Cutting die technology for ultra-thin film liners
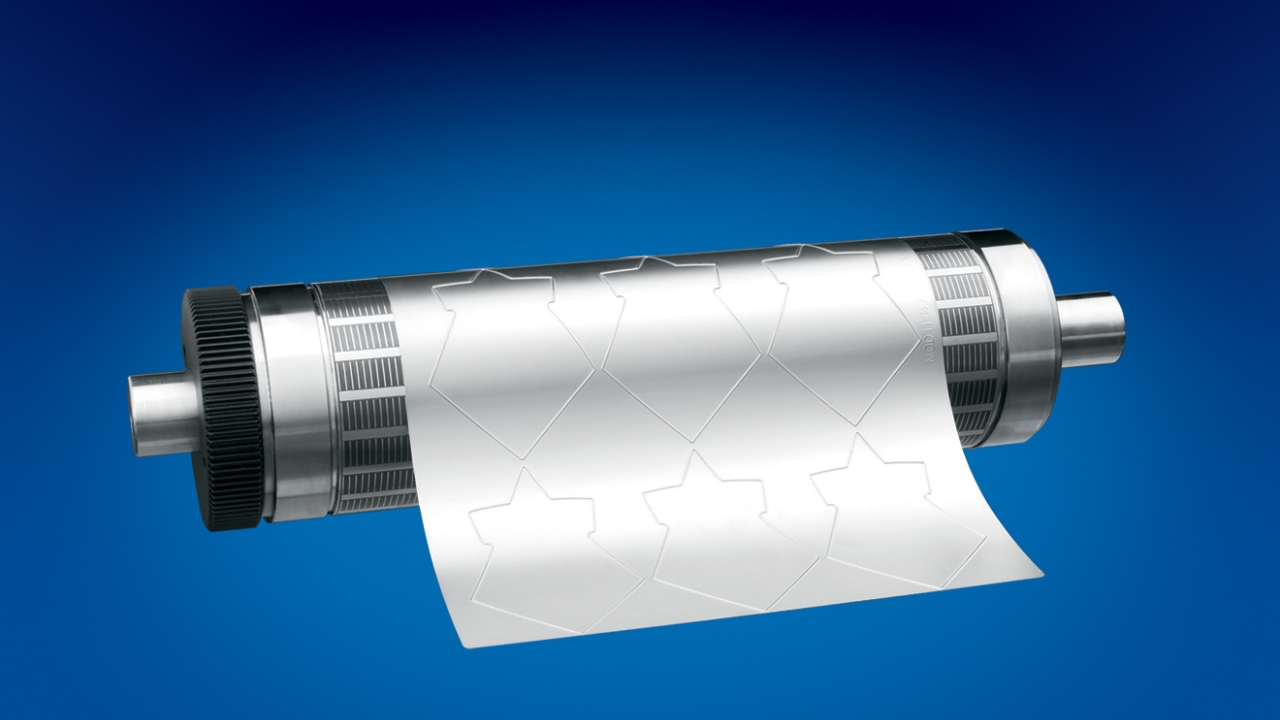
RotoMetrics’ Steve Lee, vice president of technology, and Brent Fischmann, director of marketing and corporate development, discuss requirements for die-cutting technology when dealing with ultra-thin film liners
Spurred by the potential for less waste and increased productivity, the label and packaging industry is moving to implement ultra-thin facestock and liners. Converters are pursuing the multiple promises of significant waste reduction, better resistance to moisture and humidity for food and beverage applications and material recyclability. At the same time, brand owners are looking to the combination of new 23 micron/.00092in PET liners with thinner film face materials for label application technology that enables product differentiation and an enhanced clear film, ‘no label’ or opaque conformable look for high-volume applications.
The transition to 23 micron/.00092in PET liner material – or even thinner (20 micron/.00075in) – is also posing new challenges for die-cutting. There is literally no room for error cutting to the ultra-thin PET layer. With the ultra-thin liner materials, pressure sensitive die-cutting requires separation of the facestock and adhesive while ensuring that the die does not touch the liner or cause a break during automated label dispensing. New flexible die technology has emerged in direct response to the new challenges of film substrates, with suppliers optimizing performance for 20/23/25 micron PET.
RotoMetrics has introduced the AccuStar flexible die for extensible film converting. Given the absolute premium on control of liner strike, the die is machined to a tolerance on total plate height of +/- 2.5 microns (.0001in). Advanced manufacturing technology also delivers narrower, and laser hardening achieves hardness levels of up to 68 HRC for more durable blades, providing long lasting performance in high volume applications.
Along with improved flexible die performance, the exacting requirements of new substrates require greater control of the entire die-cutting process, to include high precision, high quality magnetic cylinders and die station components. New technology cylinders are manufactured to guaranteed diameter tolerances of +0/- 2.5 microns (.0001in). Total indicator readings (TIR) are also held to this exacting level. Before converting thin film liner material, we recommend that RotoMetrics inspect the magnetic cylinder inventory to assure their overall accuracy.
Along with advanced flexible cutting die technology, machine-finished solid rotary tooling (such as RotoMetrics RD250 and MU200 series dies) remains an industry option to achieve the tight tolerances on blade edge consistency and total height required for 20/23/25 micron PET.
Beyond the cutting dies, care must be taken to maintain overall die station performance. A strong program of preventive maintenance is necessary as you address the converting challenges of thin film liners. In particular, a very smooth anvil surface must be maintained. Work with your die supplier to audit your anvil inventory. At the same time, wear in the die frame slots can mean your anvil and dies are not being held firmly, which can lead to an inconsistent die strike. Similarly, bearers on support rolls and magnetic cylinders or solid dies should be inspected for wear that could affect liner impression.
Die station component accuracy must be validated as well, given the greater requirement to manage heat build-up. When the web is hot leaving the print stations, it will bring this heat to the cutting anvil causing thermal growth. A rise in anvil temperature by as little as 20 degrees F can lead to die-cutting problems. If bearers are not in good condition and well lubricated, they too can generate excess heat and thermal expansion. Solutions for cooling the web prior to the die station are recommended.
The challenges of handling 23 micron/.00092in PET liners are leading to innovative die station solutions. New technology is being demonstrated today to avoid direct strike to the liner altogether by a process of delaminating and relaminating the substrate layers and the use of chilled dies.
Waste/matrix removal is another area of attention in converting with the ultra-thin liners. The nature of the light die strike on a thin film means there will be areas that are in tolerance but light enough that you need to help the waste removal. As with a number of challenging materials being converted today, you may have to employ the same stripping/waste removal ‘fixes’ currently used at high speeds. Testing for customers at our Converting Technology Center in Eureka, Missouri, has clearly demonstrated the need to help the stripping process as speeds increase to 1000 ft/min.
Another key process at the converter level is testing for liner strike control on press. The margin between acceptable or unacceptable die strike is 2.5 microns/.0001in out of die tolerance. High-volume, automatically applied labels require a lighter impression with no room for error. A converter should perform liner strike testing at the beginning of each run and at the end of each master roll to assure consistent quality. Some converters test every new role of material as it moves on-press. With the rapid growth of thin polyester liners, multiple new options for testing have been developed to test die strike impact for high-speed dispensing.
In many cases, and given the rapid introduction of new materials, the liner strike tests have been developed by converters themselves. Current options include stretching the material, using a ‘snap test’ or applying pressure to the die-cut areas to determine the integrity of the liner. It is critically important that the converter and the customer approve targeted liner strike prior to job launch. Visual inspection remains important, and surface inspection lights (such as LandSco) are recommended for confirming acceptable liner impression. RotoMetrics partners with converters to develop the right testing for die-cutting performance.
In conclusion, the growing acceptance of ultra-thin film liner material poses a range of challenges for converters and their partners for rotary tooling. Both solid and flexible die-cutting solutions are available today to meet the exacting demands for perfect control of liner strike. As a converter, it is more important than ever that you have partners like RotoMetrics that can help you maintain performance of your entire die-cutting system.
Pictured: RotoMetrics’ AccuStar flexible die
Click here for more stories about RotoMetrics on L&L.com.
Stay up to date
Subscribe to the free Label News newsletter and receive the latest content every week. We'll never share your email address.