OSP’s Labelexpo debut showcases materials expertise
At Labelexpo Americas 2024 Osaka Sealing Printing Company – a leading label converter in Japan and operating through the Primark America Group in the US - launches a range of sustainable label materials.
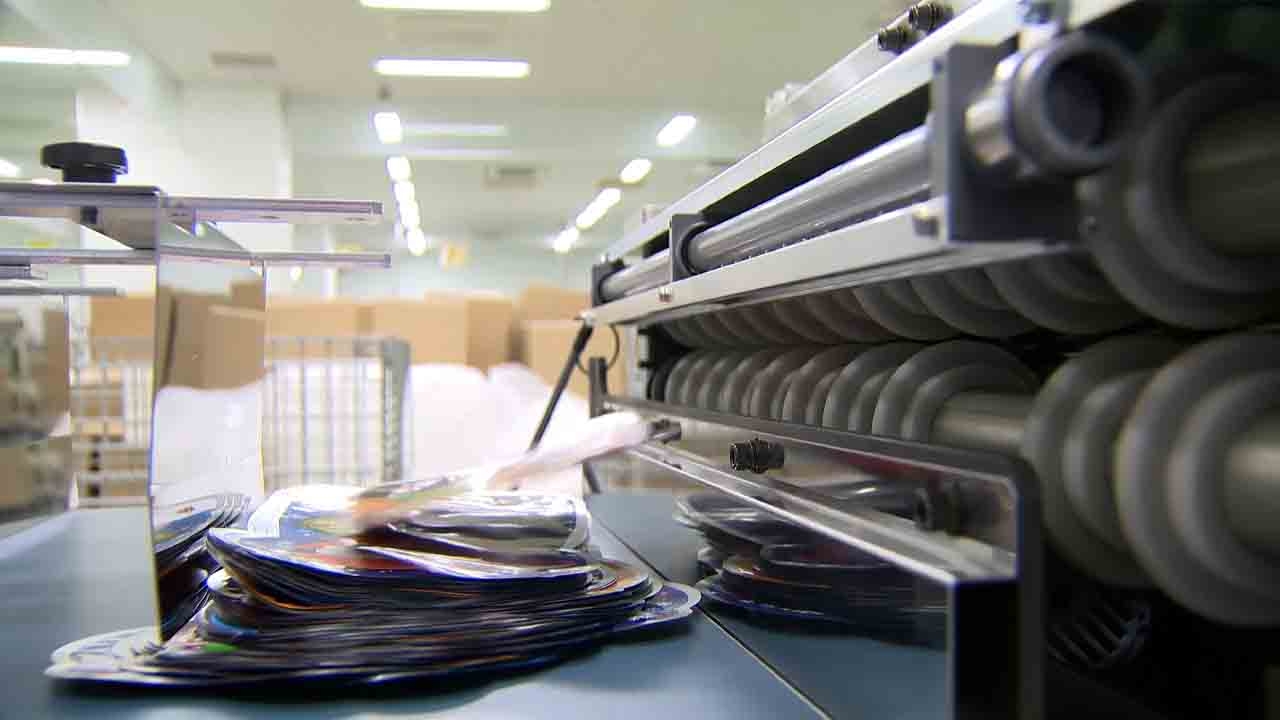
Founded almost a century ago, the Osaka Sealing Printing Company (OSP) is a leading company in Japan’s label printing landscape. The group has 14 production sites across Japan and a major global presence, including label printing operations in China and Thailand and sales offices in North America, Australia and the Philippines.
OSP was founded in 1927 when it received its first patent for a die-cutting machine. Today the group has a turnover of 105 billion Yen (USD 650m) and 4,700 employees.
The company manufactures the full range of packaging formats – labels, folding cartons, flexible packaging and POS displays – and its own specialist labelstocks, label applicators and packaging systems, printing plates and even its letterpress presses.
OSP operates as a holding company for these multiple businesses, coordinating everything from the procurement of raw materials to the implementation of efficiency programs throughout the business units.
The focus of OSP’s label and packaging printing business is food and beverage, which accounts for around 70 percent of all sales.
While most flexible packaging is printed wide-web gravure, OSP has installed digital presses for the increasing volume of short-run flexible packaging work
The company claims to produce one-third of the seals and labels for the food sector manufactured in Japan.
This year, OSP Group company Primark America will exhibit at Labelexpo Americas 2024 promoting its specialist clear thermal films and repositionable labels for logistics applications, representing a major push to become a global supplier of specialist technical materials.
Sustainability focus
OSP is actively engaged in research to create ‘non-polluting’ products. The company is FSC and Biomass Mark certified by the Japan Organic Resources Association and has obtained ISO14001 certification.
OSP recently announced the launch of a water-based emulsion adhesive that uses more than 10 percent biomass materials. Up to now, biomass has mainly been used in the development of solvent-based and hotmelt adhesives.
‘We were able to achieve adhesive properties almost equivalent to those of conventional adhesive labels that use petroleum-derived materials,’ states OSP president and CEO Matsuguchi Tadashi.
‘Our customers will be able to display the biomass mark on their labels to demonstrate the company’s commitment to addressing environmental issues.’
OSP is now researching emulsion-based adhesives with even higher biomass content.
Earlier this year, the company launched its Dottack linerless thermal tape/label using a water-based emulsion adhesive applied in dots. The base material is thermal paper, which allows the labels to be used as both tape and labels. This versatility makes them suitable for a variety of applications, such as logistics and VIP labels.
Other environmental initiatives include the Palmyashix label, a PS label paper made from palm oil production waste, and the Limex label sheet made from limestone as a base material. OSP has also commercialized a naturally translucent clear paper sticker which replaces clear fi lm.
In addition, OSP is undertaking recycling of liner and matrix waste, including waste-to-energy capacity which can be made available to local communities. OSP is a founding member of the J-ECOL association, established to promote the effective use of resources and efforts to reduce environmental impact.
OSP prints its flexible packaging mainly on solvent gravure presses but is looking to move to water-based flexo production as a more sustainable alternative.
OSP is also looking at more sustainable materials solutions for flexible packaging. One example is the paper-based Papack packaging material, specially coated to resist water and oil and with heat-sealing properties.
‘Since plastic film is not used, it has the advantages of reduced plastic usage, reduced CO2 emissions during incineration and disposal, and improved recyclability,’ says Matsuguchi Tadashi.
Digital transition
OSP is progressively moving its label printing capacity from letterpress to digital - without moving to flexo.
Annually the company prints around 1.4 million jobs, or 6,000 jobs a day, of which 70 percent are for runs of 200 meters or less. Currently, 30 percent of all jobs are printed digitally, but Matsuguchi Tadashi expects this to increase.
OSP is already a major user of Epson Surepress L-4033 water-based inkjet presses. The Epson press fleet is used for all food-related label work.
Stay up to date
Subscribe to the free Label News newsletter and receive the latest content every week. We'll never share your email address.