Finishing in- or off-line?
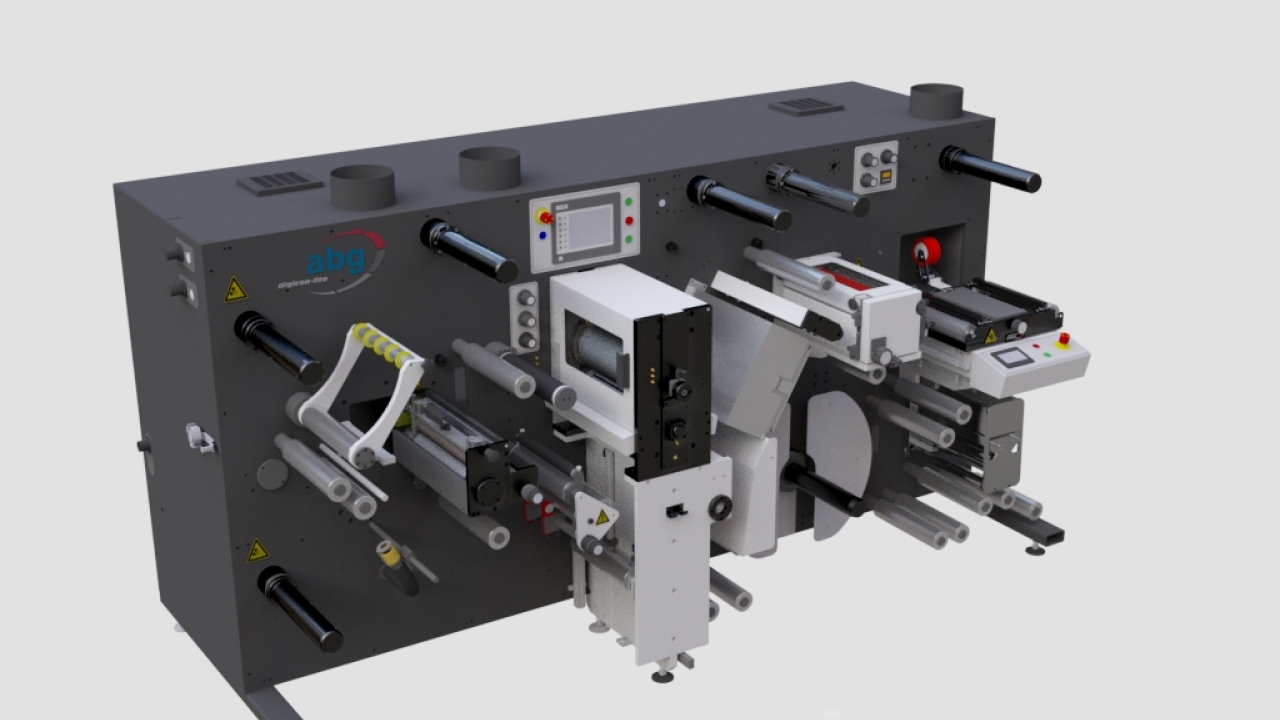
The show sees the revival of the hybrid press concept, where digital and conventional print and converting operations are carried out in one pass – the ‘traditional’ narrow web model since the earliest days of PS label converting in the 1970s and 1980s.
Hybrid models shown at Labelexpo will include FFEI’s Graphium, Gallus’ DCS340, Omet’s JetFlex and Mark Andy’s Digital Series. The advantages of processing in one pass are well known, but the challenge is how to optimally match conventional print capabilities with a digital engine, and how to avoid downtime on the digital engine while the conventional units are being made ready. This will require more sophisticated workflows, for example color matching a flexo spot color with a digital CMYK engine, allowing the bulk of ink coverage with cheaper flexo inks and leaving the detailed imaging to the digital unit. Ideally the same workflow should produce any required plates along with RIPping the data to the digital press to allow optimal syncing of the processes.
Off-line digital
Up to now off-line converting has been the overwhelming choice among label converters investing in digital presses. The key advantage is seen as allowing the digital engine to keep working without having to wait for in-line converting to be set up.
As digital presses get faster, however, manufacturers have begun to add in-line finishing as an option, particularly using laser die-cutting to create a fully variable converting system without the need to change die-cutting plates.
At Labelexpo this can be seen on a range of systems including the Durst Tau (partnering with German company Printum), EFI (who pioneered in-line laser processing) and Colordyne. Domino also launches its N610i integrated with an AB Graphic Digicon 3 converting line.
Proponents of this approach argue that as UV inkjet presses have got faster and wider, a traditional in-line approach becomes more viable, taking away the extra handling step of moving a printed roll to an off-line converter and the additional waste required to set up each job off-line
Off-line conventional finishing?.
And as this debate hots up at Labelexpo Europe, there are signs that the conventional press industry is also be looking at the possibilities of off-line conversion.
The driver here is fixed palette printing, whether offset or flexo, which greatly increases printing efficiency. Because the same inks stay in the press (and the same anilox rolls), there is no need to wash the press down between jobs. A job change is as fast as changing the plate sleeves.
This has put the focus on the converting end of the press, where making changes between jobs reduces the potential number of job changes which fixed palette makes possible.
Labelexpo sees two responses: firstly we see fast die changeover systems, particularly horizontal loading achieved in the QCDC systems from Mark Andy and Nilpeter.
The second approach is to consider taking converting off the press. Codimag, for example, shows its Viva 340 Aniflo Evolution press in a reel-to-reel format, without die-cutting and added value processing. And in an interview in the forthcoming Labels & Labelng (issue 4, 2015), Soma suggests that CI presses could efficiently print thinner PS label constructions with off-line converting.
It will be fascinating to see how these arguments and concepts play out at Labelexpo Europe 2015.
Stay up to date
Subscribe to the free Label News newsletter and receive the latest content every week. We'll never share your email address.