Major investment boosts Sappi’s production of specialty papers
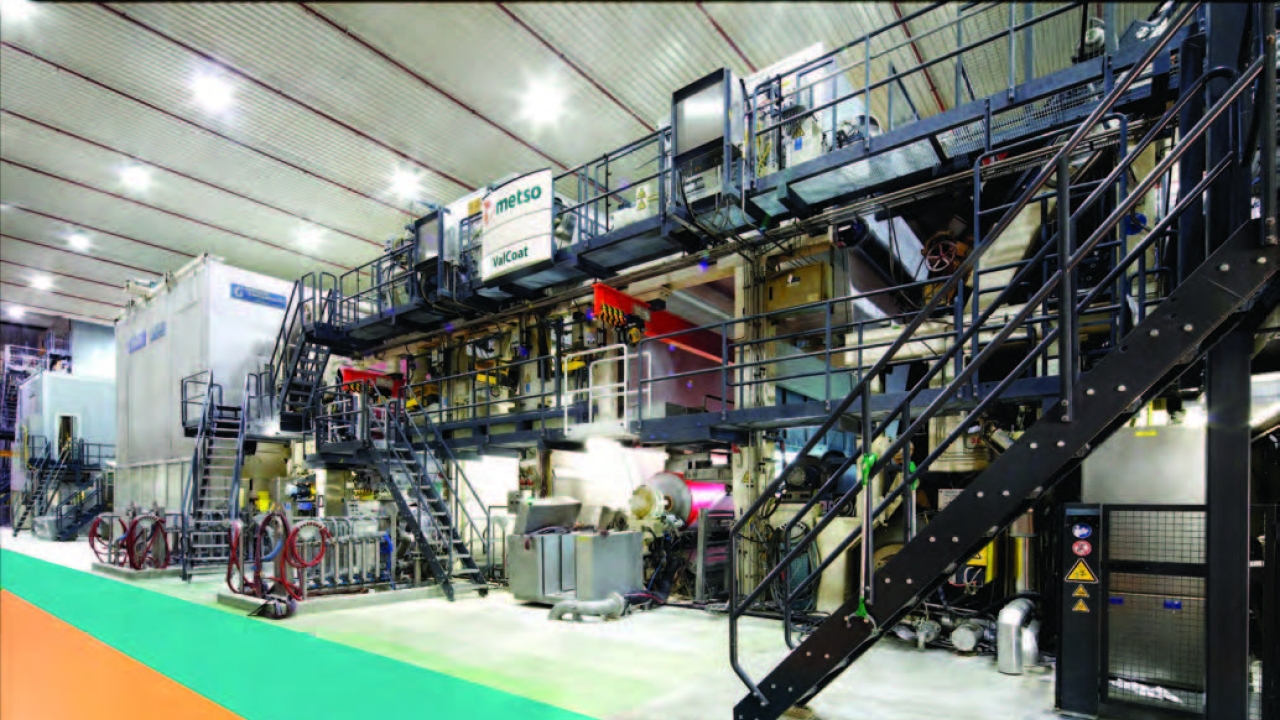
As a 300-plus-year-old business, Sappi is well placed to discuss the history of the pulp and paper industry and, more importantly, has the knowledge to make judgments on its future.
‘The paper market has changed and continues to do,’ says Gunnar Sieber, Sappi’s release liner product group manager, ‘with a lot of consolidation or companies leaving the market.
‘We were suffering in the graphic paper market due to lower demand and reached a point a few years ago where we had to make the decision of how the company should proceed.
‘This led us to make a major investment in one of our five paper machines and turn our Alfeld Mill into a 100 percent specialty products mill.’
Sappi’s specialty products include release liner, label papers, liner applications, flexible packaging, rigid packaging and technical grades, and are designed for printing with offset, flexo, gravure and digital, processing, varnishing, metallizing, lamination, siliconization, die-cutting and more. They are applicable for a broad spectrum of markets, from self-adhesive and pre-preg applications with the release liner papers to cosmetics, pharmaceuticals, food and beverage packaging.
PM 2 overhaul
Its mill in Alfeld, Germany, is a sprawling site at the heart of the town, including a log yard, raw material handling and processing, five paper machines, research and development facilities and corporate offices.
Paper machine 2 (PM 2) was the line that was chosen to receive the 61 million EUR makeover, and to help lead the site’s move to become fully dedicated to producing specialty papers. PM 2 itself was converted from the production of wood-free coated graphical papers to the production of a wide range of specialty papers and boards. The investment followed the strategy to build-up the Sappi Alfeld mill as competence center of specialty papers and boards.
The project included the installation of a 135-tonne Yankee cylinder, which owing to its size, 6.4m (21ft) in diameter, and weight necessitated the removal of the factory roof and use of one of Europe’s largest cranes to lift it into place.
‘The cylinder is quite special,’ says Sieber. ‘It’s not something you see every day in papermaking, so drew a lot of attention. It allows us to produce stable substrates in high quality with a very good surface and dimensional stability. In the production of the Algro Sol family, the smooth side of the raw coated paper, dried on one side in contact with a Yankee cylinder interface, is used as the surface for the application of the water-based coating. Unlike traditionally dried machine-finished papers, there is no significant roughening of the paper fiber surface due to the swelling of the fibers on contact with humidity. Instead, the permanent smoothness of the coated paper surface is retained.’
Rebuilding PM 2 also included the installation of a new head box and online coating system.
This has helped create better, more uniformed profiles on the substrate surface, says Peter Wenz, head of application for specialty papers at Sappi, while blade coaters are positioned directly on the machine.
Stay up to date
Subscribe to the free Label News newsletter and receive the latest content every week. We'll never share your email address.