BDT Media Automation, Fujifilm Dimatix and Phoseon to collaborate
BDT Media Automation, Fujifilm Dimatix and Phoseon Technology have agreed to work together to develop a complete digital printing system for packaging applications.
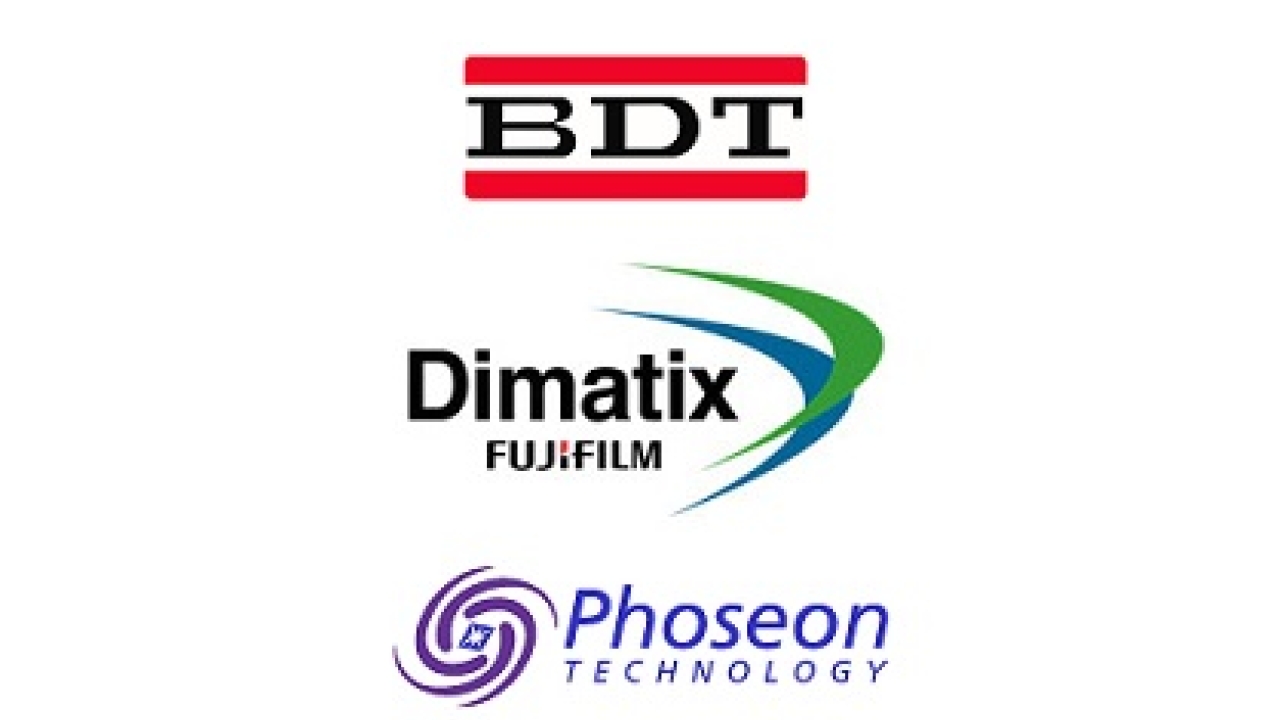
BDT Media Automation specializes in B2 format feeders in digital printing, Fujifilm Dimatix provides inkjet printheads and Phoseon Technology develops UV LED curing technology. The partners said the system will take advantage of the flexibility of the BDT Tornado media handling technology and the versatility of UV printing provided by Fujifilm Dimatix and Phoseon.
The Tornado-based product feeder (TPF) and print system will be able to perform off-line processing of standard packaging materials including coated and uncoated cardboard, corrugated board and paper stock, as well as other packing materials such as metallic foils and plastics. The system will be designed to feed, align, print, cure and stack with minimal user intervention and greatly shortened job set-up times.
The first demonstration of the system will be at Pack Expo in Chicago on November 2-5.
Howard Baldwin, vice-president of sales at Fujifilm Dimatix, said: ‘The synergy of material handling, printing and LED curing together will deliver an optimal industrial solution for both end users and OEMs.’
‘Phoseon Technology is excited to support BDT’s TPF system by providing leading-edge UV LED curing capability,’ added Chad Taggard, vice-president of marketing at Phoseon. ‘The combination with Fujifilm Dimatix and BDT showcases how industry leaders can work together to enable customers higher productivity solutions with improved quality.’
Ralf Hipp, vice-president of print media handling at BDT Media Automation, concluded: ‘We are very pleased to be cooperating with Fujifilm Dimatix and Phoseon, two market leaders in their respective fields, to bring the TPF system to market. This development will bring the best of material handling and UV digital printing to package manufacturers.
‘Our goal is to enable higher shop profitability by enabling our customers to achieve unprecedented packaging job flexibility.’
Stay up to date
Subscribe to the free Label News newsletter and receive the latest content every week. We'll never share your email address.