Minimal label waste - a new way forward
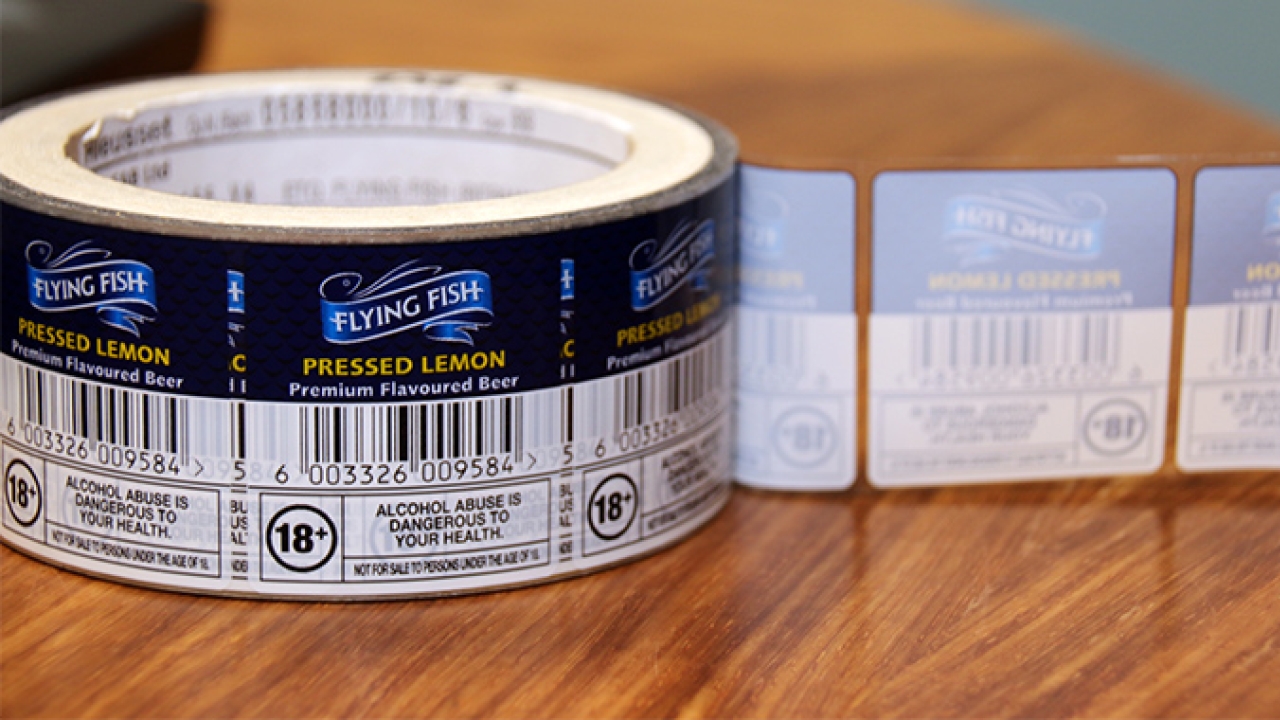
Today, some 40 plus years on, the industry is still working towards having fully viable, and global, pressure-sensitive solutions that substantially reduce or even eliminate the cost and waste generated by self-adhesive materials, whether through linerless solutions, thinner substrates, minimal matrix waste, new die-cutting technology and enhanced recycling volumes – or various combinations of some or all of these possibilities – and from which all converters can benefit.
It is not difficult to understand why the pressure-sensitive industry needs to provide a new way forward. Currently, less than five percent of the 60 billion square meters of global production of laminates with silicone liners are reused or recycled. That’s not sustainable for the future. Brands want to have 60 billion square meters of finished labels, not a waste disposal problem. Label converters will also typically waste an additional five to 10 percent of the original laminate during production and handling.
Additionally, there are all kinds of proposals by national, international, trade and other bodies to reduce overall packaging and food waste by up to 50 percent, to substantially cut plastics waste, and to recycle more. Labels are integral to all these proposals and targets, and the pressures can only intensify. It should also be noted that in some countries the silicone liner is already being taxed as packaging material and it is becoming ever more complicated and costly to dispose of it after usage.
These challenges the brand owners and label and packaging converters face are now being exacerbated by ever-more extreme climate change predictions, the ongoing war on waste, rising carbon emissions, lifecycle analysis programs, as well as the possibility of new or enhanced waste and carbon emission legislation. Retailers and brands are therefore continuously looking to be more efficient, have less downtime on labeling lines, reduce or eliminate waste to landfill, generate lower CO2 within the supply chain, and to reduce their buying costs. The label industry has to urgently find acceptable answers to all these challenges if it wants a successful long-term future.
Developments
The label industry has of course not stood still over the past 40 years since Roman’s predictions. Much has already been done in terms of linerless solutions and thinner materials over the past ten years. Leading label converters now successfully producing linerless labels include groups such as MCC, Coveris, Hub Labels, NSD Labelling, RR Donnelley and Skanem, while current developments and trials look to be close to, or ahead, of the expected challenges to come. That is, focusing on the optimum solutions for high speed labeling – no waste at the brand owner and minimal waste at the label converter.
"Currently, less than five percent of the 60 billion square meters of global production of laminates with silicone liners are reused or recycled. That's not sustainable"
To achieve these kinds of savings on a global basis means that the whole label industry supply chain needs to work together, with virtually any label converter being in a position to print, convert and substantially reduce industry waste – essentially to develop a new growth path offering a dramatic reduction in pressure-sensitive industry waste. This new growth path will be discussed later.
To better understand this evolution of linerless technology and look at the latest pressure-sensitive waste reduction developments, Labels & Labeling met with one of the industry’s leading waste reduction exponents, Mike Cooper, business development director for Catchpoint, whose long experience as a champion of both linerless technology and of pioneering developments in self-adhesive application machinery make him uniquely placed to discuss this new growth path.
However, before looking ahead with Cooper, it might be useful to have a brief look back at the history of evolving linerless technology over the past 40 years and where we stand today.
Linerless pressure-sensitive labels are, of course, not new. They first came to the fore in the early 1980s when Waddingtons in the United Kingdom developed a technology and coating system (Monoweb) to produce linerless labels which found application in label user companies such as Heinz. They were used with a specially designed applicator system that die-cut and applied the label in one pass on the production line – not the best of solutions, as Heinz did not want either the responsibility or the matrix waste.
Today, linerless labels are most commonly found in the form of pressure-sensitive labels for the blank label industry, as well as thermal labels used in print and apply weigh-price label dispensers and applicators for meat, poultry, and seafood packaging. They are also popular in several other market sectors, such as other food and logistics applications, but have generally been rather slower to make a significant impact in the wider prime label markets. These kinds of linerless labels are produced by coating the original materials with a release coating and appropriate adhesive.
"To achieve these kinds of savings on a global basis means that the whole label industry supply chain needs to work together"
The leading producer of equipment for, primarily, linerless logistics labels applications today is ETI Converting Equipment, the developer of Cohesio equipment, which has been working for some years to find solutions to the issue of release liner waste. Its Cohesio press can manufacture pressure-sensitive linerless labels with direct thermal materials right through from the raw material to the finished label product.
The technology offers converters the ability to siliconize, print, adhesive coat, print again and die-cut at speeds up to 500ft/min. A growing global base of label converters now using ETI Cohesio linerless equipment includes RR Donnelley & Sons, which installed a second ETL liner line in May 2019.
Current state of play
So where are we today with linerless decorative labels? Well, there are a number of companies that are able to offer various proprietary linerless technology and applicator systems for both primary and secondary product decoration labels. These companies include Ravenwood Packaging, Ritrama Core Linerless Solutions and Catchpoint licensees.
Ravenwood Packaging is a company that manufactures and sells coating machines to label printers, with applicators sold to retailers and packers, and particularly specializes in solutions for chilled foods. The Ravenwood technology, operating through a licensing system based on patents held by Coveris, provides the whole linerless supply chain from specialist materials to coating and application equipment for the end user using both a coater (the Comac 500) and a variety of applicators (the Nobac systems). These machines provide a completely linerless labeling workflow in which the vast majority of linerless labels produced are reportedly used in the fresh food market sector.
Today, Ravenwood has well over 1,000 linerless applicator machines installed worldwide, supplied by distributors in Europe, USA, South America and Australia, with millions of linerless labels applied annually.
Then we have Ritrama’s Core Linerless Solutions, an innovative sustainable labeling platform developed jointly with its partners Omet, Spilker and ILTI.
The first brand owner to adopt it has been South African Breweries, an ABInBev Group company, which is now successfully using the labeling platform to decorate its beer bottles. Driven by the need for a more sustainable label, the SAB project started back in 2017, went into a pilot phase in 2018, with large-scale production starting in April 2019, followed by a commercial testing and control phase on the company’s Flying Fish beer labeling line.
‘Ritrama Core Linerless Solutions has a unique conversion process that transforms a waste (PET liner) into a resource (label lamination film)’, explains Mike Cooper. ‘The 12 micron siliconized PET liner is shifted to protect the image and provide linerless label release from the web of labels in high speed applications, such as the SAB Flying Fish beer labels.
‘This Smart Multifunctional Liner format uses 30 percent less film than the current beer labels thanks to the Catchpoint micro-perforation that does not need essential label stiffness. These labels are the first concrete solution for both brand owners and converters to eliminate waste. No liner, no matrix, lower thickness and reels with much more labels bring several additional benefits like less raw material, improved logistics, and lower CO2.’
High-speed application of this new linerless solution is provided by ILTI, with support from Krones, a leader in high-speed beer labeling systems. SAB has already planned to extend the Core Linerless Solutions labeling platform to its entire product portfolio, expecting a reduction in the group’s environment impact by 57 tonnes of waste per year – in South Africa alone.
This is the first high-speed decorative PS labeling system to eliminate major waste along the labels supply chain.
LinerSave initiative
Looking at the evolution of the industry’s war on waste, the early sustainability target of seven or eight years ago was the label itself: no waste liner with new inks and eco films. Today, container recycling and re-used resin has become the target, with the industry responding with the development of wash-off adhesives. However, the industry still has a credibility issue, with a huge waste footprint and recycling logistics costs.
‘What Catchpoint is now looking to achieve,’ expands Mike Cooper, ‘is to change the pressure-sensitive industry’s logistics by producing linerless labels direct from the existing supplied laminates, using wash-off adhesives and specified facestocks – all at the label converter plant. This LinerSave initiative will totally eliminate liner waste at the brand’s labeling facility, simplify liner collection to significantly drive up recycling rates and encourage lInerless solutions to be produced to less demanding specifications.
‘Such a solution has huge potential, which could all be delivered by existing laminate capacity. It would increase recycling rates for recycled fiber in glassine, and be able to completely recycle filmic liners back into the same product. It would also provide a financial case for creating an installed base of linerless application capacity to encourage further ongoing development.
"Catchpoint now believes it has developed a successful solution for the complete elimination of the liner, which has been undergoing printed production trials at OPM Group"
‘There are obvious benefits for the brand owner from the LinerSave technology. The existing supply chain would not be disrupted, and they can be assured of long-term pressure-sensitive label supply from an industry seen to be dealing with its waste demon. Initially transitioning with back labels provides a low risk for brands. Both existing conventional PS and linerless back labels can be applied on the same adapted application control line, with Catchpoint providing the engineering to convert existing PS labeling machines for linerless application.’
But what about the label converter? ‘The Linerless LinerSave label can be produced from their same standard PS laminate,’ adds Mike Cooper, ‘while die-cutting is with the same magnetic cylinder, and many more labels are able to be delivered from the same 300mm OD reel. Liner recovered from tens, or hundreds, of label converters – rather than the brand owner – will transform PS recycling and efficiency. It also potentially halves transport logistics, with double the number of labels in a reel, or smaller lighter reels.’
The ultimate target, however, is PS labels with no liner at all, which requires a solution to two key problems: dispensing a liner-free PS web, and ensuring no blocking occurs when the adhesive comes into contact with the face material.
The laminate community has responded to these challenges with solutions for logistics applications.
Herma has introduced the InNo-Liner with an activated adhesive eliminating any silicone release coating. Herma’s integrated system with application offers clean cutting of traded unit labels. Other laminate suppliers have responded to ETI’s success with Direct Thermal Linerless in co-operation with a variety of ‘Print Apply’ machine suppliers with cutting for variable label lengths.
"The ultimate target is PS labels with no liner at all"
‘At the present time, however,’ says Mike Cooper, ‘these technologies do not provide the accuracy and speed required for decorative PS labeling, with both ILTI and Krones confirming that cutting is not yet a high-speed alternative. ETI Cohesio has disrupted traditional laminate supply chains for logistics labels, and some decorative label conversions, while Herma has pointed a pathway for laminators to meet these new perspectives through the use of activated adhesive systems.’
Catchpoint now believes it has developed a successful solution for the complete elimination of the liner, which has been undergoing printed production trials at OPM Group in the United Kingdom. This solution uses a special low-cost UV release varnish de-tack system which is deposited as a dry system in-line onto a PS adhesive web. The resulting laminate can be readily wound and rewound without blocking and this secondary layer enables the original liner and release system to be removed, rewound, and returned for recycling. OPM has demonstrated that this technology has the potential to be readily adopted by label converters. Printing and die-cutting to an anvil is the same as currently undertaken, and the labels are wound into finished reels. All the original liner waste is recovered by the printer and returned for recycling. There is no waste at the brand and reduced face and matrix waste at the converter.
"The PS label industry - after almost 40 years of linerless innovation - may now be on the cusp of significant evolution"
‘Brands can either activate in-line or be supplied with reels by the printer, with the label face decoration coated with a release varnish,’ says Mike Cooper. ‘By using a low surface energy belt to carry the labels to dispensing, or the ILTI vacuum control system, we have proved through trials that no-liner labels can be successfully dispensed. The end-user does have to invest in the linerless application equipment. However, Catchpoint’s applicator conversion kits provide a healthy return on a modest investment because they are dual function – applying both conventional and linerless labels – for investment flexibility.’
While there is still more work and trials to be undertaken, it already seems that the pressure-sensitive label industry – after almost 40 years of linerless innovation – may now be on the cusp of a significant evolution that will transform the way that labels are produced and, in turn, bring the major environmental and waste savings that the industry, and brand owners, have long been seeking.
Stay up to date
Subscribe to the free Label News newsletter and receive the latest content every week. We'll never share your email address.