Jem Packaging halves make-ready with PressProfiler
Jem Packaging, a UK printed packaging specialist, has halved make-ready times after installing a PressProfiler server package from Prepress UK.
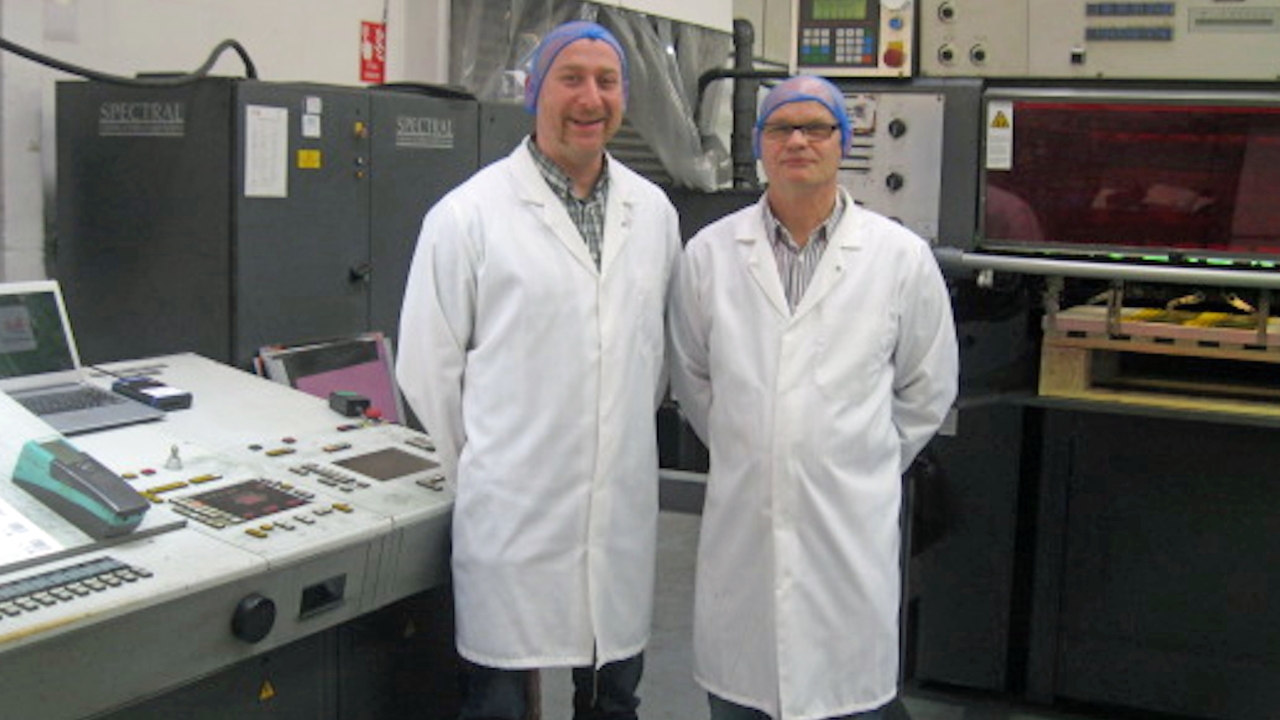
PressProfiler examines digital files received from any workflow and generates ink key pre-setting data to save set-up time. A single copy of PressProfiler can feed multiple presses.
Jem Packaging produces food packaging work for a number of high-profile food producers as well as packs for a major tool supplier. Run-lengths are typically around 2,000 to 3,000 sheets, though each sheet sees a pack repeated several times across the B2 size. Longer run work at the company could stretch to 50,000 sheets. Jem Packaging handles work from pre-press right through to a wide range of finishing operations and warehousing when required by a customer.
At Jem Packaging the profiling software works in conjunction with Prepress UK's unique CardWriter package. This allows press minders to check preview images of the job they will be running without leaving the press, before loading the pre-setting data into the printing machine.
PressProfiler is already enabling the East Anglian-based packaging provider to almost half the make-ready times on its Heidelberg Speedmaster 72 press.
Peter Horne, Jem Packaging print manager, said: ‘We had been discussing ways to help speed up our make-readies for some time, so when Prepress UK approached us with PressProfiler we were keen to hear more about what was possible.’
Bill Page, Jem Packaging director, confirmed: ‘It talked us through the theory of what was possible with PressProfiler, and whilst we were keen to see it in action, demonstrations do not always reflect reality – there is nothing like seeing it on your own press and with your own real live jobs.
‘To our surprise, the supplier agreed with this, and gave us the software and hardware needed for a 10-day trial period, so confident was it that we would see the benefits straight away,’ with Horne adding, ‘we did.’
Horne continued: ‘Dramatic savings on make-ready were accompanied by a much more straightforward approach to good color on the press. The standard ink profile that the system provides us with gives us a straightforward, known starting point.
‘Even if we do have to make adjustments for a particular job – perhaps to achieve a special corporate color – we know how to tweak things without getting too far away from the standard. We are now swiftly into good color on every job, allowing us to make savings on materials as well as time.
‘Fifty percent of time saved on make-readies is a significant amount for us – that can be equal to 20 minutes per run, and with relatively short print runs in terms of numbers of sheets, that adds up to a lot of time being clawed back during the course of a working day.’
Prepress UK sales director Nic Chapman concluded: ‘Jem Packaging is precisely the sort of business that our PressProfiler product was created for. The hardware and software combination that we offer comes at a significantly lower price than the press manufacturers own package, and the business can see a real productivity benefit from day one. We have no hesitation in placing this product into a prospects’ business on trial – when they see it working on their press, with their own work, they can see the savings straight away. You can almost see the pound signs start to spin in their eyes.’
Stay up to date
Subscribe to the free Label News newsletter and receive the latest content every week. We'll never share your email address.