Hybrid solution
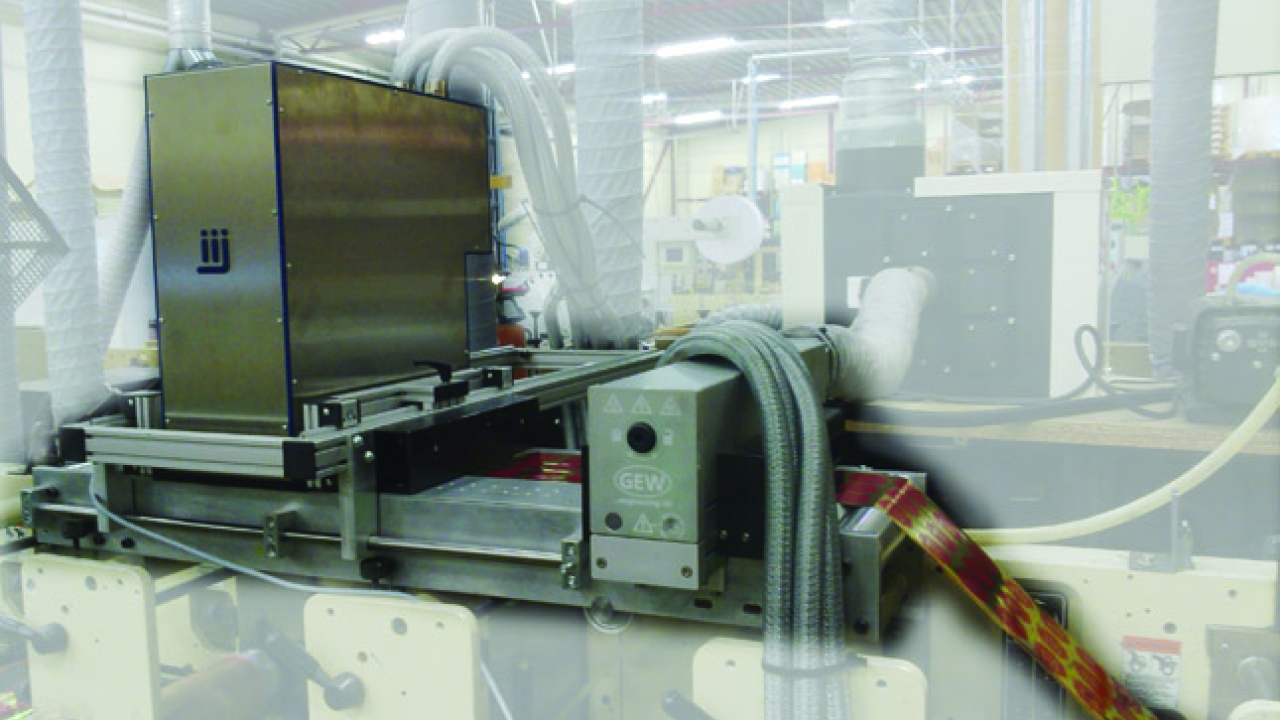
Faced with demands for shorter runs, Lundens Tryckeri in Gothenburg, Sweden opted for a hybrid flexo/inkjet solution. Andy Thomas reports
Like many label-printing companies world-wide, Lundens Tryckeri was suffering due to customer demand for smaller order-quantities, with more variation, and so ever shorter run lengths. Setup time on the company’s flexo presses dominated job costs and the trend was very clear to Bosse Andersson at Lundens : ‘To meet customers’ demand we need to produce labels in greater variety, faster and cheaper’. Bosse was sure that Lundens needed to upgrade digital printing, but having studied the systems available he was also sure that a stand-alone digital system was going to require a very large up-front investment, and the kind of cost-per-print figures he was being quoted would make such a system viable only on very short runs of high-value labels. In short, the return on investment would be long at best.
Bosse’s dream was of something different. He understood perfectly that his current flexo units deliver the low cost and high-quality that his customers demand, but only when the print run is long enough that the setup costs become affordable. His idea was that what he really needed was a hybrid system, which fused digital and flexo. Basically a system that on long runs operates as a flexo label press, on short runs becomes a pure digital system with zero setup time. In the middle somewhere it could run as a mix of flexo on some colors and digital on the rest. The decision on any particular job should become purely economic – what is the lowest cost way to produce the job. In summary, what he wanted was to add a full-color digital module to an existing flexo press.
Benefits
By utilizing an existing press as a 'base' unit Bosse foresaw he should be able to achieve good savings in the system cost. He would not need to pay for the unwind-rewind system that is usually part of a digital printer, and in addition he could use the existing pre-treatment and finishing capabilities of one of his existing presses.
In summary the expected benefits would be:-
• Low investment cost
• Hybrid system allows optimum mix of flexo and digital for lowest cost-per-print
• Little or no increase in space requirements
• Minimal retraining of staff
The next question for Bosse was simple? Could he find such a digital module and could it be adapted to one of his existing presses.
Investigation
For help in finding such a digital system, Bosse turned to Print and Cut Ltd, also in Gothenburg. Print and Cut provide maintenance and upgrade services to printing companies in Scandinavia. It has a long track record of successfully customizing or modifying presses to suit customers’ requirements. Although up to that point Print and Cut had little experience with digital printing, they were not afraid to look into it and had been looking for a suitable project on which to build digital experience. Birger Lolk, CEO of Print and Cut, began by investigating digital systems on the market.
Print and Cut suggested a visit to Industrial Inkjet Ltd in UK to look at its ‘ColourPrint’ inkjet modules. Two visits followed, with print trials on IIJ’s demo systems, before Lundens and Print and Cut decided that the IIJ system seemed to be the way forward.
Adaption Issues
During discussions with IIJ, Print and Cut had determined that a key issue in achieving a successful integration of the IIJ unit would be the accuracy of the media movement under the ColourPrint module. IIJ had explained that its module is built up from a number of smaller inkjet printheads, all contained in a single printhead unit. The individual printheads do not join end to end but are arranged in two rows (per color) and placed so that the print from one head merges seamlessly with that of its neighbour in the next row. The printheads used by IIJ - from Konica Minolta in Japan - are very slim, but the two rows are still on a 20mm pitch. Roughly speaking this means that if the label stock moves under the inkjet unit at an angle then the print from adjacent heads will either not join together (leaving a white line) or will double-up on the material (creating a dark line). The first challenge for Print and Cut was to ensure that the sideways movement of the label stock was controlled well enough that this would not be an issue. Note that total sideways movement of the label stock is not what is important. It is the angle of movement under the printheads that causes the 'stitch' to become visible.
A second issue was the cure-delay of the inkjet ink on the media. IIJ had explained to Print and Cut that on different label media the inkjet ink would wet out at different speeds. This means that the distance between the inkjet module and the UV lamp will need to be adjustable to achieve the best print quality on any different media. IIJ suggested a maximum gap between the inkjet module and the UV lamp of close to 1 meter would be required.
Following the discussions with IIJ, Print and Cut designed and built an ‘adaptor’ to go onto the Mark Andy press selected by Lundens for modification. This adaptor would hold the IIJ ColourPrint unit and the UV lamp, supplied by GEW. As well as ensuring plenty of adjustment between the UV lamp and the inkjet module, the adaptor was required not to reduce in any way the flexo capabilities of the press and must not cause any ‘wander’ of the label media under the inkjet module.
A visit to Lundens by IIJ staff showed that the label stock was tracking accurately over the new adaptor, so Lundens were able to order the IIJ system and the UV lamp.
The next issue to be solved was to ensure that the print from the IIJ unit would register accurately to the die-cut labels. The solution that Print and Cut came up with was very simple. A photo-sensor was mounted after both the in-line die cut and unit stripping of the waste material. The chosen sensor had no difficulties in detecting labels - even fully printed labels - against the background liner material. The result was a 100 percent register between die and print.
The system was finally installed in April 2011.
Media Issues
During trials of different label stocks, Lundens realized that , despite the print tests of different materials made earlier at IIJ, there were a lot of standard paper flexo label stocks on which the inkjet print just did not work. Basically the inkjet ink tended to ‘reticulate’ or ‘bead’ on the gloss label surface. Plastic films generally worked well, but many, perhaps most, paper label stocks did not work. The Mark Andy press was already fitted with a corona-treatment unit but this was found to have little effect. Finally, investigation by both Lundens and Print and Cut found a pre-treatment coating that can be applied inline by one of the existing flexo units in the press. This pre-treatment allows the inkjet to print onto almost any stock with excellent definition and ‘smoothness’. At the same time the cost of the pre-treatment is sufficiently low that it doesn’t significantly add to the overall cost per print of the digital system.
The Result
The system has now been in use for around three months. ‘It is used every day and has proven to be very reliable, easy to use and with an absolute minimum of maintenance,’ commented Bosse Andersson. ‘The system does the job brilliant! We are really pleased with it’ .
Print and Cut’s Birger Lolk believes that there is a real need for such hybrid systems in the Scandinavian label market, and he envisages fitting many more of these units to existing Gallus and Mark Andy units.
Pictured: Industrial Inkjet Colourprint inkjet module
This article was published in L&L issue 5, 2011
Stay up to date
Subscribe to the free Label News newsletter and receive the latest content every week. We'll never share your email address.