New lamps for old
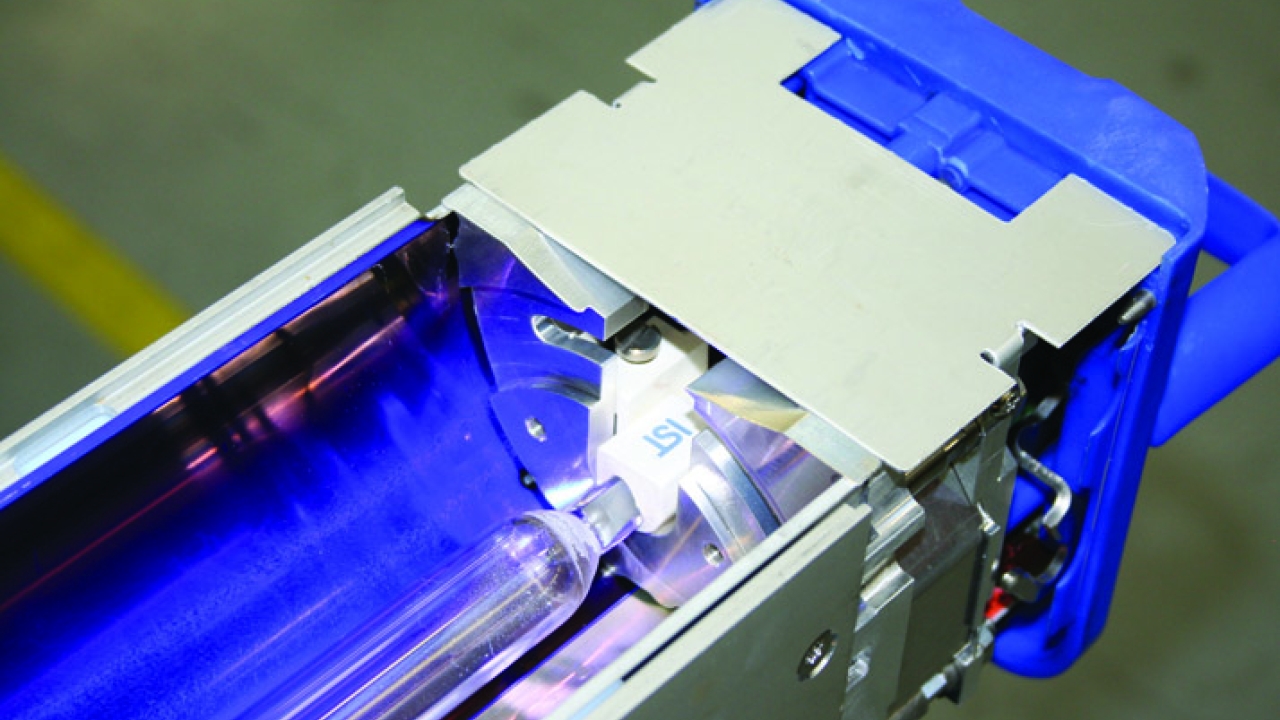
Using a new reflector design, IST has managed to squeeze 200W/cm curing power out of a 120W/cm lamp. Andy Thomas reports on the launch of the MB6
IST has developed its most energy efficient UV lamp system to date. Unveiled at the company’s ‘UV Day’ at its research and production facility in Stuttgart, Germany, the new generation MBS-6 outputs 120W/cm but has the same curing power as current generation 160 and 200 W/cm lamps.
IST calculates that for a press with eight printing units and a 450mm lamp length operating for 3,000 hours (two shifts) a year, potential savings reach 40 percent compared to its existing 200 W/cm system and 20 percent compared to a 160 W/cm system. Carbon emissions are reduced by some 6,000kg against a 200 W/cm system and over 3,000kg against a 160 W/cm system.
At the heart of the MB6 is IST’s new Duo Reflector Geometry, a ‘split’ reflector design which combines the company’s existing URS and URS-A reflectors to individually reflect longer and shorter wavelengths.
Reducing lamp output lowers its temperature and this has also allowed IST to redesign the internal components. Requirements both for exhaust air and cooling air flow to the UV unit are reduced, which in turn reduces contamination of the lamp and reflector and the time required to clean the lamp. There is also reduced heat stress on the UV lamp during ignition and in stand-by mode.
All the components of the UV curing unit can be accessed and changed without the use of tools – an FLC (Fast Lamp Change) bulb can be changed in seconds. When the MBS quick change cassette is inserted in the press all supply connections couple automatically.
The MB6 has a new rotary shutter design powered by an independent electric motor with a battery backup, so if the press pneumatics fail the shutter will always rotate into place, protecting the web from heat damage.
MBS-6 UV units are delivered and prepared for UV measurement using the portable UMS-2 UV measurement device, which connects via a dedicated cable port.
The new lamp system is complemented by IST’s new ELC electronic power supply unit, which allow stepless control of the UV lamp. The units can be stacked, greatly reducing the space required for separate power cabinets, and additional units are connected via a single cable.
In practice
Two German converters were present at the press launch of the MBS-6 to talk about their practical experiences with IST’s latest UV curing systems.
Oscar Mahl is a third generation family-owned firm with 80 employees and three divisions: adhesive labels, web offset (business forms) and sheetfed offset. Labels is the fastest growing part of Oscar Mahl’s product mix, servicing a wide range of medium -sized businesses in sectors from direct contact food labels to cosmetics, chemicals and logistics.
The company’s first experience of IST’s UV curing system came with its purchase of two Codimag offset presses, a Viva 340 and Viva 440. CEO Erwin Oscar Mahl then took the existing 160 W/cm lamps off his Gallus EM280 flexo press and replaced them with a 120 W/cm MBS-6 lamp system.
The converter was already experiencing greatly increased energy costs – rising by more than 50 percent between 2002-2011. ‘This made it welcome to reduce the lamp output to 120 W/cm,’ says Erwin Oscar Mahl. ‘We got identical drying results and production speed compared to a system with 160 W/cm lamp output and a significant reduction in energy costs. In addition IST’s service was first class.’
In addition, said Oscar Mahl, the reduced thermal load on the lamps had led to a reduction in exhaust air, a cost reduction over the whole system and reduced contamination of the lamp and reflector. ‘We noted extended lamp life of approximately three times and extended reflector life, approximately four times. It is a reliable, trouble free system which means a reduction in machine downtime and there is easy maintenance of the UV lamps thanks to quick exchangeability. This offers significant potential for savings in energy, cost, CO2 emission and downtime without any cutbacks in productivity and production speed.’
X-Label is one of Germany’s leading converters. Founded in 1991, it has grown fast by acquisition to a 123m euro operation, projected to grow to 150m euros by 2013. The company runs a wide array of print and coating processes on an equally wide range of substrates. Its major end user markets are home and personal care, premium beverages and food.
The company gave a case study of the energy reduction experienced after installation of an IST Electronic Lamp Control (ELC), with 10 140W lamps installed on a 330mm wide Gallus EM280 operating over 6,000 hours a year (three shifts plus overtime). Production uptime was 70 percent with 30 percent for machine makeready, maintenance, washup etc. The result was a reduction in energy usage of 12.5 percent.
‘We also noted increased productivity with the new IST URS reflectors – approximately four times higher reflector life,’ said X-Label CEO Tim Fiedler. ‘Reduced energy consumption is beneficial for the service life of wear parts too. For example using the UV lamp with ELC there is reduced stress for the UV lamp during ignition and in stand-by mode.’
In terms of productivity, Fast Lamp Change has had a significant impact: ‘We can change a lamp within a single minute, without disconnection of cables and removing of covers, which gives us time savings of 15-20 minutes per lamp, and so we are quicker back into production. There is also easier cleaning of UV lamps and reflectors.’
It is clear that the new MB6 UV lamp – using a simple but effective design concept – takes the labels industry a major step forward in finding ways to minimize energy costs and reduce its carbon footprint.
Pictured: Close up view of the Fast Change MB6 UV lamp housing
This article was published in L&L issue 2, 2012
Stay up to date
Subscribe to the free Label News newsletter and receive the latest content every week. We'll never share your email address.