Label News newsletter and receive the latest content every week. We'll never share your email address.