Sustainability and performance from stretch sleeve labels
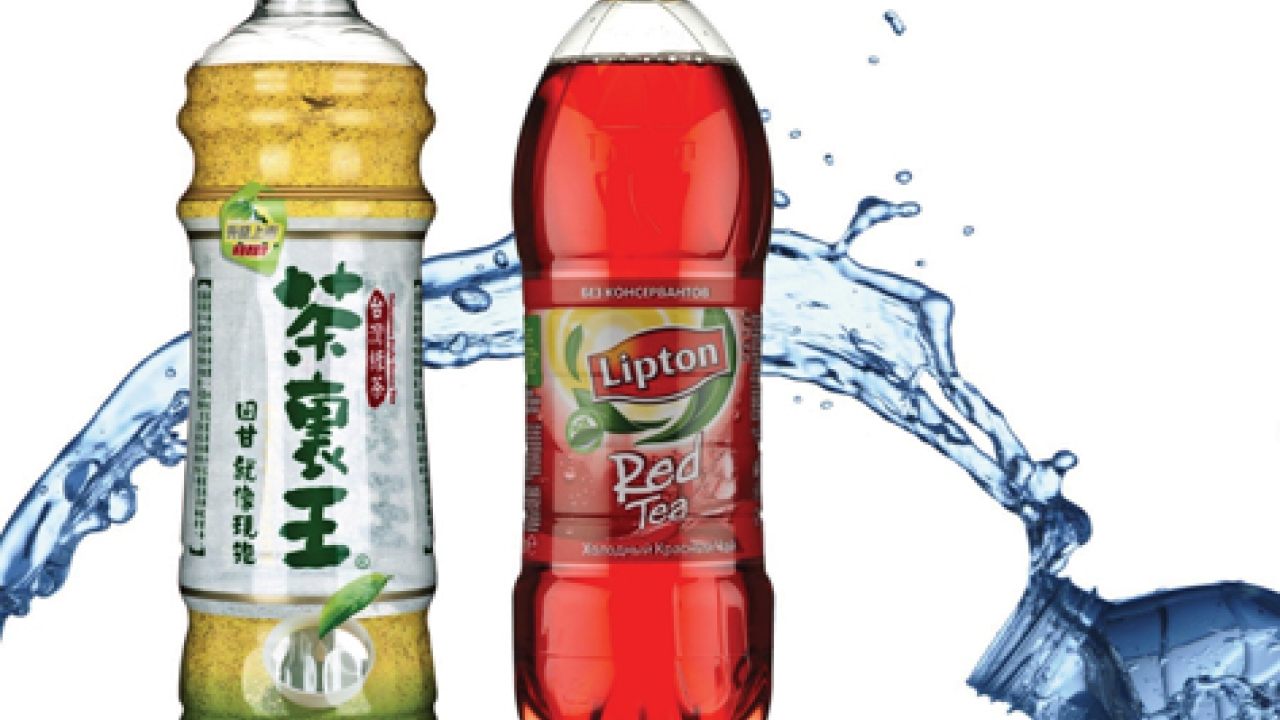
The latest developments in stretch sleeve labels offer exciting new options to address environment and sustainability issues, are highly efficient, and provide a rapid return on investment. Mike Fairley reports on the new Triple S sleeves introduced by CCL Labels
Look at any of the recent market studies on the size and growth of the label industry and it soon becomes clear that one of the fastest growing label technologies over the past few years has been sleeve labels. Latest estimates give sleeves around a 12 percent market share out of a total global label market of 76 billion US dollars.
Yet this figure is perhaps misleading. Sleeves are more than just a label that competes with other types of labeling. They can also compete with direct printing in some cases; they do offer 360 degree decoration, but so does wrap-around film or even glue-applied labels; they can provide tamper-evidence and security sealing, but then so does self-adhesives.
What sleeves do offer that is different to most other types of labeling and decoration is a cost-effective method of decorating highly complex shaped containers. They may also enable the wall thickness of plastic containers to be reduced, eliminate the need for colored containers, and provide new types of promotional opportunities. Such benefits mean that sleeves have often become a first choice for new product launches.
They are able to achieve these benefits through the sleeve conforming tightly to the container shape. Traditionally this has mainly been obtained by using a shrinkable film which has been pre-printed on a gravure or flexo press. The web is then formed into a tube, cut to size and placed over the container, and then passed through a steam, hot air or infra-red shrink tunnel, enabling the film to shrink to the container shape and provide a high quality decorated bottle or container.
Historically dominated by PVC shrink films, which in many markets have been increasingly faced with environmental considerations, new types of non-PVC shrinkable films have come into common use, including PET/PETg, PLA and OPS – which, in turn, can provide a challenge when recycling PET bottles.
Using the water separation technique which is commonly used in Europe and the USA, the shrink sleeve material needs to have a specific gravity below one so that the material floats on the water while the PET bottle flakes sink to the bottom of the tank. The non-PVC materials mentioned above all have specific gravities of about 1.25 to 1.4.
Such recycling challenges, particularly the need to meet the latest European PET Bottle Platform Guidelines, combined with other environmental pressures such as the need to reduce film usage – both in volume and weight, reduce the significant energy usage found in shrink tunnels and eliminate glue usage, have led to a growing interest and usage of alternative forms of sleeving, such as the Triple S stretch sleeve label option introduced by CCL Label, Austria.
Instead of taking an oversize shrinkable PVC, PET, PLA or OPS printed film tube and shrinking it to a tight fit using a shrink tunnel, the Triple S sleeve technology takes an LDPE printed film tube and stretches it over the bottle or container. It then contracts to guarantee a tight fit without any need for an energy-intensive shrink tunnel. It therefore uses less film and requires no shrink tunnel – potentially more than 50 percent like-for-like weight reduction per sleeve label.
Being a stretch film option, the film is also able to expand or contract with the bottle (an important requirement for carbonated beverages), is ideal for squeezable bottles, and always fits tightly and perfectly flush. Not being heat sensitive, the stretch sleeving operation helps to stabilize and counteract bottle distortion, or ‘belly-drop’ which is common with hot-filled containers.
What’s more, the LDPE stretch film used has a low density (0.91 gr/ccm) allowing easy and cleaner separation, thereby supporting PET and bottle-to-bottle recycling to become more efficient and of better quality, a point compounded by no adhesives being involved and no ink bleeding during the recycling process – as with traditional shrink sleeves.
For Tim Richards, business development manager beverage Europe at CCL Label, Triple S stretch sleeve labels are a fantastic and far more sustainable option than shrink sleeves, and indeed many other forms of labeling. He explains, ‘Triple S sleeve labels are based upon LDPE film – and being essentially a new technology – do offer a very exciting new solution to environment and sustainability issues, amongst many other advantages.
‘Indeed, I recently had a meeting with Closed Loop Recycling in Dagenham, England, in which they made a very strong appeal to us to help spread the word about just how beneficial and supportive LDPE stretch sleeves can be for the recycling process, increasing both the yield of re-won bottle material as well as improving the quality thereof.
‘This is because from a recycler’s point of view, the optimum option is always total separation of the sleeve or label from the bottle which is often quite difficult in practice, beginning of course with the identification of the clear PET bottle whilst still covered by the full-body sleeve.’
An additional environment and sustainability benefit of the stretch sleeves is that they offer a superior carbon footprint and a reduction in fossil fuel usage throughout their life-cycle (as examined by OFI and just last month validated by the Lenfest Center for Sustainable Energy, Columbia University USA).
Indeed, one of the main findings of the Center – ‘that the product carbon footprint of the Triple S Super Stretch sleeve is about four times smaller than that of the standard shrink sleeve (see Fig. 2) – seems directionally correct and explained by the combination of less raw material (per sleeve) and lack of required shrink tunnel during labeing.’
Stretch sleeves also offer significant energy and efficiency savings resulting from a leaner, cleaner application process (no shrink tunnel, no bottle drying). The extremely low density (0.91 gr/ccm) films allow the easiest and cleaner separation for recycling.
‘In summary,’ says Richards, ‘the Triple S stretch sleeve technology we have introduced is highly competitive with other label materials (up to 40 percent cost savings), is highly efficient and, when used with, say, Sleevematic ES application machinery from Krones AG, provides for a short investment payback (a ROI is possible within one year) and has low materials and utilities costs.
‘Our aim is to strengthen the brand owner’s association with "stretch" rather than only with "shrink" when discussing sleeve labels in the market place, especially as a result of stretch’s superior environmental profile.’
Pictured: Examples of bottles decorated with Triple S stretch sleeves
This article was published in L&L issue 3, 2012
Stay up to date
Subscribe to the free Label News newsletter and receive the latest content every week. We'll never share your email address.