Grafotonic launches IQ automation
Using new smart camera technology, Grafotronic has developed a fully modular automated job set-up and monitoring system
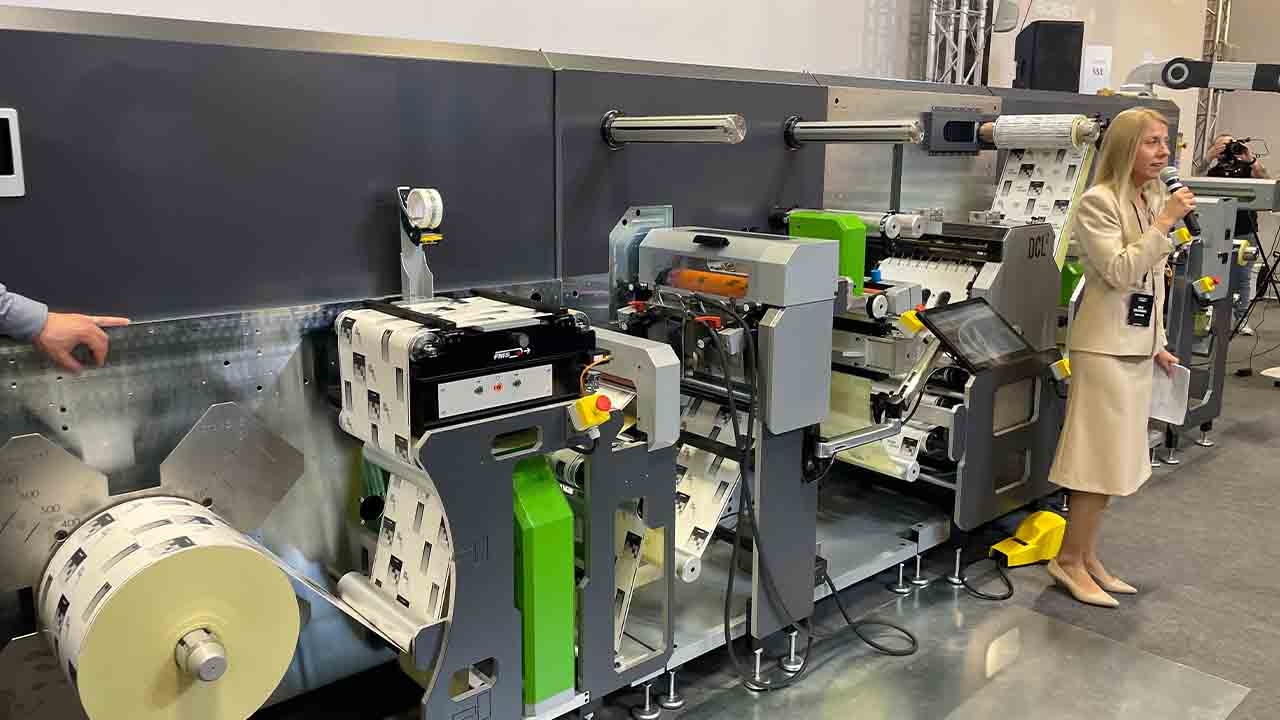
Grafotronic DCL2 with IQ automation suite
Grafotronic has demonstrated a new automated makeready and machine monitoring technology based around interlocking smart cameras at its Aspire networking event in Warsaw, Poland.
The IQ workflow automation suite will be launched at Labelexpo Europe 2023, where it will be incorporated on a Grafotronic converting line on the Automation Arena
feature.
The philosophy behind IQ is that automation should handle all routine tasks during setup, then continue to monitor each converting station during the run. This would mean that an operator could, effectively, run two machines simultaneously.
The IQ workflow automation suite is built on Grafotronic’s modular plug-and-play converting technology, with smart cameras located on each module. At the Aspire event, the IQ system was demonstrated on Grafotronic’s flagship DCL2 converting line.
The DCL2 was configured with infeed, flexo, semi-rotary die-cutting and slitting modules, each with its own smart camera. The cameras control movement of the servo motors on each module, both during job setup and while the job is running. To operate in full automation mode the IQ system only requires small cross marks printed between the label lanes and edge registration marks.
On the infeed module is a camera covering the web width. This has two functions.
Firstly, by reading the web edge registration marks, it guides the motorized registration sensors on each upstream module.
We wanted to bring to the table simple plug-and-play automation
Secondly, it provides the location of the cross marks to the camera on the slitter module, which controls the positioning of the motorized SCI-FI slitting knives. This allows slitting accuracy to be verified even after the cross marks have been removed with the matrix waste.
The camera on the flexo unit has two functions: to monitor and control registration of the flexo station print cylinder, and to identify where the die-cut should take place by reading the cross marks.
‘The flexo station camera and die-cut camera work together,’ says Marcin Wozniak, head of software development at Grafotronic. ‘The flexo camera says where
the crosses were, and the camera on the die-cut modules measures where they should have been, and checks there are gaps there.’
Each IQ-equipped module works fully independently. When the modules are connected in a simple plug-and-play
operation, they work seamlessly together as a complete system.
Standalone automation
Comments Morten Toksvaerd, business development manager at Grafotronic: ‘We wanted to bring to the table simple plug and play automation. The IQ technology means we can set the converting line up fully automatically without the need for an operator, and then we can monitor the
machine automatically during operation, just using those simple marks. We do not need a barcode or a workflow system, only those simple printed marks run the entire
automation program.’
Toksvaerd continues: ‘Grafotronic IQ is all about no more manual side adjustments, no more manual register sensor settings, and no more depending on the individual operator when it comes to set up times, waste and product quality.
Grafotronic IQ takes over all the manual adjustments, and station by station is being set up in a blink of an eye. Roll change, flexo printing, semi-rotary die-cutting and slitting, all is done and checked with a tolerance below +/- 0,1 mm.’
The IQ-equipped DCL2 machine at the Aspire event completed a fully automated job setup including varnish, die-cut and slitting with just 2-3m of waste.
The cameras control movement of the servo motors on each module, both during job setup and while the job is running. To operate in full automation mode the IQ system only requires small cross marks printed between the label
lanes and edge registration marks
‘But very important is that this automation acts stand-alone and without any IT knowledge needed by the operator,’
says Toksvaerd. ‘All the information it needs is printed on the roll-edge marks and die-cutting registration marks. Then it runs itself.’
Modularity is at the heart of Grafotronic’s converting systems. ‘We do not have a base machine – every single module is stand-alone,’ says Toksvaerd. ‘So after you buy a machine you can add modules, including IQ modules, and mix and match.
We can add a module on-site in just eight hours. Once customers realize that, it makes the initial investment decision easier.’
Young team
The IQ system’s smart camera technology was developed in-house by engineers at Grafotronic’s Warsaw research and manufacturing hub. This is a young team - indeed the average age of the workforce is just 29.5 years old, and more than one-third is female. Comments Mattias Malmqvist, partner and vice president at Grafotronic, ‘To keep the best engineers you need to always be providing them with challenges. We are facing more competition here and we are having a close cooperation with the technical universities in Warsaw
and are of course working hard to be an attractive working place for the next generation of engineers.’
Stay up to date
Subscribe to the free Label News newsletter and receive the latest content every week. We'll never share your email address.