Harness the power of lean processes
Small efficiency gains can translate to quantifiable wins when lean manufacturing is implemented, writes Brian Van de Water, CEO of SPL Consulting, LLC
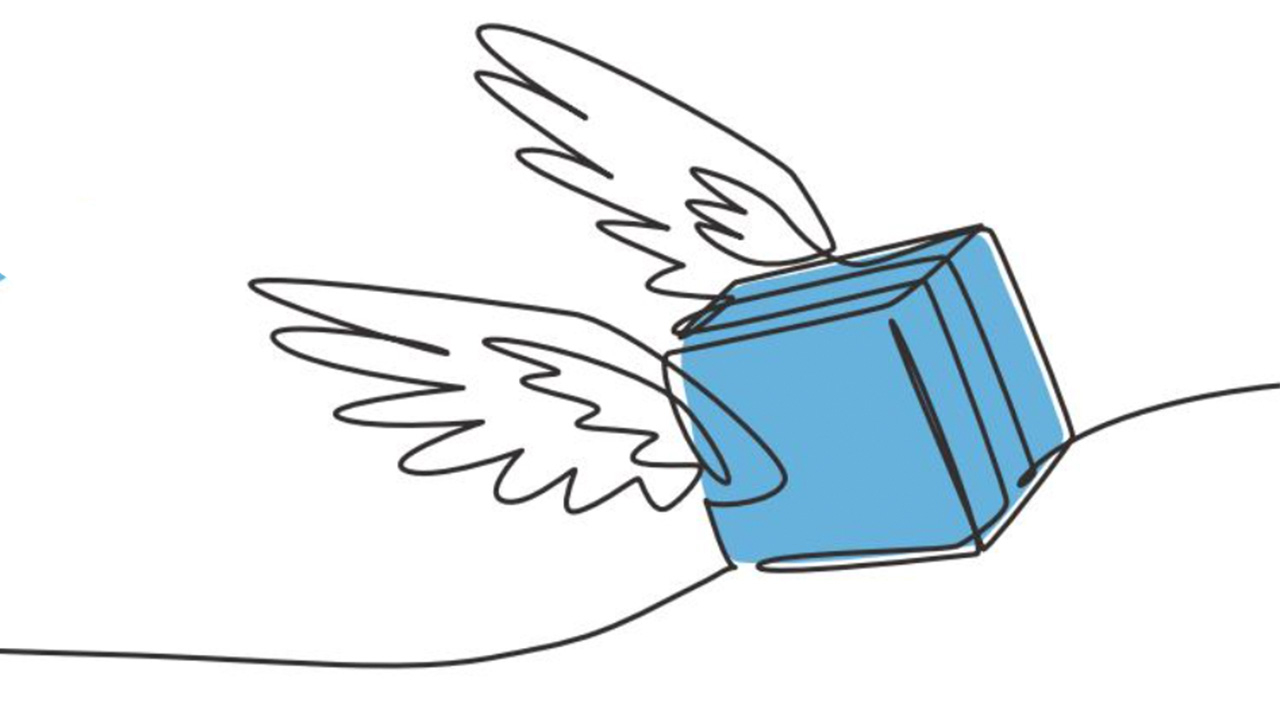
As SPL Consulting, LLC works with clients across printing and packaging industries, we often uncover that many companies are familiar with lean as a methodology for improving performance and even have teams focused on continuous improvement.
SPL polled a large group of senior executives about lean manufacturing and asked how many had documented over 1,000 hours of capacity generated in the last year. Roughly
15 hands went up out of nearly 200. I then asked how many had documented over 5,000 hours. Five hands were raised (three of them were SPL clients). Let’s explore what lean is and how you can harness its power to improve performance and the lives of your team members.
Through numerous conversations, it became clear that there are wide and varied interpretations of lean manufacturing and the processes it can impact. This is confounded further when we consider that many leaders accept the concept. They see some processes improve, see evidence of better organization in work areas and are happy with progress. I offer this thought: Although small incremental changes are a fundamental objective of lean manufacturing, major and transformational change opportunities are commonly unrecognized. Taking results from small gains in efficiency to literally thousands of quantifiable hours is within your grasp.
“I encourage you to challenge your paradigm and pursue transformational improvements”
One of SPL’s clients initially told me they didn’t need my lean consulting services as they already had mastered lean implementation. They had evidence of 5S (a future topic); they asked team members for ideas for improvement and often made small enhancements. They engaged SPL for coaching and developing a new sales-focused strategic plan. Due to the success, we generated with that project, the CEO shared that they had never had an outside lean process expert evaluate their lean maturity and asked me to look under the hood.
SPL was engaged to conduct an assessment to uncover potential opportunities. The process uncovered significant potential for generating capacity in an area that was significantly over capacity. This led to our first Kaizen, capturing over 5,000 hours of press capacity in a single Kaizen. Their VP of operations told me he thought he would lose his job because he should have known it was that bad. I share this because it is not uncommon for SPL to find opportunities, even in well-run companies.
This is not shared in judgment but to open minds to reflect on whether your journey yields thousands of hours, ultimately increasing profitability. If you’re not experiencing high-impact transformations, consider taking a deeper dive into the concept and process.
The concept of lean manufacturing is simply a systematic approach to improving efficiency and effectiveness by eliminating waste and enhancing value.
The primary goal of lean processes is to create more value for customers while using fewer resources. These opportunities are uncovered by identifying waste, such as unnecessary motion, waiting, transportation and overproduction. When waste is identified, various tools in the lean toolbox are used to reduce or eliminate it, improving performance, quality and profitability, allowing you to better satisfy customer expectations.
This is done most effectively through the Kaizen approach. Kaizen is commonly translated to ‘change for the good’ or ‘continuous improvement’. It is also often translated as rapid improvement. SPL prefers this definition as we operate with an extreme bias for action that I transfer to clients. Our experience is that most businesses have six to 10 opportunities for major, transformational Kaizens that typically range from 1,000 to 5,000 hours there for the taking. The true power of Kaizen is at the end of the event, not in the future; we immediately begin implementing the new standard work process capturing results.
When applied and facilitated properly, the Kaizen approach will also become one of the most impactful team-building opportunities a company can use to strengthen its teams. It consists of a cross-functional group of people working on a specific process.
Through the Kaizen, they understand what other teammates go through in their jobs. Invariably, people share comments like ‘I had no idea your job was so complicated’ or ‘I would never want to do your job; I’ll keep mine’.
One CEO shared that when SPL suggested having resources, like operators, participate in a customer service Kaizen, he thought I was crazy. After a few events, he acquiesced to my recommendation and shared: ‘We have team members still talking when they had never spoken even though they worked here for years’.
In summary, lean can be instrumental in improving performance in front-end transactional and manufacturing processes. I encourage you to challenge your paradigm and pursue transformational improvements as well. Harness the power of this process to improve the lives of your team members.
Consulting, LLC specializes in the printing industry and has expertise in strategic planning, lean enterprise implementation and talent development. CEO Brian Vande Water can be reached at brian@splconsultingllc.com
Stay up to date
Subscribe to the free Label News newsletter and receive the latest content every week. We'll never share your email address.