Standardizing variation
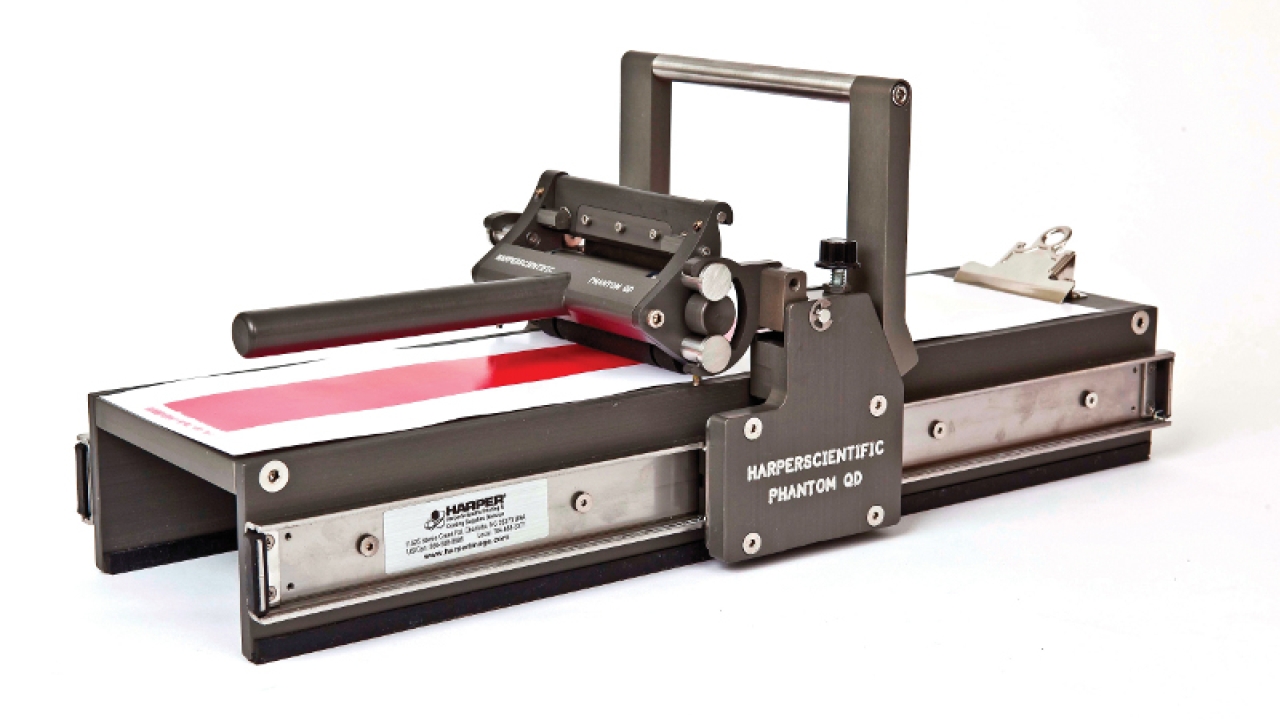
Does the flexo process have too many variables to allow true standardization? Paul Teachout at Harper Graphics argues that the numbers are there to be hit, so long as we can identify them and work to their strengths
Over the years I have seen flexography grow into a well rounded manufacturing process. The numbers are all there to achieve a standaridized workflow if we know how to identify them and work towards their strengths, despite the fact that the flexographic process has more variables than other print formats.
We also need to remember that flexography – both central impression and the inline process – offers many other advantages for packaging converters, including the ability to run 12 micron film materials, laminations, paper labels, multi-layer coupons, folding cartons or corrugated at speeds up to 2,000 fpm.
The flexographic process continues to evolve with new photopolymer plate processing technologies, graphics software, thinner ink films and advanced automated printing and converting machines. This evolution provides the perfect opportunity for standardization. Tighter tolerance products and consumables have reduced the size of the window where we need to create upper and lower control limits. This has allowed flexography to be much more competitive with other printing formats. It has also created the perfect opportunity for lean initiatives to be implemented throughout the converting process to turn a flexible, and generally manual craft, into a fully fledged manufacturing workflow.
Perhaps the most important part of the workflow is the color management process. The ability to hit repeatable and predictable color on press will allow us to be more efficient.
In many cases the ink cost is roughly four to six percent of the total operating cost. The substrate could be as much as 60 to 70 percent of the total operating cost. Most converters are concerned at the rising cost of substrates and the waste thereof. But in most cases it is the four percent ink cost that is causing the waste of our most costly consumable, the substrate. This is due to poor color management practices, including ink chemistries, poor anilox selection or lack of knowledge on how to properly identify the root causes of any problems.
The primary tool in the flexographic printing process is the anilox roller. This is the roller that will deliver the required ink film thickness at the desired printable viscosity. This tool when properly selected will allow us to hit specified solid ink densities and delta E tolerances. We have the targets to hit and we know the numbers. Now we need to determine the ideal anilox roller and most importantly, volume, to be able to hit those targets consistently and repeatedly.
Solid ink density and ink volume are directly related. If we can determine the proper volume of ink to hit a desired ∆E or SID target then it will provide the opportunity to standardize the anilox roller inventory.
Setting upper and lower control limits to identify our operating window is easier than you think. For example, we know that when printing process yellow in flexography we shoot for a solid ink density of 1.0. We also know that +/- .05 is the acceptable working tolerance. So we can read from .95 to 1.05 on yellow and achieve acceptable solid ink density. Now we need to determine the exact anilox roller volume that hits the high side of our window. For example, a 2 bcm volume roller hits 1.05 density. This is acceptable on the high side and leaves room for wear and minor plugging.
We know from previous trials that a 1.8 bcm roller will give us a .95 density reading. So we can predict that a new 2.0 bcm anilox roller will deliver a 1.05 SID for process yellow, and once it wears to a 1.8 bcm it will hit the lower limit. Now the decision is either to re-cover the roller to its original tolerance, or become an ink chemist and create a lot of variations of process yellow to sit on the shelf. If we work by the numbers, standardize to our control limits and work within them, we can make and proof inks the same way all the time as well as send them to press and achieve color first time every time.
This process can also be repeated to identify targets and volumes for spot colors. Depending on your ∆E specifications we can determine volume control limits to maintain within your ∆E tolerances. In some cases it has been identified that a .5 deviation in anilox volume will correlate to a ∆E of 1. Again, the numbers are there, we just need to identify our needs and work towards them. Now we just need to implement a procedure to optimize our anilox inventory to work towards the tolerances we put in place.
Standardizing your entire anilox inventory is the key. With standardized line screens and volumes you will have fewer targets to hit from the ink room. With a standardized and scheduled cleaning program your anilox will always be consistent and repeatable. This will all lead to reduced waste, reduced set up time and a properly managed process.
There are many ways to identify the anilox engravings that will work in our environment. The most common and efficient way is to perform a banded roller test. This will allow us to trial pre-determined cell count and volumes all at once. The other way is to utilize our existing inventory. By performing a roller audit we can determine what volumes we currently have and which are working to our strengths.
For example, if we have several 400 cpi rollers but the volumes are all different, our operators will have little chance of hitting color repeatedly. This is where the work off ink and material wastes comes into play, while we customize an ink for one roller. If we have a 3 bcm, 3.5 bcm and a 4 bcm roller we can run our own test to see which volume with our press ready ink hits the color management target. Then adjust our process to that standardized volume. Now it will not matter what 400 CPI roller is chosen because they all have the same volume. This will allow us to reduce our anilox inventory and manage it much more efficiently.
Many converters are standardizing their inventories by selecting, for example, five CPI values along with five volume values and setting them as the new standard. Anytime future rolls are ordered they must fall within this profile. Now, regardless of what operator, or on what press, the results will be consistent and repeatable.
The best way to achieve acceptable color match is to proof the inks before we go to press. This can easily be done in the ink room with the use of a hand held proofer system. We can correlate the proofer rolls to match that of the standardized anilox inventory.
Now that we have standardized volumes on press, the ink technicians will have a consistent target to shoot for. Depending on the ink system being run – UV, solvent or water-based – we can determine the proper set of proofer rolls for predictable color matching.
UV inks are 100 percent solids – what goes on the web stays on the web. UV inks will correlate one to one with the press rolls. Solvent and water based inks have high percentages of vehicles and evaporants that flash off in the drying process. This needs to be taken into consideration when selecting the proper proofer rolls. Typically you will see proofer rolls with a 10-30 percent increase in volume over press anilox to obtain proper color match with thinner ink film printing. It will always be easier to err on the high side and extend than to have to build color. Your ink and proofer roll supplier have well defined processes to support the selection or proofer roll engravings and color matching guidelines so always consult them when determining the proper proofing systems.
The best way to maintain consistency in our anilox rollers is to be sure they are properly cleaned after use. This will ensure that each time we go back to press with that roller it will pull consistent color. Off-line anilox cleaners such as chemical bath cleaners, media blast or pressure cleaners are very important tools. Our anilox inventory should cycle through a cleaner on a scheduled basis to ensure they are deep cleaned properly. This would eliminate the concern of plugging that will rob us of volume and create inconsistent color on press. Each roller should cycle through a deep clean cycle at least once every two weeks, as long as they are being properly cleaned on press as well.
When it comes down to ensuring that your rollers are in good condition for use we will need to inspect them. There are a couple options we have here. The first is the step up audit program. This is where a reverse impression is taken of each roller in your inventory. This is done by using a small pressure-sensitive tape with an Indium foil on the back. The foil is compressed into the cells, forming an exact mirror image of the roller surface. The samples are then returned to the anilox supplier for full evaluation. They will be able to identify wear patterns, damage, poor engravings and if the rollers are being properly cleaned. They will also document the exact line screen and volume of each roller so we can better control our color management process. A complete report will be returned to the converter with digital images and statistics of each roller.
Performing a yearly audit of our rollers will give us all the information we need to manage the inventory. We will identify wear patterns and roller lifecycles. By identifying our volume tolerances and performing the roller audits we will be able to make educated decisions on roller orders and forecasts.
Some converters decide to purchase their own scopes and measurement devices. This allows us to measure and maintain our inventory onsite. There are different types of scopes available for this process, although they require extensive training and are somewhat costly. For pressroom use we recommend the use of handheld inspection scopes just to see if the roller is clean and identify any wear or damage. A 400x power handheld scope will allow us to see the surface of the roll to identify these concerns. It does not take any measurements; it is for inspection only. But it will very quickly tell us if a roller is plugged or worn, thus giving us a direction to go in without just changing anilox all day until a good one is found.
As with any process, flexography is an endless pursuit of continuous improvement. It will continue to grow and reach new levels of performance. As we take each step we will continue to tighten the tolerances that have created challenges in the past. This is not your grandfather’s flexo anymore. We are a manufacturing process with specifications and tolerances and when we work by the numbers we standardize our results and reap tremendous financial rewards. That’s a fact!
Pictured: Phantom QD Drawdown
This article was published in L&L issue 2, 2011
Stay up to date
Subscribe to the free Label News newsletter and receive the latest content every week. We'll never share your email address.