Are wet glue labels ready for disruption?
The wet glue label market is highly commoditized with limited opportunities for personalization, and one where efficiency is key. Is it ready for the level of disruption we’ve seen in other label technologies?
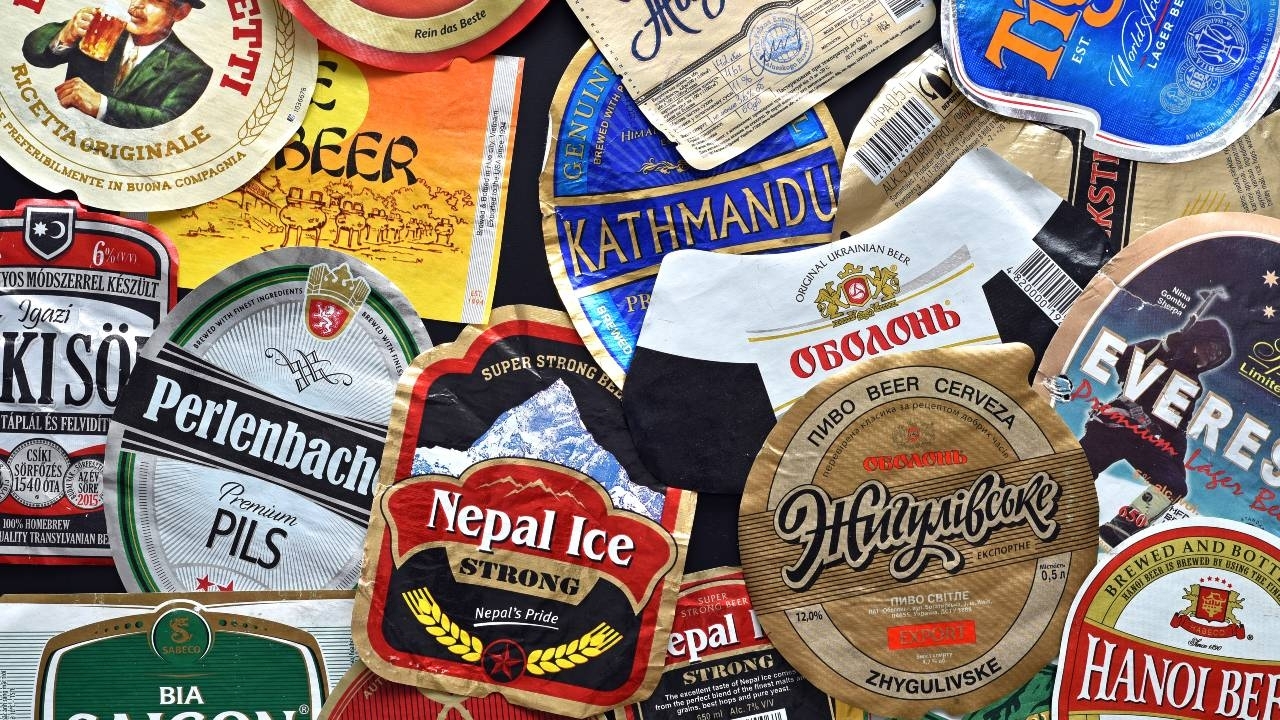
Despite the consistently high growth of pressure-sensitive labels over the last 20 years and the recent boom in shrink sleeve labels, glue-applied labels remain the most widely used prime label technology.
Consultancy Research and Markets estimates the paper glue-applied labels segment will reach a value of USD 19.7 billion by 2030 with a CAGR of 4.5 percent year-on-year from 2013.
Trends towards sustainability are likely to boost wet-glue label volumes, particularly for returnable glass containers in the beverage and food industries and where brands are moving away from plastics.
Wet glue label production is all about efficiency. This is overwhelmingly a commodity market apart from value-added niches in high-end wines and spirits, so driving down the cost of production through automation and process control is critical.
Apart from a small amount of gravure for high-volume production, wet glue is overwhelmingly a sheetfed offset process followed by multiple off-line decoration and converting steps.
Apart from the continued application of automation and robotization to wet glue finishing machinery, the separate process steps have remained fundamentally unchanged. Adding hot foil stamping/embossing, for example, requires a further process step and more work in progress, along with pallets of sheets waiting for their turn on multiple converting stations.
So, are there any disruptive technologies on the horizon?
drupa developments
At drupa we saw the rise of the second and third generations of digital sheetfed technology, both toner and inkjet, and the announcement of the Heidelberg-Canon partnership to transition Heidelberg to digital sheetfed production.
However, it seems unlikely digital will disrupt the wet glue market in the same way as the self-adhesive and now flexible packaging sectors.
Wet glue, as we have noted, is generally a highly commoditized market with limited opportunities for personalization.
In addition, offset printers are skilled at ganging multiple jobs across a sheet to produce shorter runs economically and using extended color gamut ink systems to hit Pantone colors without the need to wash up spot colors between jobs. Add to that the high levels of automation of conventional offset seen at drupa and the low cost of plates and it is difficult to see much space for digital.
What about in-line production? We can easily imagine a combination press set up to handle multiple decoration processes in line, but what about finishing? One possibility is that labels could be sheeted and then fed into a conventional wet glue finishing line.
What about fully in-line production from print to finished bundle? Interestingly, that technology has been developed.
History lessons
In 1998, Jarvis Porter – then one of the UK’s leading label converting groups – invested GBP 2.5m in a self-contained 15,000sqft unit created alongside the company’s conventional label operation in Leeds to develop a fully in-line process from print and decoration to finishing and packaging of wet glue labels.
The 520mm-wide press, called GN520, was a joint development between Nilpeter and Goebel. It was made up of nine interchangeable print stations able to run offset litho, rotary screen, UV flexo, foil and embossing on any station.
The key to single-process manufacturing was a Kuglar-Womako label line specially configured for use in line with the GN520 printing press.
The web was fed out of the printing press via a turner bar into the Womako, which then slit and cross-cut the printed web into deep-piled strips, boarded top and bottom, ready for either square cutting or profile punching. Automatic waste extraction operated throughout.
“It seems unlikely digital will disrupt the wet glue market in the same way as the self-adhesive and now flexible packaging sectors”
Using print mark register controls, a host of previously manual operations were eliminated. Automatic waste expulsion, aeration, jogging, knocking up stacks, and guillotining were now done automatically and with startling accuracy.
Servo controls allowing cutting at 2,000cpm, or slitting of the web at plus or minus 0.1mm tolerance and a maximum mechanical speed of 200m/min was achieved.
Slitting used rotary knives, registering to the marks at 0.1mm accuracy with three rotary knives, working against a bottom knife to cross-cut a web into sheets. Up to 1,250 sheets 90mm in height, were then stacked. The strips for profile die-cutting were then transported automatically to a Blumer Atlas system for profile punching and they were then counted, batched and banded before a VCH autobox unit boxed and conveyor-delivered the final product ready for despatch.
Sadly, after three years of development work, the Jarvis Porter Group was broken up, meaning that the unit was never put into full commercial production. Nevertheless, it proved that the technology worked and there was indeed a ‘better way’ to manufacture wet glue labels. Perhaps there are others?
Stay up to date
Subscribe to the free Label News newsletter and receive the latest content every week. We'll never share your email address.