Lorge Imprimeur installs BST TubeScan system
French converter uses BST TubeScan digital strobe 430 on a converting machine to verify labels with variable barcodes produced in digital printing
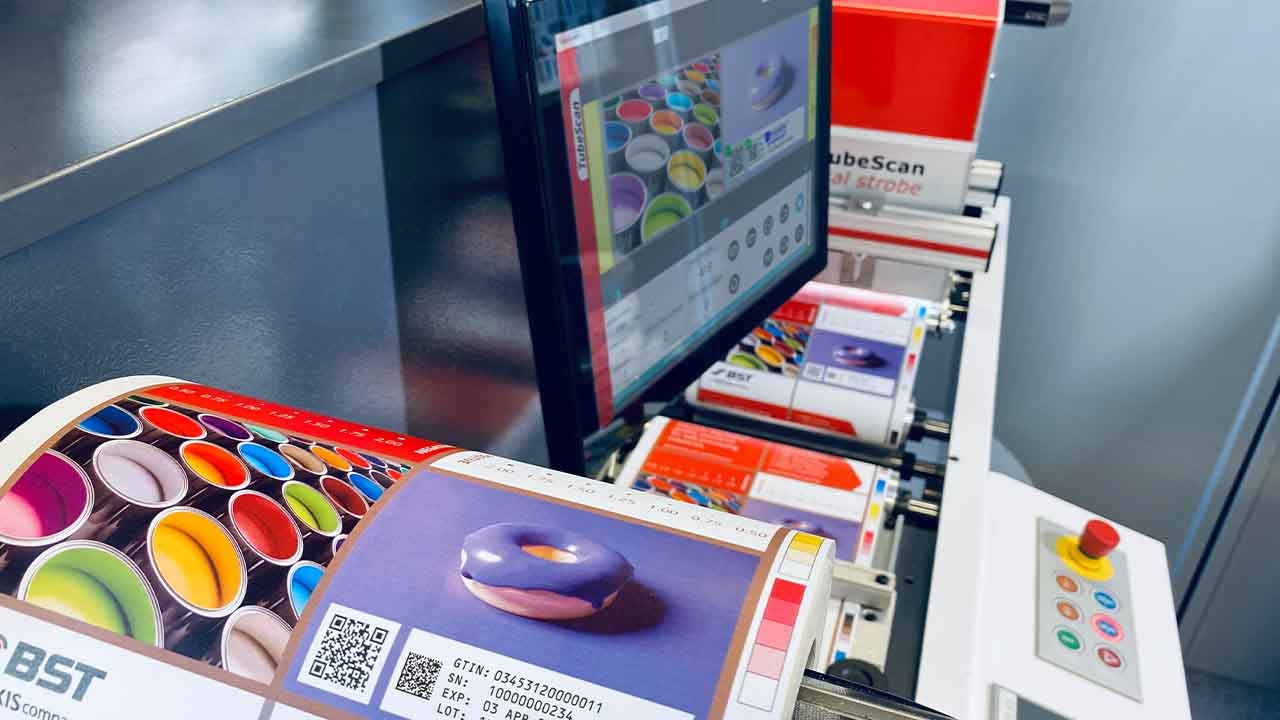
French label printing specialist, Lorge Imprimeur from Vénissieux, has installed BST TubeScan digital strobe 430 with a high-resolution 4K camera on a converting machine to verify labels with variable barcodes produced in digital printing and compare its content with a database provided.
The system uses smart BST image processing in combination with high-resolution matrix cameras to check the correctness and functionality of the printed products.
Lorge produces small and large batches of self-adhesive labels on rolls using digital and flexographic printing. The manufacturer required a system that would simultaneously check the printed image of the labels and validate the variable data printed on them. The company installed a BST TubeScan digital strobe 430 with a high-resolution 4K camera on a converting machine. In the event of both print errors and code data errors, the machine automatically stops to take appropriate corrective action. The read codes with inspection results are stored in a results database on an order-by-order basis.
BST TubeScan reads the content of the codes, verifies the decoded information for continuous sequence, unintentional repetition or against an input database, and optionally checks the print quality inline according to ANSI/ISO classification. Brand owners often require their products to meet the minimum quality of C on the ANSI scale from A to F. The system is also able to check the print quality inline.
The barcode module of BST TubeScan is based on the ISO/IEC 15426-1 and ISO/IEC 15426-2 standards for barcode inspection devices, which examine quality criteria such as symbol contrast, bar width variation, or raster non-uniformity and, when combined with offline verification, provide 100 percent inline quality control. The minimum resolvable module size, that is the smallest element of a code, depends on the resolution of the selected camera configuration. A matrix code's element must be at least three pixels wide, while a barcode's smallest bar width must be at least two pixels wide.
Parallel to the inspection of the printed image, TubeScan performs an inline and real-time comparison of the inspected code with the input database. TubeScan saves the comparison results with other inspection results into a CSV file. This is also true at Lorge in France, where TubeScan has been integrated into the company's network. The system reads the CSV file assigned to the job from the server at the beginning of the roll processing and stores the result file in a new folder there after the inspection is complete.
The implementation of the BST system at Lorge has allowed it to concurrently inspect and validate variable data, such as matrix codes or serial numbers inline.
Stay up to date
Subscribe to the free Label News newsletter and receive the latest content every week. We'll never share your email address.