Gravure responds to 21st Century market pressure
What is happening in today’s market for gravure printing? Nick Coombes reports from Novara in Northern Italy, where the European Rotogravure Association (ERA) recently held its 2013 Packaging & Decorating Conference.
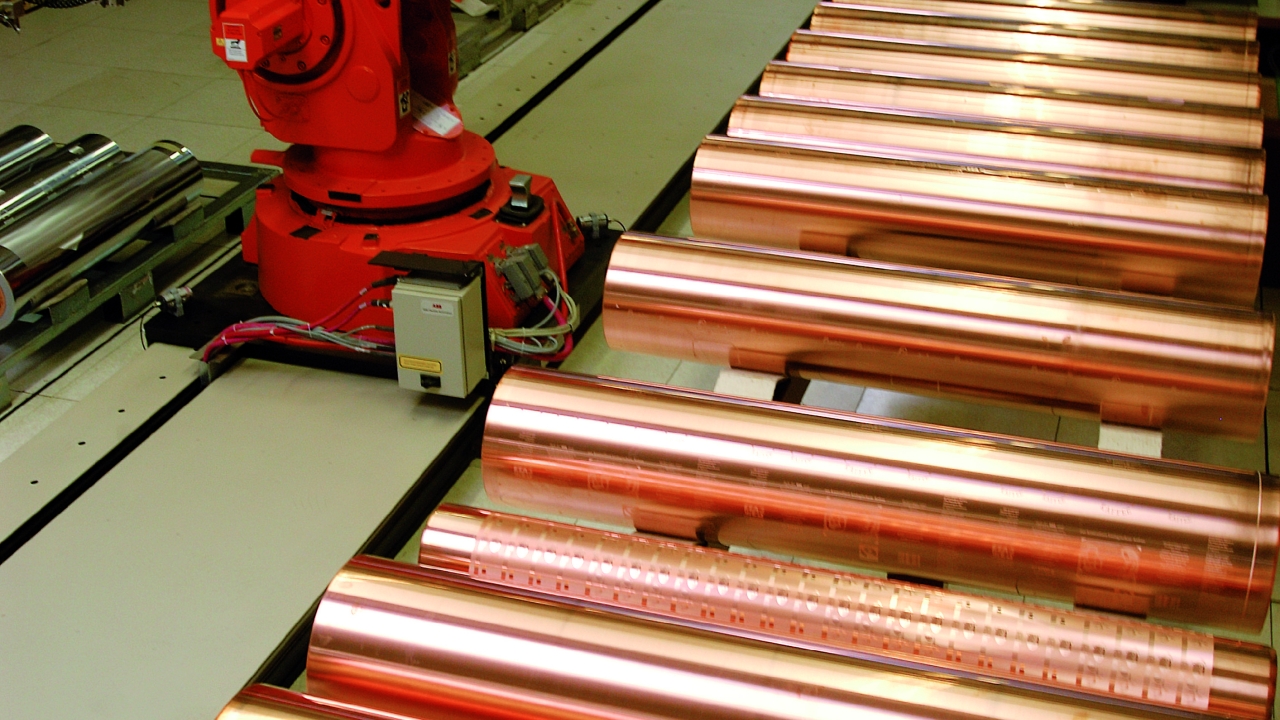
Welcoming more than 100 members and delegates to the biennial Packaging & Decorative Conference, ERA Secretary James Siever announced that the global gravure industry was actually growing, with more plants and presses in use than in 2011.
Setting the scene, he said that gravure continues to enjoy many advantages over other print techniques, namely: speed, color consistency, infinitely variable cut-off, excellent repro and half tones, and the capability of handling a wide substrate range, and with the rapid growth areas of Asia and India being major users, as well as the Middle East and South America, the future for technology manufacturers looks bright. Only in North America, often considered the heartland of flexo printing, is gravure’s market share stagnating. In Europe, where gravure and flexo hold an approximate equal market share (for flexible packaging), Germany continues to dominate, with Italy, Russia, France, Spain and the UK making up the top six, and accounting for the vast majority of plants and presses.
ERA, which is approaching its 60th birthday in 2016, was originally established as a forum for gravure printers. In 1969, it created an Associate Membership to accommodate suppliers of technology and consumables, and more recently, in 1996, it acknowledged the growing importance of packaging by creating a special category. A good cross-section of members were in attendance in Novara to hear presentations from many of the industry’s leading suppliers, all of whom spoke of their confidence in the future of gravure as it adapts to a changing marketplace.
The conference presentations began with Nikos Stamatis and Michalis Vardavoulias of ICR Ioannou. The company, which went on to win one of this year’s ERA Awards, has developed a new concept for gravure cylinders that eases logistics by using lightweight aluminium. By solving the bonding problem between copper and aluminum, ICR has produced a cylinder that is both easier to handle (typically a 1.2m cylinder weighing only 20kg), and significantly reduced the costs associated with freight shipping.
Saueressig, represented by Alwin Göring and Stefan Heßeling, also explained how their lightweight cylinder technology m-Roll, although based on steel, has achieved a substantial weight reduction by being foam filled. The lighter weight combined with smaller volume results in warehouse costs savings, while traditional copper plating and engraving techniques can still be used.
On the subject of print quality, Esko, Daetwyler SwissTec and QuadTech each explained how their technology had raised the benchmark. Giovanni Vigone from Esko Italy explained how the key values sought by brand owners are: right color, first time, every time and time-to-market savings. The latest system is ‘color by numbers’ he explained with the new spectral data creating the DNA of a color. By making use of ‘the cloud’, all parties involved have access to the approved standard that is integrated into the workflow. For converters this means faster make ready, reduced waste, and more a consistent color quality.
Kishore Sarkar, spoke of how modern doctor blade technology is responding to the rapidly changing market of FMCG, citing Amazon and the growth of mini supermarkets at petrol stations as prime examples. With retailers and brand owners needing to respond instantly to changes in demand, the need for transparency at all stages is obvious. The advent of QR coding, and other techniques that allow manufacturers to target their consumers more precisely, places greater emphasis on production techniques. In the case of doctor blades, this means the ability to cope with a new generation of inks and varnishes with their inherent chemicals, with new and often abrasive substrates, with down-gauging, new cylinder surfaces and shorter runs. It’s a high-tech world these days, he said.
Stephan Dopplehammer of QuadTech explained that 100 percent web inspection is now available and considered essential. His company’s modular system uses a 3-CCD RGB line scan camera, with proprietary LED lamps that are water-cooled. The system tolerates web wander, marks slow-growing defects, and supports all substrates. Faults detected include: splashing; streaking; missing print; mis-register; color variance; hazing; and contamination. Simple to control from a 19in touchscreen, with a five-step set-up wizard, it offers improved quality, reduced waste, increased yield and color consistency.
Moving on to the press technology, Cerutti, Bobst and Windmöller & Hölscher all spoke to the delegates about how they are responding to the changes in demand, notably for shorter run work. Arturo Bergamaschino introduced Cerutti’s two families of presses, designed with different production environments in mind. The R972 range is highly automated and aimed at countries where labor costs are high, whereas the R980, and in its latest guise the R98X, is aimed at regions where labor and associated costs are lower. Pre-setting, to reduce changeover times, is crucial, with improved drying technology that suits the shorter web path under the hood. By cutting waste, which encompasses substrate, energy, time and manpower, Cerutti claims its latest technology is a match for any flexo operation.
Bobst Bielefeld (better known as Fischer & Krecke) continued the theme with its MW range of packaging presses. According to the company’s Thomas Reckert, minimizing waste is the key to short run efficiency, and with 30 machines of this series already installed, he said runs as short as 300 metres are viable. The press, which is operated from ground level, thus obviating the need for a gallery, is therefore well suited to smaller production areas, and Bobst claims early successes highlight the trends for a press specifically focused on short run, fast changeover work.
Presenting the case for Windmöller & Hölscher, Markus Bauschulte described the company’s ‘Efficiency Accelerator’. By offering fast data input that gives higher press utilization with short set-up times, it claims that a higher degree of consistency can be obtained. The system effectively removes some of the variables created by manual inputting, and substitutes these with a series of fixed parameters that are actioned automatically, giving a more secure and reliable end result. Highlighting one aspect of how small things can make big savings, Bauschulte said the latest design washed the ink trays within the press, without using spray nozzles.
Away from technology, Bert Hoffman of the German Institute of Global and Area Studies (GIGA), gave an enlightening presentation on Brazil as an emerging market, highlighting how, with 200 million people in its middle class, the purchasing power of the country represented a major opportunity for branded goods, and therefore printed packaging. Having enjoyed stellar economic growth since the turn of the millennium, Brazil is currently seeing its economy slowing. But, with a soccer World Cup and a Summer Olympic Games due there in the near future, the World Bank is predicting continued growth for the next five-year period.
The conference concluded with two presentations on health and safety. Osvaldo Bosetti of Goglio updated the delegates on the SAFEMTECH project, which is examining the impact of adhesives on food packaging. Supported by the European Union, and carried out in cooperation of the University of Zaragoza (Spain), the research indicates that Ethyl vinyl Alcohol polymers (EvOH) can be used as an effective functional barrier against the migration of non-intentionally added substances (NIAS). An ongoing theme for the gravure industry and one of major concern is the authorization process for chromium trioxide, which is currently listed as a dangerous substance by EU REACH legislation. Without authorization, chrome plating will be banned, and ERA is working closely with the consortium to secure an acceptable outcome for the industry.
The conference also featured the biennial ERA Awards ceremony for Gravure Packaging. Winners of the best printed material were Hatzopoulos from Greece and Ukrplastic from Ukraine, while Innovation Awards went to Schepers, for its Digilas Direct 2100, and to ICR Ioannou for its lightweight aluminum cylinder technology. GMG received a commendation for its OpenColor software, and a special mention was given to Tsimis as the best entry from an ERA newcomer.
On day two, delegates were invited to visit two important gravure facilities: the production plant of cylinder engravers ICR in Origgio, and leading international gravure converters Goglio in Daverio, near Varese. ICR, which was founded in the 1970s, is a family owned and operated business, which uses the latest technology to manufacture more than 18,000 cylinders each year, mainly for flexible packaging, but also for wallpaper, gift wrap, security papers, decorative leathers and decorative laminates..
The company was keen to show off its Acigraf line, which images cylinders by electrolytic copper removal, as well as its K500 engravers, manufactured by Hell.
Moving on to Goglio, delegates were given a tour of its modern production facilities. The company began life back in 1850 in Rho (now part of Milan), and has grown to become a multi-national supplier of complete packaging systems. The Daverio plant specializes in the production of high barrier, multi layer laminates for coffee, food products, tomato and vegetable preserves for retail and catering markets, as well as for petfood, detergents, and other industrial products. It is one of ten Goglio manufacturing sites spread across Europe, America and Asia, and is a fine example of what today’s gravure converting of high quality flexible packaging is all about.
Overall, the conference mood was one of genuine optimism, with other presentations all contributing to a story that shows an industry in a state of controlled change as it responds to new market demands. There is no doubt that gravure has a future, and a bright one, but I can’t help thinking it could offer a whole lot more and extend its scope if it were to become more pro-active with its marketing, and managed to do a better job educating the package print buyers about the quality and flexibility it offers.
Stay up to date
Subscribe to the free Label News newsletter and receive the latest content every week. We'll never share your email address.