Output – producing the components required for print
The pre-press output function is the part of the manufacturing process that converts the data from the manufacturing specification and the digital design files, to produce the components required for the manufacture of the labels and packaging, such as the printing plates and cylinders.
PRE-PRESS OUTPUT
At this stage the pre-press output procedures includes the creation of layouts, control and application of the step and repeat data, the imaging of films, the preparation and imaging of the printing plate ready for mounting into the printing press (Figure 5.1).
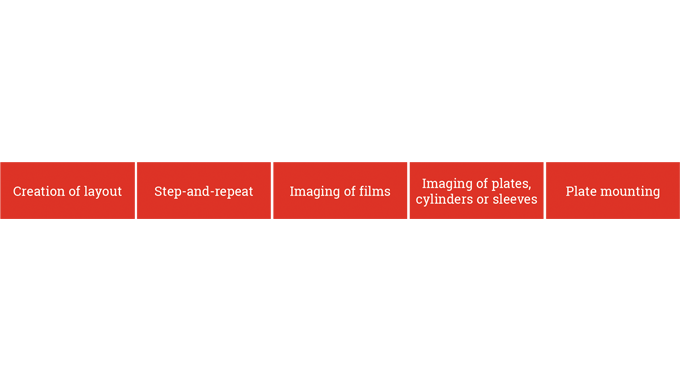
Stay up to date
Subscribe to the free Label News newsletter and receive the latest content every week. We'll never share your email address.