Eperon enjoys huge savings and faster production with AeroLED
GEW’s latest case study examines the benefits Eperon enjoy from its AeroLED retrofits.
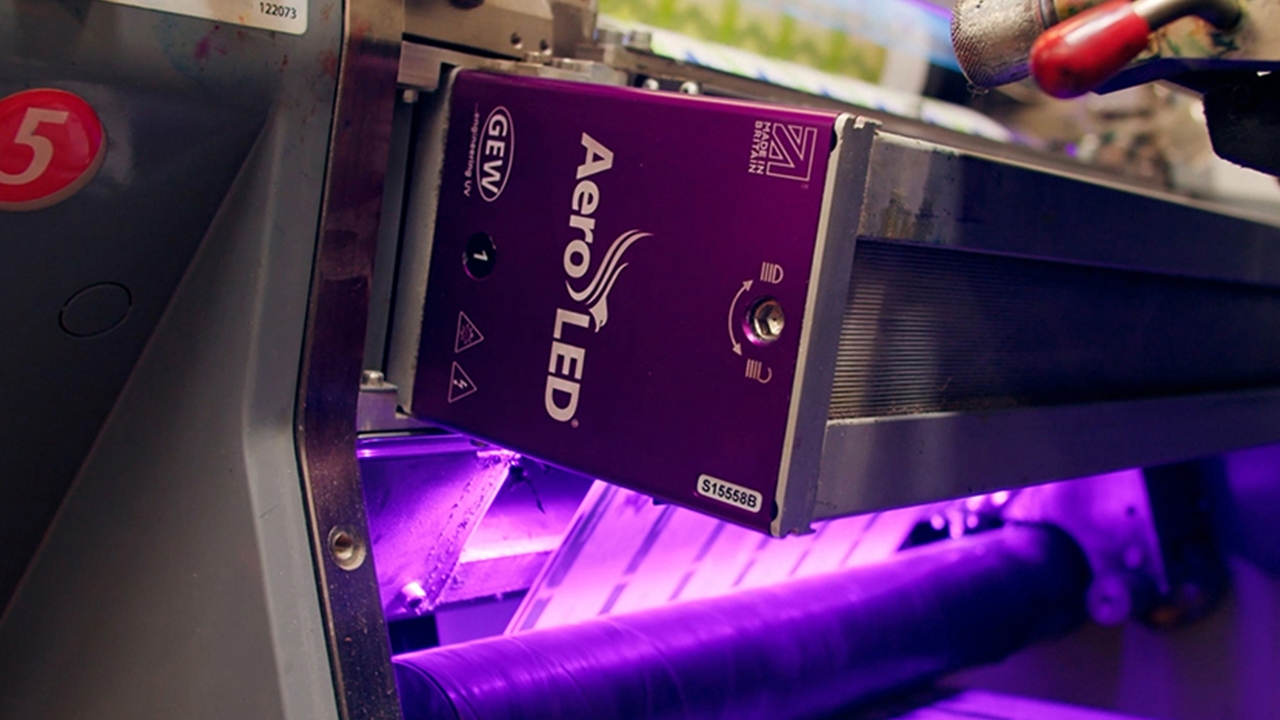
Eperon chose AeroLED for 'a gain in energy saving, productivity and certainty in terms of drying'.
Nestled in a tranquil countryside location in the Dordogne region of France, Imprimerie de L’Eperon is a hive of industry within its calm exterior. Established in 1956, the company first began supplying packaging for the dairy industry. In the 1980s, Eperon became renowned as the leading supplier of ski lift passes, covering 60 percent of the French ski resort market. The 1990s saw the company moving into flexographic printing and adhesive labeling, which has been driven by the food industry to become its core business today.
Christophe Vavassori became president of Eperon in 2015, having spent 15 years in different positions within the company. In 2021 he oversaw the installation of an 80kW photovoltaic plant at the printworks, generating up to 15 percent of its power requirements. Whilst this visionary planning has reaped rewards and enhanced Eperon’s sustainability credentials, recent and significant increases in energy costs have meant that Vavassori and his management group have had to look for further savings, which has ultimately led to their decision to upgrade their presses to use GEW’s air-cooled AeroLED UV curing systems, instead of the conventional UV arc lamps they were running.
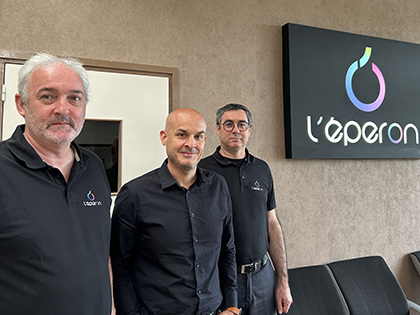
While the company wanted to reduce its energy consumption and environmental footprint, it is still necessary to continue to work with traditional mercury arc lamps on certain print stations, for varnishes and coatings that are not yet LED-compatible.
Eric Villemaine, maintenance manager at Eperon, explained: ‘In our logic it seemed obvious that to reduce our environmental impact we had to move in this direction. It was just a matter of timing for when to go ahead and do it.
‘Being able to keep mercury UV and being able to put LED if necessary was an important criterion for us because we work with varnishes, techniques that currently work under mercury and are not yet necessarily completely developed in LED.
‘This, in fact, simplifies the transition, in case of unexpected formulation changes or anything else, we can revert briefly to mercury while finding the solution. Why AeroLED? Because quite simply it consumed the least amount of energy.’
The production team now has a 47cm, 6-lamp GEW AeroLED system installed on the Omet X4 440 press, and a 45cm, 9-lamp AeroLED system on the Omet X-Flex 430. Both systems are compatible with GEW’s ‘ArcLED’ platform, meaning that UV lamp cassettes can be interchanged on each print station, to revert to running GEW’s E2C conventional mercury arc UV lampheads whenever necessary.
A further benefit of the switch to UV LED has been a significant reduction in the level of lamp maintenance necessary, and the more stable and controllable curing process that UV LED brings.
Laurent Millon, production manager at Eperon, commented: ‘We no longer have the pressure to check whether the lamps are at the end of their life or not, so it is reassuring for the operators also who can print much faster and much more easily; and a gain in quality too, of course. So, the only thing we have kept today is a mercury lamp on the last print unit.
‘Today we must remember that the varnishes are not completely ready for the change to low migration and low odor applications, but it's coming very soon in any case. Today we work for the food industry; we had to prepare our production and of course our customers to change in the very near future to this ink technology and convert the press to LED at the same time.
‘Today we use LED on all processes. We work 95 percent on adhesive labels today but even on plastic films or things like this, we are going to switch to LED for the same reasons: being much more secure in relation to drying and relation to migration.’
When considering the switch to UV LED, the Eperon team had concerns about the transition to LED inks and the potential inconsistencies this could bring.
Those issues did not arise, as Villemaine explained: ‘So, to switch from standard inks to LED inks, honestly, we hardly saw any difference. For us it was as easy as throwing a switch, on/off, exactly the same. Between LED and traditional UV inks there is indeed a small difference in colorimetry.
‘We adapted but we didn't at all need to change neither the clichés nor aniloxes. Our customers haven't seen any difference since we changed to LED in fact.’
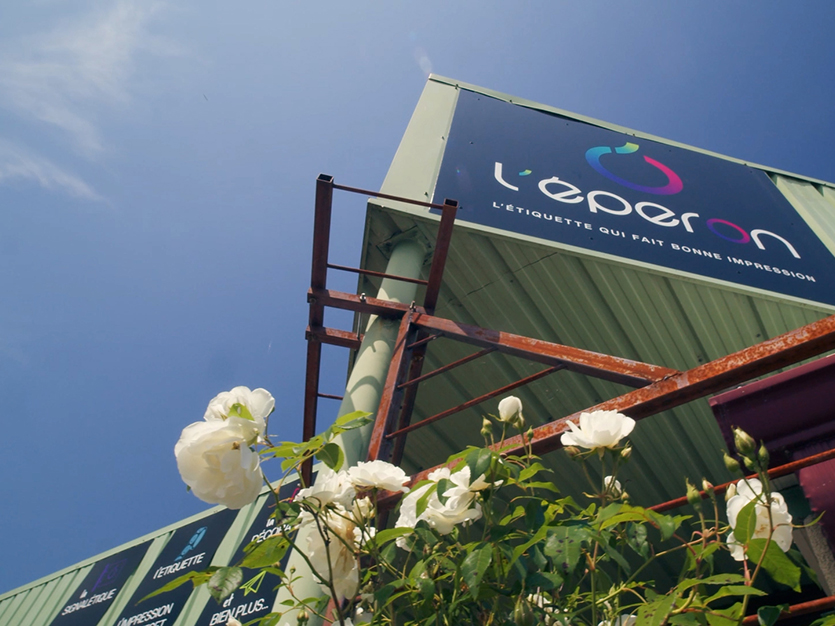
Millon added: ‘We had the Ancora range from Flint and we switched to the EkoCure range. The transition was much easier than we expected. The colorimetry was almost the same and for customers it was cost-neutral for them, everything was fine.
‘In terms of process colorimetry, apart from a very small drop in density (but nothing alarming), it was as before and in terms of Pantones we have achieved so far, despite our short experience, 80 percent of our Pantones existing in the same way as before, so this reassured us for the future, and reassured us once again of the switch to LED. We mix Pantone colors by ourselves today and we make them the same way as before and we have not changed anything at all - the transition happened very easily.’
Regarding the higher cost of UV LED inks, Villemaine offered a pragmatic perspective: ‘Indeed, LED inks are a bit more expensive, but we will recover this with the difference in performance: if you gain 10 or 15 percent in productivity, the additional cost of the ink, which also does not represent the biggest cost, the biggest burden on making a label, it's absorbable. That's it.’
Villemaine also highlighted the ease of use and stability that they have found with UV LED: ‘I think the quality of production is directly linked to the quality of drying. From the moment you dry your ink correctly, you already have better surface resistance and therefore it can avoid in all cases product quality problems for our clients. An added benefit is we no longer worry about lamp ageing or adjusting press speed. Well, we still have to do a little bit of cleaning, but in perspective this is almost nothing. It gives us much more confidence.
‘Here we found comfort above all, and press operators have regained some pleasure in working without having in their mind “I'm going to still have problems... you have to keep an eye on that”. It is much more user-friendly, that's what we found.’
Benoit Gibaud, a flexo press operator at Eperon, is similarly enthusiastic about the boost in productivity that has come with LED: ‘The big plus really is the gain in speed, drying more easily and more capably at higher speeds and also starting and stopping the lamps quickly that allows us to really win time in production today. It hasn't changed a lot for our work, we didn't really have to learn anything new in how we are working but it's really the time of drying and starting which allows you to move from one job to another more quickly and therefore produce a little faster.’
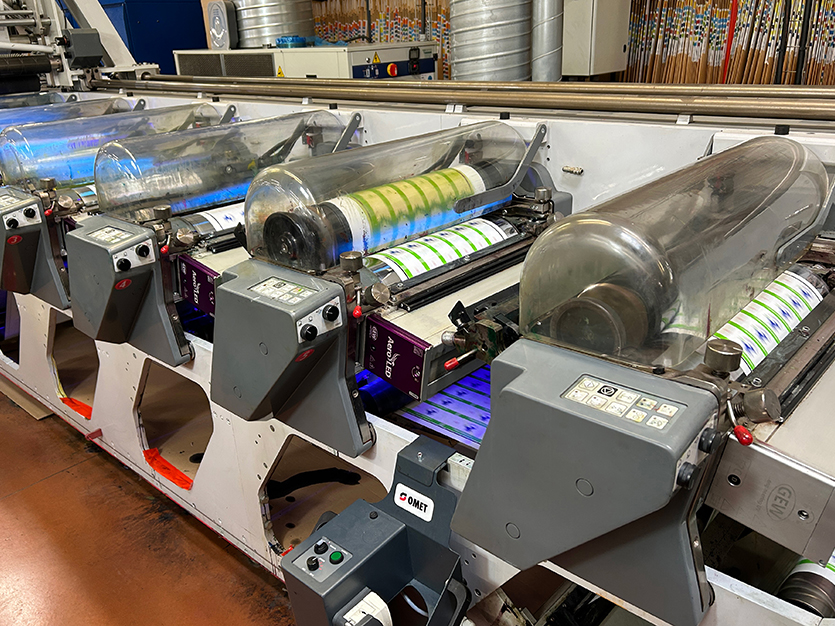
Villemaine consolidated this view and adds comment on the all-important energy savings: ‘Concerning production speeds, we estimate that we have gained around 30 percent. Roughly speaking, we estimate that from 80m/min, we increased to 110 or 120m/min. Effectively, productivity is also measured by the time that we gain during starting and stopping. And that can quickly add up to half an hour per day.
‘Energy savings. You have to recognize that when you had 160 Watts per centimeter x 15 stations and that each lamp was on; that when the machine when stopped still consumed 30 percent of its power. Yes, this makes a difference: and I think it is at least twice less energy consumption.’
On the subject of Eperon’s ROI period for the two AeroLED UV systems, Vavassori, said : ‘We hope to see the return on our investment faster than predicted. The initial analysis was of the order of two years.’
Villemaine, added: ‘I think that the return on investment will be probably much earlier. In the theoretical calculations we had not taken into consideration the dizzying energy price increases in these last months. And even though we were a little bit protected because we had contracts that still shield us a little. But in the end, we will not escape these increases anyway.’
‘My take on the LED system? Convinced. Convinced because it consumes less, because there is less maintenance, because it is reliable, because there is less heat, less waste. I haven't found any disadvantages yet,’ concluded Villemaine.
Stay up to date
Subscribe to the free Label News newsletter and receive the latest content every week. We'll never share your email address.