Leading from the front
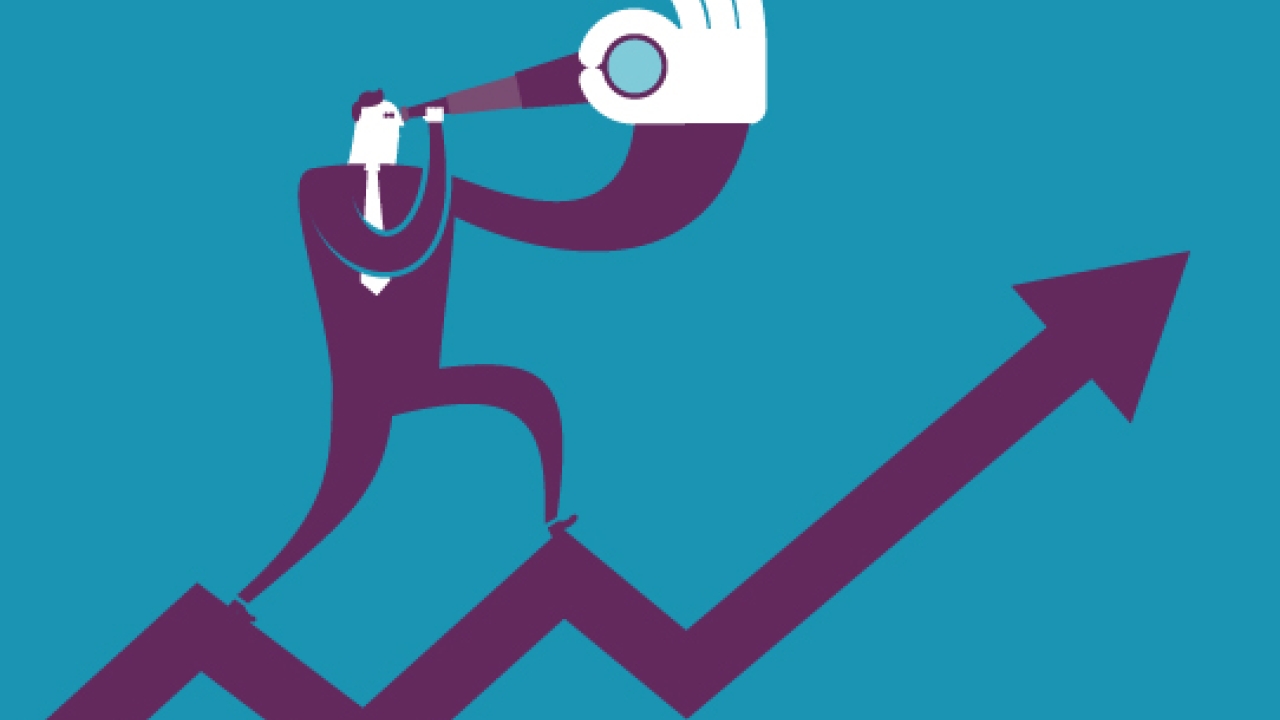
Douglas Storrie Labels’ ‘digital dilemma’ was solved by the installation of the first Edale FL-350 press, developed as a joint project between the two companies. Andy Thomas reports
Leading UK converter Douglas Storrie Labels has purchased the industry’s first Edale FL-350 flexo press following a two year joint development program.
The FL-350 at Douglas Storrie is a top of the range variant, with eight fully servo-driven UV flexo print heads with computerized pre-register, auto register and print length control. The press incorporates chill rolls, cold foil, turnbars and a sheeter. A comprehensive ancillary package includes 100 percent inspection supplied by Lake Vision Systems, double sided web cleaning and corona treater.
According to managing director Nigel Storrie, the decision to co-develop a press with Edale was a ‘calculated risk’ as the company wrestled with the dilemma of whether to take the digital route.
‘I was initially the most enthusiastic about digital,’ concedes Storrie. ‘But prices keep going up and you still have to buy secondary finishing equipment. Also too many people have already gone digital and you need to have the right mix of work. So we decided on the quick change conventional route. We thought we could fight digital and we are now better than digital.’
Neal Livermore, sales manager at Douglas Storrie, agrees: ‘We all felt we were fighting against digital. But ultimately the quality of the printing with this press, with so little waste and the ability to run fast and finish in-line means it’s so much more versatile.’
The press also gives Douglas Storrie the option to extend its business into package printing. ‘Labels and tickets is our core, but sometimes you can make more money from different parts of the business,’ says Neal Livermore.
He compares the print quality of the FL-350 press with offset litho and gravure, and with good reason (see below), ‘with the added advantage that UV flexo can print on any substrate without requiring special coating.’
The addition of chill rolls and servos on the press has already opened up new markets beyond PS labels. A particularly striking example is a job for conference and exhibition name badges printed on a very expensive 200 micron thermal pp film specially imported from the US. ‘The stretch is huge, but because we have no gears and no pulling, we can run it. We tried and failed to run it on our older technology, and this is a job that could not be run digital,’ remarks Neal Livermore.
Another piece of new work came from a chance conversation with a label buyer who asked if Douglas Storrie could print a 280 micron board insert. ‘This was easy to achieve using our sheeter and conveyor and we could do it faster than their current supplier using flat bed cutting – and in one pass.’
Open Day demos
The versatility of the FL-350 was shown during a recent Open Day at Douglas Storrie Labels, with press demos moving rapidly between a PS label, folding board and unsupported wraparound OPP.
The first job was a 4-color process cut sheet on gloss laser paper with gold cold foil. ‘The feedback from the trade is they have never seen a better laydown of foil – and we have had a lot of interest in manufacturing machine trials for other companies,’ said Neal Livermore.
The second job, ‘Wuffitmix’, was a 4-color process plus special color label on PP film. Douglas Storrie has entered this label into the 2012 Flexotech awards (Edale has entered the FL-350 press into the new machine innovation category).
The third job was an unsupported OPP wraparound film for a water bottle application.
‘With the colors preset in the machine, we have a record for changing a job in 70 seconds and in the industry this is as fast as it gets,’ says Douglas Storrie production manager Stuart Robinson. ‘Auto register means each job runs perfectly without the operator having to do any manual adjustment. We print registration marks off each plate and this brings the eight colors automatically into line and keeps them there through any variation in web tension. We are seeing just 15 meters of waste in an 8-color job, which is around one machine length. Once the plate hits, the press is in register.’
Continues Robinson: ‘If we run the job again, the press control recalls all press tension settings, as well as the position of the cylinders and moves them into position relative to each color and the press is virtually in register before any material is run.’ In addition, Edale’s inking and impression ‘strike’ feature allows print station set up with minimal waste.
‘The older the machine, the more printing is an art and the more you need a good machine minder. This machine almost runs itself,’ says Neal Livermore.
Pushing quality
The gravure-like print quality on Douglas Storrie’s Edale FL-350 press was achieved in great part by an extensive fingerprinting program undertaken by their repro suppliers, as well as the use of leading edge flexo plate technologies.
Creation Reprographics used Esko’s Equinox deltaE color management software to develop 4-color process profiles for the FL-350 which are used to optimize digital platemaking. These sheets can also be made available to designers to show the color gamut which can be achieved without special colors.
As well as using Kodak NEXcel digital plates, supplied by Pulse Media, Creation Reprographics has tested Asahi’s new AWP water-wash digital plate imaged with an Esko HD CDI, and these were also used during the Open Day demos.
‘Water wash technology has really moved on and we can now run flexo to the same quality as litho,’ enthuses Alan Coker, business development manager at Creation Reprographics.
‘The Asahi plate does not start to deteriorate like previous waterwash plates we’ve used, and we are conducting trials with plate resolutions up to 350lpi. We are seeing better ink transfer due to the reduced surface energy characteristics of the plate and no dot bridging, which also giving us a wider color gamut. They are also more environment friendly.’
The 1600 line/inch aniloxes were supplied by Cheshire Anilox Technology and use the company’s new ProFlo cell profile developed specifically for high definition flexo.
This high-release cell delivers as much as 15 percent additional ink compared to Cheshire’s conventional engravings, allowing printers to achieve high color densities at extremely fine line counts.
‘This unique cell profile allows printers to work with the expanded tone range of offset and rotogravure to produce vibrant colors and high contrast images,’ says Cheshire Anilox md Paul Smith.
‘Because we can hold such tight register, process printing now really works on this press and this makes life a lot easier,’ adds Neal Livermore.
Concludes Livermore, ‘This project with Edale has taken a long time but I’m certain the calculated risk will be repaid. It is a cracking machine and the possibilities it offers are endless. Our biggest quandary is where we go from here. My ambition for next year is to create new jobs through an extra shift and be in a position where we have to get second machine.’
FL-350 close up
‘The FL-350 could be considered Edale’s first “mainstream” label press,’ says Edale managing director James Boughton. ‘Up to now just 25 percent of Edale’s market has been label printers, with the rest being for packaging and specialist applications such as security lottery tickets. We will use this press to build up our label printing base.’
The FL-350 print units are based on Edale’s Gamma package printing press. ‘The beauty of this print head is it gives you all the functionality of more advanced three axis machines,’ says Boughton. ‘You can take the inking elements out of the machine without changing print pressure or anilox, which gives you good control over color management. Also because there are no gears between plate and impression rolls you can run a wide range of materials from 30 to 450 microns.’ The FL-350 prints up to 200 m/min with a print width of 350mm and will be offered by default with a single axis of servo on each print station.
‘Edale now offers a product that pushes back the perceived advantages of digital to only the ultra-short runs whilst providing the printer with the comfort and simplicity of printing technology that he fully understands,’ says James Boughton.
This article was published in L&L issue 5, 2012
Stay up to date
Subscribe to the free Label News newsletter and receive the latest content every week. We'll never share your email address.