Offset launch
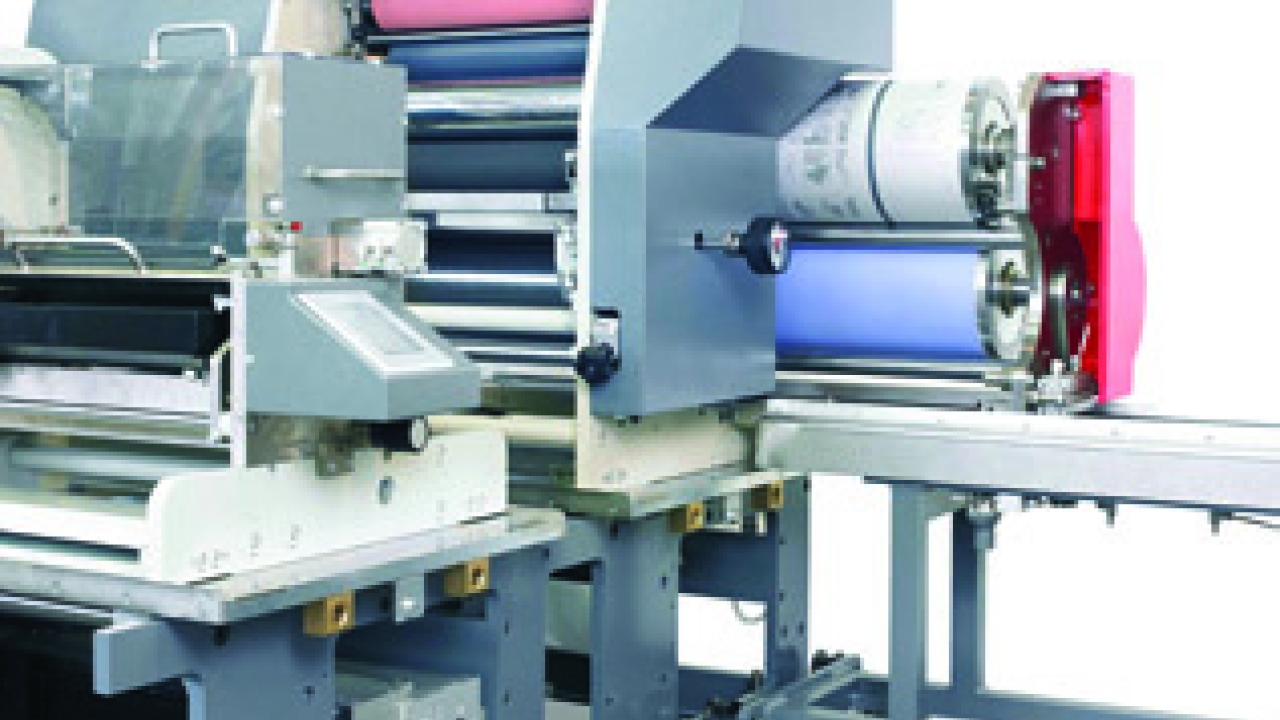
A new offset press from Nuova Gidue was the star of the company’s recent open house held at its manufacturing base in Florence, Italy. Andy Thomas reports
Nuova Gidue has unveiled a new offset press design during an open house at its manufacturing base in Florence, Italy.
The M7 Xpannd offset press line features the company’s new lightweight ‘mini-cassettes’ for different repeat lengths which can be exchanged quickly and easily using a cart + rail system. The offset mini-cassettes are stored next to the press in an area Gidue calls ‘The Organizer’.
During the open house a complete changeover of four cassettes was carried out in 90 seconds, showing the efficiency of Gidue’s easy access ‘Offset Cube’ Lean working layout. A short web path helps reduce waste during setup.
‘Flower’ flexo units and screen units use the same Universal cart + rail system, and can be positioned at any point in the press. These process heads are also stored in the Organizer in front of the press: a total of eight mini-cassettes and process heads can be held opposite each print unit. Additional process units available for the press include gravure units, rotary and flat bed embossing units, and inkjet numbering station. The dies are also moved to the press on the universal cart + rail system and stored in the Organizer.
The M7 press incorporates what Gidue calls ‘Digital Offset’ technology. This uses an HD Camera for each print station in combination with multiple servo-motors to measure and automatically adjust the register and ink density using specific ‘master’ marks. Digital Offset performs press set up in few meters without operator intervention, and maintains constant print and register quality at any speed.
For handling heat sensitive substrates there are chill drums on each print unit, and the servo-driven inking rollers are chilled for temperature control.
Federico d’Annunzio, managing director of Nuova Gidue says he decided against the current trend for a variable sleeve press design, despite the fact that the company had already developed such a system for its Leonardo offset press back in 2003.
‘Firstly, offset needs heavy duty pressures and especially on wine label papers and carton a lot of printing pressure is required. A double frame hard steel cassette can stand high printing pressure without any deformation, keeping excellent printing quality for many years. Hollow printing sleeves can show quality inaccuracy, unless fully in metal. But this increases the weight of the sleeve dramatically, making it heavy to handle.’
D’Annunzio argues that his mini- cassettes have no moving parts which require maintenance. ‘Offset printing sleeves need sliding mechanical elements in the print unit to allow the format change. These are elements of mechanical weakness and need constant maintenance, to keep the same print quality during the years.’
In terms of logistics, d’Annunzio says that with a variable sleeve press, two offset metal sleeves have to be loaded and unloaded per each print station (blanket and plate cylinders). This means loading and unloading on at least four print units probably three to four times a day. ‘The Mini Cassette instead can be literally moved “with one finger”, at a convenient height, and it is loaded and unloaded with simple, light and fast operations. No physical effort or handling risk from the operator is needed.’
The Open Day showcased Kocher & Beck’s aluminum print cylinders where the biggest sized 24in cylinder weighs no more than eight kg. In terms of cost, the mini-cassette costs around 30-40 percent more than a double set of metal sleeves.
The M7 Xpaand press has been designed with a small footprint, so seven platforms and three dies occupy less than eight meters.
The press incorporates features developed for Gidue’s flexo press lines including the ‘Snowball’ matrix stripping unit, which keeps the matrix removal roll in constant contact with the stripping unit, moving horizontally as the matrix roll increases in size. This allows the press to run at full speed even on jobs with complex waste stripping profiles. The full rated speed of the M7 Xpaand is up to 150m/min in offset and flexo mode.
The press line is available in widths of 370mm, 430mm, 530mm and 630mm. A special variant, the LTO 530-630 is dedicated to packaging, lottery ticket and heavy duty carton production.
Fully loaded flexo
Visitors also saw a fully loaded Gidue Master M5 ‘Digital Flexo’ press with the ‘Print Tutor’ system which allowed the press to be set up with 14-16 meters waste over each day of the open house.
The system uses cameras to read density, register and pressure, then multiple servos dynamically adjust both print pressure and register during the run. One camera reads registration marks printed on the narrow strip of waste on the edge of the roll, and automatically adjusts length and cross register. A second camera incorporates pattern recognition algorithms – as seen on traffic cameras – which constantly read the number of pixels on a printed patch. If print pressure is too high, the patch expands, telling Print Tutor system to reduce the pressure. If the patch shrinks, print pressure is increased.
The press was shown printing at speeds up to 150 m/min running with the Snowball matrix waste removal system. There was no print waste associated with stopping and starting the press.
‘Our aim in all our machines is digital control of all print processes to eliminate or reduce the amount of operator intervention by measuring and controlling print pressure, register and density,’ said Federico d'Annunzio. ‘This means the operator can be doing other useful tasks such as preparing the next job and finding ways to become more efficient. With this technology we can compete with digital on short runs.’
The third press on show was an 8-unit M3 Combat, demonstrated with in-line multi-page label/coupon conversion. The press comes as standard with Gidue’s Print Tutor for automatic control of print pressure, register and ink density. Die-cutting pressure is also controlled digitally. All these parameters can be stored for when the job is run again.
It is also possible to fit the press with a semi-rotary die-cutting unit with a single cylinder, which allows the press to match the set-up times of digital presses, says Gidue.
Pictured: The Gidue Cube unit unites the new removable mini-cassette with the existing Xpaand inking system
This article was published in L&L issue 2, 2012
Stay up to date
Subscribe to the free Label News newsletter and receive the latest content every week. We'll never share your email address.