Rotary tooling update
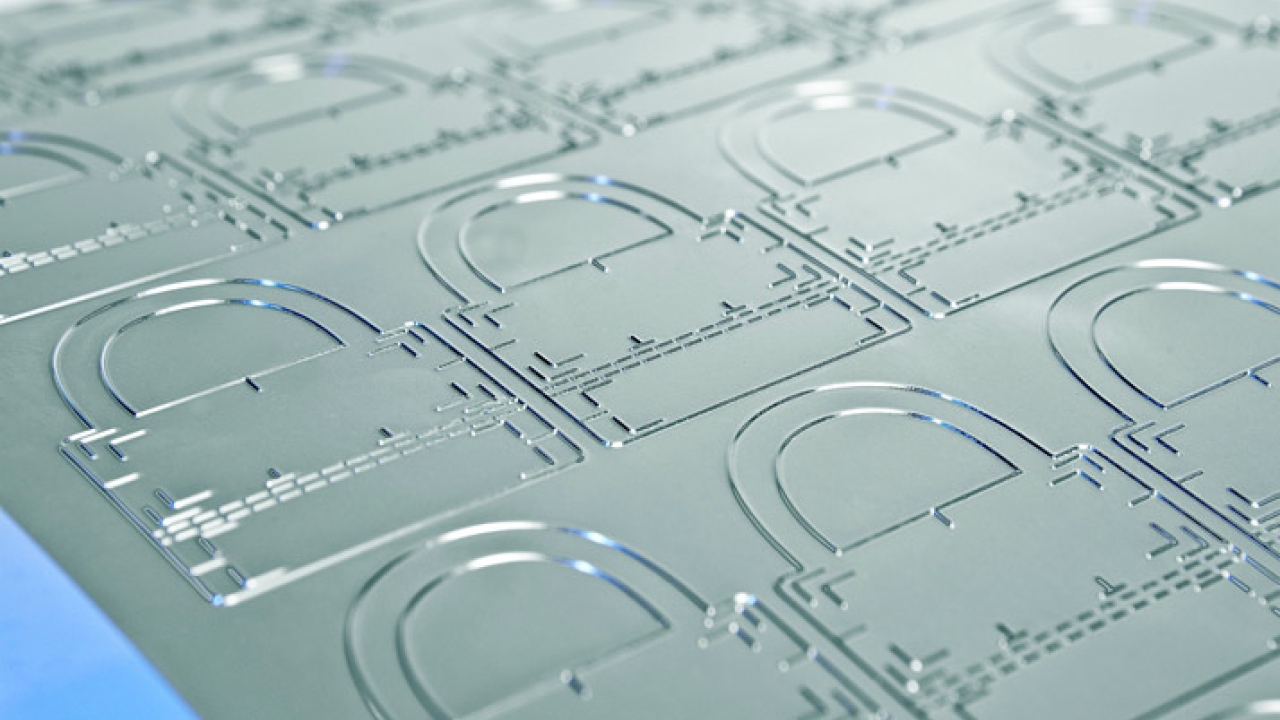
Increasing use of thin film liners is throwing up challenges for label converters and leading to a range of solutions from suppliers. Andy Thomas reports on this and other rotary tooling developments
Labelexpo Americas saw the manufacturers of flexible dies tackling the challenges presented by the increasing use of thin filmic liners and thinner face films.
Electro Optic was promoting its latest Gold Line Special die as a solution to cutting on thin film liners down to 20 microns (0,0008”) and less. In addition, the company’s Dura Line Special-C Quality has a resistant black ion coating (DLS-C) for long life requirements.
‘Extreme height accuracy due to our patented back side treatment and optimum sharpness are the most important keys for permanent success in the challenge on ultra thin liners,’ said Electro Optic sales manager Dietmar M. Becker.
But the company stressed the importance of the complete die system in these challenging applications. ‘Basic requirements for label production on thin PET liners are magnetic cylinder and anvil cylinders – recommended with smoothly polished surface – with three microns run out accuracy,’ Becker told L&L.
‘An anvil cylinder without support rollers also minimizes a build-up of errors. Adjustable units must be in absolute mint condition to keep the tolerances. When dimensioning, the 1:1 rule should be respected: The circumference of the magnetic cylinder as well as of the anvil cylinder must reach at least the maximum working width of the press. The die lines must be sharpened with a cutting angle of 40 to 75 degrees and tailor-made to the softness, lamination or lay-up properties of the material being cut. They need to be manufactured with the best possible cutting ability at the top of the blade. In addition, a die height tolerance of +/- two microns (0.00008in) is a must. There will be success for the label printer in the use of thin PET liners only when all these die-cut preconditions and other affecting points, like thermal influences and so on, are optimized.’
Wink demonstrated its SuperCut flexible dies with tight tolerances optimized for thin liner applications. Various combinations of surface treatments are available including MC coating, laser hardening, and non-stick coating.
Wink recently completed a 1,400 sqm expansion of its production facility and installed new machines specifically for the etching, engraving and coating of the SuperCut flexible dies.
But Wink’s big technology announcement was the North American launch of its ProMount aligning tool for flexible dies. ProMount is available for all popular narrow web presses in seven standard types (PM 1 to 7), with special sizes available on request. Not only does ProMount improve operator ergonomics and safety during retooling, but helps optimize die-cutting results, reduces wasted time and materials during make ready, says the manufacturer.
Rotometrics featured its recently launched Accustar line of flexible dies to provide converters with the capability to convert thin liner materials down to 23 micron/.00092” gauge PET liner material and thinner (.00075”) gauge films. The die is machined to a tolerance on total plate height of +/- two and a half micron (.0001”) with narrower, more durable blade angles, while laser hardening achieves hardness levels of up to 68 HRC for high volume applications and improved die longevity.
The company also launched a new Pin-Eject Solid Die for cutting out extremely small parts – diameters as small as 0.06” – and effectively clearing out the tiny pieces from the web where spring-eject or vacuum options struggle. This option is suitable for specialty printers and converters in niche industrial and medical markets.
Another challenging area is in-line die cutting of in-mold labels. US converter Hammer Packaging recently installed a Berhalter die-cutter to facilitate its from sheetfed to web production in the injection in-mold and lidding markets. This takes Hammer’s abilities beyond what’s possible with current counter pressure cutting systems. The Berhalter system can die-cut complex shapes directly from the company’s fleet of VSOP offset web and Nilpeter UV flexo presses.
Stamping and embossing tools
Brazilian press manufacturer Etirama has entered the market for hot stamp presses with the European launch of its flatbed Stamp Foil machine, distributed by Grafitec Label Presses.
The robust machine offers a 350mm web width and a die cutter, so labels can be finished in one pass. It can process up to 10,000 impressions per hour.
The servo-controlled Stamp Foil press can over-laminate as well as applying holograms, and has a foil re-registration system to minimize wastage. The machine features a digital touch screen, electronic reinsertion sensor and lateral, longitudinal and diagonal register of the hot foil and die-cutting stations as standard.
DMS has meanwhile introduced its new FV-Series hot stamping system. Featuring interchangeable shafts, the FV-Series can run a variety of tooling systems. The standard two inch shaft allows the use of DMS standard hard tooling. RingBase shafts provide the ability to run ring dies and thin sleeve tooling. Each RingBase shaft can accommodate a one to 1.24 inch range of repeats. SheetBase shafts provide the ability to run sheet dies similar to magnetic bases but with superior thermal and fit properties, says DMS. The FV-Series controller incorporates a predictive/adaptive control algorithm which monitors the die’s temperature and running speed and continuously adapts to press conditions.
Pantec has built on its stamping expertise with the introduction of the Swift rail-mounted foil saver, based on Pantec’s pSave vacuum saving technology and designed specifically for short run work in the high quality cosmetics market.
Pictured: Wink Supercut Die optimized for think filmic liners
This article was published in Labels & Labeling issue 6, 2012
Stay up to date
Subscribe to the free Label News newsletter and receive the latest content every week. We'll never share your email address.