DuPont focuses on converter challenges
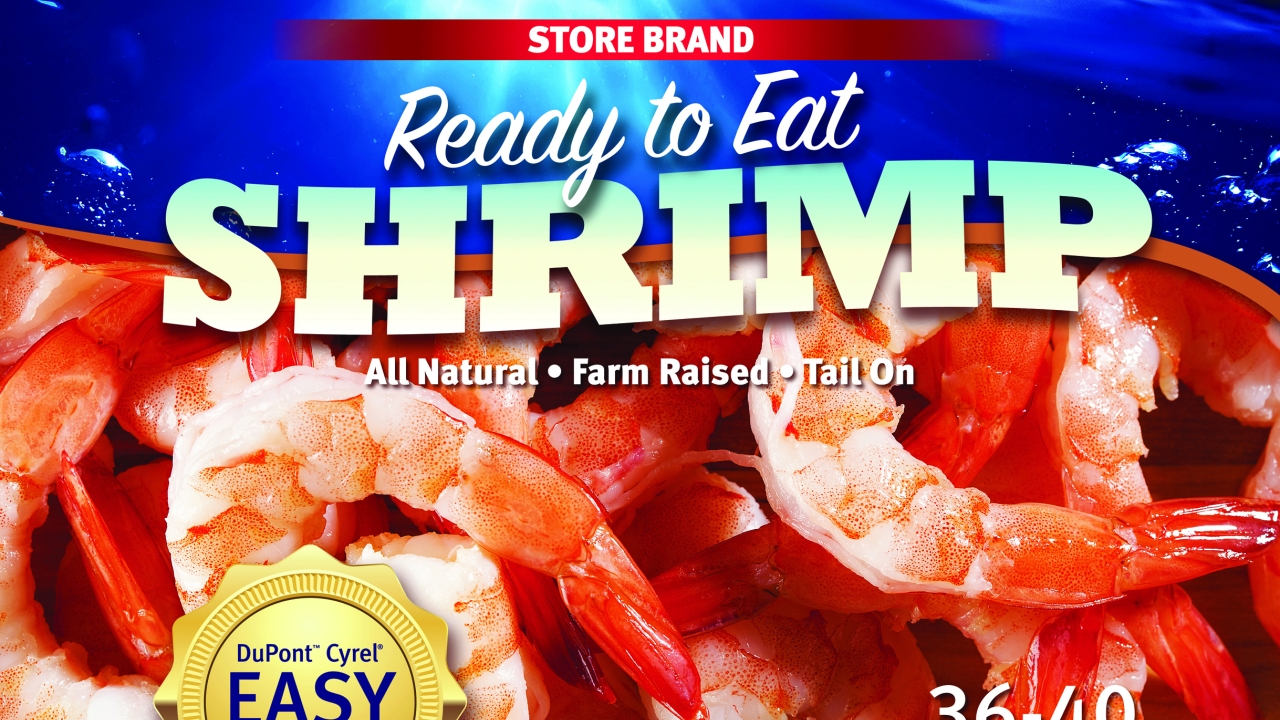
DuPont Advanced Printing has announced upgrades to its flexographic plate and plate processing technology which bring significant productivity and process control benefits to its users.
Perhaps the most important introduction is Cyrel Easy Plate technology which simplifies the process of producing flat-top dot plates by building the capability directly into the plate material. The Easy Plate portfolio is available for thermal and solvent-free processes with an engineered or smooth surface.
Up to now, producing flat-top dot Cyrel plates has required an extra processing step to inhibit oxygen on the plate surface during exposure.
Jan Scharfenberg, DuPont technical manager for EMEA, says flat-top dots have advantages under certain conditions. ‘People like the fact you can measure flat-top dots more easily – because where do you measure when you have something point shaped, effectively infinite? Another advantage is less abrasion and more stability on long run lengths.’
With Easy Plate materials the plateau can be seen at around the 8-10 micron dot size. Everything below that uses ‘digital’ dots for the highlights. ‘So with Easy Plate we combine the stability benefits of flat-top dots while retaining highlights which are almost as good as fully digital plates.’
Fast developments
On the plate processing side, DuPont has launched a new Fast thermal processor aimed at flexible packaging and label customers. The DuPont Cyrel Fast 2000 TD system has a mid-size 42in x 60in format but can handle plate sizes of 35in x 48in without any modification as well. DuPont has made several significant ‘under the hood’ enhancements to the Fast processor design which will help reduce downtime.
Firstly, the ‘sticky’ drum surface, which required frequent maintenance to keep the adhesion level correct, has been replaced by a mechanical system to hold the plate. In addition, the heated roller, which was contaminated by polymer residues over time, is now protected by a thin PET film which keeps the contact roller clean. ‘This improves processing quality and requires significantly less of a service effort,’ says Scharfenberg.
In-house platemaking
Jan Scharfenberg believes that DuPont’s latest technology developments make it easier than ever for converters to take plate manufacturing in-house. ‘Thermal processing makes more sense the closer you are to the press. If a plate breaks you can start the press again in one hour.’
Scharfenberg believes that the names invented by repro houses to brand their services confuse converters into thinking the platemaking process is more complex than it actually is. ‘Platemaking is a non-creative process – you just follow the rules. Our ideal scenario would be to have all the complex stuff at the trade house, like digital file handling, color management and retouching, and all the non-creative end at the converter – even if it’s managed by the repro house.’
Scharfenberg believes it comes down to how repro houses see their future role. ‘Is a repro house a service provider or a plate maker? If a service provider, then the future is handling digital assets and file distribution. They could say to a converter, “Put a Fast unit by your press and we will handle the files”. You can then think much broader. As DuPont we do not care who owns what. We sell plates to both trade shops and printers. But for the sake of the industry, platemaking should be closer to the press.’
Flexo vs gravure
Another issue which concerns Scharfenberg is the lack of standardization in the flexo process at a time when gravure and offset printers are looking for alternatives.
‘It is very hard to explain to a gravure guy who wants to move to flexo all the different possibilities and systems, like water-wash versus thermal, all the different ink systems, plate thicknesses and so on. So it is a dynamic market, but for a decision maker it became a bit complicated.’
DuPont believes thermal processing is the most effective alternative to solvents. ‘We do not do water-wash because we do not like the complexity and high maintenance effort in processing or the risk of water contamination,’ says Scharfenberg. ‘We are committed to thermal as can be seen by our 1,000+ Fast installations.’
Interestingly, lack of standards is a further reason for converters to take platemaking in-house, Scharfenberg believes, since standardization is easier to achieve when applied to a single operation.
‘Esko’s Equinox (extended gamut system) can be implemented best if you work with a limited number of pre-press partners. But if you work with too many, implementation might become too time consuming. If you have an in-house workflow, however, you can standardize everything and we can help you more effectively.
This has certainly been Scharfenberg’s experience as DuPont’s representative on the Bobst Revo team, which brings together a full complement of suppliers to ensure each press installation works smoothly. Revo users must commit to 7-color process printing using Esko’s Equinox software, and to qualified products including DuPont’s Cyrel Easy plates, Apex anilox and Flint UV inks. ‘Our experience is that Revo works best where you can standardize at one site,’ says Scharfenberg. ‘But even then it only works if you keep all the same components.’
Although lack of standards in flexography has major drawbacks, Scharfenberg stresses that the process as a whole has huge advantages for packaging printers: the wide range of substrates it can handle; the density of ink laydown; and an increasingly eco-friendly profile as the industry – with DuPont leading from the front – moves away from solvent processing.
Stay up to date
Subscribe to the free Label News newsletter and receive the latest content every week. We'll never share your email address.