Sappi Europe introduces eco-friendly release liner
Sol BCK promises a reduced carbon footprint, better recyclability, and cost savings over conventional PCK-based liners
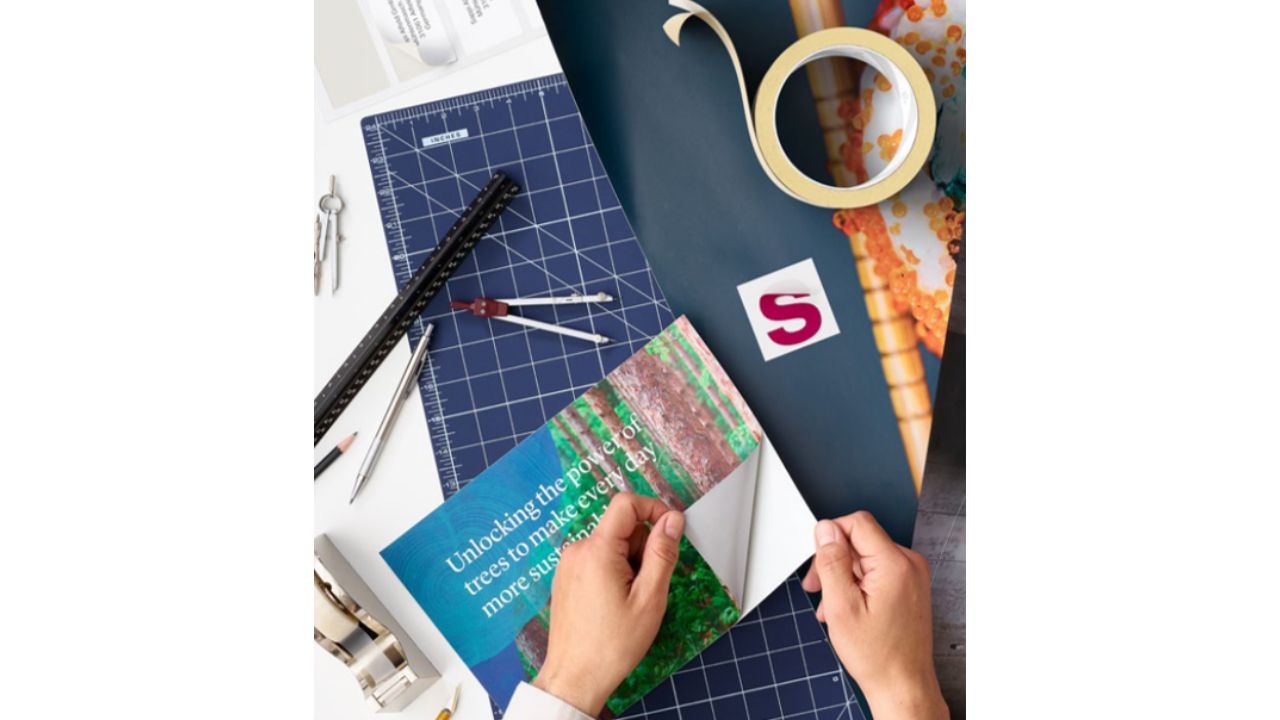
Sappi Europe introduces eco-friendly release liner
At the recent AWA Global Release Liner Industry Conference & Exhibition, Sappi Europe presented its new Sol BCK release liner for visual communication and industrial applications as well as adhesive tape products.
Manufactured in Alfeld, Germany, the release liner offers a greatly improved carbon footprint by eliminating plastic coating, better recyclability by saving plastic material and significant cost savings when compared with the commonly used PCK-based (Polyethylene Coated Kraft) release liner.
Sol BCK provides benefits over PCK by reducing the CO2 footprint by more than 50 percent compared to PCK. By avoiding the use of plastic PE, Sol BCK has significantly better recyclability compared to PCK. A special coating layer improves the flatness of the self-adhesive laminate and simplifies processing, for example, under challenging climatic conditions. It also gives outstanding results in further processing.
The AWA Global Release Liner Industry Conference & Exhibition 2023, which took place at the end of March in Denver, Colorado, is the international meeting place for release liner manufacturers and their customers. At the conference, sharing ideas, networking with industry members and presenting new market developments were on the agenda. It was an ideal opportunity for Sappi Europe to present its new Sol BCK (Barrier Coated Kraft) release liner.
Gunnar Sieber, head of sales CCK papers at Sappi Europe, explains: 'We developed the new BCK liner with a clear focus on the American market. PCK papers currently dominate there as a backing material for visual communication adhesive applications, such as indoor and outdoor advertising, vehicle wrapping, traffic signs, safety markings, shelf labeling as well as architectural and construction signs. The Sol BCK can also be used as a backing for industrial applications and for adhesive tape production.'
With PCK papers, a plastic polyethylene (PE) coating on the reverse side protects against moisture - an important feature in tropical or subtropical climates. 'On the one hand, applying PE is very material-intensive and costly, and on the other, the use of plastic is detrimental to the later recycling of PCK papers. With BCK paper, we aim to provide users with an alternative that not only boasts great processing properties but also excels in terms of recyclability and carbon footprint,' Sieber continues.
Sol BCK paper with a special surface coating improves the flatness of the self-adhesive bond. The new Sol BCK release liner features a clay coating that ensures a smooth surface. This makes it ideal for 'siliconization' and later ensures easy separation between the release liner and the respective adhesive application.
Additionally, Sappi developed a functional coating that enables the polyethylene previously used for PCK papers to be dispensed with while still minimizing moisture penetration.
Sieber adds: 'The innovative layer on the reverse side developed by Sappi is not a barrier in the classical sense, but rather a type of control option with which we can manage the effects of moisture. High humidity is a factor that causes the greatest challenges for paper-based release liners of visual communication applications.'
Significant reductions in carbon footprint have been achieved compared with PCK papers. As internal tests demonstrate, the applied functional coating on the new Sol BCK paper is significantly more environmentally friendly because the new release liner type does not have a polyethylene layer. Sappi calculated the CO2 consumption of both backing papers using a standard data model. The results are impressive: the production of Sol BCK saves up to 57 percent of CO2 emissions compared to PCK. And costs can be further reduced thanks to material savings in grammage and a significant reduction in polymer content.
Sol BCK delivers promising results in processing. The properties of the new release liner, especially in terms of further processing, were also promising: for example, the new BCK not only demonstrates good dimensional stability and flatness but also as much bond strength as a common PCK paper. Especially in terms of heat resistance in the 'siliconization' process - for example, standard silicones can be cured at temperatures up to 160 deg C - and surface strength during plotting, where the BCK has a clear advantage over the PCK. The use of PCK is only recommended for processing when there is a need for high dimensional stability and therefore good flatness of the self-adhesive laminate under climatically demanding conditions with high humidity for instance.
Despite all the advantages of the new product, Sappi is keen to point out that the new Sol BCK paper is not intended to replace PCK on a 1:1 basis. Wolfgang Hoffmann, senior application expert of self-adhesive and flexible packaging solutions at Sappi Europe, highlights: 'With our new Sol BCK release liner, we are offering a viable and more environmentally friendly alternative. Many companies we work with report that, as part of their sustainability goals, they are also taking a closer look at their suppliers and their products. We aim to make a contribution here as well - by helping our customers avoid "over-engineering", i.e., using a product that has more or better features than are actually needed for its processing. Specifically, it doesn't always have to be PCK paper. In many instances, a Sol BCK paper is sufficient to achieve great results.'
Stay up to date
Subscribe to the free Label News newsletter and receive the latest content every week. We'll never share your email address.