Advanced Labels invests in DCM technology
Durban’s Advanced Labels installed DCM’s seaming and inspection-rewinding technology to meet burgeoning demand for shrink sleeves in South Africa.
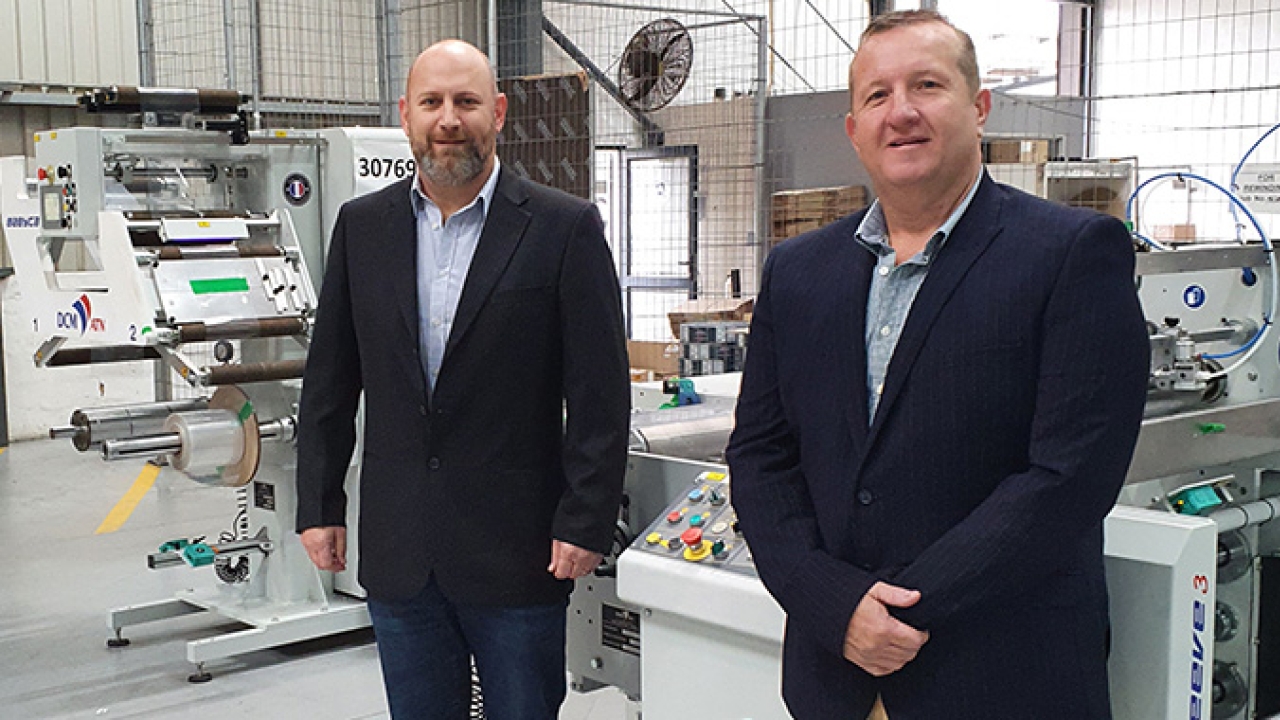
Imported from France through local representative, packwise-africa, two new machines from DCM, a Sleeve 3 Classic seamer and a Babycat 4 inspection-rewinder are enhancing production efficiency and reducing waste levels at Advanced Labels, based in Durban, KwaZulu-Nata.
From modest beginnings in 2010, Advanced Labels is firmly established as a top-class self-adhesive label converter and, increasingly, of other packaging formats, such as shrink sleeves, boasting a host of local and export customers in the consumer goods industry.
This latest investment is boosting the company's market share for shrink sleeves.
'It has significantly improved our output and reduced our waste levels,' said Richard Jones, founder and managing director of Advanced Labels. 'In turn, these waste savings are minimizing payback time on this vital investment. We were impressed by the equipment’s undoubted market success, and its competitive pricing. Our purchasing decision was further facilitated when we learnt that DCM had machines in stock, allowing us to fast track this project.
‘The seaming machine is extremely accurate and keeps wastage to an absolute minimum. It provides exceptional quality seaming and achieves the soft shoulders that are particularly necessary in the personal care market where on-shelf aesthetics are paramount. The Babycat inspection-rewinder is fast and simple to operate.’
Since day one, Jones has worked hard to build lasting business relationships based on unswerving product quality and service. These latest investments are a manifestation of this policy. And, in another significant development, has recently been joined as a business partner by Georges de Fresnes, another well-known label industry expert.
'Short lead times, consistently high-quality print and competitive prices are the cornerstones on which this business is built,' commented Georges. ‘We understand what our customers want and have implemented procedures, employed people and purchased equipment to ensure we respond to a dynamic market, meeting demand for ever-shorter lead times and faster artwork approval, quotations and deliveries. We did extensive trials and made widespread comparisons to determine which equipment would meet or exceed customers' expectations in terms of quality, efficiency and speed to market, and DCM ticked all the boxes.’
Stay up to date
Subscribe to the free Label News newsletter and receive the latest content every week. We'll never share your email address.