Mastering the pharma industry
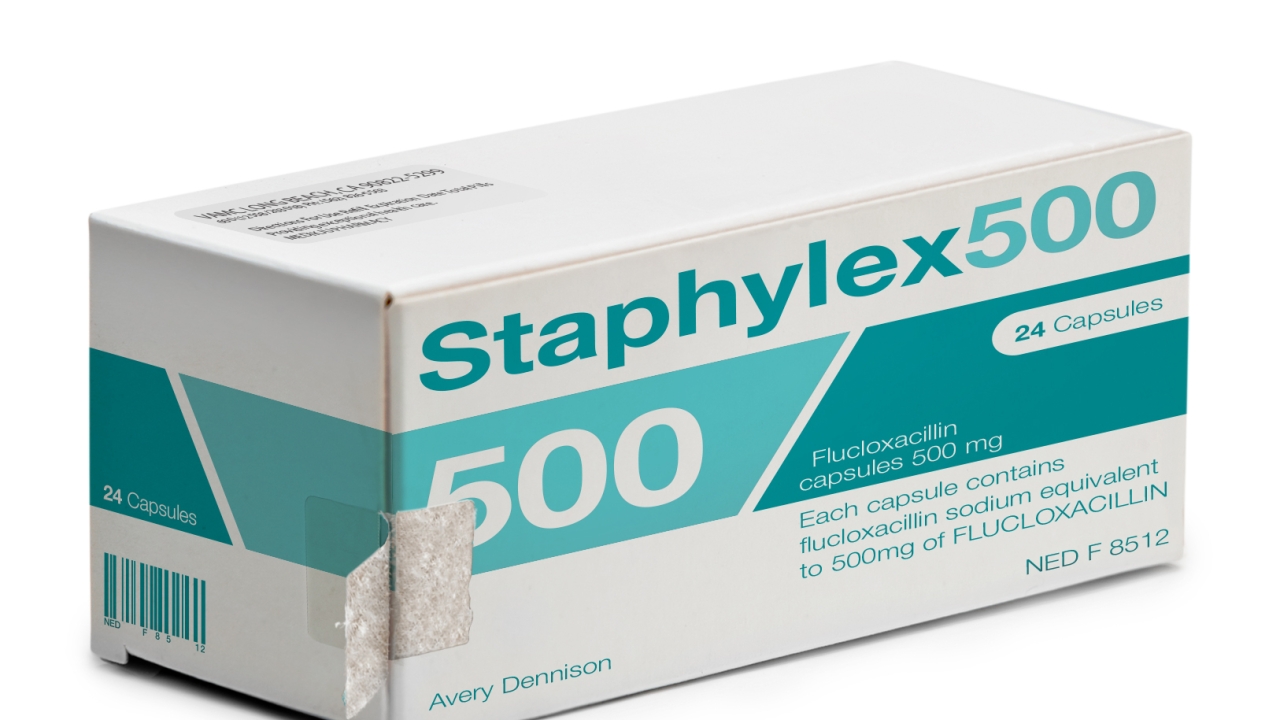
Labels and packaging are helping the pharmaceutical industry meet ever-more complex legislative and compliance requirements for serialization, as governments around the world look to safeguard the health of consumers.
They are evolving to meet new demands from consumers too, listed by Trevor Nichols, business development manager at Domino Printing Sciences as: utilizing the strengths of flexible packaging in child-resistant and barrier property applications; growth in the use of blister packaging; and rising demand for pre-filled syringes.
Product formats such as single-dose, mixed dose and daily dose continue to have an impact, while Nichols’ colleague, Craig Stobie, director, global sector management and development, Domino Printing Sciences, indicates a trend towards more bespoke products, with runs becoming shorter and more changeovers.
Chuck Pemble, vice president, business development, Americas at DataLase, reiterates this view, saying: ‘There is a move towards private label over-the-counter products. This trend will continue and see more demand to customize pharmaceutical packaging, place private label logos, and print country of origin information, codes and symbols.’
In this light, Pemble speaks of the use of DataLase’s laser reactive pigment technology to print complete back panels
or sections to meet the need for short runs of small batches, reducing the number of SKUs but increasing the variety of packaging.
Hapa proposes the use of systems capable of printing full packaging artwork and serialized data in a single pass, with UV
drop-on-demand piezo inkjet technologies able to print text, graphics and data unique to each pack. These can be integrated into existing packaging lines or new OEM lines, as well as ERP workflows, and play into the bigger trend for ensuring the authenticity and securing the supply chain of pharmaceuticals.
Combating counterfeiting
Counterfeiting is a widespread issue in the market, particularly in the geographies of Africa and Asia. Ricardo ten Velden, global segment director for pharma and healthcare at Avery Dennison Materials Group Europe, quotes figures from the World Health Organisation (WHO) to underline the depth of counterfeiting in the pharmaceutical market.
‘WHO has previously estimated that up to 10 percent of medicines across the globe are counterfeits. It no longer gives a figure, but says that counterfeiting can involve large scale manufacturing, and affects every country.’
Quality control specialist Leatus notes that traceability and supply chain transparency have been longstanding requirements in the automotive and food industries, with a dramatic global increase of counterfeits in industrial and consumer goods, and various national regulations established in order to protect the legal supply chain. Version 2.6.0 of its S-TTS software package is a tool for serialization, aggregation, and track and trace, offering enhanced capabilities to meet all requirements of international product traceability regulations, and modularity.
‘It is a problem worldwide,’ affirms Michael Urso, product manager within the Pharma Packaging Solutions division of Atlantic Zeiser. ‘There are even examples of counterfeits being counterfeited.
‘And while the rate of counterfeiting is not particularly high in Western countries, we are seeing regulations coming in to help identify, track and trace.’
UDI and FMD
The regulatory landscape is dominated by two forthcoming developments: the latest stops on the road to full implementation of the Falsified Medicines Directive (FMD) in Europe and the US FDA’s Unique Device Identification (UDI) system. Both pieces of legislation focus on serialization, now a matter of urgency for suppliers.
UDI is intended to identify medical devices through both distribution and use, improving patient safety and modernizing post-market surveillance. When fully implemented, labels will include a unique device identifier in human- and machine-readable form. Device labelers must submit certain information about each device to FDA’s Global Unique Device Identification Database (GUDID). The next major deadline for UDI is September 24, 2018.
‘There has been ongoing dialog for the last five years, and we have passed the point of delays and there is no more putting it on the back burner,’ states Pemble. ‘It is now about execution.’
In Europe, FMD means new harmonized, pan-European measures including obligatory safety features on the outer packaging of the medicines. While the European directive has applied since early 2013, the relevant ‘delegated act’ was published in its final draft earlier this year meaning the delegated regulation, and the new medicine verification system it lays down, is to apply as of February 9, 2019.
UPM Raflatac says FMD places two demands on pharmaceutical product packaging – to carry a unique serial number to identify and authenticate individual products, and to be sealed in a way that visibly enables tamper verification.
Stay up to date
Subscribe to the free Label News newsletter and receive the latest content every week. We'll never share your email address.