The evolution of anilox technology for HD printing
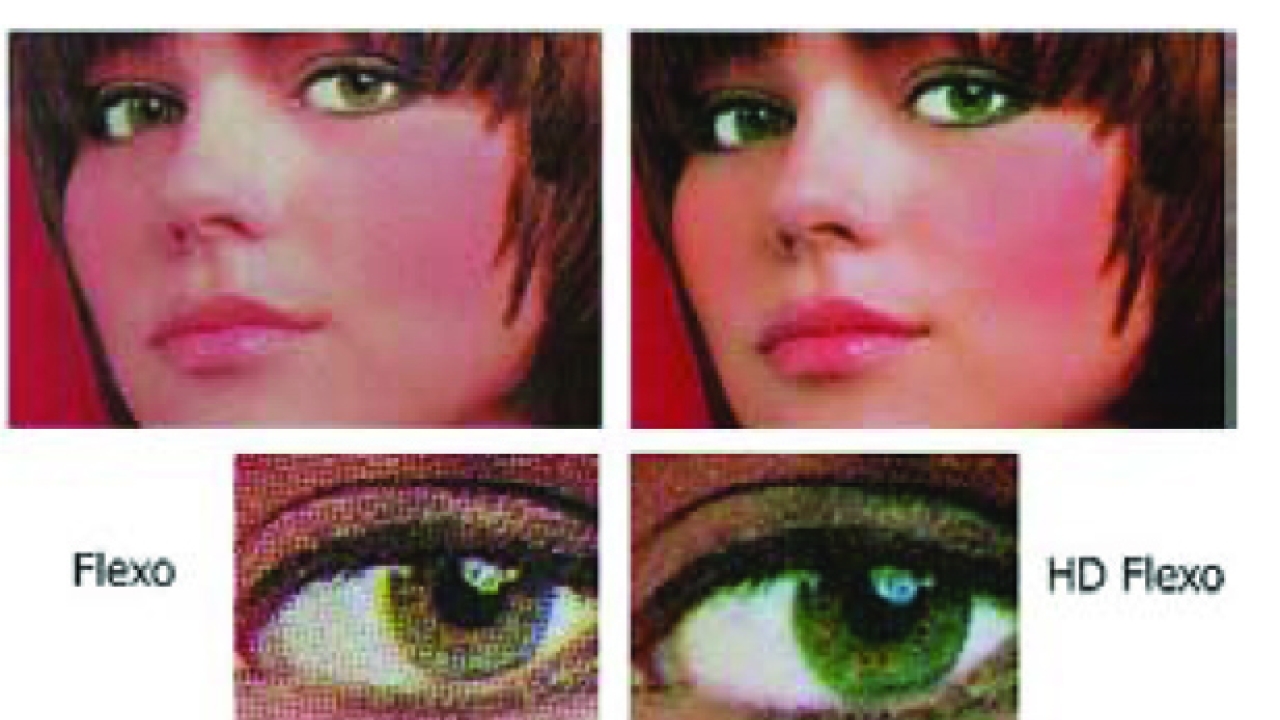
Flexographic printing has made tremendous technical advances in the last 15 years, allowing the process to grow to the point where it is now globally the most popular package printing process in many print segments. Dave MacBeth of Pamarco Global Graphics writes
High quality flexo printing is now the norm – rather than the exception – around the world. Press technology in conjunction with anilox has made this achievable, moving design away from gravure to a 10 (or more) color flexo process. New print processes and the demand for higher quality have seen HD Flexo becoming the new key driver within the flexo industry.
HD Flexo has taken problematic designs, such as flesh tones, and raised the bar in tonal reproduction using new screening techniques and finer dots on the printing plates. This has also been a challenge for anilox manufactures to be able to manufacture finer screened rolls that will work with these new technologies. Over the last 10 years offset and gravure have seen more and more printed designs moving to flexo. Designs that were once thought impossible to print flexo – and that only gravure or offset were capable of producing the fine tonal elements – have moved to high quality flexo print.
Equipment manufacturers, consumable suppliers, graphic houses and plate makers are now actively promoting HD advancements particularly within HD plate technology. While better press technology, CTP, polymers and inks have all played their part, the heart of the press remains the anilox roll, without the technical developments of this technology all the other components would not see the real benefits within the printing process.
For example, conventional and hybrid screens, and even a combination screen on the same plate; moving printers from 100lpi to 150lpi or even 200lpi, doesn’t mean the quality will be better, it could actually cause more problems. Do printers today really understand the benefits and challenges that this superior plate and higher plate screen technology give them?
Are the anilox choices they have today correct for finer highlight dots that run with solids or in fact highlight dots that are less than one percent with no support? The anilox spec always needs to be considered before moving to higher screens. There is no question that CTP technology has raised the bar in what is achievable in terms of plate technology today. However, independent market research tells us that 45 percent of the global marketplace has anilox rolls incorrectly specified for CTP plate technology of plates higher than 120lpi and incredibly, as we push harder with HD printing, 98 percent of the global market has anilox technology incorrectly specified for printing this technology of 150lpi and higher. In 2011, Pamarco linked the global investment of 500W multi-hit laser technology with new screening software. This allowed the company to improve on the already successful EFlo design, not only from a shape wall perspective cell, but more importantly change the inner dimensions of the construction of the cell.
This technology is called Bitmap Cell technology. Basically, take the shape of the cell and apply a unique bitmap file to the cell shape. This bitmap file is made up of 255 shades from white to black, in a process similar to what pre-press companies use when making their digital pre press files. Each pixel determines the laser spot size and how that laser engraves the inner profiles of the cell shape.
Pamarco’s Bitmap file has been created in conjunction with its 500W lasers along with a considerable investment in research and development evaluating the inner workings of the cell, the ink release, optimum angle and how clean the cell stays open. All of these variables are important key factors to a printer who is looking to print by numbers or in other words, the correct density number; for example 1.70 black running down the gray scale to zero producing offset and gravure quality. Each Bitmap file uses a different pixel per inch resolution for the highest quality profile and inner dynamics of the cell.
The difference is the number of pixels used to create the file, making a HD roll much sharper and allowing it to lay down a consistent thin layer of ink on the dot surface, something that is key when applying ink onto flat top dot technology or a combination of different FM and AM dot sizes. The makeup of a HD plate is very different than that of a conventional CTP plate. It’s made up by a number of variable dot sizes and support dots on the plate.
The variable dots give a much better lay down of ink but the anilox roll selection and type of engraving is critical to get the best printed result. Otherwise printers are just wasting money on higher priced plates with no real value. The benefits are clear when you run all the elements in a CTP and HD environment. Using an EFlo-HD anilox at a lower BCM volume and higher line screen allows the ink to transfer at a much better rate to the plate allowing for a sharper and cleaner dot, with a higher contrast of color.
Pamarco is the only anilox roll manufacturer that is staying up to date with the new HD technology. EFlo-HD branded PHD engravings are the result of Pamarco’s investment into the latest thermal YAG laser technology applying custom software, laser optics and custom parameters that, when combined, provide the ability to manipulate and control laser engravings to unprecedented levels.
The technology provides the ability to produce custom cells by employing a variety of software applications and optical paths that produce a large selection of laser engraving manipulation tools. The PHD cell itself evolved from Pamarco’s EFlo product line. After studying the EFlo and its transfer characteristics we felt it would be perfect as a foundation for the formation of the PHD engraving.
The standard EFlo product is produced by the use of either 'multi-beam' or 'multi-hit' laser manipulation depending on the screen count and volume. This cell has found a home in many applications where low dot gain, increased ink transfer, improved solid ink coverage and cleaner highlights have been realized. With the PHD product we have enhanced the cell structure to work with HD Digital Plate Technology to produce superior densities and contrasts at higher line screens along with all the other features of the EFlo product.
Pictured: Demonstrating the difference in flexo and HD flexo
Click here for more stories about Pamarco on L&L.com.
Stay up to date
Subscribe to the free Label News newsletter and receive the latest content every week. We'll never share your email address.