The JDF connection
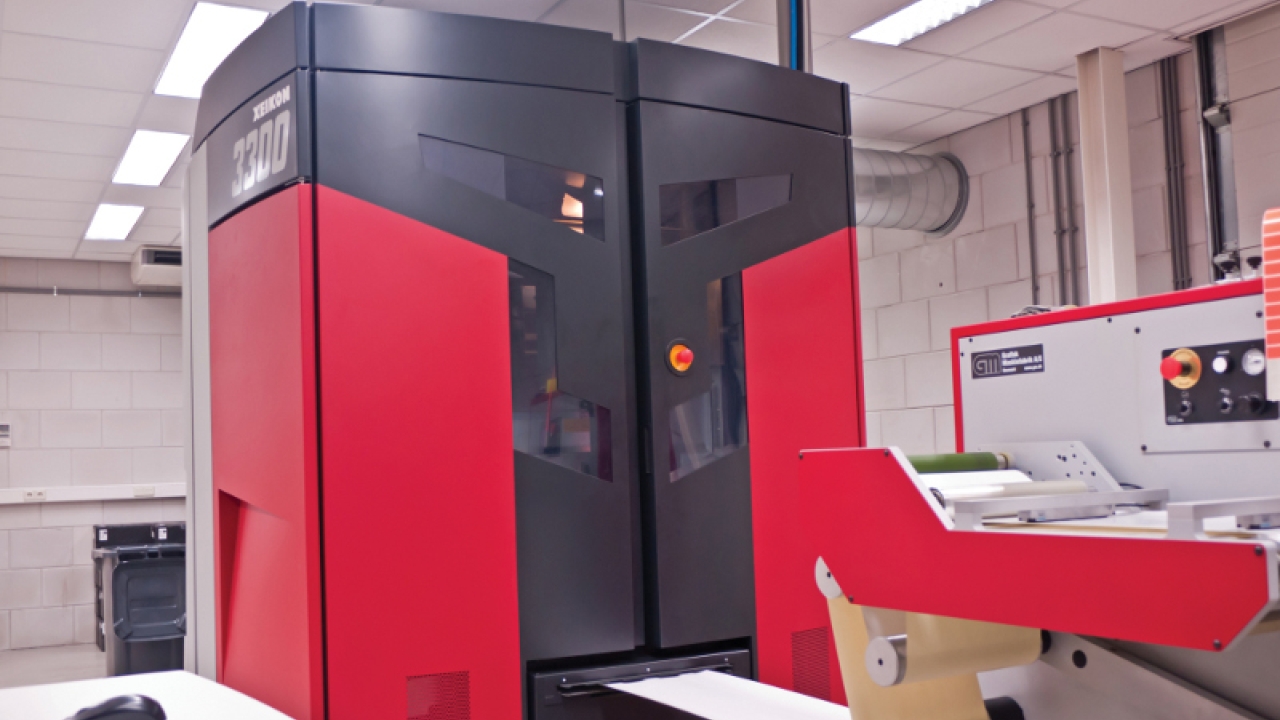
Barry Hunt reports on a Dutch printer's experience with a JDF workflow linking MIS and pre-press systems
It is generally accepted that digital printing works best within a dedicated workflow. Today, that means not just an automated pre-press system to optimize the studio workflow, but also using a customized management information system to handle the many administration and production tasks. Best of all is to integrate these disparate functions within a JDF-enabled (Job Definition Format) digital workflow. This method of increasing productivity is a more recent development. In fact W&R Etiketten of Tilburg in the Netherlands is one of the first label converters to adopt this end-to-end approach.
The company was formed in 1992 by Jack Willemsz and his business partner Leo van Rooy. It has 40 employees and occupies a plant with 4,500 sqm of floor space. It uses the recently-introduced Xeikon 3300 label press (330mm maximum web width), printing with the latest QA-I dry toner system. It runs with a rewinder from Grafisk Maskinfabrik.
Digital printing is just one process in a production set-up that includes four MPS EP-Series UV flexo presses (a seven-color, three-color, five-color and a six-color). They are supported by a new Matho matrix waste removal system, while Athena, a local trade house supplies digitally-made flexo plates. The company also produces large volumes of blank stock-size self-adhesive labels using six LeoMat slitter/rewinders with die cutters.
Most of the firm's thousand or so clients are from Holland. They vary greatly in size, operating mainly in the transport, logistics, food and retail sectors. No more than 25 of the larger customers account for roughly 50 percent of turnover, which last year was 6.4 million euros ($US9.36 million).
From the outset, continual investment and development has shaped the company's growth. Following industry trends, the demand for short-run jobs has increased, but with fewer labels per job and shorter lead times. The firm also experienced increased pressure at the high end of the market, compounded with an economic downturn and decreasing prices. Faced with this negative spiral, the company recognized that it had to face the challenge of adapting and developing the business to ensure its future, which implied differentiating itself from competitors.
The digital choice
To answer the shorter-run scenario, W&R Etiketten decided to introduce some form of digital color printing. But not before waiting to see where this technology was heading. 'It was only when Xeikon re-entered the label market and offered a serious alternative to existing systems that we saw real possibilities to re-invent our business. The 3300 is a new model and offers us the right quality at a constant speed. The overall investment was a lot more attractive than other systems. We don't like the idea of click charging. Plus it is a “green machine” because it uses more environmentally-friendly toners for printing on ordinary labelstocks,' says Willemsz.
He adds that the account managers still required the same amount of time to manage each order, so the choice was between hiring more of them, or automating and standardizing the work processes as much as possible to handle the increasing number of jobs. Cerm, which had earlier installed the firm's management information system, worked with EskoArtwork to jointly develop an automated pre-press workflow. It incorporated an intelligent JDF connection suited to label production. EskoArtwork also supplied the RIP that drives the Xeikon 3300.
All job specifications, finishing requirements and delivery data are entered into the Cerm system, which eliminates the need for double entries and minimizes the risk of errors. The database provides all the necessary information for the EskoArtwork Automation Engine workflow, including color management for all jobs. The MIS passes job information to the Xeikon X-800 digital front-end through a JDF connection. This allows the X-800 to select the correct PDF job file from the central server and process it according to the settings specified by the MIS. During production, Xeikon sends real-time status information back to the MIS with a JDF/JMF connection to track jobs and monitor the uptime of the digital press.
At present some 50 percent of the company's sales are digital. With annual sales volumes increasing by around 10 percent, the company finds that some 20-30 percent of sales involve digital printing. Later this year the second phase of JDF workflow integration comes into effect for all production stages. Cerm's Web4Labels will allow customers to submit orders via the internet, upload data and track job status. The Cerm MIS and EskoArtwork Automation Engine will jointly plan and control the job information to, and retrieve data from, the UV flexo presses using shop floor data collection modules. The system also allows for scanning of bar coded labels on material reels for stock control purposes. The goal is to speed-up order intake and job preparation, make planning and production more efficient, and significantly reduce the risk for errors. Tracking every aspect of a job's lifecycle will result in highly accurate invoicing and cost analysis.
Further into the future, Willemsz forecasts that W&R Etiketten will become a larger and more professional company: 'We will have two Xeikon digital presses running side by side, while we expect our conventional flexo presses to become even more efficient. In addition, the internet will become a major sales channel for us, and clients will be increasingly involved in managing jobs themselves. Ultimately we will make a big difference to our customers, thanks to our partners’ unique end-to-end solution.'
Pictured: Xeikon 3300 at W&R Etiketten, Tilburg
This article was published in L&L issue 3, 2011
Stay up to date
Subscribe to the free Label News newsletter and receive the latest content every week. We'll never share your email address.