The top 10
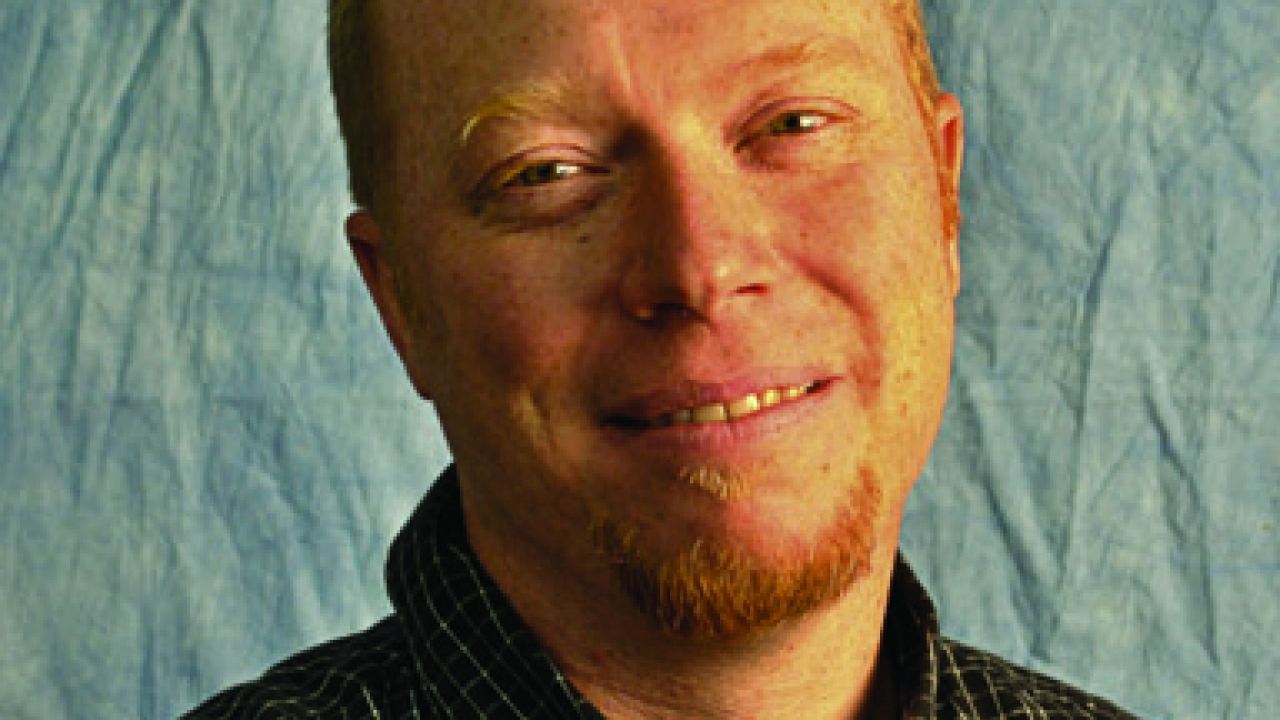
L&L asks Mactac technical guru David Ohnmeiss what are the ten questions most commonly asked by converters
Pressure-sensitive adhesives have been used for years in the labeling industry as a clean, unobtrusive means of adhering labels to various substrates. While highly customizable to fit a wide range of applications, many converters, manufacturers and printers find it difficult to grasp which pressure-sensitive adhesive chemistries will best fit their needs, what printing methods will work best and how to ensure that all regulatory requirements are met. To help address some of these concerns, we’ve compiled a list of the top 10 technical questions that pressure sensitive adhesive manufacturers typically field and have enlisted the help of veteran industry experts to provide straightforward answers.
No1. What type of adhesive is recommended for hard-to adhere-to substrates, such as waxy corrugated, and rough or porous surfaces?
When dealing with abnormal, difficult surfaces, it is important to use adhesives that are designed for use with these particular substrates. In general, soft, cold-flow, high-tack adhesives with a higher-than-average coat weight are desirable for these applications.
Testing is very important when dealing with hard-to-adhere-to substrate, especially those with limited-contact surface area and rough-textured surfaces. Because of their distinct properties, it is difficult to anticipate how these surfaces will respond to various adhesives, making rigorous testing the best way to ensure that a given adhesive will work for your application. Also be sure to consider environmental factors that will affect a substrate, such as temperature, moisture, and surface contamination as these factors can have a significant effect on adhesive performance.
No2. Should I use an acrylic or rubber-based adhesive?
Rubber- and acrylic-based adhesives each have their strengths and weaknesses, and should be carefully selected for each application to take advantage of those strengths. Permanent rubber-based adhesives generally exhibit high tack and peel, providing quick tack and strong bonds to low surface energy substrates. They also typically offer higher humidity and moisture-resistance, but are typically more susceptible to high temperatures, oxidation, UV degradation, plasticizers and chemicals.
Acrylic adhesives, on the other hand, typically provide moderate initial tack eventually building to their ultimate adhesion over time. Some acrylic adhesives perform exceptionally well on small-diameter cylinders like medical vials and in outdoor applications. They also typically offer better resistance to high temperature, UV degradation, chemicals, oxidation and plasticizers when compared to rubber-based alternatives.
No3. When should I select an all-temperature adhesive versus a general-purpose permanent (GPP) adhesive?
When selecting an adhesive, the environment in which the adhesive will be applied should determine which type of adhesive will best suit the needs of the application. All-temperature adhesives should be selected if the label will be applied to the substrate in a cold temperature environment. They are not necessarily needed if applied at room temperature then subjected to cold temperatures. All-temp adhesives are softer and offer better cold flow to allow for labeling in cold temperature environments. GPP adhesives are designed to be more aggressive at room temperature, yet they can be exposed to cold temperature environments after adequate residence time. While both all-temperature and GPP adhesives will perform adequately under a range of temperatures, each type is optimized for an intended application environment.
No4. What’s the difference between removability, open time, and repositionability?
While similar terms, it is important to know the difference between removability, open time, and repositionability when selecting the best adhesive for an application where clean label removal is essential. First, removability describes how cleanly and easily a label can be pulled from a substrate without damaging the substrate and without leaving residue or ghosting. Removability is highly dependent upon the substrate’s surface energy, environmental conditions, dwell time on the substrate, face strength, and adhesive formulation. Open time is a relative measure of removability. It describes the length of time one has to remove a label before its bond becomes permanent. Open time is important to consider when determining ease of removal of misapplied or misaligned labels. The term repositionability refers to a label’s removability in addition to the ability to reapply the same label to the same or a different substrate, sometimes multiple times.
While clean removability and adequate open time to correct placement errors are common labeling needs, repositionability generally comes into play for unique applications where it is important to reapply a specific label. These applications are generally more challenging, and as with all product selections, should be accompanied by practical testing to confirm fitness for use.
No5. What regulatory requirements should I be aware of when selecting a pressure sensitive adhesive?
When selecting an adhesive, it is important to remember that regulatory requirements change frequently and are highly application-dependant. It is a good idea to request that your customer provide you with all requirements for their specific application so that you can work with a supplier to provide a recommendation that meets all of those needs. Take into account that suppliers will need exact regulatory requirement numbers to make an informed recommendation. As always, it is important to test adhesive options within the specific application to ensure regulations are met.
No6. How long will a label last?
Label life expectancy can be broken into two categories, shelf life and durability. Shelf life refers to the amount of time a label maintains its quality and performance level in an unapplied state. To maximize shelf life, raw material label stock and finished labels should be stored in conditions as close to 72 F and 50 percent RH as possible. Durability relates to how long a label will perform on a substrate in its end- use application. Label durability depends on label construction, print technology and environmental conditions. Understanding the durability needs for an application is key to designing a cost-effective and successful label solution.
No7. When do I need a direct vs. indirect food contact adhesive for my application?
The main factor that determines whether food contact labeling is considered direct or indirect revolves around whether there’s a functional barrier between the food that is being labeled and the adhesive. For more specific information, please refer to the Food and Drug Administration’s mandates on the topic: FDA spec 21 CFR 175.105 for regulations on indirect food contact adhesives and FDA spec 21 CFR 175.125 for direct food contact adhesives. Also remember that with food labeling there can be additional regulations that relate to the label facestock, inks, varnishes, etc, further highlighting the importance of working with knowledgeable suppliers.
No8. What film facestock should I use?
There are numerous types of film facestocks to choose from that could fit the needs of labeling applications, and all have their own unique characteristics that may help or hinder performance. Knowing these performance characteristics are only part of the equation, however, as you’ll also need to know the facestock’s converting characteristics, such as usefulness for printing, die cutting and so on. The most popular film facestocks used in prime labeling are biaxially-oriented polypropylene (BOPP/PP) or polyolefin (PO), polystyrene (PS), and polyethylene (PE). For more durable labeling requirements, polyvinyl chloride (PVC) and polyethylene terephthalate (PET) are often used. For those customers that would like a more environmentally friendly facestock, polylactic acid (PLA) has become quite popular. The usual rules apply when it comes to selecting a film facestock: know your application needs and select a face stock accordingly.
No9. What advice can you give regarding digital printing on pressure sensitive laminates?
When planning the best method for digitally printing labels, research what products are recommended for your digital press or printer model for optimal results. Knowing what model you or your customer is using, required properties of printing materials (such as basis weight and caliper range), the printer or press’s media handling capabilities (whether it can handle pressure-sensitive label media), and whether the printer requires ink-specific stock (ink jet, toner, thermal transfer, Indigo, etc.) is very helpful when making printing decisions. For any pre-print requirements, check with your ink manufacturer to find out whether a given ink will work well on certain substrates and be functional and safe for use in that digital press or printer. As a result, it is safest to steer toward products made specifically for digital printers.
When working with thermal transfer printers, finding the right ribbon to use is imperative. In general, wax-resin ribbon should be trialed on substrates not originally designed for thermal printing. Testing all aspects of the printing and end-use for a product is the only way to be sure that your label construction and design will effectively meet your customer’s expectations.
No10. What general advice can you offer someone selecting a pressure-sensitive laminate?
As has been stated numerous times before, it is important to test products sufficiently in any application. The more circumstances and conditions you account for in testing, the more likely you are to select the correct pressure-sensitive laminate. Do not hesitate to talk to your supplier, they can help you ask the right questions and can recommend products designed for your specific application. Attaining the needed performance, price and aesthetics is critical, so communication is key to working with your customer and your PSA supplier to find the best product to meet you and your customer’s wants and needs.
Pictured: David Ohnmeiss
This article was published in L&L issue 6, 2011
Stay up to date
Subscribe to the free Label News newsletter and receive the latest content every week. We'll never share your email address.